
Ru 촉매에서의 암모니아 부분산화에 대한 연구
2022 The Korean Hydrogen and New Energy Society. All rights reserved.
Abstract
Green ammonia is a promising renewable energy carrier. Green ammonia can be used in various energy conversion devices (e.g., engine, fuel cell, etc.). Ammonia has to be fed with hydrogen for start-up and failure protection of some energy conversion devices. Ammonia can be converted into hydrogen by decomposition and partial oxidation. Especially, partial oxidation has the advantages of fast start-up, thermally self-sustaining operation and compact size. In this paper, thermodynamics, start-up and operation characteristics of ammonia partial oxidation were investigated. O2/NH3 ratio, ammonia flow rate and catalyst volume were varied as operation parameters. In thermodynamic analysis, ammonia conversion was maximized in the O2/NH3 range from 0.10 to 0.15. Ammonia partial oxidation reactor was successfully started using 12 V glow plug. At 0.13 of O2/HN3 ratio and 10 LPM of ammonia flow rate, ammonia partial oxidation reactor showed 90% of ammonia conversion over commercial Ru catalyst. In addition, Increasing O2/NH3 ratio from 0.10 to 0.13 was more effective for high ammonia conversion than increasing catalyst volume at 0.10 of O2/NH3.
Keywords:
Ammonia, Partial oxidation, Auto-thermal cracking, Ru catalyst, Hydrogen키워드:
암모니아, 부분산화, 자열 분해, Ru 촉매, 수소1. 서 론
최근 암모니아가 무탄소 연료로서 수송 분야와 발전 분야에서 많은 관심을 받고 있다1). 암모니아는 탄소를 포함하지 않지만 암모니아를 생산하는 하버-보슈 공정(Haber-Bosch process)에서는 천연가스를 개질하여 수소를 공급하여 CO2가 발생한다. 반면, 재생 에너지로 생산한 수소를 하버-보슈 공정에 공급하면 CO2 발생이 없는 그린암모니아를 생산할 수 있다. 재생에너지가 풍부한 호주와 사우디아라비아 등에서는 수전해와 연계하여 그린암모니아를 생산하기 위한 실증이 진행되고 있다2). 암모니아는 상온 10 bar 이하에서 액화하여 운송과 저장이 용이하다3). 또한 비료 산업에서 구축된 암모니아 생산, 저장 및 수송에 필요한 기반 시설의 활용이 가능하다. 다만, 암모니아는 독성 물질로 취급에 주의가 필요하다.
그린암모니아를 엔진과 연료전지 등에 사용하여 CO2 배출을 저감하기 위한 연구가 진행되고 있다4). 암모니아를 엔진과 연료전지에 사용하기 위해서는 암모니아의 전부 또는 일부를 수소로 전환하여 공급해야 한다. 암모니아는 분해 반응과 부분산화 반응을 통해 수소로 전환될 수 있다. 암모니아 분해 반응식은 식 (1)과 같다. 암모니아는 1 mol이 분해되면 1.5 mol의 수소와 0.5 mol의 질소가 생성된다.
(1) |
반면, 암모니아 부분산화 반응은 공급된 산소가 모두 소모된다고 가정하면 식 (2)와 같이 나타낼 수 있다.
(2) |
여기서 oxygen to ammonia ratio (OAR)은 O2/NH3비이며, x는 암모니아 전환율을 나타낸다.
암모니아는 O2/NH3비가 0.75인 조건에서 완전산화된다. 암모니아 부분산화 반응에서는 공기 중 질소에 의해 희석되고 암모니아 일부가 연소되어 생성되는 수소 농도가 낮아진다. 하지만 암모니아 부분산화는 발열 반응으로 외부 열원이 없이 운전이 가능하여 빠른 시동과 소형 시스템에 적합하다.
암모니아 엔진은 암모니아의 낮은 발열량과 느린 화염 전파 속도로 인하여 이종의 연료와 혼소엔진 형태로 개발된다5). 특히, Frigo 등6-8)과 Comotli와 Frigo9)는 15 kW SI 엔진에 암모니아 분해 반응기를 장착하여 암모니아와 수소 혼소를 위한 최적의 수소 혼합비를 찾았다. 하지만 배기가스로 암모니아 분해 장치를 가열하고 작동하는데 약 10분 이상이 소요되었다9). 반면, Koike 등10)은 3,685 cc SI 엔진에 암모니아 부분산화 반응기를 적용하여 3초 이내에서 빠르고 안정적인 냉시동이 가능한 것을 확인하였다. 연료전지에도 암모니아를 사용하기 위해서도 적정한 형태로의 전환이 필요하다. 고온에서 작동하는 고체산화물 연료전지(solid oxide fuel cell)는 셀 단위에서는 암모니아를 직접 활용이 가능한 것으로 알려져 있다. 하지만 Yang 등11)은 암모니아가 공급되면서 600℃와 700℃에서 반복적으로 작동된 고체산화물 연료전지가 질화(nitriding)에 의해 파손되는 것을 보고하였다. 암모니아 부분산화 반응기가 적용된 고체산화물 연료전지의 스택 효율은 29.1%로 암모니아를 직접 공급하거나 분해 반응기를 설치한 경우보다 낮았다11-14). 하지만 부분산화 반응기를 이용하면 시동 과정의 저온 영역에서 수소를 공급해 줌으로써 질화를 방지할 수 있을 것으로 판단된다. 암모니아 부분산화 반응기를 엔진과 연료전지에 사용하기 위해서는 시동 특성과 암모니아 전환을 최대화할 수 있는 운전 조건에 대한 연구가 필요하다.
본 연구에서는 암모니아 부분산화 반응의 열역학적 특성, 시동 특성 및 운전 특성을 살펴보았다. 특히, 상용 Ru 촉매에서 O2/NH3비, 공급유량 및 촉매량에 따른 암모니아 부분산화에 대한 실험을 하였다.
2. 실 험
Fig. 1은 암모니아 부분산화 반응기의 평가에 사용된 실험 장치의 모식도를 나타낸다. 암모니아 부분산화 반응기는 25.4 mm stainless steel관으로 제작하였다. 반응기에는 촉매를 장입하기 위하여 타공판을 설치하였다. 타공판으로부터 19 mm 위치에는 촉매를 가열하여 시동하기 위한 차량용 12 V 글로우 플러그(glow plug)를 설치하였다. 타공판으로부터 40 mm, 100 mm 및 160 mm 위치에는 열전대를 설치하여 반응기 내부 온도를 모니터링하였다. 반응기 외부는 세라믹 울로 단열하였다. 암모니아 부분산화 반응기에는 직경 2.97±0.26 mm 구형의 상용 Ru 촉매를 장입하였다. 반응기 상단과 하단에는 압력계를 설치하여 반응기 내 압력을 모니터링하였다. 암모니아 부분산화 반응기에 암모니아와 공기는 mass flow controller (MS3150V, Line tech inc., Daejeon, Korea)를 사용하여 공급하였다. 반응을 거치고 난 가스의 암모니아 농도는 fourier-transform infrared spectroscopy (Antaris IGS, Thermo Fisher Scientific Inc., Waltham, MA, USA)를 이용하여 측정하였다.
암모니아 전환율과 분해 효율은 식 (3)과 식 (4)와 측정된 암모니아 농도로 계산하였다. 수소, 질소 및 수증기의 농도는 식 (2)로부터 측정된 암모니아 농도를 사용하여 환산하였다.
(3) |
(4) |
3. 결과 및 고찰
3.1 암모니아 부분산화의 열역학적 특성
Fig. 2는 암모니아 부분산화 반응의 열역학적 평형에서의 암모니아 전환율, 가스 조성 및 단열 반응온도를 나타낸다. 단열 조건에서 열역학적 평형의 가스 조성을 O2/NH3비를 0.05에서 0.75까지 증가시키며 Aspen Plus를 이용하여 계산하였다. Fig. 2(a)는 열역학적 평형에서의 암모니아의 전환율을 나타낸다. 암모니아 전환율은 O2/NH3비가 0.05에서 0.15로 증가함에 따라 약 40%에서 99%로 증가하여 0.15 이상의 O2/NH3비에서 대부분의 암모니아가 전환되는 것을 확인하였다. 또한 O2/NH3비가 증가함에 따라 산화 반응에 의해 소모되는 암모니아가 비례하여 증가하게 된다. 따라서, 암모니아 전환율과 산화 반응에 의한 전환율의 차이가 큰 0.10에서 0.20의 O2/NH3비 영역에서 암모니아 부분산화 반응기를 운전하는 것이 분해 효율을 높일 수 있을 것으로 판단된다. Fig. 2(b)는 열역학적 평형에서의 가스 조성을 나타낸다. 암모니아 전환율과 같이 암모니아 농도는 O2/NH3비가 0.05에서 0.15의 영역에서 대부분 전환되었다. 수소 농도도 O2/NH3비가 0.10에서 0.15인 영역에서 약 45-46% 수준으로 가장 높았다. 0.15이상의 O2/NH3비에서는 추가적으로 분해될 수 있는 암모니아가 존재하지 않아 수소가 연소되어 농도가 감소하였다. 또한, 높은 O2/NH3비에서 공급되는 질소와 생성되는 수증기에 의한 희석 효과가 증가함을 알 수 있다. Fig. 2(c)는 단열 조건에서 열역학적 평형에서와 암모니아 전환율에 따른 반응 온도를 나타낸다. 단열 반응 온도는 O2/NH3비가 높을수록 산화 반응과 함께 증가한다. 열역학 평형에서 단열 반응 온도는 0.15의 O2/NH3비에서 약 376℃가 된다. 다만, 암모니아 전환율이 80%와 90%로 감소하면 암모니아 분해에 의한 흡열 반응이 진행되지 않아 단열 반응 온도는 각각 약 438℃와 506℃로 증가하게 된다.
3.2 암모니아 부분산화 반응기의 시동 특성
Fig. 3은 암모니아 부분산화 반응기의 시동 과정에서 암모니아 농도와 반응기 내부 온도를 나타낸다. 암모니아 부분산화 반응기의 시동은 상용 Ru 촉매를 30 mL 장입하고 0.10의 O2/NH3비에서 암모니아를 10 LPM으로 공급하면서 진행되었다. Fig. 3(a)는 암모니아 부분산화 반응기의 시동 과정에서 암모니아 농도의 변화를 나타낸다. 암모니아와 공기가 공급되고 있는 상황에서 약 2분간 측정되는 가스 조성을 안정화시키고 시동용 글로우 플러그를 30초간 작동하여 촉매를 가열하였다. 암모니아 농도는 가열 시작 후 1분간 30%까지 급격히 감소하였다. 해당 영역에서는 암모니아의 산화 반응에 의해 직접적으로 가열된 촉매에서 암모니아가 반응한 결과로 보인다. 반면, 3분에서 8분까지는 암모니아가 추가적으로 분해되어 암모니아 농도가 약 15%에서 안정화되었다. Fig. 3(b)는 암모니아 부분산화 반응기의 시동 과정에서 반응기 온도를 나타낸다. 대부분의 암모니아가 전환된 2분에서 3분 사이에서는 40 mm의 촉매층 온도는 100℃ 이하로 측정되었다. 이는 반응 속도가 빠른 암모니아 산화 반응이 온도가 측정되지 않은 0 mm에서 40 mm 이내의 촉매층에서 진행된 것을 나타낸다. 8분 이후에서는 40 mm와 100 mm의 촉매층의 온도가 각각 약 330℃와 220℃로 촉매층의 온도가 상승하면서 추가적인 암모니아 분해 반응이 진행된 것으로 보인다. 이러한 암모니아 부분산화 반응기의 시동 특성을 활용하여 1분 내에 암모니아를 분해하여 수소를 공급할 수 있을 것으로 판단된다.
3.3 O2/NH3비에 따른 암모니아 부분산화 반응 특성
Fig. 4는 O2/NH3비에 따른 암모니아 부분산화 반응 특성을 나타낸다. 실험은 상용 Ru 촉매가 30 mL 장입된 반응기에 암모니아를 10 LPM으로 공급하면서 O2/NH3비를 0.10에서 0.13까지 증가시켰다. Fig. 4(a)는 O2/NH3비에 따른 암모니아 전환율과 분해 효율을 나타낸다. 암모니아 전환율은 O2/NH3비가 0.10에서 0.13까지 증가함에 따라 61%에서 90%까지 증가하였다. 산화에 의한 암모니아 전환율도 산소의 공급 증가에 따라 13%에서 17%로 증가하게 된다. 전체 암모니아 전환율이 산화에 의한 암모니아 전환율보다 가파르게 증가하는 것을 바탕으로 O2/NH3비가 증가함에 따라 암모니아가 분해되어 수소가 생성되는 것을 알 수 있다. 이때 최대 분해 효율은 O2/NH3비가 0.13인 조건에서 83%로 측정되었다. Fig. 4(b)는 O2/NH3비에 따른 암모니아 부분산화 반응의 가스 조성을 나타낸다. O2/NH3비가 0.10에서 0.13으로 증가하면서 암모니아 농도는 18%에서 4%로 감소하였으며, 암모니아 농도에서 환산된 수소 농도는 39%에서 48%로 증가하였다. O2/NH3비가 0.14 이상으로 공기가 공급되는 조건에서는 암모니아의 농도가 측정 범위 미만으로 감소하여 측정이 불가능하였다. O2/NH3비의 증가에 따라 공급되는 질소와 산화 반응에 의한 수증기의 생성이 증가한다. 하지만 0.10에서 0.13까지의 O2/NH3비의 영역에서는 암모니아의 전환율이 급격하게 증가하여 질소와 수증기에 의해 환산된 수소 농도는 감소하지 않았다. Fig. 4(c)는 O2/NH3비에 따른 암모니아 부분 산화반응기의 내부 온도를 나타낸다. O2/NH3비가 증가함에 따라 산화에 의한 발열량이 증가하여 반응기의 내부 온도가 증가하게 된다. 높은 O2/NH3비에서 온도의 상승은 분해 반응에 의한 암모니아 전환을 증가시킨다. 부분산화 반응은 촉매 전단부에서 빠른 산화 반응이 발생하며, 후단부에서는 개질 및 분해 반응과 같은 반응 속도가 느린 흡열 반응이 진행되는 것으로 알려져 있다15). 반응기 내부 40 mm와 100 mm의 온도 차이는 100 mm와 160 mm의 온도 차이보다 크다. 촉매를 30 mL 장입한 반응기는 100 mm에서 160 mm 구간에는 촉매가 장입되지 않아 열손실에 의한 온도 감소가 나타난다. 반면, 40 mm에서 100 mm 구간에서는 암모니아 분해에 의한 흡열 반응에 의해 온도가 크게 감소하였다.
3.4 공급유량과 촉매량에 따른 암모니아 부분산화 반응
Fig. 5는 암모니아 공급유량과 촉매량에 따른 암모니아 부분산화 반응의 암모니아 전환율, 분해 효율 및 가스 조성을 나타낸다. O2/NH3비는 0.10으로 고정하고 실험을 진행하였다. 암모니아 공급유량이 2.5 LPM인 조건에서는 촉매량이 15 mL인 반응기가 가장 낮은 암모니아 전환율과 분해 효율을 나타냈다. Fig. 6에 나타낸 것과 같이 암모니아 공급유량이 2.5 LPM인 조건에서 반응기 40 mm에서의 온도는 촉매량에 상관없이 일정하다. 이는 암모니아 산화 반응은 촉매량에 상관없이 동일하게 진행된 것을 의미한다. 따라서 암모니아 공급유량 2.5 LPM에서 촉매량이 15 mL인 반응기의 낮은 암모니아 전환율은 암모니아의 산화 반응 이후에 분해 반응에 필요한 촉매가 충분히 확보되지 않은 결과로 보인다. 특히, 해당 조건에서는 반응기의 온도가 250℃ 이하로 암모니아 분해의 반응 속도가 느리다. 반면, 촉매량이 60 mL인 조건에서는 촉매가 장입된 160 mm까지 암모니아 분해 반응이 진행되어 160 mm에서 촉매가 장입되지 않은 촉매량이 15 mL인 반응기보다 더 낮은 온도를 보였다. 촉매량이 15 mL인 반응기는 암모니아 공급유량이 5.0 LPM인 조건에서 약 66%의 최대 암모니아 전환율을 보였으며, 암모니아 공급유량이 5.0 LPM 이상으로 증가하면 암모니아 전환율이 감소하였다. 특히, 암모니아 공급유량이 12.5 LPM으로 증가함에 따라 암모니아 전환율이 크게 감소하였다. Fig. 6에서 보는 것과 같이 반응기의 온도는 암모니아 공급유량이 12.5 LPM인 조건에서는 340℃ 이상으로 증가하였으나, 촉매량이 15 mL인 반응기의 온다가 촉매량이 60 mL인 반응기의 온도보다 약 25℃ 낮았다. 이는 촉매량이 15 mL인 반응기에 12.5 LPM의 암모니아가 공급되면 일부 산소가 암모니아와 반응하지 않고 촉매를 통과하여 발열량과 암모니아 전환율이 감소한 결과일 가능성이 있다. 암모니아의 농도로 환산된 수증기의 농도도 암모니아 분해 반응 없이 산화 반응만 진행됨에 따라 증가하는 것을 볼 수 있다. 30 mL의 촉매를 장입하면 암모니아 공급유량이 2.5 LPM인 조건에서는 암모니아 전환율이 향상되었다. 하지만 암모니아 공급유량이 증가함에 따라 촉매 장입량이 15 mL인 반응기와 30 mL인 반응기는 암모니아 전환율, 분해 효율 및 가스 조성이 유사한 값을 보였다. 촉매량이 60 mL인 반응기에서는 모든 암모니아 공급유량에서 촉매량이 15 mL와 30 mL인 반응기보다 높은 암모니아 전환율을 얻었다. 반면, 측정된 암모니아 농도는 암모니아 공급유량에 상관없이 13-14% 수준으로 일정하여 환산된 수소, 질소 및 수증기의 농도도 일정하였다. O2/NH3비가 0.10인 조건에서 열역학 평형에서의 암모니아 농도는 9.67%로 암모니아 전환율은 79.04%이다. 촉매량이 60 mL인 반응기에서는 암모니아 전환율이 증가하였지만, 열역학 평형의 암모니아 전환율에 도달하지는 못하였다. 촉매 장입량이 60 mL인 조건에서는 공간속도가 암모니아 유량이 2.5 LPM에서 12.5 LPM으로 증가함에 따라 암모니아 부분산화 반응기의 공간 속도는 2,500/h에서 12,500/h로 증가한다. 암모니아 분해 반응기의 공간 속도는 99% 이상의 암모니아 전환율을 위하여 5,000/h 이하 수준으로 적용되어 왔다16,17). 따라서 해당 조건에서 암모니아 전환율을 높이기 위해서는 추가적인 촉매량의 증가가 필요해 보인다. 결론적으로 O2/NH3비의 영향을 실험한 결과와 비교하여 볼 때, 수소 생성을 높이기 위해서는 O2/NH3비가 0.1인 조건에서 촉매량을 증가시키는 것보다 O2/NH3비를 0.13으로 운전하는 것이 유리한 것으로 판단된다.
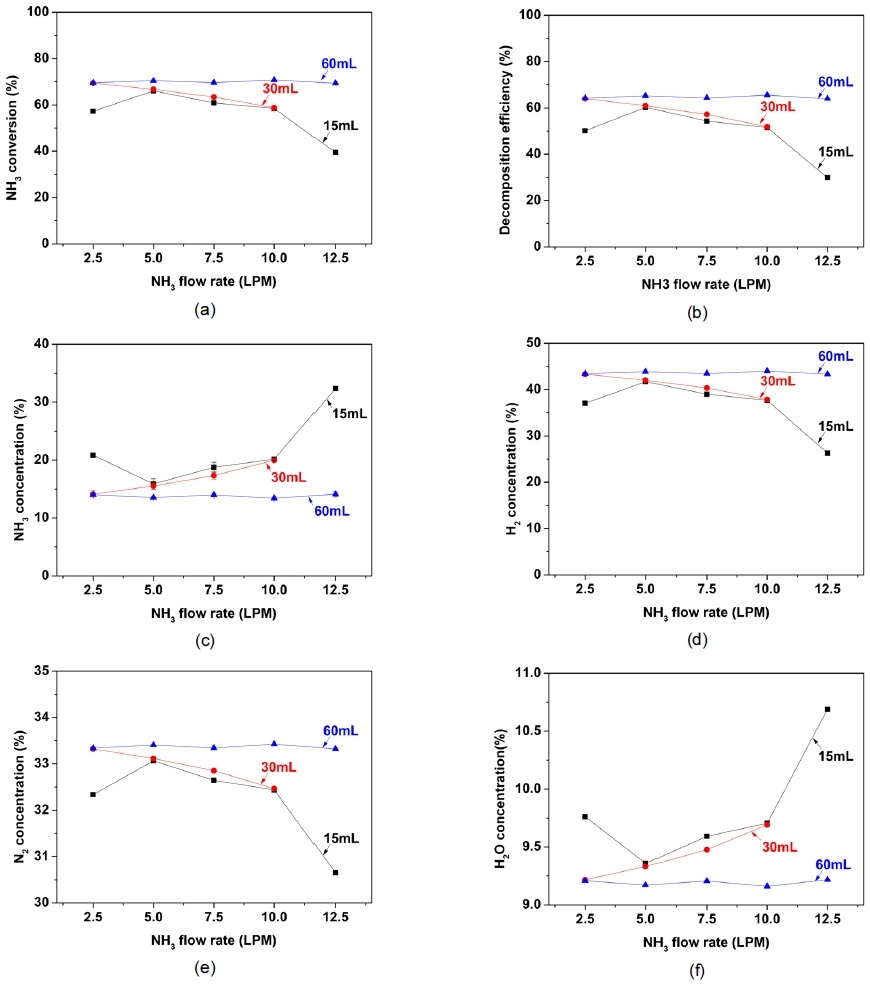
Effects of ammonia flow rate and catalyst volume on ammonia partial oxidation at 10 LPM of ammonia flow rate and 0.1 of O2/NH3 ratio (a) ammonia conversion, (b) decomposition efficiency, (c) ammonia concentration, (d) hydrogen concentration, (e) nitrogen concentration, (f) water concentration
4. 결 론
본 연구에서는 암모니아 부분산화 반응에 대한 열역학적 분석을 진행하였다. 또한, 암모니아 부분산화 반응기에 상용 Ru 촉매를 장입하고 시동 특성을 살펴보았으며, O2/NH3비, 암모니아 공급유량 및 촉매량에 따른 암모니아 부분산화 반응기의 운전 특성을 살펴보았다.
1) 단열 조건에서 암모니아 부분산화 반응기가 열역학적 평형에 도달하면 O2/NH3비가 0.15인 조건에서 암모니아 전환율이 99.0%로 대부분의 암모니아가 전환되었다. 수소 농도도 O2/NH3비가 0.10에서 0.15 사이인 영역에서 가장 높았다.
2) O2/NH3비가 0.10인 조건에서 10 LPM의 암모니아를 공급하면서 12 V 차량용 글로우 플로그로 30초간 가열하여 시동하였다. 시동 후 1분 이내에 암모니아 농도가 급격히 감소하였다. 시동 후 6분 이후에 암모니아 농도가 일정하여 암모니아 부분산화 반응기가 안정적으로 시동되는 것을 확인하였다.
3) 암모니아가 10 LPM으로 공급되는 조건에서 O2/NH3비를 0.10에서 0.13로 증가시키면 암모니아 전환율이 90%까지 증가하여 열역학적 분석 결과와 일치하는 것을 확인하였다. O2/NH3비가 0.13인 조건에서 측정된 암모니아 농도와 환산된 수소 농도는 각각 4%와 48%였다.
4) 15 mL의 촉매가 장입된 반응기에서 O2/NH3비를 0.1로 10 LPM의 암모니아를 공급하여도 암모니아의 산화 반응이 진행되는 것을 확인하였다. 반면, 느린 암모니아 분해 반응 속도로 인하여 촉매량을 60 mL로 증가시켜도 열역학적 평형에서의 조성에 도달하지 못하였다.
5) O2/NH3비와 촉매량에 대한 실험을 바탕으로 암모니아 부분산화 반응기의 암모니아 전환율을 높이기 위하여 O2/NH3비가 0.1인 조건에서 촉매량을 증가시키는 것보다 O2/NH3비를 0.13으로 운전하는 효과적인 것으로 판단된다.
Acknowledgments
본 연구는 한국기계연구원 기본사업 “차세대 암모니아 연료전지 스택 및 시스템 개발”의 지원으로 수행되었으며, 이에 감사드립니다.
References
-
J. H. Woo, T. Y. Kim, J. E. Kim, B. O. Cho, S. Y. Jung, S. M. Park, S. C. Lee, and J. C. Kim, “Ni catalyst properties for ammonia reforming: comparison of Ni content and space velocity”, Trans. Korean Hydrogen New Energy Soc., Vol. 32, No. 6, 2021, pp. 464-469.
[https://doi.org/10.7316/KHNES.2021.32.6.464]
-
C. Arnaiz del Pozo and S. Cloete, “Techno-economic assessment of blue and green ammonia as energy carriers in a low-carbon future”, Energy Conversion and Management, Vol. 255, 2022, pp. 115312.
[https://doi.org/10.1016/j.enconman.2022.115312]
-
P. Dimitriou and R. Javaid, “A review of ammonia as a compression ignition engine fuel”, International Journal of Hydrogen Energy, Vol. 45, No. 11, 2020, pp. 7098-7118.
[https://doi.org/10.1016/j.ijhydene.2019.12.209]
-
S. Giddey, S. P. S. Badwal, C. Munnings, and M. Dolan, “Ammonia as a renewable energy transportation media”, ACS Sustainable Chemistry & Engineering, Vol. 5, No. 11, 2017, pp. 10231-10239.
[https://doi.org/10.1021/acssuschemeng.7b02219]
-
R. Cavaliere da Rocha, M. Costa, and X. S. Bai, “Chemical kinetic modelling of ammonia/hydrogen/air ignition, premixed flame propagation and NO emission”, Fuel, Vol. 246, 2019, pp. 24-33.
[https://doi.org/10.1016/j.fuel.2019.02.102]
-
S. Frigo and R. Gentili, “Analysis of the behaviour of a 4-stroke Si engine fuelled with ammonia and hydrogen”, International Journal of Hydrogen Energy, Vol. 38, No. 3, 2013, pp. 1607-1615.
[https://doi.org/10.1016/j.ijhydene.2012.10.114]
-
S. Frigo, R. Gentili, G. Ricci, G. Pozzana, and C. Comotti, “Experimental result using ammonia plus hydrogen in a S.I. engine”, Lecture Notes in Electrical Engineering, Vol. 191, 2013, pp. 65-76.
[https://doi.org/10.1007/978-3-642-33777-2]
-
S. Frigo, R. Gentili, and F. De Angelis, “Further insight into the possibility to fuel a SI engine with ammonia plus hydrogen. In: SAE/JSAE 2014 Small Engine Technology Conference & Exhibition”, SAE Technical Paper, Vol. 32, No. 82, 2014, pp. 2014-32-0082.
[https://doi.org/10.4271/2014-32-0082]
-
M. Comotti and S. Frigo, “Hydrogen generation system for ammonia–hydrogen fuelled internal combustion engines”, International Journal of Hydrogen Energy, Vol. 40, No. 33, 2015, pp. 10673-10686.
[https://doi.org/10.1016/j.ijhydene.2015.06.080]
-
M. Koike, T. Suzuoki, T. Takeuchi, T. Homma, S. Hariu, and Y. Takeuchi, “Cold-start performance of an ammonia-fueled spark ignition engine with an on-board fuel reformer”, International Journal of Hydrogen Energy, Vol. 46, No. 50, 2021, pp. 25689-25698.
[https://doi.org/10.1016/j.ijhydene.2021.05.052]
-
J. Yang, A. Fathi Salem Molouk, T. Okanishi, H. Muroyama, T. Matsui, and K. Eguchi, “A stability study of ni/yttria-stabilized zirconia anode for direct ammonia solid oxide fuel cells”, ACS Applied Materials & Interfaces, Vol. 7, No. 51, 2015, pp. 28701-28707.
[https://doi.org/10.1021/acsami.5b11122]
-
M. Kishimoto, H. Muroyama, S. Suzuki, M. Saito, T. Koide, Y. Takahashi, T. Horiuchi, H. Yamasaki, S. Matsumoto, H. Kubo, N. Takahashi, A. Okabe, S. Ueguchi, M. Jun, A. Tateno, T. Matsuo, T. Matsui, H. Iwai, H. Yoshida, and K. Eguchi, “Development of 1 kW-class ammonia-fueled solid oxide fuel cell stack”, Fuel Cells, Vol. 20, No. 1, 2020, pp. 80-88.
[https://doi.org/10.1002/fuce.201900131]
-
T. Okanishi, K. Okura, A. Srifa, H. Muroyama, T. Matsui, M. Kishimoto, M. Saito, H. Iwai, H. Yoshida, M. Saito, T. Koide, H. Iwai, S. Suzuki, Y. Takahashi, T. Horiuchi, H. Yamasaki, S. Matsumoto, S. Yumoto, H. Kubo, J. Kawahara, A. Okabe, Y. Kikkawa, T. Isomura, and K. Eguchi, “Comparative study of ammonia-fueled solid oxide fuel cell systems”, Fuel Cells, Vol. 17, No. 3, 2017, pp. 383-390.
[https://doi.org/10.1002/fuce.201600165]
-
B. Stoeckl, M. Preininger, V. Subotić, H. Schroettner, P. Sommersacher, M. Seidl, S. Megel, and C. Hochenauer, “Ammonia as promising fuel for solid oxide fuel cells: experimental analysis and performance evaluation”, ECS Transactions, Vol. 91, No. 1, 2019, pp. 1601-1610.
[https://doi.org/10.1149/09101.1601ecst]
-
S. Yoon, S. Lee, and J. Bae, “DDevelopment of a self-sustaining kWe-class integrated diesel fuel processing system for solid oxide fuel cells”, International Journal of Hydrogen Energy, Vol. 36, No. 16, 2011, pp. 10302-10310.
[https://doi.org/10.1016/j.ijhydene.2010.10.001]
-
J. Cha, Y. S. Jo, H. Jeong, J. Han, S. W. Nam, K. H. Song, and C. W. Yoon, “Ammonia as an efficient COX-free hydrogen carrier: fundamentals and feasibility analyses for fuel cell applications”, Applied Energy, Vol. 224, 2018, pp. 194-204.
[https://doi.org/10.1016/j.apenergy.2018.04.100]
-
S. Lee, Y. Choi, C. Park, H. Kim, Y. D. Lee, and Y. S. Kim, “A study on ammonia reforming catalyst and reactor design for 10 kW class ammonia-hydrogen dual-fuel engine”, Trans. of the Korean Hydrogen and New Energy Society, Vol. 31, No. 4, 2020, pp. 372-379.
[https://doi.org/10.7316/KHNES.2020.31.4.372]