
미래 국방 무인 이동체를 위한 NaBH4 수소 발생 시스템 기반 연료전지 시스템 설계 및 검증
2024 The Korean Hydrogen and New Energy Society. All rights reserved.
Abstract
In this study, a fuel cell system for future defense unmanned vehicles was designed and validated. A Co/Al2O3-Ni foam catalyst for NaBH4 hydrolysis was characterized using several analytical methods. A NaBH4 hydrogen generation system with the Co/Al2O3-Ni foam catalyst continuously generated hydrogen at elevated reaction temperatures. The fuel cell system with the NaBH4 hydrogen generation system was designed and tested. The performance of the fuel cell system was comparable to that of the fuel cell system using pure hydrogen. Therefore, the fuel cell system with the NaBH4 hydrogen generation system is a suitable power source for future defense unmanned vehicles owing to its easy refueling and simple system.
Keywords:
Future defense, Unmanned vehicles, Sodium borohydride, Hydrogen generation system, Fuel cell system키워드:
미래 국방, 무인 이동체, 수소화붕소나트륨, 수소 발생 시스템, 연료전지 시스템1. 서 론
대한민국의 인구 감소에 따라 국방 병력의 규모 또한 감소하고 있다. 이에 따라 육상 무인 이동체, 해상 무인 이동체, 공중 무인 이동체 등의 다양한 무인 이동체가 미래 국방 전장 환경에서 활용될 주요 임무 시스템으로 주목받고 있다. 무인 이동체는 전장 환경에서 다양한 돌발 상황을 스스로 인지하고 대응하며 임무를 수행해야 한다. 또한 무인 이동체는 적에게 발각되지 않으면서 다양한 임무(정찰, 탐색, 전투 등)를 장시간 수행할 수 있어야 한다. 따라서 무인 이동체의 성공적인 임무 수행을 위해 에너지밀도가 높고 소음이 적으며 성능이 안정적인 동력원이 필요하다.
한화오션사(Seoul, Korea)는 배터리를 동력원으로 활용하는 해상 무인 이동체인 OKPO-600을 개발하였다1). 또한 DOK-ING사(Zagreb, Croatia)는 내연기관을 동력원으로 사용하는 육상 무인 이동체인 MVF-5를 개발하였고 BAE Systems사(Farnborough, UK)는 태양전지 기반의 공중 무인 이동체인 PHASA-35를 개발하였다. 이처럼 다양한 동력원들이 무인 이동체에 적용되었지만 이러한 동력원들은 낮은 에너지밀도(배터리), 심한 소음(내연기관), 환경 변화에 따른 성능의 불안정성(태양전지)과 같은 단점을 지니고 있다. 하지만 연료전지는 높은 에너지밀도, 적은 소음, 성능의 안정성과 같은 장점이 있어 무인 이동체용 동력원으로 활용하기 위해 많은 연구가 수행되어 왔다2,3).
다양한 연료전지 중에서 직접 메탄올 연료전지(direct methanol fuel cell, DMFC)와 고분자 전해질 연료전지(polymer electrolyte membrane fuel cell, PEMFC)가 무인 이동체용 주요 동력원으로 주목받고 있다. DMFC는 액상의 메탄올을 연료로 활용하기 때문에 연료의 재충전은 용이하지만 메탄올의 연료 교차 현상으로 인해 에너지밀도가 감소하는 단점을 지니고 있다4,5). 이에 반해 PEMFC는 DMFC에 비해 연료 교차 현상이 심각하지 않고 효율 및 출력밀도가 우수하다. 이러한 차이점으로 인해 PEMFC가 DMFC보다 무인 이동체용 동력원으로 적합하다.
PEMFC에는 주로 고압기체 저장법, 액화수소 저장법, 금속 수소화물, 화학 수소화물과 같은 수소 저장법이 활용된다. 고압기체 저장법과 액화수소 저장법은 수소 보급 지역이 충분히 구축되어 있지 않기 때문에 재충전이 어렵다. 금속 수소화물은 수소를 방출하기 위한 별도의 열공급 시스템이 필요하기 때문에 수소의 재충전 과정이 복잡하다. 하지만 화학 수소화물은 재충전이 용이하고 시스템이 단순한 장점으로 인해 타 수소 저장법에 비해 미래 국방 무인 이동체에 적합하다.
다양한 화학 수소화물 중에서 수소화붕소나트륨(sodium borohydride, NaBH4)은 안전성, 높은 수소 저장 용량(10.6 wt%)과 같은 장점을 지니고 있다. NaBH4는 아래 식 (1)에 의해 가수분해되어 수소를 방출한다. 수소가 필요 없는 상황에서 NaBH4의 자발적인 가수분해는 수소의 낭비를 유발한다. 따라서 수소의 낭비를 방지하기 위해 NaBH4를 알칼리 수용액의 형태로 저장해야 한다6). 일반적으로 전체 수용액 질량 대비 1-5 wt%의 수산화나트륨(sodium hydroxide, NaOH)을 활용하여 알칼리 NaBH4 수용액이 제작된다7,8).
(1) |
임무 수행을 위해 수소가 필요할 때 촉매 반응기에 NaBH4 수용액을 공급하여 수소를 발생시킬 수 있다. 즉 원활한 수소 발생을 위해서는 성능과 내구성이 우수한 촉매가 필수적이다. 많은 연구진들은 높은 가격의 귀금속 기반 촉매7-10)를 대체하기 위해 저렴한 Co 기반 촉매를 개발하고 있다11-19).
NaBH4 기반의 수소 발생 시스템은 식 (1)로부터 발생하는 반응열로 인해 별도의 열공급 없이 높은 반응 온도(>60℃)에 도달한다20-24). 높은 반응 온도를 활용하여 비교적 간단하고 안정적으로 많은 양의 수소를 공급할 수 있다. 일부 연구진들은 PEMFC를 위한 NaBH4 기반의 수소 발생 시스템을 연구하였다. Kim 등20)은 500 W급 연료전지를 위한 수소 발생 시스템의 시동 특성 및 반응기 설계 최적화에 관한 연구를 수행하였다. Oh와 Kwon21)은 200 W급 연료전지를 위한 수소 발생 시스템을 개발하였다. Park 등22)은 NaBH4의 농도가 수소 발생 시스템에 미치는 영향을 연구하고 가수분해 촉매의 성능 저하 원인을 분석하였다. 또한 Oh와 Kwon23)은 NaBH4의 가수분해 부산물인 메타붕산나트륨(sodium metaborate, NaBO2)의 석출 방지를 위한 다양한 첨가제가 수소 발생 시스템에 미치는 영향을 연구하였다. 이처럼 많은 연구가 수행되었지만 대부분 수소 발생 시스템 측면에서의 연구(수소 발생 시스템 설계 및 성능 평가 등)가 주로 수행되었다. 따라서 실제 무인 이동체에 활용할 수 있도록 수소 발생 시스템이 통합된 연료전지 시스템을 설계하고 연료전지 시스템의 활용성을 검증하는 연구가 필요하다.
본 연구에서는 미래 국방 무인 이동체에 적합한 연료전지 시스템을 설계한 후 연료전지 시스템의 활용성을 검증하고자 하였다. 먼저 Co/Al2O3-Ni foam 촉매를 분석하여 다양한 특성을 파악하고, 이를 NaBH4 기반 수소 발생 시스템에 적용하여 수소 발생 성능을 평가하였다. 또한 수소 발생 시스템과 PEMFC를 통합하여 무인 이동체에 적합한 연료전지 시스템을 설계하였다. 최종적으로 연료전지 시스템의 성능 평가를 수행하여 미래 국방 무인 이동체용 동력원으로써의 활용성을 검증하였다.
2. 실 험
2.1 시약 및 기구
본 연구를 위해 활용된 시약은 다음과 같다. Sigma-Aldrich사(St. Louis, MO, USA)의 나노 파우더형 산화알루미늄(Al2O3), 알루미늄 이소프로폭사이드(Al[OCH(CH3)2]3), 폴리비닐알코올([–CH2CHOH–]n)을 사용하였고, Samchun Chemical사(Seoul, Korea)의 염화코발트(CoCl2ㆍ6H2O), 증류수(H2O), 에탄올(C2H6O), NaBH4, 실리카겔(SiO2), NaOH, 70 wt% 질산 수용액(HNO3)을 사용하였다. 또한 Dong Jin Metaltech사(Busan, Korea)의 니켈폼(Ni foam)과 eSUN사(Shenzhen, China)의 PLA 필라멘트(PLA+)를 사용하였다.
또한 본 연구를 위해 활용된 실험 기구는 다음과 같다. Ika사(Königswinter, Germany)의 가열 교반기(RCT Basic), Inwha HNC사(Namyangju, Korea)의 고온 전기로, Tamiya사(Shizuoka, Japan)의 스프레이 건(Spray-Work Basic Airbrush), Omega사(Norwalk, CA, USA)의 부피 유량계(FMA-1605A), Graphtec사(Yokohama, Japan)의 데이터 수집 장치(GL240), Boxer사(Ottobeuren, Germany)의 펌프(9QQ), Itech사(New Taipei City, Taiwan)의 전원 공급기(IT6720), Prodigit사(New Taipei City, Taiwan)의 전자부하 장치(3330F), Horizon Fuel Cell Technologies사(Jurong East, Singapore)의 30 W급 연료전지 스택(H-30), Lugo Labs사(Busan, Korea)의 3D 프린터(LUGO L)를 사용하였다.
2.2 Co/Al2O3-Ni foam 촉매 제작
Fig. 1의 과정을 거쳐 Co/Al2O3-Ni foam 촉매를 제작하였다. 먼저 졸-겔법을 활용하여 Al2O3 코팅 용액을 제작하였다25). 158.8 g의 H2O를 360 rpm으로 교반하며 85℃까지 가열한 후, 가열된 H2O에 18 g의 알루미늄 이소프로폭사이드를 용해하였다. 알루미늄 이소프로폭사이드가 모두 용해된 후 6.18 g의 폴리비닐알코올을 첨가하여 30분 동안 교반하였다. 교반이 끝난 용액에 0.56 g의 70 wt% 질산수용액을 첨가한 후, 1시간 동안 해교 반응을 유지하며 상온으로 서서히 냉각하였다. 이후 해교 반응이 종료된 졸을 나노 파우더형 Al2O3 수용액(42.6 g Al2O3 + 88.9 g H2O)에 첨가하였다. 마지막으로 침전 방지를 위해 70 wt% 질산수용액을 소량 첨가 및 교반하며 코팅용액의 pH를 3.5-4.0의 범위에서 유지하였다.
다음으로 워시 코팅법을 활용하여 Ni foam (95 PPI, 너비 20.0 mm × 길이 45.0 mm × 두께 1.6 mm)표면에 나노 파우더형 Al2O3를 코팅하였다25). 앞서 제작한 Al2O3 코팅 용액에 Ni foam을 침지하여 충분히 흡수시킨 후, 스프레이 건으로 고압의 질소를 분사하여 Ni foam 세공 안에 있는 과도한 Al2O3 코팅 용액을 제거하였다. 과도한 Al2O3 코팅 용액이 제거된 Ni foam은 전기로를 활용하여 100℃에서 30분 동안 건조하였다. 이러한 코팅 과정을 5번 반복 수행하여 전체 촉매 지지체 질량 대비 23.6-24.4 wt%의 Al2O3가 코팅된 Al2O3-Ni foam을 제작하였다.
마지막으로 화학적 환원법을 활용하여 Al2O3-Ni foam 표면에 활성금속 Co를 담지하였다11). 40 g의 H2O에 17 g의 염화코발트를 용해하여 Co 용액을 제작하였다. 또한 24 g의 NaBH4와 1.2 g의 NaOH를 94.8 g의 H2O에 용해하여 Co 환원을 위한 NaBH4 용액을 제작하였다. 앞서 제작한 Al2O3-Ni foam을 Co 용액에 침지하여 충분히 흡수시킨 후, 스프레이 건으로 고압의 질소를 분사하여 Al2O3-Ni foam 세공 안에 있는 과도한 Co 용액을 제거하였다. 과도한 Co 용액이 제거된 Al2O3-Ni foam을 NaBH4 용액에 10초 동안 침지하여 Co를 환원하였다. 환원이 종료된 Co/Al2O3-Ni foam 촉매를 H2O로 세척한 후, 전기로를 활용하여 100℃에서 1시간 동안 건조하였다. 이러한 환원 과정을 5번 반복 수행하여 전체 촉매 질량 대비 20.6-23.1 wt%의 Co가 환원된 Co/Al2O3-Ni foam 촉매를 제작하였다.
2.3 촉매 분석
촉매의 특성을 파악하기 위해 다음과 같은 분석을 실시하였다. 촉매의 형태학적 특성과 표면 조성을 분석하기 위해 고분해능 전계 방사 주사전자현미경(JSM-7900F; JEOL, Tokyo, Japan)과 에너지 분산 X선 분광기(JSM-7900F)를 활용하였다. 촉매의 결정 구조를 분석하기 위해 X선 회절 분석기(X’Pert PRO MPD; Malvern Panalytical, Malvern, UK)를 활용하였다. 또한 촉매의 화학적 상태를 분석하기 위해 X선 광전자 분광기(AXIS SUPRA+; Kratos Analytical, Manchester, UK)를 활용하였다.
2.4 수소 발생 시스템 성능 평가
수소 발생 시스템의 성능을 평가하기 위해 Fig. 2(a)와 같이 실험 장치를 구성하였다. 수소 발생률의 변동폭(평균 수소 발생률 ± 10%)을 고려하여 정상 상태에서의 최소 수소 발생률이 420 mL/min (30 W급 연료전지 스택의 필요 수소 발생률)이 되도록 목표 수소 발생률을 470 mL/min으로 설정하였다20). 열 장의 Co/Al2O3-Ni foam 촉매를 반응기 내부 촉매 영역(가로 20.0 mm × 세로 20.0 mm × 높이 45.0 mm)에 투입하고 수소 발생률을 정확히 측정하기 위해 수소를 공급하여 실험 장치 내부의 공기를 제거하였다16). 공기를 모두 제거한 후 펌프를 활용하여 25℃의 NaBH4 수용액(15 wt% NaBH4 + 5 wt% NaOH + 80 wt% H2O)을 반응기에 일정하게 공급하였다. 반응기 내부의 촉매와 NaBH4 수용액이 반응하여 발생한 액상의 NaBO2는 중력에 의해 분리기에 별도로 분리되고 수소는 실리카겔을 거쳐 수분이 제거된다. 수분이 제거된 수소의 부피 유량은 부피 유량계를 활용하여 측정하였고 반응기 상단부, 중단부, 하단부의 온도는 각각 K-type 열전대를 활용하여 측정하였다. 측정한 수소 발생률과 온도는 데이터 수집 장치를 이용하여 컴퓨터에 저장하였다.
2.5 연료전지 시스템 성능 평가
연료전지 시스템의 활용성을 검증하고자 Fig. 2(b)의 실험 장치를 활용하여 성능 평가를 수행하였다. 고압의 가스 실린더에 저장된 순수한 수소 또는 2.4절의 과정을 거쳐 발생된 NaBH4 기반 수소를 연료전지에 동일하게 공급하여 연료전지 시스템의 성능을 측정하였다. 먼저 부하 변동에 대한 연료전지 시스템의 성능을 평가하기 위해 0.5 A 간격(0-3.0 A의 범위)으로 각 전류에서 1분 동안 전압을 측정하였다. 또한 연료전지 시스템의 성능 안정성을 평가하기 위해 2.5 A의 단일 부하를 30분 동안 부여하며 전압을 측정하였다. 측정한 전압은 데이터 수집 장치를 이용하여 컴퓨터에 저장하였다.
3. 결과 및 고찰
3.1 Co/Al2O3-Ni foam 촉매 특성 분석
Fig. 3은 주사전자현미경으로 촬영한 Co/Al2O3-Ni foam 촉매의 표면 이미지이다. Co/Al2O3-Ni foam 촉매는 표면에 코팅된 Al2O3와 환원된 Co로 인해 전반적으로 다공성의 거친 표면을 가졌다19).
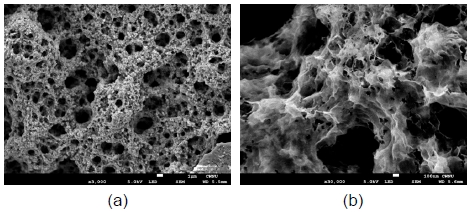
Surface morphology of Co/Al2O3-Ni foam catalyst. (a) Catalyst surface (3,000×) and (b) catalyst surface (30,000×)
Fig. 4는 Co/Al2O3-Ni foam 촉매의 표면을 에너지 분산 X선 분광기 맵핑으로 분석한 결과이다. 촉매 표면은 주로 Co, Al, O, Ni로 구성되어 있었으며 에너지 분산 X선 분광기 맵핑을 통해 Co가 비교적 균일하게 분산 및 환원된 것을 확인할 수 있었다.
Table 1에 촉매 표면을 구성하는 주요 원소의 구성비를 정리하였다. Co의 비율은 29.66 at%로 높았지만 Al과 Ni의 비율은 각각 0.10 at%와 0.39 at%로 비교적 낮았다. 이는 Al2O3-Ni foam의 표면에 Co가 완전히 도포되어 Al과 Ni이 거의 측정되지 않았기 때문으로 사료된다. Al의 비율은 0.10 at%로 낮았지만 O의 비율은 69.85 at%로 비교적 높았다. 즉 촉매 표면의 O는 Al2O3로부터 기인한 것이 아니라 Co가 촉매 보관 과정에서 산화된 것으로 판단된다.
Co/Al2O3-Ni foam 촉매의 결정 구조를 분석하여 Fig. 5에 제시하였다. Co/Al2O3-Ni foam 촉매는 산화된 Ni과 Ni로 구성되었다26). 촉매 지지체로 활용한 Ni foam이 촉매 보관 과정에서 일부 산화되어 산화된 Ni과 Ni이 함께 측정된 것으로 판단된다. 산화된 Ni은 36.7°과 43.0°의 피크로 구성되었고 이는 각각 (110)면과 (200)면의 결정 구조를 나타내었다26). 또한 Ni은 44.4°와 51.8°의 피크로 구성되었고 이는 각각 (111)면과 (200)면의 결정 구조를 나타내었다14). 하지만 이전 연구에서의 분석 결과와 다르게 Co의 결정 구조는 측정되지 않았다13). 이는 본 연구에서 사용된 촉매의 Co가 비정질 구조를 가지고 있기 때문으로 사료된다15).
Fig. 6은 Co/Al2O3-Ni foam 촉매의 화학적 상태를 분석한 결과이다. Co/Al2O3-Ni foam 촉매에서 주로 Co, O가 측정되었으며 촉매 반응에서 중요한 활성금속인 Co의 화학적 상태를 자세히 분석하였다. Co 2p스펙트럼은 Co 2p1/2와 Co 2p3/2로 구성되었고 각각의 스펙트럼은 위성 피크(Co 2p1/2, 802.3 eV; Co 2p3/2, 783.5 eV)와 산화된 Co 피크(Co 2p1/2, 797.1 eV; Co 2p3/2, 781.1 eV)로 구성되어 있었다12,14). 촉매 표면의 Co가 보관 과정에서 산화되어 산화된 Co 피크가 측정된 것으로 판단된다18).
3.2 수소 발생 시스템 성능 평가
Fig. 7은 수소 발생 시스템의 성능 평가 결과이다. 목표 수소 발생률을 470 mL/min으로 설정하였지만 실험에 사용한 NaBH4 수용액의 질량을 통해 계산한 이론 수소 발생률은 474 mL/min이었다. 10-30분 구간에서는 목표 수소 발생률에 비해 과도한 수소 발생률이 측정되었다. 이는 0-10분 구간에서 낮은 반응온도에 의해 분해되지 못하고 촉매 표면에 축적된 NaBH4가 10-30분 구간에서 반응 온도가 증가함에 따라 한꺼번에 분해되었기 때문으로 판단된다24). 30분 이후의 구간에서는 목표했던 수소 발생률 범위(420-510 mL/min)에서 비교적 일정하게 수소를 발생하였다. 반응기의 온도는 10분 이후의 구간에서 각 부분의 최대 반응 온도(상단부, 93℃; 중단부, 88℃; 하단부, 85℃)에 도달하는 경향을 보였다. 최대 반응 온도에 도달한 반응기는 반응이 지속되는 동안 일정하게 반응 온도를 유지하였다.
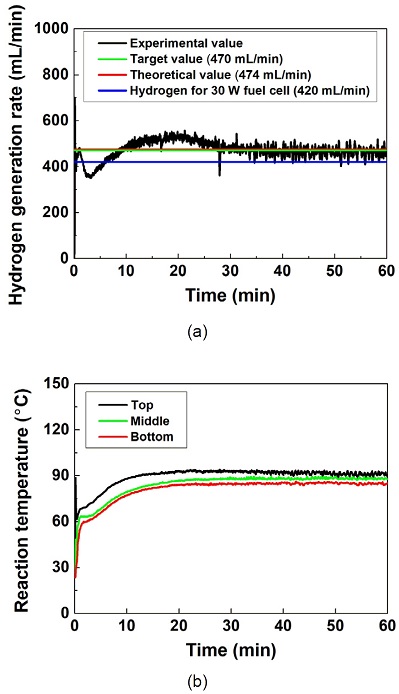
Performance evaluation of hydrogen generation system. (a) Hydrogen generation rate and (b) reaction temperature
본 연구의 NaBH4 기반 수소 발생 시스템은 1시간 동안 목표한 수소 발생률을 안정적으로 발생시켰다. 또한 반응기의 온도도 고온에서 안정적으로 유지하였다. 따라서 본 수소 발생 시스템은 미래 국방 무인 이동체용 연료전지 시스템의 수소 공급원으로 활용하기에 적합하다고 판단된다.
3.3 연료전지 시스템 설계
Fig. 8과 같이 연료전지 시스템을 설계하였다. 연료전지 시스템의 프레임(가로 220 mm × 세로 160 mm × 높이 150 mm × 두께 5 mm)은 융합 증착 모델링 방식의 3D 프린터와 폴리락타이드 재질의 필라멘트를 활용하여 출력하였다. 또한 폴리에틸렌 재질의 용기를 활용하여 NaBH4 수용액, 분리기, 실리카겔 용기를 경량화하였다. NaBH4 가수분해의 부산물인 액상의 NaBO2는 Fig. 9와 같이 부피가 큰 거품형태로 발생하고 이는 분리기를 금방 가득 채우게 된다. 이러한 거품은 파이프라인 내부의 유동을 차단하여 수소 발생기의 원활한 작동을 방해할 수 있다. 따라서 소포제 역할을 수행하는 에탄올을 분리기에 소량 첨가하여 거품 형태 부산물의 축적을 방지하였다17,27). 펌프와 반응기는 수소 발생 시스템의 요소들을 그대로 활용하였으며 펌프의 작동을 위한 전력원은 리튬폴리머 배터리를 활용하였다.
3.4 연료전지 시스템 성능 평가
연료전지 시스템의 성능 평가 결과를 Fig. 10에 정리하였다. 다양한 부하에 대한 연료전지 시스템 성능평가 결과에서 순수 수소를 공급하였을 때의 동력과 NaBH4 기반 수소를 공급하였을 때의 동력은 거의 동일하였다. 또한 안정성 평가에서 NaBH4 기반 수소를 공급하였을 때의 평균 동력(16.9 W)은 순수 수소를 공급하였을 때의 평균 동력(17.6 W)보다 4% (0.7 W)만큼 낮았다.
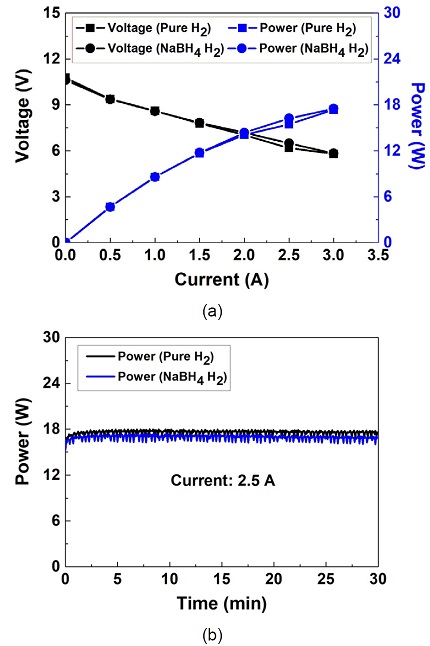
Performance evaluation of fuel cell system. (a) Various load test and (b) stability test (current 2.5 A)
부하 변동에 대한 NaBH4 수소 발생 시스템 기반 연료전지 시스템의 성능은 순수 수소 기반 연료전지 시스템의 성능과 유사하였다. 또한 30분간 수행된 안정성 평가에서도 두 연료전지 시스템의 성능은 큰 차이가 없었다. 따라서 본 연료전지 시스템은 미래 국방 무인 이동체용 동력원으로써 활용 가능성이 우수하다고 판단된다.
4. 결 론
본 연구에서는 미래 국방 무인 이동체를 위한 연료전지 시스템을 설계하고 연료전지 시스템의 활용성을 검증하였다. Co/Al2O3-Ni foam 촉매 표면의 Co는 균일하게 분산 및 환원되어 있었다. Co/Al2O3-Ni foam 촉매를 활용하는 NaBH4 기반 수소 발생 시스템은 1시간 동안 높은 반응 온도를 유지하며 목표한 수소 발생률을 안정적으로 유지하였다. 또한 NaBH4 기반 수소 발생 시스템을 수소 공급원으로 활용하여 연료전지 시스템을 설계하였다. 본 연구의 연료전지 시스템은 순수 수소를 활용하는 연료전지 시스템과 성능이 유사하였다. 따라서 본 연구의 연료전지 시스템은 연료 재충전의 용이성, 단순한 시스템 구성 등의 다양한 장점으로 인해 미래 국방 무인 이동체에 충분히 활용될 수 있을 것으로 판단된다.
Acknowledgments
이 논문은 2023-2024년도 국립창원대학교 자율연구과제 연구비 지원으로 수행된 연구 결과입니다.
References
- Y. S. Joo, K. N. Jo, J. I. Kim, K. M. Lee, S. G. Han, M. C. Park, J. S. Ryu, J. S. Woo, and M. G. Han, “Design and experiment of coastal autonomous underwater vehicle 'OKPO-600'”, Proceedings of the KOSME Conference, 2009, pp. 339-340. Retrieved from https://www.dbpia.co.kr/journal/articleDetail?nodeId=NODE01210812, .
-
T. Kim and S. Kwon, “Design and development of a fuel cell-powered small unmanned aircraft”, International Journal of Hydrogen Energy, Vol. 37, No. 1, 2012, pp. 615-622.
[https://doi.org/10.1016/j.ijhydene.2011.09.051]
-
N. Lapeña-Rey, J. A. Blanco, E. Ferreyra, J. L. Lemus, S. Pereira, and E. Serrot, “A fuel cell powered unmanned aerial vehicle for low altitude surveillance missions”, International Journal of Hydrogen Energy, Vol. 42, No. 10, 2017, pp. 6926-6940.
[https://doi.org/10.1016/j.ijhydene.2017.01.137]
-
J. Lee, S. Lee, D. Han, G. Gwak, and H. Ju, “Numerical modeling and simulations of active direct methanol fuel cell (DMFC) systems under various ambient temperatures and operating conditions”, International Journal of Hydrogen Energy, Vol. 42, No. 3, 2017, pp. 1736-1750.
[https://doi.org/10.1016/j.ijhydene.2016.09.087]
-
T. H. Kin, W. Y. Shieh, C. C. Yang, and G. Yu, “Estimating the methanol crossover rate of PEM and the efficiency of DMFC via a current transient analysis”, Journal of Power Sources, Vol. 161, No. 2, 2006, pp. 1183-1186.
[https://doi.org/10.1016/j.jpowsour.2006.06.009]
- M. M. Kreevoy and R. W. Jacobson, “The rate of decomposition of NaBH4 in basic aqueous solutions”, Ventron Alembic, Vol. 15, No. 2, 1979, pp. 2-3.
-
Y. Liang, H. B. Dai, L. P. Ma, P. Wang, and H. M. Cheng, “Hydrogen generation from sodium borohydride solution using a ruthenium supported on graphite catalyst”, International Journal of Hydrogen Energy, Vol. 35, No. 7, 2010, pp. 3023-3028.
[https://doi.org/10.1016/j.ijhydene.2009.07.008]
-
J. Zhang, Y. Li, L. Yang, F. Zhang, R. Li, and H. Dong, “Ruthenium nanosheets decorated cobalt foam for controllable hydrogen production from sodium borohydride hydrolysis”, Catalysis Letters, Vol. 152, 2022, pp. 1386-1391.
[https://doi.org/10.1007/s10562-021-03730-5]
-
V. G. Minkina, S. I. Shabunya, V. I. Kalinin, and A. Smirnova, “Hydrogen generation from sodium borohydride solutions for stationary applications”, International Journal of Hydrogen Energy, Vol. 41, No. 22, 2016, pp. 9227-9233.
[https://doi.org/10.1016/j.ijhydene.2016.03.063]
-
A. Uzundurukan and Y. Devrim, “Hydrogen generation from sodium borohydride hydrolysis by multi-walled carbon nanotube supported platinum catalyst: a kinetic study”, International Journal of Hydrogen Energy, Vol. 44, No. 33, 2019, pp. 17586-17594.
[https://doi.org/10.1016/j.ijhydene.2019.04.188]
-
J. Lee, K. Y. Kong, C. R. Jung, E. Cho, S. P. Yoon, J. Han, T. G. Lee, and S. W. Nam, “A structured Co-B catalyst for hydrogen extraction from NaBH4 solution”, Catalysis Today, Vol. 120, No. 3-4, 2007, pp. 305-310.
[https://doi.org/10.1016/j.cattod.2006.09.019]
-
S. Fang, Y. Chen, S. Wang, J. Xu, Y. Xia, F. Yang, Y. Wang, J. Lao, C. Xiang, F. Xu, L. Sun, Y. Zou, and H. Pan, “Modified CNTs interfacial anchoring and particle-controlled synthesis of amorphous cobalt-nickel-boron alloy bifunctional materials for NaBH4 hydrolysis and supercapacitor energy storage”, Journal of Alloys and Compounds, Vol. 936, 2023, pp. 167990.
[https://doi.org/10.1016/j.jallcom.2022.167990]
-
T. H. Oh and S. Kwon, “Effect of bath composition on properties of electroless deposited Co-P/Ni foam catalyst for hydrolysis of sodium borohydride solution”, International Journal of Hydrogen Energy, Vol. 37, No. 22, 2012, pp. 17027-17039.
[https://doi.org/10.1016/j.ijhydene.2012.08.083]
-
Y. Wei, M. Wang, W. Fu, L. Wei, X. Zhao, X. Zhou, M. Ni, and H. Wang, “Highly active and durable catalyst for hydrogen generation by the NaBH4 hydrolysis reaction: CoWB/NF nanodendrite with an acicular array structure”, Journal of Alloys and Compounds, Vol. 836, 2020, pp. 155429.
[https://doi.org/10.1016/j.jallcom.2020.155429]
-
X. Luo, L. Sun, F. Xu, Z. Cao, J. Zeng, Y. Bu, C. Zhang, Y. Xia, Y. Zou, K. Zhang, and H. Pan, “Metal boride-decorated CoNi layered double hydroxides supported on muti-walled carbon nanotubes as efficient hydrolysis catalysts for sodium borohydride”, Journal of Alloys and Compounds, Vol. 930, 2023, pp. 167339.
[https://doi.org/10.1016/j.jallcom.2022.167339]
-
S. M. Yun, T. H. Lee, and T. H. Oh, “A study on characteristics of NaBH4 hydrolysis using Co/Al2O3 nanopowder catalyst”, Journal of Hydrogen and New Energy, Vol. 33, No. 4, 2022, pp. 343-352.
[https://doi.org/10.7316/KHNES.2022.33.4.343]
-
H. R. Lee, D. H. Park, W. Ju, I. C. Na, and K. P. Park, “Characteristics of byproduct after NaBH4 hydrolysis reaction using unsupported catalyst”, Korean Chemical Engineering Research, Vol. 55, No. 1, 2017, pp. 13-18.
[https://doi.org/10.9713/kcer.2017.55.1.13]
-
H. Li, B. Li, Y. Zou, C. Xiang, H. Zhang, F. Xu, L. Sun, and K. He, “Modulating valence band to enhance the catalytic activity of Co-Cr-B/NG for hydrolysis of sodium borohydride”, Journal of Alloys and Compounds, Vol. 924, 2022, pp. 166556.
[https://doi.org/10.1016/j.jallcom.2022.166556]
-
Y. Liang, P. Wang, and H. B. Dai, “Hydrogen bubbles dynamic template preparation of a porous Fe-Co-B/Ni foam catalyst for hydrogen generation from hydrolysis of alkaline sodium borohydride solution”, Journal of Alloys and Compounds, Vol. 491, No. 1-2, 2010, pp. 359-365.
[https://doi.org/10.1016/j.jallcom.2009.10.183]
-
H. Kim, T. H. Oh, and S. Kwon, “Simple catalyst bed sizing of a NaBH4 hydrogen generator with fast startup for small unmanned aerial vehicles”, International Journal of Hydrogen Energy, Vol. 41, No. 2, 2016, pp. 1018-1026.
[https://doi.org/10.1016/j.ijhydene.2015.11.134]
-
T. H. Oh and S. Kwon, “Performance evaluation of hydrogen generation system using NaBH4 hydrolysis for 200 W fuel cell powered UAV”, Journal of the Korean Society for Aeronautical & Space Sciences, Vol. 43, No. 4, 2015, pp. 296-303.
[https://doi.org/10.5139/JKSAS.2015.43.4.296]
-
D. I. Park, S. U. Kim, D. M. Kim, and T. G. Kim, “Performance evaluation of hydrogen generator for fuel cell unmanned aircraft”, Journal of the Korean Society for Aeronautical & Space Sciences, Vol. 39, No. 7, 2011, pp. 627-633.
[https://doi.org/10.5139/JKSAS.2011.39.7.627]
-
T. Oh and S. Kwon, “Effect of additives for prevention of NaBO2 precipitation on hydrogen generation properties of NaBH4 hydrolysis”, Journal of Hydrogen and New Energy, Vol. 24, No. 1, 2013, pp. 1-11.
[https://doi.org/10.7316/KHNES.2013.24.1.001]
-
T. H. Oh and S. Kwon, “Performance evaluation of hydrogen generation system with electroless-deposited Co-P/Ni foam catalyst for NaBH4 hydrolysis”, International Journal of Hydrogen Energy, Vol. 38, No. 15, 2013, pp. 6425-6435.
[https://doi.org/10.1016/j.ijhydene.2013.03.068]
-
D. Park, D. J. Moon, and T. Kim, “Steam-CO2 reforming of methane on Ni/γ-Al2O3-deposited metallic foam catalyst for GTL-FPSO process”, Fuel Processing Technology, Vol. 112, 2013, pp. 28-34.
[https://doi.org/10.1016/j.fuproc.2013.02.016]
-
M. Huang, F. Li, J. Y. Ji, Y. X. Zhang, X. L. Zhao, and X. Gao, “Facile synthesis of single-crystalline NiO nanosheet arrays on Ni foam for high-performance supercapacitors”, CrystEngComm, Vol. 16, No. 14, 2014, pp. 2878-2884.
[https://doi.org/10.1039/C3CE42335B]
- H. L. Lee and J. H. Lee, “Development of multi-functional mulch papers and evaluation of their performance (part 3) - defoaming treatment during trial production of mulch papers and their influence on wet end system -”, Journal of Korea Technical Association of The Pulp and Paper Industry, Vol. 32, No. 3, 2000, pp. 25-31. Retrieved from https://www.dbpia.co.kr/journal/articleDetail?nodeId=NODE00295473, .