
극저온 고체화 수소 및 과냉각 액화수소 평가 장치에 대한 수치 해석 기술 개발
2025 The Korean Hydrogen and New Energy Society. All rights reserved.
Abstract
In this study, we developed a numerical analysis technique for an evaluation device for cryogenic solidified hydrogen and sub-cooled liquefied hydrogen generated from liquid hydrogen through heat exchange of helium gas. The helium was was selected as a heat exchange medium to cool the liquid hydrogen, and hence a spiral-shaped indirect heat exchanger was manufactured to increase the efficiency of heat exchange. According to the analysis of the solidification mechanism, this study analyzed the production amount of solidified hydrogen and its influence on the mass flow rate and the cryogenic temperature of helium gas. It was confirmed that the mass flow rate had a significantly greater effect on the production amount of solidified hydrogen than the inlet temperature.
Keywords:
Numerical simulation, Solidification/melting model, Solidified hydrogen, Cryogenic helium gas, Heat exchanger키워드:
수치 해석, 응결/용융 모델, 고체화 수소, 극저온 헬륨 가스, 열교환기1. 서 론
수소 연료의 주요 특징은 높은 에너지 밀도, 낮은 무게, 청정 연료로서의 친환경성, 다양한 저장 및 운송 가능성 등이 있다. 특히 액체 수소는 극저온 상태에서 높은 순도와 부피당 에너지 밀도를 제공하여 장거리 운송과 대규모 저장에 적합하며 재생 에너지의 변동성을 완화하는 데 사용될 수 있다1,2). 수소 연료의 장점으로는 화석 연료 대비 탄소 배출이 없고 연료 전지나 다양한 산업적 용도에 활용할 수 있다는 점이 있으며 낮은 점도와 높은 확산성과 같은 물리적 특성은 저장 효율을 높이는 데 기여할 수 있다. 그러나 단점으로는 수소의 생산, 액화, 저장 과정에서 높은 에너지 소모와 비용이 발생하며 극저온 조건과 고압 저장을 유지하여야 하는 기술적 복잡성이 있다. 또한 수소의 낮은 분자량으로 인한 누출 가능성과 높은 인화성을 고려한 엄격한 안전 관리가 요구된다. 이처럼 수소는 장단점이 혼재된 에너지 매체로 대규모 저장과 효율적 활용을 위하여 지속적인 기술 개발이 필수적이다3,4).
고체화 수소는 수소를 극저온 상태에서 고체 형태로 저장한 것으로 일반적으로 온도가 약 14 K 이하에서 형성된다. 고체화 수소는 액체 수소와 비교하여 저장 밀도가 더 높아 같은 부피에서 더 많은 수소를 저장할 수 있는 장점이 있다5). 또한 고체 상태로 저장되기 때문에 액체 수소에서 흔히 발생하는 증발 가스(boil-off gas, BOG) 문제가 없으며 이를 통해 연료 손실을 최소화할 수 있다6). 고체화 수소는 낮은 기체 압력으로도 안정적으로 저장할 수 있어 고압 탱크가 필요한 액체 수소보다 안전성이 높다. 그러나 고체화 수소는 극저온 상태를 유지하여야 하므로 이를 위한 고도의 냉각 기술과 높은 에너지 소비가 필요하며 저장 및 처리 과정에서 기술적 복잡성이 증가할 수 있다7,8). 따라서 고체화 수소는 액체 수소보다 저장 효율과 안정성이 우수하지만 실용화를 위해서는 냉각 및 취급 기술의 추가적인 발전이 필요하다.
20 K인 액화 수소를 14 K까지 더 낮은 온도로 냉각시켜 고체 형태로 얼린 수소를 극저온 고체화 수소라고 하며 과냉각 액화 수소는 고체화 수소가 되기 전까지 20 K 이하에서 액화 수소 형태를 유지하고 있는 수소의 상태를 의미한다. 현재 많은 연구자들이 BOG의 처리와 관리를 위해 고체화 수소나 과냉각 액화수소 등의 연구를 수행하였다9-13). Ma 등14)은 오일러-오일러 모델과 입자 흐름의 운동 이론을 기반으로 수치 모델을 구축하여 지구 및 미소 중력 조건에서 원형 파이프 내 슬러시 수소의 유압 및 열전달 특성을 조사하였다. Jin 등15)은 수평 파이프에서 슬러시 수소의 흐름 특성을 예측하기 위해 오일러-오일러 2유체 모델을 기반으로 한 개선된 3차원 수치 모델을 구축하였다. 결과적으로 슬러시 수소를 사용하여 유체의 온도를 국부적으로 충분히 낮출 수 있어 액체 수소의 증발을 억제할 수 있음을 보고하였다.
Xia 등16)은 상변화와 열전달을 고려한 수치 모델을 통해 슬러쉬 수소의 저장 특성과 2상 유동장 등을 조사하였다. 해석 결과는 슬러시 수소의 물리적 법칙을 명확하게 보여줄 수 있으므로 슬러시 수소의 균일한 분포가 효율적인 저장 및 적용을 위해 촉진될 수 있었다. Park 등17)은 NASA가 제안한 소형 및 이동식 탱크용 통합 냉동 및 저장 기술을 적용하여 슬러시 수소의 장기 보관 및 운송 개념을 실험적으로 검증했다. 수소가 실제로 슬러시 상태인지 관찰하고 밀도를 결정하는 방법론이 제시되었다.
고체 수소는 극저온 환경에서 형성되므로 열전달, 냉각 속도, 고체 형성 과정에서의 상변화와 같은 복잡한 물리적 현상을 이해하는 데 computational fluid dynamics (CFD)가 효과적으로 사용될 수 있다. 이를 통해 고체 수소의 형성 조건을 최적화하고 저장 효율을 극대화하며 에너지 소비를 줄이는 설계 피드백을 제공할 수 있다. 하지만 고체화 수소에 대한 CFD 해석은 복잡한 물리적 현상과 극저온 환경의 정밀한 시뮬레이션이 요구되기 때문에 여러 어려움이 존재한다. 선행 연구18,19)를 통해 소형 응축형 액화 장치를 사용하여 액체 수소를 생산하는 방법을 개발하였고 장기 보관을 위한 자동 제어 기술을 통해 액체 수소의 zero boil-off를 달성하였다. 본 연구에서는 헬륨 가스의 열교환을 통해 액체 수소로부터 생성되는 극저온 고체화 수소 및 과냉각 액화 수소 평가 장치에 대한 수치 해석 기술을 개발하였다.
2. 수치 해석 기법
Fig. 1은 본 연구에서 고려한 극저온 고체화 수소 및 과냉각 액체 수소의 생성을 위한 실험 장치를 보여준다. 본 연구에서 제작한 헬륨 극저온 장치(He cryostat)와 기존의 소형 응축형 액화기(LH2 liquefier), 압축기(compressor), 프리쿨러(pre-cooler), 플랜지에 부착된 극저온 냉동기(cryocooler) 등을 보여준다. 액체 수소의 극저온 냉각을 위하여 극저온 장치가 설계되었다. 액체 수소 생산에 사용되는 극저온 용기의 경우 액체 수소 냉매를 직접 저장해야 하므로 전도를 통한 열 침투를 최소화하기 위하여 액체 질소 쉴드 및 이중 진공 단열 탱크 등이 포함되었다. 또한 헬륨 극저온 장치도 액체 헬륨을 통한 열교환이 이루어져 내부가 진공 환경으로 유지가 필요하므로 이중 용기로 설계되었다.
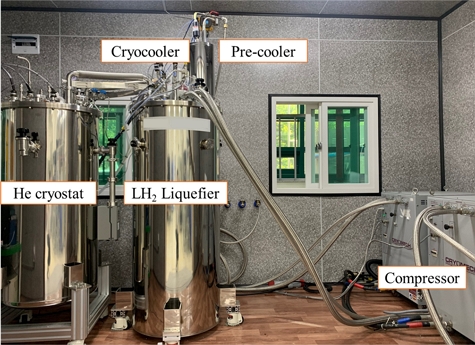
Experimental setup for cryogenic solidified hydrogen and subcooled liquefied hydrogen evaluation device
Fig. 2는 본 연구에서 고려한 극저온 고체화 수소 및 과냉각 액체 수소의 생성을 위한 실험 장치의 모식도를 보여준다. 극저온 송풍기는 헬륨 극저온 용기의 상부 플랜지에 설치되었으며 이를 통해 극저온의 헬륨 가스 냉열이 액체 수소로 전달되도록 설계하였다. 열교환에 사용되는 가스는 액체 수소의 온도를 낮추기 위해 헬륨을 열교환 매체로 선택하였으며 열교환의 효율성을 높이기 위하여 나선 형태의 간접 열교환기를 제작하였다. 본 연구에서는 액체 수소의 고체화 현상을 수치 해석 기법을 통해 구현하기 위하여 응축형 수소 액화기 내부의 형상만 고려하였다. 액체 수소가 30-35% 정도 충분히 생성되었다고 가정하였으며 헬륨 가스와 열교환을 통해 생성되는 극저온 고체화 수소의 변화량을 분석하였다.
본 연구에서는 극저온 고체화 수소 및 과냉각 액체 수소의 상변화 과정을 모델링하기 위하여 ANSYS Fluent (ANSYS, Canonsburg, PA, USA)를 사용하였다. 본 연구에서 사용된 지배 방정식인 연속 방정식, 운동량 방정식 및 에너지 보존 방정식은 다음과 같이 정의된다20).
(1) |
(2) |
(3) |
여기서 V는 유체 속도 벡터 항이며 ρ는 밀도, μ는 동점성 계수, P는 압력, g는 중력 가속도, k는 열전도도를 각각 나타낸다. 식 (2)의 소스 항인 S는 대류에 대한 위상 변화 효과로 인하여 운동량 방정식에 추가된 Darcy 감쇠 법칙의 항을 나타내며 다음과 같이 정의된다.
(4) |
여기서 계수 C는 머시 존 상수이다. 이 상수는 감쇠의 진폭을 측정하며 이 값이 높을수록 응고될 때 재료의 속도가 0으로 전환되는 정도가 더 가파르다. 대부분 계산에 권장되는 값은 104-107 사이며 이 범위를 초과하는 값은 수치 해석의 솔루션이 진동할 수 있다. β는 액체 분율이며 0은 고체 상태를 나타내고 1은 액체 상태를 나타낸다.
H는 단위 질량당 엔탈피이며 이는 헌혈 엔탈피(h) 와 잠열 엔탈피(ΔH)의 합으로 다음과 같이 정의된다.
(5) |
(6) |
잠열의 함량은 0 (고체의 경우)에서 L (액체의 경우) 사이에 달라진다.
(7) |
액체 분율(β)은 다음과 같이 정의된다.
(8) |
Fig. 3은 본 연구에서 고려한 극저온 고체화 수소 생성을 위한 수치 해석 도메인 영역을 보여준다. 극저온 냉동기는 20 K을 유지한 상태로 온도를 유지하고 있으며 액체 수소는 30-35% 생성되어 기체 수소와 함께 존재하는 것으로 가정하였다. 극저온의 헬륨 가스는 직선 파이프라인을 통해 하강하면서 주입되고 나선 형태의 열교환기를 통해 액체 수소와 열교환을 한 뒤 직선 파이프라인을 통해 상승하면서 토출되는 형태로 구현하였다. 액화기의 중심에 존재하는 히트 파이프와 핀은 액체 수소를 형성하기 위해서 존재하는 열교환기를 나타낸다. 본 연구에서 고려한 극저온 고체화 수소 생성에 대한 전산 해석의 작동 조건 및 이산화 조건은 Table 1에 명시되어 있다. Solidification 및 melting 모델의 완화 계수 중 압력은 0.15, 모멘텀은 0.3, 에너지는 0.5를 각각 고려하였다.
Fig. 4는 본 연구에서 고려한 해석 영역의 격자 분포를 나타낸다. 본 연구에서는 사면체 격자를 활용하여 격자 의존성 테스트를 통해 약 1,265만 개를 생성시켰다. 기체 수소 영역과 액체 수소 영역 및 열교환 영역 등을 나누어 격자를 생성시켰으며 열교환 영역의 격자를 상대적으로 조밀하게 구현하였다. 선행 테스트를 통해 본 연구에서 고려한 격자수는 고체화 수소의 생성 속도에 대해 충분히 합리적인 정확도로 수행될 수 있음을 확인하였다.
Fig. 5는 본 연구에서 고체화 수소 상변화 해석의 타당성을 확보하기 위한 검증 결과를 보여준다. 수소 물질의 특수성으로 인하여 고체화 수소의 흐름과 열전달에 대한 실험은 거의 없다. 따라서 본 연구에서 전산 해석 모델 검증은 고체화 수소의 압력 강하의 수치적 결과와 실험적 결과의 비교를 통해서만 수행되었다. 직경이 16.6 mm인 수평 파이프에서 고체화 수소의 흐름 특성과 다양한 속도에서 압력 강하를 조사하였다. 검증 결과 Ma 등14)에 의해 수행된 수치 해석 결과와 현재 기법을 통해 수행된 수치 해석 결과가 오차 범위 내에서 경향이 잘 일치하였다.
3. 결과 및 고찰
3.1 고체화 메커니즘 분석 결과
Fig. 6은 본 연구에서 수행한 극저온 고체화 수소 형성에 대한 상변화 해석에서 시스템 내부 수직 평면에서의 시간에 따른 온도 분포 변화를 보여준다. 온도장의 구간은 10 K에서 35 K까지의 11개의 값으로 표현하였다. 그림과 같이 극저온 헬륨 가스가 파이프라인을 따라 이동함에 따라 액체 수소의 온도가 점점 낮아진다. 또한 연속적으로 주입되는 극저온 헬륨 가스에 의하여 내부 열교환기 좌측 및 우측에서 급격하게 온도가 급격하게 낮아지는 것을 볼 수 있다. 고체화 수소는 14 K 이하에서 형성되므로 열교환기 주위에서 20 K로 존재하던 액체 수소가 열교환에 의해 고체화 수소로 상변화가 발생하게 된다.
Fig. 7은 액체 수소에서 고체화 수소로의 상변화를 확인할 수 있는 고체화 수소의 체적 분율을 나타낸다. 시간이 지남에 따라 직선 구간에서부터 고체 수소가 급격하게 생성되기 시작하며 연속적인 극저온 헬륨 가스에 의해 나선형 코일 형태를 따라 형성되기 시작한다. 극저온 헬륨 가스와 충분한 열교환에 의해 액체 수소의 온도가 감소하고 파이프라인을 따라 고체화 수소가 생성되는 것을 확인할 수 있다. 특히 파이프라인이 인접해 있는 열교환기 영역에서 온도가 상대적으로 급격하게 감소하므로 고체화 수소의 생성량이 많은 것을 확인할 수 있었다.
Fig. 8은 충분히 열교환이 이루어진 상태(5,000초)에서 최종 고체화 체적 분율을 보여준다. 극저온 헬륨 가스가 주입됨에 따라 나선형 열교환기 좌측 부분에서 우측 부분에 비해 고체화 수소가 상대적으로 두껍게 형성된다. 또한 시간이 지남에 따라 열교환기 주변에서 전체적으로 고체화 수소의 영역이 천천히 증가하게 된다. 실제 실험에서는 안전을 고려하여 열교환기로부터 생성되는 고체화 수소의 무게 등을 고려해야 할 필요가 있다. 또한 입구 직선 라인을 제외하고 모든 영역에서 파이프라인을 따라 많은 고체화 수소가 형성되는 것을 볼 수 있다. 이는 극저온 헬륨 가스가 주입됨에 따라 입구 영역에서의 급격한 열교환에 영향을 받기 때문이다.
Fig. 9는 시스템 내부 수직 평면에서의 고체화 생성에 따른 속도 벡터 및 시간에 따른 고체화 수소 분포를 나타낸다. 열교환기의 가장 하부의 파이프와 상부의 파이프에서 주변 표면을 따라 고체화 수소가 가장 많이 생성되며 중앙 부분은 옆면에 주로 형성됨을 알 수 있다. 또한 고체화 수소가 열교환기 주변에 형성되면 액체 수소의 유동을 방해하는 경계층의 역할을 하게 되므로 유동이 파이프 주위를 원활하게 지나가지 못하게 된다. 따라서 파이프 주위를 따라 급격한 유속 방향의 변화를 형성하고 고체화 수소의 성장에 따라 파이프 주위로 모여드는 형태로 전체적인 유동 분포를 보였다. 앞서 언급한 바와 같이 고체화 수소가 생성되는 영역은 시간이 지남에 따라 극저온 헬륨 가스가 주입되면서 하부 파이프라인에서부터 상부 파이프라인까지 차례대로 생성됨을 확인하였다. 충분한 열교환 과정을 거쳐 파이프 주위의 액체 수소의 온도를 충분히 낮출 필요가 있으며 고체화 수소가 생성되면 경계층의 역할을 하는 것을 확인할 수 있었다. 이러한 고체화 메커니즘 분석을 통해 본 연구에서는 극저온 헬륨 가스의 유량과 온도 변화에 따른 고체화 수소 생성량과 영향도를 분석하였다.
3.2 헬륨 가스 유량 및 온도 영향도 분석
Fig. 10은 극저온 헬륨 가스의 유량에 따른 온도 분포 및 고체화 수소 체적 분율을 보여준다. 본 연구에서 고려한 극저온 헬륨 가스의 질량 유량은 0.010, 0.015 및 0.020 kg/s이며 입구 온도는 5 K로 고정하였고 계산의 편의성을 위하여 총 2,000초로 계산하였다. 유량이 증가할수록 극저온 헬륨 가스의 온도는 열교환기에서 감소하게 되며 이에 따라 고체화 수소의 생성량이 증가하는 것을 알 수 있다. 입구 유량이 증가하게 되면 액체 수소와의 열교환량이 증가하게 되므로 고체화 수소의 생성량이 증가하기 때문이다. 2,000초까지 액체 수소로부터 발생하는 과냉각량은 최대 1.2×10-3 m3가 생성됨을 확인하였다.
Fig. 11은 극저온 헬륨 가스의 입구 온도에 따른 온도 분포 및 고체화 수소 체적 분율을 보여준다. 본 연구에서 고려한 극저온 헬륨 가스의 입구 온도는 4, 5 및 6 K이며 유량은 0.015 kg/s로 고정하였다. 극저온 헬륨 가스의 입구 온도를 이렇게 낮게 설정한 이유는 액체 수소의 온도 변화를 고려하여 14 K까지 낮춰야 하기 때문이다. 입구 온도가 증가할수록 극저온 헬륨 가스의 온도는 열교환기에서 큰 변화가 없는 것으로 관찰되었으며 이에 따라 고체화 수소의 생성량은 눈에 띄는 큰 변화는 관찰되지 않았다. 이는 극저온 헬륨 가스의 온도가 매우 낮아 열교환의 변화에 큰 영향을 끼치지 못했기 때문이다. 현재 온도 범위에서는 2,000초까지 액체 수소로부터 발생하는 과냉각량은 최대 1.6×10-4 m3가 생성됨을 확인하였다.
Fig. 12는 고체화 수소 생성량에 영향을 미치는 변수들에 대한 주요 영향을 분석한 것이다. 시스템 내부 수직 평면에서의 파이프라인에서 수직선을 따라 500개의 점에서 데이터를 추출하여 높이에 따른 고체화 수소 체적 분율을 분석하였다. 그래프에서 질량 분율이 0으로 갈수록 액체 수소가 과냉각되어 있는 고체화 수소 상태를 나타내며 1로 갈수록 액체 수소 상태를 나타낸다. 전체적으로 고체화 수소는 파이프라인 상부 및 하부에서 주로 많은 양이 생성되며 파이프 사이의 간격에서는 상대적으로 생성량이 적다. 유량이 증가할수록 파이프라인 상부 및 하부에서 급격하게 고체화 수소량이 증가하게 됨을 알 수 있다. 반면 입구 온도가 증가하더라도 고체화 수소의 생성량에는 상대적으로 큰 영향을 끼치지 못한다. 따라서 본 연구에서 고려한 시뮬레이션 파라미터의 범위에서는 온도에 따른 영향보다 유량에 따른 영향이 액체 수소의 과냉각에 의한 고체화 수소의 생성량에 큰 영향을 끼침을 확인할 수 있다.
Fig. 13은 본 연구에서 고려한 시뮬레이션 파라미터에 대한 고체화 수소 체적 분율과 고체화량을 3차원으로 도식화한 것이다. Fig. 13과 같이 1,000초와 2,000초에서 각각 비교하였다. 1,000초에 비해 2,000초에서 고체화 수소 체적 분율과 고체화량이 상대적으로 증가하는 것을 볼 수 있으며 이는 시간에 따라 열교환량이 증가하면서 고체화 수소의 생성량이 증가함을 의미한다. 또한 고체화 수소의 생성량에는 유량의 변화가 입구 온도의 변화보다 두드러지게 큰 영향을 끼침을 확인할 수 있다. 본 연구에서 생성한 고체화 수소의 최대 생성량은 4.6×10-3 m3이며 극저온 헬륨 가스의 다양한 유량 및 온도에 따른 액체 수소의 과냉각량 데이터베이스를 구축하였다. 향후 연구에서는 본 연구에서 확보한 다양한 액체 수소의 과냉각량 데이터베이스를 바탕으로 액체 수소와의 BOG 발생량을 비교하고 이를 바탕으로 액체 수소의 장기 저장을 위한 지연 시간(holding time) 등을 분석하고자 한다.
4. 결 론
본 연구에서는 헬륨 가스의 열교환을 통해 액체 수소로부터 생성되는 극저온 고체화 수소 및 과냉각 액화수소 평가 장치에 대한 수치 해석 기술을 개발하였다. 열교환에 사용되는 가스는 액체 수소의 온도를 낮추기 위하여 헬륨을 열교환 매체로 선택하였으며 열교환의 효율성을 높이기 위하여 나선 형태의 간접 열교환기를 제작하였다. 해석 결과 극저온 헬륨 가스가 파이프라인을 따라 이동함에 따라 액체 수소의 온도가 점점 낮아진다. 극저온 헬륨 가스와 충분한 열교환에 의해 액체 수소의 온도가 감소하고 파이프라인을 따라 고체화 수소가 생성되는 것을 확인할 수 있었다. 이러한 고체화 메커니즘 분석을 통해 본 연구에서는 극저온 헬륨 가스의 유량과 온도 변화에 따른 고체화 수소 생성량과 영향도를 분석하였다. 유량이 증가할수록 극저온 헬륨 가스의 온도는 열교환기에서 감소하게 되며 이에 따라 고체화 수소의 생성량이 증가하는 것을 알 수 있다. 입구 온도가 증가할수록 극저온 헬륨 가스의 온도는 열교환기에서 큰 변화가 없는 것으로 관찰되었으며 이에 따라 고체화 수소의 생성량은 눈에 띄는 큰 변화는 관찰되지 않았다. 또한 고체화 수소의 생성량에는 유량의 변화가 입구 온도의 변화보다 두드러지게 큰 영향을 끼침을 확인할 수 있었다. 향후 연구에서는 고체화 수소와 액체 수소와의 BOG 발생량을 비교하고 이를 바탕으로 액체 수소의 장기 저장을 위한 지연 시간(holding time) 등을 분석하고자 한다.
Acknowledgments
본 연구는 2025년도 정부(과학기술정보통신부)의 재원으로 국가과학기술연구회의 지원을 받아 수행된 한국전기연구원 기본 사업임(No. 25A01048). 본 연구는 2025년도 산업통상자원부 및 한국산업기술기획평가원(Korea Planning & Evaluation Institute of Industrial Technology) 연구비 지원에 의한 연구임(No. 25A02069).
References
-
M. Aasadnia and M. Mehrpooya, “Large-scale liquid hydrogen production methods and approaches: a review”, Applied Energy, Vol. 212, 2018, pp. 57-83.
[https://doi.org/10.1016/j.apenergy.2017.12.033]
-
D. Zivar, S. Kumar, and J. Foroozesh, “Underground hydrogen storage: a comprehensive review”, International Journal of Hydrogen Energy, Vol. 46, No. 45, 2021, pp. 23436-23462.
[https://doi.org/10.1016/j.ijhydene.2020.08.138]
-
D. Berstad, S. Gardarsdottir, S. Roussanaly, M. Voldsund, Y. Ishimoto, and P. Nekså, “Liquid hydrogen as prospective energy carrier: a brief review and discussion of underlying assumptions applied in value chain analysis”, Renewable and Sustainable Energy Reviews, Vol. 154, 2022, pp. 111772.
[https://doi.org/10.1016/j.rser.2021.111772]
-
H. Wang, B. Wang, J. Sun, Q. Pan, G. Luo, X. Tao, Y. He, J. Pfotenhauer, T. Jin, and Z. Gan, “Experimental and computational fluid dynamic investigation on thermal behaviors of liquid hydrogen during the no-vented storage process: a literature review”, International Journal of Hydrogen Energy, Vol. 57, 2024, pp. 822-843.
[https://doi.org/10.1016/j.ijhydene.2024.01.062]
-
K. Ohira, K. Nakamichi, and Y. Kihara, “Study on the development of a capacitance-type flowmeter for slush hydrogen”, Cryogenics, Vol. 43, No. 10-11, 2003, pp. 607-613.
[https://doi.org/10.1016/S0011-2275(03)00171-1]
-
K. Ohira, “Development of density and mass flow rate measurement technologies for slush hydrogen”, Cryogenics, Vol. 44, No. 1, 2004, pp. 59-68.
[https://doi.org/10.1016/j.cryogenics.2003.08.001]
-
Y. M. Park, “Literature research on the production, loading, flow, and heat transfer of slush hydrogen”, International Journal of Hydrogen Energy, Vol. 35, No. 23, 2010, pp. 12993-13003.
[https://doi.org/10.1016/j.ijhydene.2010.04.074]
-
K. E. Lamb and C. J. Webb, “A quantitative review of slurries for hydrogen storage - slush hydrogen, and metal and chemical hydrides in carrier liquids”, Journal of Alloys and Compounds, Vol. 906, 2022, pp. 164235.
[https://doi.org/10.1016/j.jallcom.2022.164235]
-
S. Xia, Y. Li, and F. Xie, “Influence of process parameters on production of slush hydrogen by freeze-thaw method”, International Journal of Hydrogen Energy, Vol. 48, No. 88, 2023, pp. 34520-34535.
[https://doi.org/10.1016/j.ijhydene.2023.05.241]
-
F. S. Xie, S. Q. Xia, Y. H. Zhu, Y. Ma, Y. Z. Li, L. Y. Xiong, and C. A. Lu, “Visual experimental study of slush hydrogen production by freezing-melting method”, Cryogenics, Vol. 131, 2023, pp. 103663.
[https://doi.org/10.1016/j.cryogenics.2023.103663]
-
W. Guo, F. Xie, Y. Yu, D. Yang, and Y. Li, “Phase field-lattice Boltzmann method investigation of particle morphology evolution in slush hydrogen during convective freezing and melting”, International Journal of Hydrogen Energy, Vol. 94, 2024, pp. 650-663.
[https://doi.org/10.1016/j.ijhydene.2024.11.013]
-
C. Lee, J. Ryu, G. Sohn, and S. Park, “Technical review on liquid/solid (slush) hydrogen production unit for long-term and bulk storage”, Journal of Hydrogen and New Energy, Vol. 32, No. 6, 2021, pp. 565-572.
[https://doi.org/10.7316/KHNES.2021.32.6.565]
-
S. Park, C. Lee, J. Ryu, and S. Hwang, “An economic analysis on slush hydrogen containing liquid and solid phase for long-term and large-scale storage”, Journal of Hydrogen and New Energy, Vol. 33, No. 3, 2022, pp. 247-254.
[https://doi.org/10.7316/KHNES.2022.33.3.247]
-
F. Ma, P. Zhang, and X. J. Shi, “Hydraulic and heat transfer characteristics of slush hydrogen in a circular pipe under terrestrial and microgravity conditions”, International Journal of Heat and Mass Transfer, Vol. 110, 2017, pp. 482-495.
[https://doi.org/10.1016/j.ijheatmasstransfer.2017.03.024]
-
T. Jin, Y. J. Li, Z. B. Liang, Y. Q. Lan, G. Lei, and X. Gao, “Numerical prediction of flow characteristics of slush hydrogen in a horizontal pipe”, International Journal of Hydrogen Energy, Vol. 42, No. 6, 2017, pp. 3778-3789.
[https://doi.org/10.1016/j.ijhydene.2016.09.054]
-
S. Xia, Y. Li, and F. Xie, “Numerical study on particle distribution characteristics of slush hydrogen in a cryogenic tank”, International Journal of Hydrogen Energy, Vol. 48, No. 40, 2023, pp. 15280-15291.
[https://doi.org/10.1016/j.ijhydene.2023.01.046]
-
S. Park, C. Lee, S. Chung, S. Hwang, J. Lim and D. J. Chang, “Feasibility study on production of slush hydrogen based on liquid and solid phase for long term storage”, Energies, Vol. 17, No. 17, 2024, pp. 4415.
[https://doi.org/10.3390/en17174415]
-
D. W. Ha, H. W. Noh, Y. M. Seo, T. H. Koo, and R. K. Ko, “Development of a condensing-type hydrogen liquefaction system for improving cooling efficiency and long-term storage”, International Journal of Hydrogen Energy, Vol. 49, Pt. B, 2024, pp. 1558-1571.
[https://doi.org/10.1016/j.ijhydene.2023.10.181]
-
D. W. Ha, H. W. Noh, T. H. Koo, R. K. Ko, and Y. M. Seo, “Experimental study on the liquid hydrogen zero boil-off in a liquefaction system with an automatic control technology”, International Journal of Hydrogen Energy, Vol. 83, 2024, pp. 933-945.
[https://doi.org/10.1016/j.ijhydene.2024.07.167]
-
H. Sattari, A. Mohebbi, M. M. Afsahi, and A. A. Yancheshme, “CFD simulation of melting process of phase change materials (PCMs) in a spherical capsule”, International Journal of Refrigeration, Vol. 73, 2017, pp. 209-218.
[https://doi.org/10.1016/j.ijrefrig.2016.09.007]