
스퍼터링 니켈박막 연료극 적용 수소공급 저온 세라믹 연료전지의 초기작동 안정성 평가
2022 The Korean Hydrogen and New Energy Society. All rights reserved.
Abstract
The initial operation stability of hydrogen-fueled, solid oxide fuel cell with Ni thin-film anode fabricated by direct current sputtering was evaluated in terms of electrochemical properties such as peak power density, open circuit voltage, overpotential, and alternating current impedance at 500°C. Hydrogen and air were used as anode fuel and cathode fuel, respectively.
Keywords:
Initial operation stability, Ni thin-film anode, Direct current sputtering, Hydrogen, Low-temperature solid oxide fuel cell키워드:
초기작동 안정성, 니켈박막 연료극, 직류 스퍼터링, 수소, 저온 세라믹 연료전지1. 서 론
지구의 계속되는 온난화 및 증가하는 에너지 소비는 온실가스를 다량 배출하는 화석연료 기반 에너지를 대체하는 신재생에너지의 필요성을 부각시키고 있다. ‘외부에서 공급되는 연료를 전기화학적으로 에너지로 변환’하는 기능을 가지는 연료전지는 화학에너지를 추가적인 기계에너지 손실 없이 바로 전기에너지로 변환할 수 있는 작동 특성상 기존의 에너지 변환장치(예: 엔진, 터빈)와 비교하여 높은 효율을 제공하는 특징을 가진다. 특히, 세라믹 연료전지(세라믹을 전해질 소재로 사용하는 연료전지)는 고효율의 전기와 양질의 폐열을 생산할 수 있는 장점으로 인해 각광받는 연료전지 형태로 고려되고 있다. 그럼에도 불구하고 일반적인 세라믹 연료전지의 작동 온도는 800°C 이상으로 매우 높기 때문에 1) 활용 가능 소재의 폭이 매우 좁고 2) 시동/정지 사이클에 취약하다는 단점이 있다. 이러한 단점을 극복하기 위해 세라믹 연료전지의 작동 온도를 낮추는 것이 효과적인 방안으로 고려되며 이를 위해 세라믹 전해질의 두께를 줄이는 실험적 검증을 바탕으로 최근 활발히 제안되고 있다1).
기존 세라믹 연료전지보다 훨씬 낮은 온도에서 작동되는 저온 세라믹 연료전지(Fig. 1)로부터 높은 출력밀도를 얻기 위해서는 박막 전해질이 사용되어야 함과 동시에 스케일 측면 양립성을 고려하여 박막 전극이 사용될 필요가 있다. 니켈은 연료극 분위기에서 화학적으로 안정하며 높은 전기전도도 그리고 전기화학적 활성도를 제공하는 소재이며 스퍼터링 기법을 통해 비교적 용이하게 제작될 수 있다. 니켈박막 연료극을 사용하는 저온 세라믹 연료전지에 대한 연구가 활발히 진행된 바 있으며 주요 연구는 다음과 같다. Ji 등2)은 100-400 nm 두께의 스퍼터링 니켈박막 연료극을 갖는 나노 다공성 알루미나 기판 지지형 세라믹 연료전지를 제작하여 전기전도도, 가스투과도 등을 종합적으로 검토한 바 있다. 이 연구에서는 100 nm 두께의 니켈 연료극이 상대적으로 높은 전기전도도를 제공하였고 250 nm보다 얇은 니켈 연료극은 0.5 이상의 수소투과도를 보였다. 특히 니켈 연료극의 평형방향 집전성능은 대면적 설계에서 중요한 변수임이 평가되었다. Lee 등3)은 150-450 nm 두께의 스퍼터링 니켈박막 연료극을 갖는 나노다공성 알루미나 기판 지지형 세라믹 연료전지를 제작하였고, 니켈 연료극의 미세구조는 스퍼터링 진공도 제어를 통해 조절되었다. 이 연구에서는 다공성 니켈 연료극 적용 시 두께 증가에 의해 출력이 증가하는 반면 치밀한 니켈 연료극 적용 시 두께 증가는 출력을 다소 감소시킴을 보여주었다. Lee 등4)은 150-1,200 nm 두께의 스퍼터링 니켈박막 연료극을 갖는 나노다공성 알루미나 기판 지지형 세라믹 연료전지를 제작하였고, 여기서 나노다공성 기판의 기공 크기는 80 nm 과 200 nm로 다양하였다. 450 nm보다 두꺼운 니켈 연료극에 대해서는 200 nm 기공 크기의 나노다공성 알루미나 기판 사용 시, 출력밀도가 비교군보다 모두 높게 생성되었으며 500oC에서 290 mW/cm2 이상의 높은 출력밀도를 생성하였다. 한편, 위와 같은 연구들에도 불구하고 니켈박막 연료극을 갖는 저온 세라믹 연료전지의 시간에 따른 성능 변화에 관한 이해는 매우 부족한 실정이며 성능 안정성의 확보는 상용화에 있어서 매우 중요한 요건에 해당한다.
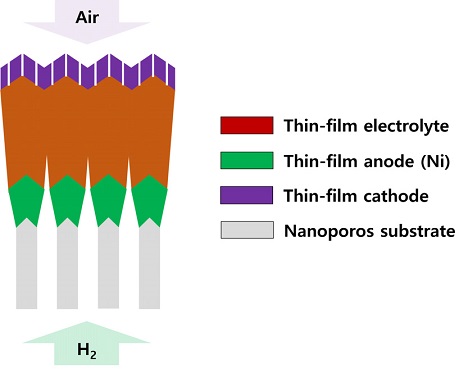
A schematic diagram of hydrogen-fueled, low-temperature solid oxide fuel cell (LT-SOFC) with Ni thin-film anode
본 연구에서는 스퍼터링을 통해 제작되는 니켈박막 연료극을 갖는 저온 세라믹 연료전지의 출력밀도 변화를 살펴보았고 이것의 변화거동을 설명하기 위해 개회로전압, 손실전압, 임피던스를 비교 분석하였다. 특히, 임피던스의 분석 결과는 오믹저항이 비오믹저항과 비교하여 증가율은 크지만 증가량은 작은 결과를 보여주며 비오믹저항의 증가가 출력밀도 감소의 주된 요인인 것으로 판단된다.
2. 방 법
저온 세라믹 연료전지는 나노다공성 알루미나를 기판으로, 니켈 연료극, 이트리아안정화지르코니아 전해질, 백금 공기극에 대한 직류 스퍼터링 을 통해 제작되었다. 나노다공성 알루미나 기판은 약 80 nm 크기의 기공을 가지고 두께는 100 μm이다. 니켈 연료극은 나노다공성 알루미나 기판상에서 다공성 미세구조를 생성함과 동시에 높은 집전성능을 제공하기 위해 5 mTorr 아르곤 분위기(비교적 고진공)에서 증착하였고 두께는 300 nm로 조절하였다. 이트리아안정화지르코니아 전해질은 이트륨/지르코늄 금속 타겟을 사용하여 치밀한 미세구조를 갖도록 10 mTorr 아르곤/산소 분위기에서 증착하였고 두께는 500 nm로 조절하였다. 백금 공기극은 다공성 미세구조를 갖기 위해 50 mTorr 아르곤 분위기에서 증착하였고 두께는 80 nm로 조절하였다.
저온 세라믹 연료전지의 성능평가는 공기극 표면이 백금 와이어와의 물리적 접촉을 통해 집전되는 단위셀 테스트 장치를 통해 수행되었다(Fig. 2). 전기화학적 성능분석은 전자부하기와 임피던스 측정기를 통해 수행되었다. 임피던스 측정은 0.5 V와 개회로전압에서 수행되었다. 연료전지의 활성면적(공기극 크기)은 1 mm2로 설정하였다. 1 A/cm2 기준 당량비 5에 해당하는 수소를 연료극에 공급하였고 상압 공기가 공기극에 수동으로 공급되었다. 가열로는 5 oC/min 속도로 승온하였고 500oC에서 10분 유지 후 성능을 측정하였다.
3. 결과 및 고찰
3.1 초기작동에 따른 출력밀도 변화
저온 세라믹 연료전지의 초기작동에 의한 출력밀도 변화를 살펴보기 위해 작동 초기 그리고 작동 0.5시간 후의 전류밀도에 대한 전압 값을 얻고 그로부터 출력밀도(전류밀도와 전압의 곱)를 산출하였다. Fig. 3은 전류밀도에 대한 출력밀도 그래프를 보여주고 있다. 작동 0.5시간 후에 측정된 출력밀도는 모든 전류밀도 영역에 있어서 작동 초기에 측정된 출력밀도보다 낮다는 것을 알 수 있다. 작동 초기의 최대 출력밀도는 113 mW/cm2로 측정되었고 작동 0.5시간 후의 최대 출력밀도는 83 mW/cm2로 측정되었으며, 이를 통해 0.5시간의 초기작동을 통해 최대 출력밀도가 30% 감소함을 알 수 있다. 작동 초기의 출력밀도는 고전류밀도 영역(400 mA/cm2 이상)에서 급격히 감소한 반면 작동 0.5시간 후의 출력밀도는 고전류밀도 영역(200 mA/cm2 이상)에서 상대적으로 완만하게 감소됨을 알 수 있다. 최대 출력밀도의 감소율은 0.5시간 동안 30%로 평가되었으며, 단순 선형감소를 가정하면 약 100분 작동 후에 연료전지 수명이 다함을 예상할 수 있다. 따라서 본 연구에서는 제안하는 저온 세라믹 연료전지의 상용화 가능성을 향상시키기 위해서는 작동 초기의 출력밀도 저하를 줄이기 위한 방안 마련이 필수적일 것으로 판단된다. 한편, 출력밀도를 결정하는 주요 성능지표인 개회로전압, 손실전압, 임피던스의 변화 양상을 분석하고자 한다.
3.2 초기작동에 따른 개회로전압 및 손실전압 변화
개회로전압은 전해질에 의해 독립된 분위기를 갖는 연료전지에 있어서 기밀측면 전해질 신뢰성을 간접적으로 평가할 수 있는 성능지표에 해당한다. 이러한 개회로전압은 전해질을 통한 기체투과 또는/그리고 전극침투 발생 시 그 수치가 낮아지는 경향이 있다. Fig. 4에서의 우측상단 그래프는 작동 초기 그리고 작동 0.5시간 후 측정된 저온 세라믹 연료전지의 개회로전압 값을 보여주고 있다. 작동 초기의 개회로전압은 1.2 V로 측정되었고 작동 0.5시간 후의 개회로전압은 1.13 V로 측정되었으며, 이를 통해 0.5시간의 초기작동으로 개회로전압이 6% 감소하였음을 알 수 있다. 작동 초기 개회로전압 값은 1.2 V로 충분히 높게 나타났으며 이러한 값은 네른스트식(작동 온도 그리고 반응물과 생성물 분압으로부터 산출된 이론적인 전압 값)을 통해 얻어지는 개회로전압 값에 상당히 근접한 수치다. 이를 통해 낮은 등방성을 보이는 물리적 기상증착의 주상구조 성장 특성에도 불구하고 기밀측면 신뢰성이 높은 전해질 박막이 니켈 연료극 상부에 성막된 것으로 판단할 수 있다. 저온 세라믹 연료전지의 단면형상 분석 결과(Fig. 5)를 살펴보면 니켈 연료극 표면에서부터 생성된 핀홀이 전해질 하부의 수십 나노미터 높이까지 형성되었음에도 불구하고 전해질의 총 두께(500 nm)에 있어서 전해질을 관통하는 핀홀은 관찰되지 않았다. 이러한 결과는 초기작동 이전 전해질 박막의 성막 완성도는 높다는 것을 보여준다. 한편, 저온 세라믹 연료전지의 기판으로 사용된 알루미나 연료극으로 사용된 니켈, 전해질로 사용된 이트리아안정화지르코니아의 열팽창 계수(단위: 10-6 m/[m·K])는 각각 8.1, 13.4, 10.5로 비교적 큰 차이가 있다. 이러한 차이는 작동 온도인 500oC로의 승온 시(상온 기준 약 480oC 온도 상승) 전해질을 포함한 박막 요소들의 기계적 결함을 발생시켜 개회로전압 감소의 원인이 될 수 있다5). 알루미나 기판과 비교하여 열팽창 계수가 큰 니켈 연료극은 승온 시 수축력이 내부에 가해지는 반면 니켈 연료극과 비교하여 열팽창 계수가 작은 이트리아안정화지르코니아 전해질은 이완력이 내부에 가해질 것이다.
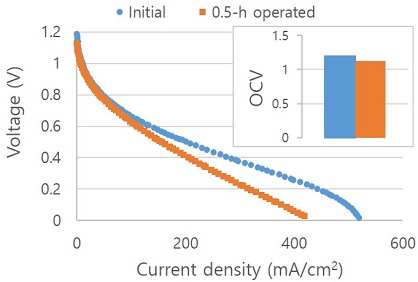
Open circuit voltage (OCV) and voltage curves of initial and 0.5 h-operated LT-SOFC with Ni thin-film anode at 500°C
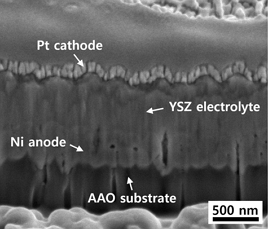
A focused ion beam-prepared field emission scanning electron microscopic, cross-sectional image of LT-SOFC composed of anodic aluminum oxide (AAO) substrate, Ni anode, yttria-stabilized zirconia (YSZ) electrolyte, and Pt cathode
작동시간에 관계없이 손실전압은 전류밀도가 증가함에 따라 계속해서 증가하였으며 특히 활성화손실로 인한 저전류밀도에서의 손실전압이 상대적으로 크게 나타났으며(Fig. 4), 전류밀도 전 영역에 있어서 작동 0.5시간 후 상대적으로 높은 손실전압이 발생됨을 보여주고 있다. 특히, 작동 초기 고전류밀도에서 눈에 띄는 손실전압이 나타났기 때문에 물질전달 저항이 높게 나타남을 알 수 있는 반면 작동 0.5시간 후 고전류밀도에의 눈에 띄는 손실전압은 나타나지 않았고 이는 물질전달 저항이 미비함을 보여주고 있다6). 작동 초기 결과는 고체적 밀도의 미세입자로 구성된 니켈 연료극 또는/그리고 백금 공기극을 통한 가스이송 저항으로 인한 것인 반면 작동 0.5시간 후 그러한 입자들의 열적 뭉침 현상으로 인한 가스이송 경로의 증가로 해당 저항이 감소되었기 때문으로 예상된다. 오믹저항과 비오믹저항에 대한 분석은 다음 절의 임피던스 측정 결과를 통해 수행하였다.
3.3 초기작동에 따른 임피던스 변화
Fig. 6(a)는 작동 초기 그리고 작동 0.5시간 후 저온 세라믹 연료전지의 0.5 V 인가 시 임피던스 곡선을 보여주고 있다. 작동 초기의 총 임피던스 값은 2.5 ohm cm2였고 작동 0.5시간 후의 총 임피던스는 3 ohm cm2였으며, 이를 통해 0.5시간의 초기작동으로 임피던스는 20% 증가되었음을 알 수 있다. 임피던스의 증가는 3.2절에서 살펴본 손실전압의 증가 경향과 상통한 양상을 보여준다. 작동 초기 그리고 작동 0.5시간 후 모두 1 MHz와 1 kHz의 시상수를 가지는 임피던스 반원이 비교적 뚜렷하게 나타났으며 이들은 전해질 입자경계 저항, 전극촉매 반응, 물질전달 저항 영향을 종합적으로 보여주는 것이다7). 특히 1 MHz 시상수에 대한 임피던스 반원은 Fig. 6(b)에서 제시되는 것처럼 전압 값에 관계없이 중첩되는 현상을 보이며 전극촉매 반응과 물질전달 저항에 기인한 것은 아님을 보여주었다. 따라서 본 결과들과 기존 관련 연구들을 바탕으로, 1 MHz 시상수를 가지는 임피던스 반원은 전해질 입자경계 저항으로부터 기인하고 1 kHz 시상수를 가지는 임피던스 반원은 전극촉매 반응으로부터 기인함을 고려할 수 있다.
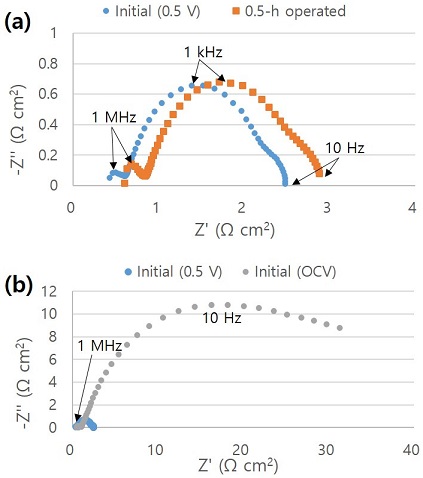
(a) Impedance curves of Initial and 0.5-h operated LT-SOFC at 500°C (0.5 V-biased) and (b) impedance curves of initial LT-SOFC at OCV and 0.5 V
Fig. 7은 Fig. 6(a)의 임피던스 데이터로부터 얻은 저항 값을 오믹저항, 비오믹저항(전해질 입자경계 저항, 전극촉매 반응, 물질전달 저항의 합)으로 구분한 것이다. 임피던스 곡선에서의 고주파수(10 MHz) 절편에 해당하는 값인 오믹저항의 경우 작동 초기 0.43 ohm cm2였고 0.5시간 작동 후 0.6 ohm cm2였으며, 이를 통해 0.5시간 초기작동에 의해 오믹저항은 40% 증가하였음을 알 수 있다. 오믹저항에 영향을 미치는 요소는 전해질 전도저항과 전극 집전저항이며, 본 연구에서는 500 nm의 매우 얇은 전해질 사용으로 전해질 전도저항은 상당히 작기 때문에 집전저항이 대부분을 차지할 것이다. 집전저항의 증가는 공기극으로 사용된 80 nm 두께의 매우 얇은 백금 박막의 입자 뭉침 및 입자클러스터 단락으로 인한 전자전도 경로의 감소로 인한 것으로 보인다8). 니켈 연료극의 경우 기판과 전해질 사이에 삽입된 구조로 백금 공기극에 비해 상대적으로 높은 열기계적 안정성을 가질 것이다. 초기작동에 따른 비오믹저항은 상대적으로 낮은 증가율(15%)을 보였다. 그럼에도 불구하고 저항 증가량의 경우 오믹저항과 비오믹저항은 각각 0.17 ohm cm2와 0.3 ohm cm2였고, 이를 통해 출력밀도의 감소에는 비오믹저항이 상대적으로 더 크게 기여했음을 알 수 있다. 특히 이러한 비오믹저항의 눈에 띄는 증가는 승온 환경에서 상당히 높은 표면에너지를 갖는 백금 공기극 입자(다공성 미세구조)의 활발한 열적 뭉침 현상으로 인한 삼상계면 감소 때문일 것으로 기존의 타 연구들을 바탕으로 예상할 수 있다1).
4. 결 론
본 연구에서는 스퍼터링을 통해 제작되는 니켈박막 연료극을 갖는 저온 세라믹 연료전지의 수소공급 시 초기작동 안정성 평가를 위해 500oC에서의 출력밀도 변화를 측정하였다. 출력밀도는 초기작동에 의해 크게 감소하였고 이에 대한 요인을 살펴보기 위해 개회로전압, 손실전압, 임피던스 변화를 초기작동 0.5시간 동안 살펴보았으며 결과 및 고찰의 핵심은 다음과 같다.
1) 출력밀도는 30% 감소하였기 때문에 단순 산출 시 총 작동 가능시간은 100분 이내로 상용화를 위한 기술개선 필요성을 보여주었다.
2) 개회로전압은 6% 감소하였으며 이는 기판/연료극/전해질 소재의 열팽창 계수 차이로부터 기인한 것으로 판단된다.
3) 작동 초기의 손실전압에서는 고전류밀도에서 높은 물질전달 저항이 관찰되었지만 초기작동 후 그러한 저항은 미비하게 나타났다.
4) 임피던스 분석을 통해, 오믹저항과 비오믹저항의 증가율은 각각 40%와 15%였고 증가량은 각각 0.17 ohm cm2와 0.3 ohm cm2였다. 이에 따라 출력밀도의 감소에는 비오믹저항의 영향이 상대적으로 큰 것으로 평가될 수 있다.
Acknowledgments
본 연구는 한국건설기술연구원 내부사업(No. 20220232, 20220081)과 한국연구재단 이공분야기초연구사업(No. NRF-2018R1D1A1B07048082)의 지원에 의해 수행되었다.
References
-
Y. H. Lee, I. Chang, G. Y. Cho, J. Park, W. Yu, W. H. Tanveer, and S. W. Cha, “Thin film solid oxide fuel cells operating below 600°C: a review”, International Journal of Precision Engineering and Manufacturing - Green Technology, Vol. 5, No. 3, 2018, pp. 441-453.
[https://doi.org/10.1007/s40684-018-0047-0]
-
S. Ji, H. G. Seo, S. Lee, J. Seo, Y. Lee, W. H. Tanveer, S. W. Cha, and W. C. Jung, “Integrated design of a Ni thin-film electrode on a porous alumina template for affordable and high-performance low-temperature solid oxide fuel cells”, RSC Advances, Vol. 7, No. 38, 2017, pp. 23600-23606.
[https://doi.org/10.1039/C7RA02719B]
-
Y. Lee, J. Park,W. Yu, W. H. Tanveer, Y. H. Lee, G. Y. Cho, T. Park, C. Zheng, W. Lee, and S. W. Cha, “Nickel-based bilayer thin-film anodes for low-temperature solid oxide fuel cells”, Energy, Vol. 161, 2018, pp. 1133-1138.
[https://doi.org/10.1016/j.energy.2018.07.147]
-
M. S. Lee, S. Lee, W. Jeong, S. Ryu, W. Yu, Y. H. Lee, G. Y. Cho, and S. W. Cha, “Nanoporous nickel thin film anode optimization for low-temperature solid oxide fuel cells”, International Journal of Hydrogen Energy, Vol. 46, No. 73, 2021, pp. 36445-36453.
[https://doi.org/10.1016/j.ijhydene.2021.08.138]
-
F. Tietz, “Thermal expansion of SOFC materials”, Ionics, Vol. 5, 1999, pp. 129-139.
[https://doi.org/10.1007/BF02375916]
-
Q. Yan, H. Toghiani, and H. Causey, “Steady state and dynamic performance of proton exchange membrane fuel cells (PEMFCs) under various operating conditions and load changes”, Journal of Power Sources, Vol. 161, No. 1, 2006, pp. 492-502.
[https://doi.org/10.1016/j.jpowsour.2006.03.077]
-
S. Ji, Y. H. Lee, T. Park, G. Y. Cho, S. Noh, Y. Lee, M. Kim, S. Ha, J. An, and S. W. Cha, “Doped ceria anode interlayer for low-temperature solid oxide fuel cells with nanothin electrolyte”, Thin Solid Films, Vol. 591, Part B, 2015, pp. 250-254.
[https://doi.org/10.1016/j.tsf.2015.05.005]
-
C. W. Kwon, J. I. Lee, K. B. Kim, H. W. Lee, J. H. Lee, and J. W. Son, “The thermomechanical stability of micro-solid oxide fuel cells fabricated on anodized aluminum oxide membranes”, Journal of Power Sources, Vol. 210, 2012, pp. 178-183.
[https://doi.org/10.1016/j.jpowsour.2012.03.020]