
촉매유효도 상관식에 기반한 마이크로 채널형 수증기/메탄 개질기의 효율적인 전산유체역학 해석모델
2022 The Korean Hydrogen and New Energy Society. All rights reserved.
Abstract
An efficient computational fluid dynamics model was proposed for simulating microchannel-type steam/methane reformers with thin washcoat catalyst layers. In this model, by using the effectiveness factor correlations, the overall reaction rate that occurs in the washcoat catalyst layer could be accurately estimated without performing the detailed calculation of heat transfer, mass transfer, and reforming reactions therein. The accuracy of the proposed model was validated by solving a microchannel-type reformer, once by fully considering the complex steam/methane reforming (SMR) process inside the washcoat layer and again by simplifying the SMR calculation using the effectiveness factor correlations. Finally, parametric studies were conducted to investigate the effects of operating conditions on the SMR performance.
Keywords:
Steam/methane reforming, Catalyst effectiveness factor, Effectiveness factor correlation, Microchannel-type reformer, Nickel washcoat layer키워드:
수증기/메탄 개질, 촉매유효도, 유효도 상관식, 마이크로 채널형 개질기, 니켈 워시코트 촉매층1. 서 론
화석연료의 고갈, 환경오염의 심화 및 지구온난화 문제의 해결을 위하여 대체 에너지 공급원으로서 수소에너지에 대한 관심이 증가하고 있다1,2). 이와 관련하여 수소 생산을 위한 다양한 공정 기술에 관한 연구도 활발히 진행되고 있다3). 현재 사용되고 있는 대부분의 수소는 산업용 플랜트에서 대규모로 이루어지는 천연가스의 수증기 개질공정(steam reforming process)을 통해 얻어진다. 천연가스의 주성분이 메탄이므로 이 공정을 수증기/메탄 개질(steam/methane reforming, SMR)이라 지칭하기도 한다. 수증기/메탄 개질은 탄화수소 연료로부터 수소를 생산하는 가장 일반적이며 동시에 기술적 성숙도가 높은 잘 확립된 기술이다.
자원 고갈 및 환경 문제의 해결책으로서 수소에너지의 중요성이 높아짐에 따라 현장(on-site)에서 수소를 생산하여 필요한 수요에 따라 바로 공급을 할 수 있는 소규모 수증기/메탄 개질기에 대한 관심이 증가하고 있다. 특히 도시가스(city-gas)망을 통해 공급된 메탄을 개질하여 분산 발전용 연료전지 시스템에 수소연료를 공급하는 소규모 수증기/메탄 개질기에 대한 연구도 활발히 진행되고 있다4-8). 연료전지 시스템에 결합된 개질기의 경우 수소 생산 성능의 향상을 위하여 형상이 복잡해지고 크기는 소형화되는 경향을 가진다9,10). 개질기의 형상설계 및 최적 작동 조건의 도출을 위하여 촉매 내부에서 일어나는 열/물질전달과 화학반응에 대한 정확한 예측에 더하여 개질기를 통한 열전달, 유체유동의 정확한 해석이 필수적이며 이러한 필요에 따라 많은 전산유체역학(computational fluid dynamics, CFD) 해석 연구가 수행되고 있다11-13).
본 연구에서는 촉매유효도(catalyst effectiveness factor)에 대한 선행연구14-16)를 바탕으로 니켈 워시코트 촉매층(nickel washcoat layer)에 대해 제안된 유효도 상관식(effectiveness factor correlation)16)을 2차원 마이크로 채널형 개질기에 적용하여 효율적인 해석모델을 개발하고자 하였다. 상용 CFD 소프트웨어 ANSYS Fluent (ANSYS Inc., Canonsburg, PA, USA)17)를 전산유체해석 플랫폼으로 사용하였으며, 기본 모델(base model)에서는 50 μm 두께의 워시코트 촉매층 내부에서 일어나는 열/물질전달, 화학반응 등 수증기/메탄 개질과정 전체를 빠짐없이 정확히 해석하였다. 이와는 대비되게 유효도 모델(effectiveness model)에서는 복잡한 계산 없이 촉매유효도 상관식을 통해 워시코트 촉매층에서 발생하는 반응량을 결정한 후 체적반응률로 환산하여 대입하는 계산 방식을 취하였다. 이후 기본 모델과 유효도 모델의 해석 결과 비교를 통하여 본 연구에서 제안하는 유효도 CFD 모델의 타당성을 검증하였다. 또한 검증된 유효도 CFD 모델을 이용하여 수증기/메탄 혼합기체의 입구유속의 변화 및 개질기 작동온도의 변화에 따른 개질 성능의 변화를 검토하였다.
2. 해석모델
2.1 해석영역
Fig. 1은 본 연구에서 고려한 50 μm 두께의 니켈 워시코트 촉매층이 적용된 2차원 마이크로 채널형 수증기/메탄 개질기에 대한 형상모델을 나타내고 있다. 개질기의 유동방향 길이를 10 cm, 채널 높이(channel height)를 1.5 mm, 위/아래 지지판 두께(substrate thickness)를 0.2 mm로 설정하였으며, 채널과 벽면 사이에 50 μm 두께의 워시코트 촉매층이 존재하는 것으로 가정하였다. 개질가스는 좌측의 입구경계를 통해 유입되어 우측의 출구경계를 통해 빠져나간다. 해석영역의 대칭성을 고려하여 실제 CFD 해석에서는 유동채널의 중심선을 따라 대칭 조건을 부여하여 반 영역(half region)만을 고려하였다. Fig. 1(a)와 Fig. 1(b)는 각각 마이크로 채널형 개질기에 대한 기본 모델(base model) 및 유효도 모델(effectiveness model)의 CFD 해석영역을 나타내고 있다.
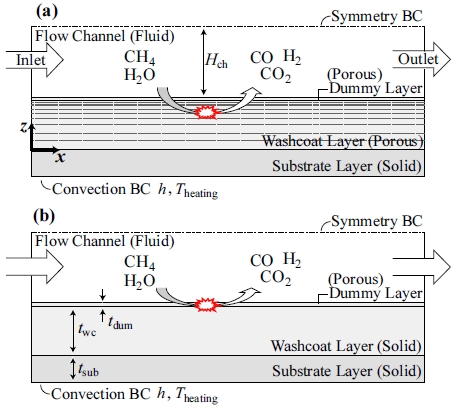
An exemplary microchannel-type steam/methane reformer: the calculation domains for (a) the base model and (b) the effectiveness model
Fig. 1(a)의 기본 모델에서는 물리적 영역과 동일하게 마이크로 채널은 유체 영역(fluid region)으로, 워시코트 촉매층은 다공성 영역(porous region)으로, 지지판은 고체 영역(solid region)으로 설정하였다. 추가적으로 Fig. 1(a)에서 마이크로 채널과 워시코트 촉매층 사이에 화학반응이 일어나지 않는 가상의 다공성 더미층(dummy layer)을 삽입한 것에 주목할 필요가 있다. 더미층은 두께가 1 μm로 작고 확산계수가 마이크로 채널에서의 값과 동일하게, 열전도도는 워시코트 촉매층과 동일하게 설정되었다. 이러한 더미층은 비교를 위하여 유효도 모델과의 형상적 동일성을 확보하고 동시에 CFD 해석의 오류를 피하기 위하여 삽입되었다.
Fig. 1(a)의 기본 모델에서는 50 μm 두께의 워시코트 촉매층 내부에 두께방향으로 50개의 조밀한 비균일 체적셀(최대/최소 격자크기 비율을 50으로 설정)을 배치하여 내부에서 일어나는 열/물질전달, 화학반응 등 수증기/메탄 개질과정 전체를 정확히 해석하였다. 반면에 Fig. 1(b)의 유효도 모델에서는 워시코트 촉매층을 고체 영역으로 설정하고 대신에 1 μm 두께의 가상의 다공성 더미층(두께방향으로 1개의 체적셀) 내부에서 워시코트 촉매층에서 일어나는 모든 개질반응이 일어나는 것으로 처리하여 해석을 단순화하여 처리하였다. 더미층의 두께가 작을수록 유효도 모델의 결과는 더욱 정확해진다. 보다 자세한 사항은 다음의 지배방정식 절에서 설명하였다.
2.2 지배방정식
본 연구에서는 상용 CFD 소프트웨어 ANSYS Fluent (ANSYS Inc.)17)를 활용하여 Fig. 1에서 나타낸 마이크로 채널형 개질기에 대한 해석을 수행하였다. Fluent는 그 정확성 및 활용도에서 CFD 분야의 많은 연구자들에 의해 거의 표준으로 받아들여지고 있는 CFD 계산 플랫폼이다. 따라서 fluent를 이용하여 2차원 유동채널에서 일어나는 유체유동, 열전달, 물질전달을 k-ε 난류모델을 고려하여 정확하게 해석하였다. 개질가스는 메탄(CH4), 수증기(H2O), 수소(H2), 일산화탄소(CO), 이산화탄소(CO2) 등 5종의 기체종이 고려되었다.
워시코트 촉매층의 경우 공극크기가 매우 작은(dpore~25 nm) 다공성 미세구조를 가지고 있어 유동투과율(flow permeability)이 Kv~1×10-18 m2 정도로 매우 낮다. 이러한 낮은 유동투과율은 워시코트 촉매층 내부에서의 유체유동 및 난류 효과를 효과적으로 억제한다. 따라서 Fig. 1(a)의 기본 모델에서 워시코트 촉매층은 층류 다공성 영역으로 처리되어 유체유동이나 난류 효과가 거의 없이 개질반응 및 열전달, 물질전달만이 상세하게 해석되었다. Fig. 1(a)에서 추가적으로 삽입되어 있는 1 μm 두께의 다공성 더미층 또한 층류 다공성 영역으로 처리되었으나 개질반응 없이 열전달, 물질전달 만이 고려되었다. 고체 영역인 지지판의 경우 열전도 방정식만 해석되었다.
Fig. 1(b)의 유효도 모델에서는 기본 모델과는 다르게 워시코트 촉매층이 고체 영역으로 처리되어 열전도 방정식만 해석된다. 1 μm 두께의 다공성 더미층에는 두께방향으로 하나의 체적셀만이 배치되었기 때문에 더미층 내부에서의 개질과정에 대한 상세한 해석은 본질적으로 불가능하다. 대신 다공성 더미층에서의 기체농도 및 온도를 기준으로 수증기/메탄 개질반응의 촉매유효도 및 명목반응률(nominal reaction rate)을 계산하고 이를 곱해 워시코트 촉매층 내부에서 발생하는 총 반응량을 결정한다. 이후 이 반응량을 다공성 더미층에 대한 체적반응률로 환산하여 대입하는 방식으로 해석을 수행하였다. 다공성 더미층은 그 두께가 1 μm로 매우 작게 생성되었고, 또 기체 확산계수는 유동채널과 동일하게, 열전도도는 워시코트 촉매층과 동일하게 설정되어, 더미층 내부의 기체농도 및 온도는 유동채널과 워시코트 촉매층 계면에서의 값과 거의 동일하도록 하였다.
기본 모델 및 유효도 모델에서 수증기/메탄 개질반응에 대한 반응률 및 기체종의 유효확산계수의 복잡한 관계식은 ANSYS Fluent에서 제공하는 사용자정의함수(user-defined function, UDF) 기능을 이용하여 처리되었다.
2.3 개질반응식
마이크로 채널형 개질기의 워시코트 촉매층에서 일어나는 수증기/메탄 개질과정을 설명하기 위하여 다음과 같이 수증기개질(steam reforming, SR), 수성가스화(water-gas shift, WGS), 역메탄화(reverse methanation, RM)의 3단계로 구성된 단순화된 전체반응단계(global reaction step)18)를 고려하기로 한다.
I. 수증기개질(Steam reforming, SR):
(1) |
II. 수성가스화(Water-gas shift, WGS):
(2) |
III. 역메탄화(Reverse methanation, RM):
(3) |
Xu와 Froment18)는 니켈 촉매에 대하여 이상의 반응단계에 대한 반응속도를 연구하였으며, 반응단계 i에 대한 내재적 반응속도 ri (kmol/kgcat-h)는 다음과 같이 계산된다.
(4) |
(5) |
(6) |
위 식에서 DEN은 다음과 같다.
(7) |
위 식에서 ki 및 Keq,i는 반응단계 i에 대한 반응률상수 및 반응평형상수로 다음과 같다.
(8) |
(9) |
(10) |
(11) |
(12) |
(13) |
Kj는 기체종 j에 대한 흡착계수로 다음과 같다.
(14) |
(15) |
(16) |
(17) |
수증기/메탄 개질반응은 가역반응이며 정반응 시 메탄과 수증기가 결합하여 수소가 생산된다. 개질반응의 평형은 온도, 압력 및 기체 농도에 의해 결정되며 특히 전체반응이 대체로 흡열반응이기 때문에 높은 개질온도 조건에서 반응평형은 정반응이 우세하게 나타나며 수소 생산이 증가하게 된다.
2.4 유효확산계수
2차원 마이크로 채널에서의 물질전달과정은 분자확산, 난류확산 및 유체유동이 결합되어 발생하며 특히 개질가스에 존재하는 기체종(CH4, H2O, H2, CO, CO2)을 고려하면 분자확산은 다성분 전달과정이다. 따라서 유동채널을 흐르는 기체종 i에 대한 유효확산계수 Dm,i (m2/s)가 필요하며 이는 Wilke의 공식19)에 따라 다음과 같이 계산된다.
(18) |
위 식에서 xi는 종 i의 몰분율이고, Dij (m2/s)는 기체종 i-j쌍에 대한 이성분 확산계수로 Fuller 등20)의 경험적 상관식을 이용하여 다음과 같이 Dij를 결정하였다.
(19) |
위 식에서 온도 T는 K 단위, 총 압력 pt는 bar 단위이다. 또한 vi 및 vj는 확산부피(CH4: 25.14, H2O: 13.1, H2: 6.12, CO: 18.0, CO2: 26.7)를 나타내며 Mij는 Mij=2[(1/Mi)+(1/Mj)]-1로 정의되는 혼합 분자량을 나타낸다. 참고로 CH4, H2O, H2, CO 및 CO2의 분자량은 각각 16.043, 18.015, 2.016, 28.01 및 44.01 kg/kmol이다.
다공성 워시코트 촉매층에서 기체종 i의 유효확산계수 Di,eff (m2/s)는 유동채널에서의 Dm,i보다 훨씬 작은데, 이것은 워시코트 촉매층의 공극구조가 물질확산을 크게 저해하기 때문이다. 다공성 매질에서의 복잡한 공극구조에 따른 확산면적의 감소와 확산경로의 증가는 일반적으로 기공률(porosity) ε과 굴곡도(tortuosity) τ를 결합한 ε/τ 인자에 의해 고려된다21). 게다가 공극크기가 기체분자의 평균자유행정(mean free path)보다 작아질 경우 다공성 매질을 통한 물질확산 속도는 Knudsen 확산22)이라고 알려진 확산과정에 의해 더욱 감소한다.
본 연구에서는 워시코트 촉매층 내 기체종 i의 유효확산계수 Di,eff를 다음과 같이 Bosanquet 근사22)를 이용하여 결정하였다.
(20) |
위 식에서 DK,i는 Knudsen 확산계수로 다음과 같이 평균 공극크기 dpore의 함수로 계산된다.
(21) |
개질기의 다양한 해석영역에 대한 기체종 유효확산계수는 ANSYS Fluent의 DEFINE_DIFFUSIVITY UDF를 사용하여 정의하였다. 즉, Di,eff는 기본 모델의 경우에 다공성 워시코트 촉매층의 유효확산계수로 정의하였으며, Dm,i는 2D 유동채널 및 더미층의 유효확산계수로 정의하였다.
2.5 촉매유효도
수증기/개질의 SR, WGS, RM 반응에 대한 촉매유효도 ηk (k=I, II, III)는 니켈 촉매의 겉보기 밀도 ρcat (kgcat/m3)과 워시코트 촉매층의 두께 twc를 통하여 다음과 같이 정의된다.
(22) |
위 식에서 우변의 분자는 워시코트 촉매층 내부에 분포된 기체분압 pi 및 온도 T에 따른 국부적인 반응률 rk(pi|i=1···5,T)를 촉매층 두께에 대해 적분한 값이며, 즉 워시코트 촉매층 내부에서 실제로 일어나는 총 반응률을 rA,k (kmol/m2-s)를 의미한다. 반면에 우변의 분모는 유동채널과 워시코트 촉매층 경계에서의 기체분압 pi,∞ 및 온도 T∞를 통해 계산되는 명목 반응률 Rwc,k (kmol/m2-s)로 다음과 같이 정의된다.
(23) |
따라서 신뢰할 수 있는 촉매유효도 ηk가 주어지는 경우 워시코트 촉매층 내부에서 발생하는 총 반응률 rA,k를 복잡한 계산없이 다음의 식을 통해 정확하고 효율적으로 결정할 수 있다.
(24) |
이러한 논의에 따라 Jeong 등16)은 50 μm 내외의 얇은 니켈촉매 워시코트층에 대하여 다음과 같은 촉매유효도 상관식을 제안하였다.
(25) |
(26) |
위 식에서 SR(ηI) 반응 및 RM(ηIII) 반응에 대해서만 촉매유효도 상관식이 제시되어 있음에 주의하라. Jeong 등16)은 WGS 반응에 대하여 간단히 ηII≈1.0을 사용하는 것을 추천하였다. 이는 WGS 반응이 전체 수증기/메탄 개질반응에서 차지하는 비중이 상대적으로 적고 또 평형제한(equilibrium-limited) 반응처럼 거동하기 때문이다. 식 (25), (26)의 φI* 및 φIII*는 유효 Thiele 모듈러스 φI 및 φIII를 수정하여 얻은 수정 Thiele 모듈러스를 의미하며 다음과 같다16).
(27) |
(28) |
이상의 수정 Thiele 모듈러스는 온도(600-800°C), 압력(1-3 bar) 및 탄소 대 수증기 비율인 S/C비(2-4) 등 다양한 수증기/메탄 개질조건의 영향을 고려하기 위해 도입되었다15,16). 유효 Thiele 모듈러스는 명목 반응률 Rwc,k과 명목 메탄확산률 Mwc,CH4을 통해 다음과 같이 정의된다.
(29) |
위 식에서 Rwc,I와 Rwc,III는 식 (23)에서 정의된 명목 반응률을 의미하여 명목 메탄확산률 Mwc,CH4 (kmol/m2-s)은 다음과 같이 정의된다15,16).
(30) |
위 식에서 xCH4,eq는 주어진 압력, 온도 및 S/C비 등 개질조건에 따라 결정되는 수증기/메탄 개질반응의 평형 메탄 몰분율을 의미한다. 계산과 관련된 자세한 내용은 Jeong 등16)을 참고하라.
각각의 개질반응 단계에 대한 반응률은 ANSYS Fluent의 DEFINE_VR_RATE UDF를 사용하여 정의하였다. 기본 모델의 경우 식 (4)-(6)으로 계산된 반응률을 kmol/m3-s 단위의 체적반응률로 적절하게 변환(ρcat×rk/3600/εwc)하여 다공성 워시코트 촉매층의 체적셀에 대입하였다. 유효도모델의 경우에는 식 (23), 식(24)를 통해 계산된 반응률을 kmol/m3-s 단위의 체적반응률로 적절하게 변환(ηk×Rwc,k/tdum/εdum)하여 다공성 더미층의 체적셀에 대입하였다.
2.6 해석조건
본 연구에서 고려한 마이크로 채널형 개질기의 물리적 특성은 Table 1에 요약되어 있다. Table 1에서 겉보기 촉매밀도 ρcat은 Xu와 Froment18)에서 측정된 2,355 kgcat/m3을 사용하였다. 또한 공극률과 굴곡도의 경우 Xu와 Froment18)가 사용한 ε=0.528, τ=3.54 및 Zanfir와 Gavriilidis9)가 사용한 ε=0.4, τ=4를 참고하여 각각 0.5 및 4.0으로 설정하였다. 다공성 워시코트 촉매층의 경우 유효 열전도도 keff가 1 W/m-K이 되도록 설정하였으며, 지지판의 열전도도는 ksub=20 W/m-K으로 설정하였다. Table 2에서는 본 연구에서 고려한 마이크로 채널형 개질기의 작동조건을 정리하였다. 탄소 대 수증기 비율인 S/C비는 개질기 입구에서의 메탄의 몰유량 대비 수증기의 몰유량로 정의되며, S/C=3에 따라 xCH4,in=0.25, xH2O,in=0.75으로 설정되었다(H2, CO, CO2의 입구 몰농도는 0).
마이크로 채널형 개질기를 통해 혼합기체가 흐르면 수증기/메탄 개질과정의 진행에 따라 메탄의 농도가 축방향으로 점차 감소하게 된다. 메탄전환율 βCH4는 유동채널의 입구 및 출구에서의 메탄 몰유량 NCH4,in 및 NCH4,out를 통해 다음과 같이 정의된다.
(31) |
따라서 메탄전환율 βCH4는 수증기/메탄 개질기를 통한 수소 생산의 효율성을 측정하는 주요한 성능지표(performance index)이다.
2차원 해석영역에 대한 격자생성은 전체적으로 직사각형 형태의 체적셀로 구성된 구조격자(structured grid)를 사용하였다. 기본 모델과 유효도 모델 모두에서 유동채널에 대해 x축 방향으로 200개 및 z축 방향으로 20개의 균일한 체적셀을 배치하였다. 기본 모델의 경우, z축 방향으로 다공성 워시코트 촉매층에 50개의 체적셀을, 더미층에 1개의 체적셀을, 지지판에 5개의 체적셀을 배치하여 총 15,200개의 체적셀이 생성되었다. 유효도 모델의 경우, z축 방향으로 더미층에 1개의 체적셀, 워시코트 촉매층에 3개의 체적셀, 지지판에 5개의 체적셀을 배치하여 총 5,800개의 체적셀이 사용되었다.
3. 결과 및 고찰
3.1 유효도 모델의 검증
본 연구에서 고려하는 마이크로 채널형 개질기에는 마이크로 유동채널의 벽면에 50 μm 두께의 니켈촉매 워시코트층이 존재한다. 우선 유동채널을 통한 난류를 포함한 유체유동과 열전달, 물질전달을 정확히 고려하기 위하여 그 정확도가 검증된 ANSYS Fluent를 계산플랫폼으로 설정하여 해석을 수행하였다. 우선 기본 모델(base model)에서는 워시코트 촉매층에 많은 수의 격자(두께 방향으로 50개)를 배치하고 Fluent의 UDF 기능을 활용하여 내부에서 일어나는 열전달, 물질전달 및 개질반응 단계를 정확하게 고려하였다. 다음으로 유효도 모델(effectiveness model)에서는 촉매유효도와 명목반응률을 통해 워시코트 촉매층의 총 반응률을 결정한 후 이를 1 μm 두께의 더미층(두께방향으로 1개의 격자)에 대입하는 방식으로 해석을 수행하였다.
Table 1의 물리적 형상 및 물성과 Table 2의 작동조건 및 가열조건에 대하여 마이크로 채널형 개질기의 CFD 해석을 수행한 결과, 메탄전환율 βCH4은 기본 모델이 84.2%, 유효도 모델이 84.3%로 매우 잘 일치하는 것으로 나타났다. 보다 자세한 해석모델의 비교, 검증을 위하여 마이크로 채널형 개질기 내부 유동채널 대칭면(윗면) 및 지지판 바닥면의 온도분포 T를 Fig. 2에서 비교하였다. 수증기/메탄 개질반응은 전체적으로 강한 흡열반응이며 따라서 반응률이 큰 개질기 입구 근처에서 온도가 급격하게 떨어지게 된다. 이후 지지판 바닥면에서의 대류에 의해 가열이 되면서 축방향으로 점차 온도가 상승한다. Fig. 2에서 기본 모델 및 유효도 모델에 의해 얻어진 온도분포가 매우 잘 일치함을 확인할 수 있다.
다음으로 Fig. 3에서는 유동채널의 대칭면(윗면)에서의 기체종의 몰분율 xi의 분포를 나타내어 비교하고 있다. 반응물에 해당하는 메탄(CH4)과 수증기(H2O)는 유동채널을 따라 흐르고 그 농도가 점차로 감소하며 반대로 생성물인 수소(H2) 및 일산화탄소(CO), 이산화탄소(CO2)의 농도는 점차 증가한다. 특히 개질기 입구 근처에서의 농도 변화가 큰데 이것은 이 영역에서의 빠른 개질반응의 결과이다. 기본 모델과 유효도 모델의 결과는 매우 잘 일치하고 있으며 몰분율의 차이는 1% 이내로 잘 유지되고 있다.
마지막으로 Fig. 4에서 워시코트 촉매층 내부에서 발생하는 kmol/m2-s 단위의 총 반응률 rA,k를 각각의 반응단계에 대하여 비교하였다. 식 (24)에서 나타낸 바와 같이 기본 모델에서는 국소 반응률을 워시코트 촉매층 두께에 대하여 적분하여 총 반응률 rA,k를 결정할 수 있으며 유효도 모델의 경우 촉매유효도와 명목반응률을 곱하여(ηk×Rwc,k) 결정할 수 있다. Fig. 4에서 SR 반응 및 RM 반응에 대하여 촉매유효도 상관식을 적용한 유효도 모델과 기본 모델의 반응률을 비교하여 잘 일치하는 것을 관찰할 수 있다.
또한 Fig. 4는 본 모델에서 고려한 SMR 과정의 3가지 반응 중 SR 반응이 다른 반응에 비해 가장 지배적인 것을 잘 보여주고 있다. 전체적으로 입구 근처에서 큰 반응률이 나타나며 유로를 따라서 점차 감소하는 경향을 확인할 수 있다. 이것은 입구 근처에서는 반응물의 농도가 매우 높고 생성물의 농도가 매우 낮아 개질반응이 빠르게 일어나고, 반면에 출구 근처로 갈수록 점점 개질반응의 평형점에 접근함에 따라서 반응속도가 느려지기 때문이다. 유효도 모델의 경우 Jeong 등16)의 추천에 따라 WGS 반응의 촉매유효도를 ηII=1로 고정하여 해석을 수행하였으며, 그 결과 입구 근처에서 기본 모델과 유효도 모델이 완전히 다른 경향의 WGS 반응률 거동이 나타낸다. 그러나 WGS 반응률의 이러한 차이가 전체적인 SMR 과정에 미치는 영향은 앞서 메탄전환율의 비교나 Fig. 2와 Fig. 3의 온도, 몰분율 분포의 비교에서 확인한 바와 같이, 그리 크지 않은 것으로 유추된다.
마지막으로 유효도 모델의 효율성에 대한 검토를 위해 격자구성 및 해석시간에 대하여 비교하였다. 기본 모델의 경우 15,200개의 체적셀로 격자계를 구성하였고 유효도 모델의 경우 5,800개의 체적셀로 격자계를 구성하여, 유효도 모델이 격자수를 대략 1/3 정도로 적게 사용하고 있다. 또한 레노버 P620 워크스테이션(AMD 3955WX CPU, Lenovo, Beijing, China)에서 8개의 병렬노드를 사용하여 ANSYS Fluent 계산을 수행하는 경우, 1,000번의 반복계산(iteration)에 걸리는 CPU 시간은 기본 모델의 경우 1,362초, 유효도 모델의 경우 298초로, 유효도 모델이 대략 4.5배 빠른 계산이 가능하였다. 따라서 기본 모델과 비견할 만한 해의 정확도와 상대적으로 빠른 계산 속도를 고려하면 유효도 모델의 효율성을 확인할 수 있다. 특히 이러한 유효도 모델의 효율성은 3차원 형상의 개질기 등으로 해석격자가 많고 해석영역이 더욱 복잡해지는 경우에 그 활용성이 더욱 증가할 것으로 기대하고 있다.
3.2 작동온도의 영향
수증기/메탄 개질반응은 전체적으로 강한 흡열반응이므로 작동온도에 큰 영향을 받을 것으로 예측할 수 있다. 또한 작동온도는 개질반응의 평형점을 변화시키며 동시에 기체의 열물성, 확산계수 등 물리적 특성에도 많은 영향을 미친다. 따라서 유효도 모델을 이용하여 파라미터 연구를 통해 Table 2에서 나타낸 혼합기체의 입구온도 Tin와 가열온도 Theating이 함께 600-900°C로 변화하는 경우를 고찰하였다.
Fig. 5(a)는 작동온도가 변화하는 경우에 대하여 메탄전환율 βCH4의 축방향 분포를 나타내고 있다. 강한 흡열반응인 수증기/메탄 개질반응은 작동온도가 높아질수록 메탄전환율이 증가하는 것을 잘 보여주고 있다. 작동온도가 600°C인 경우 마이크로 채널형 개질기의 메탄전환율이 54.4%인 것에 비하여 작동온도가 900°C로 높아지는 경우 메탄전환율은 99.8%로 대부분의 메탄이 분해됨을 확인할 수 있다. 또한 작동온도가 높을수록 개질기 입구 근처에서 개질반응이 매우 빠르게 진행되며, 예를 들어 작동온도가 900°C인 경우 개질기 입구에서 1.25 cm 떨어진 지점에서 이미 메탄전환율이 51.4%까지 높아진다.
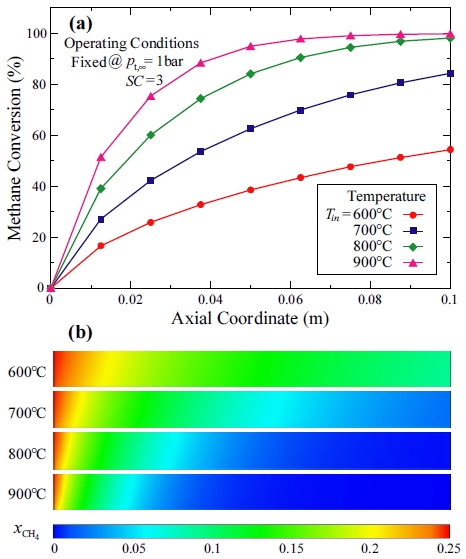
Effects of the operating temperature on (a) methane conversion distribution and (b) methane mole fraction distribution along the axial coordinate
Fig. 5(b)에서는 개질기의 유동채널에서 작동온도에 따른 메탄의 몰분율 분포를 나타내고 있다. 개질기 입구에서 메탄 몰분율은 0.25로 동일하게 유입되지만 작동온도가 증가함에 따라서 개질반응에 의해 메탄이 더욱 빠르게 소모되고 몰분율이 소진되는 지점 또한 점점 더 짧아지는 것을 확인할 수 있다.
3.3 유동속도 및 대류열전달의 영향
이번 절에서는 수증기/메탄 개질기의 작동조건을 1 bar, 700°C, S/C비 3으로 고정한 상태에서 다른 작동 조건이 개질반응에 미치는 영향을 고찰하였다. Fig. 6에서는 우선 수증기/메탄 혼합기체가 개질기 입구를 통해 유입되는 속도의 영향을 고려하였다. 참고로 본 연구에서 고려한 마이크로 채널형 개질기의 경우 1 bar, 700°C의 작동조건에서 유동채널 입구속도가 uin=6.6 m/s이 되는 경우 표준온도압력(1 bar, 0°C) 기준으로 공간속도(gas hourly space velocity, GHSV) GHSV=1,000,000 h-1에 해당한다. Fig. 6에서는 개질기 입구에서의 수증기/메탄 혼합기체의 유동속도를 0.5-25 m/s로 변화시키면서 파라미터 연구를 수행하여 얻어진 메탄전환율을 나타내고 있다.
Fig. 6에서 유동속도가 1 m/s 이하로 매우 낮을 때 100%에 근접하는 메탄전환율이 얻어지는 것을 확인할 수 있다. 이것은 낮은 유동속도에 따라 반응물과 촉매가 접촉하는 체류시간(residence time)이 충분히 길어져 마이크로 채널형 개질기 출구에서 개질가스가 거의 개질반응의 평형점에 도달하였기 때문인 것으로 판단된다. 수증기/메탄 혼합기체의 유입속도를 낮추면 메탄전환율은 증가하지만 개질반응과 수소생산량의 절댓값은 유속에 비례해 작아지게 된다. 따라서 최적의 메탄전환율 및 수소 생산량을 얻을 수 있도록 수증기/메탄 혼합기체의 유입속도를 포함하여 개질기의 작동조건을 설정해야 한다.
수증기/메탄 개질반응은 강한 흡열반응으로, 적절한 열 설계를 통해 반응열을 촉매층에 얼마나 빠르게 공급하는가 하는 것이 개질기의 성능에 큰 영향을 미치게 된다. Fig. 7에서는 지지판 바닥면의 대류열전달계수 h를 100-400 W/m2-K로 변화시키면서 파라미터 연구를 수행하여 얻어진 메탄전환율을 나타내고 있다. 대류열전달계수가 증가할수록 개질반응에 필요한 반응열이 워시코트 촉매층으로 더욱 원활하게 전달되게 되고 그 결과로 개질반응률의 상승에 따라 메탄전환률이 증가하게 된다. Fig. 7에서 대류열전달계수가 100에서 200 W/m2-K로 증가할 때 메탄전환율이 급격히 증가하지만 이후로는 완만한 증가만이 관찰된다. 수증기/메탄 개질기의 전체적인 개질성능은 열전달속도, 물질전달속도, 화학반응속도 모두에 의하여 제한받으며 이들이 복합적으로 작용하여 얻어진 결과이다. 따라서 단순히 열전달속도만을 증가시킨다고 하여 전체 개질성능이 그에 비례하여 향상되는 것은 아니다. 따라서 각각의 전달과정이나 반응속도 등 제한요인들을 적절한 수준에서 조절하여 요구되는 개질 성능을 만족시키는 개질기 형상 설계 및 작동조건 최적화 등이 필요하다.
4. 결 론
본 연구에서는 촉매유효도 상관식을 활용하여 워시코트 촉매층을 가지는 마이크로 채널형 수증기/메탄 개질기의 운전을 정확하게 예측할 수 있는 효율적인 CFD 해석모델을 제안하였다. 해석에 사용된 촉매유효도 상관식은 저압의 작동조건(p=1-3 bar, T=600-800°C, S/C=2-4)에 대하여 유도되어 소규모 분산형 수증기/메탄 개질시스템으로의 적용성이 높다. 본 연구에서 제안된 효율적인 CFD 해석모델은 워시코트 촉매층 내부에서 일어나는 열전달, 물질전달, 화학반응을 상세하게 고려한 CFD 해석모델과의 결과비교를 통해 그 정확성이 검증되었으며 또한 계산시간의 비교를 통해 그 효율성을 실증하였다. 검증연구가 완료된 후 마이크로 채널형 수증기/메탄 개질기에 대하여 작동온도, 유동속도 및 대류열전달 등 작동 조건이 개질성능에 미치는 영향에 대하여 파라미터 연구를 수행하고 그 결과를 고찰하였다. 따라서 본 연구에서 제안한 CFD 해석모델이 적은 수의 격자계를 가지고 복잡한 개질과정의 정확한 해석을 가능케 하여 수증기/메탄 개질기 개발을 위한 효율적인 해석툴로서 활용될 수 있을 것으로 기대한다.
Acknowledgments
본 논문은 정부(교육부)의 재원으로 한국연구재단의 지원을 받아 수행된 기초연구사업(Grant No. NRF–2019R1F1A1041995)의 연구 결과이며 이에 감사드립니다.
References
-
M. Granovskii, I. Dincer, M. A. Rosen, “Environmental and economic aspects of hydrogen production and utilization in fuel cell vehicles”, Journal of Power Sources, Vol. 157, No. 1, 2006, pp. 411-421.
[https://doi.org/10.1016/j.jpowsour.2005.07.044]
-
I. Dincer and C. Acar, “Review and evaluation of hydrogen production methods for better sustainability”, International Journal of Hydrogen Energy, Vol. 40, No. 34, 2015, pp. 11094-11111.
[https://doi.org/10.1016/j.ijhydene.2014.12.035]
- R. P. O'Hayre, “Fuel cell fundamentals. 1st ed.”, John Wiley & Sons, Hoboken, NJ, USA, 2006.
-
Y. YI, S. J. Park, M. S. Kim, J. S. Shin, and S. J. Shin, “A Study on optimization of reformer for kW class SOFC system”, Trans. of the Korean hydrogen and new energy society, Vol. 29, No. 4, 2018, pp. 317-323.
[https://doi.org/10.7316/KHNES.2018.29.4.317]
-
T. H. Lee, T. S. Park, T. W. Kim, J. H. Noh, and Y. J. Kang, “Heat exchanger design for the individually allocated fuel cell for 1kw power generation”, Trans. of the Korean Hydrogen and New Energy Society, Vol. 25, No. 1, 2014, pp. 39-46.
[https://doi.org/10.7316/KHNES.2014.25.1.039]
-
M. Irani, A. Alizadehdakhel, A. N. Pour, N. Hoseini, and M. Adinehnia, “CFD modeling of hydrogen production using steam reforming of methane in monolith reactors: surface or volume-base reaction model?”, International Journal of Hydrogen Energy, Vol. 36, No. 24, 2011, pp. 15602-15610.
[https://doi.org/10.1016/j.ijhydene.2011.09.030]
-
P. Ferreira-Aparicio, M. J. Benito, and J. L. Sanz, “New trends in reforming technologies: from hydrogen industrial plants to multifuel microreformers”, Catalysis Reviews, Vol. 47, No. 4, 2005, pp. 491-588.
[https://doi.org/10.1080/01614940500364958]
-
A. Y. Tonkovich, S. Perry, Y. Wang, D. Qiu, T. LaPlante, and W. A. Rogers, “Microchannel process technology for compact methane steam reforming”, Chemical Engineering Science, Vol. 59, No. 22-23, 2004, pp. 4819-4824.
[https://doi.org/10.1016/j.ces.2004.07.098]
-
M. Zanfir and A. Gavriilidis, “Catalytic combustion assisted methane steam reforming in a catalytic plate reactor”, Chemical Engineering Science, Vol. 58, No. 17, 2003, pp. 3947-3960.
[https://doi.org/10.1016/S0009-2509(03)00279-3]
-
I. Schjølberg, C. Hulteberg, I. Yasuda, and C. Nelsson, “Small scale reformers for on-site hydrogen supply”, Energy Procedia, Vol. 29, 2012, pp. 559-566.
[https://doi.org/10.1016/j.egypro.2012.09.065]
-
X. Zhai, Y. Cheng, Z. Zhang, Y. Jin, and Y. Cheng, “Steam reforming of methane over Ni catalyst in micro-channel reactor”, International Journal of Hydrogen Energy, Vol. 36, No. 12, 2011, pp. 7105-7113.
[https://doi.org/10.1016/j.ijhydene.2011.03.065]
-
C. Cao, N. Zhang, and Y. Cheng, “Numerical analysis on steam methane reforming in a plate microchannel reactor: Effect of washcoat properties”, International Journal of Hydrogen Energy, Vol. 41, No. 42, 2016, pp. 18921-18941.
[https://doi.org/10.1016/j.ijhydene.2016.09.034]
-
J. Chen, X. Gao, L. Yan, and D. Xu, “Millisecond methane steam reforming for hydrogen production: a computational fluid dynamics study”, International Journal of Hydrogen Energy, Vol. 43, No. 29, 2018, pp. 12948-12969.
[https://doi.org/10.1016/j.ijhydene.2018.05.039]
-
S. M. Baek, J. H. Kang, K. J. Lee, and J. H. Nam, “A numerical study of the effectiveness factors of nickel catalyst pellets used in steam methane reforming for residential fuel cell applications”, International Journal of Hydrogen Energy, Vol. 39, No. 17, 2014, pp. 9180-9192.
[https://doi.org/10.1016/j.ijhydene.2014.04.067]
-
J. H. Nam, “Effectiveness factor correlations for spherical nickel catalyst pellets used in small-scale steam methane reformers”, International Journal of Hydrogen Energy, Vol. 40, No. 16, 2015, pp. 5644-5652.
[https://doi.org/10.1016/j.ijhydene.2015.02.119]
-
A. Jeong, D. Shin, S. M. Baek, and J. H. Nam, “Effectiveness factor correlations from simulations of washcoat nickel catalyst layers for small-scale steam methane reforming applications”, International Journal of Hydrogen Energy, Vol. 43, No. 32, 2018, pp. 15398-15411.
[https://doi.org/10.1016/j.ijhydene.2018.06.059]
- ANSYS, “ANSYS fluent theory guide (Release 15.0)”, ANSYS Inc. and SAE IP Inc., 2013. Retrieved from http://www.pmt.usp.br/academic/martoran/notasmodelosgrad/ANSYS%20Fluent%20Users%20Guide.pdf, .
-
J. Xu and G. F. Froment, “Methane steam reforming, methanation and water-gas shift: I. Intrinsic kinetics”, AIChE Journal, Vol. 35, No. 1, 1989, pp. 88-96.
[https://doi.org/10.1002/aic.690350109]
- R. B. Bird, E. N. Lightfoot, and W. E. Stewart, “Transport phenomena. 2nd ed.”, John Wiley & Sons, USA, 2002.
-
E. N. Fuller, P. D. Schettler, and J. C. Giddings, “New method for prediction of binary gas-phase diffusion coefficients”, Industrial & Engineering Chemistry, Vol. 58, No. 5, 1966, pp. 18–27.
[https://doi.org/10.1021/ie50677a007]
- M. Kaviany, “Principles of heat transfer in porous media. 2nd ed.”, Springer, USA, 1999.
- E. A. Mason and A. P. Malinauskas, “Gas transport in porous media: the dusty-gas model”, Elsevier, Netherlands, 1983.