
음이온 교환막 수전해용 Pt-Fe/카본블랙 나노 촉매 제조 및 특성
2022 The Korean Hydrogen and New Energy Society. All rights reserved.
Abstract
Pt-Fe/carbon black nanocatalysts were prepared by spontaneous reduction reaction of Platinum(II) acetylacetonate and Iron(II) acetylacetonate in a nucleophilic solvent and they were characterized by scanning electron microscopy (SEM), energy dispersive X-ray analyzer (EDS), thermogravimetric analyzer (TGA), transmission electron microscopy (TEM), Brunauer, Emmett and Teller (BET) surface area analysis and anion exchange membrane (AEM) water electrolysis test station. The distribution of the Pt and Fe nanoparticles on carbon black was observed by TEM, and the loading weight of Pt-Fe nanocatalysts on the carbon black was measured by TGA. Elemental ratio of Fe:Pt was estimated by EDS and it was found that elemental ratio of Pt and Fe was changed in the range of 1:0 to 0:1, and the loading weight of Pt-Fe nanoparticles on the carbon black was 5.95-6.78 wt%. Specific surface area was greatly reduced because Pt-Fe nanocatalysts blocked the pores. I–V characteristics were estimated.
Keywords:
Anion exchange membrane, AEM water electrolysis, Pt nanocatalyst, Fe nanocatalyst키워드:
음이온 교환막, AEM 수전해, 백금 나노 촉매, 철 나노 촉매1. 서 론
산업혁명 이후 화석연료 사용량 증가로 인해 온실가스(greenhouse gas) 배출이 지구환경에 악영향을 미치고 있다1-5). 즉, 배출가스의 주성분인 이산화탄소는 대기 중에 축적됨으로 인해 지구 온난화와 기후 변화의 주요 원인으로 작용하고 있다. 산업혁명 이전 대기 중 이산화탄소 농도는 280 ppm 정도였고, 산업사회가 고도화됨에 따라 2020년 413.2 ppm에 도달하였으며, 이는 산업화 이전 수준의 148%에 해당하는 값이다1,2). 이와 같은 속도로 증가할 경우 2050년에는 약 530 ppm에 다다를 것으로 예상되며, 이렇게 되면 지구 온난화 및 기후 변화 문제는 돌이킬 수 없게 될 것으로 예측된다1). 따라서 화석연료 소비 감축을 통한 온실가스 영향을 완화시키기 위해 지난 몇십 년 동안 탄소를 대체할 수 있는 에너지원으로 무독성이면서 에너지 밀도(140 MJ/kg)가 높고, 에너지 효율(>70%)이 높은 수소를 신규 에너지 운반체로 활용하는 기술 개발이 지속되고 있다3).
수소를 생산하는 방법으로는 석유화학 및 제철공업 등의 부생 수소, 수증기 개질 반응, 수전해, 열분해, 광촉매 및 바이오매스 가스화 등과 같은 것들이 있으나4), 수소 생산비용과 효율을 고려할 때 현재는 부생 수소와 수증기 개질 방식이 거의 대부분 채택되고 있고, 궁극적으로는 수전해 방식으로 전환될 것으로 기대되고 있다. 2020년 세계 수소 생산량은 약 1억 톤 정도이며, 그 가운데 대부분은 그레이 수소 방식(부생 수소 및 개질 수소)으로 생산되고 있고, 약 1백만 톤 정도만이 블루 수소 방식으로 생산되고 있으며, 그린 수소 시장은 매우 미흡한 상황이다5). 국내 수소 생산량은 2020년에 198만 톤 정도이고, 화석연료 기반의 그레이 수소(부생 수소 및 개질 수소)가 100%를 차지하고 있다3). 그러나 부생 수소나 개질 수소를 사용하는 것은 수소 사용 단계에서는 온실가스가 발생하지 않지만, 수소 생산 단계에서 이미 이산화탄소를 많이 배출했기 때문에 엄밀한 의미에서 친환경 연료가 아니다. 따라서 급속히 증가하는 에너지 수요를 지속적으로 충족시키면서 친환경적인 고순도 수소(99.999%)를 얻기 위해서 수전해 방식이 새로운 대체기술로 떠오르고 있다.
수전해 법은 사용되는 전해질과 이동되는 이온의 종류에 따라 (i) 강알칼리 수용액(KOH 용액)을 전해질로 사용하는 알칼리 수전해, (ii) 양이온 폴리머 막을 고체 전해질로 사용하는 양이온 교환막 수전해 및 (iii) 고체 세라믹을 전해질로 사용하는 고체 산화물 수전해 등으로 분류된다6,7). 최근에는 강알칼리를 사용하는 알칼리 수전해와 고가의 귀금속 촉매를 사용하는 양이온 교환막 수전해의 단점들을 개선하기 위해 저가의 전이금속 촉매를 사용하는 음이온 교환막 수전해에 대한 연구가 활발히 진행되고 있다4,8). 또한 OH- 이온의 전달 속도를 증가시키면서 내구성이 향상된 음이온 폴리머 막을 제조할 필요성이 증대되고 있다9,10).
음이온 교환막 수전해 장치에서 수소 및 산소 발생 메커니즘은 다음과 같다. 먼저 캐소드 측의 촉매층에서 2분자의 H2O에 2개의 전자가 공급되면서 1분자의 수소(H2)와 2개의 하이드록실 이온(OH-)을 생성한다. 생성된 H2는 캐소드 촉매 표면으로부터 떨어져서 기체 형태로 방출된다. 캐소드 측에서 생성된 2개의 OH- 이온은 음이온 폴리머 막을 통해 애노드 측으로 이동한 후 1/2 분자의 산소(O2)와 1분자의 H2O 및 2개의 전자를 생성한다. 생성된 O2는 애노드 촉매 표면으로부터 떨어져서 기체 형태로 방출된다4,5). 캐소드 전극층의 수소 발생 반응(hydrogen evolution reaction) 촉매로는 Pt가 가장 우수하지만, 너무 고가이면서 채굴량에 한계가 있기 때문에 저가의 촉매를 개발할 필요성이 날로 증대되고 있다. 이와 같은 관점에서 anion exchange membrane (AEM) 수전해에서는 Ni, Fe, Co 등과 같은 저가의 전이금속 촉매들을 단독 또는 복합 촉매 형태로 사용하거나, 금속 산화물 또는 C, N, O, P, S 등과 같은 비금속 원소들을 도핑한 형태로 사용될 수 있으며, 그 성능이 크게 개선된 결과들을 보고하고 있다11-14).
본 연구에서는 친핵성 용매 중에서 Pt 및 Fe 전구체를 자발적으로 환원시켜서 AEM 캐소드용 Pt-Fe 혼합 촉매를 제조하였고, Pt와 Fe 혼합비가 촉매 활성에 미치는 영향을 연구하였다.
2. 실험 방법
2.1 재료
Pt-Fe 혼합 촉매를 제조하기 위해 Pt 및 Fe 전구체는 Sigma-Aldrich사의 Platinum(II) acetylacetonate (Pt(acac)2)와 Iron(II) acetylacetonate (Fe(acac)2)를 구입하여 사용하였고, 친핵성 용매는 대정화금㈜의 N,N-dimethylformamide (DMF)를 사용하였다. 촉매 지지체는 Cabot Switzerland GmbH사의 Vulcan XC-72 카본블랙를 사용하였고, 음이온 아이노머는 Fumatech BWT GmbH사의 Fumion FAA-3-SOLUT-10를 사용하였다. 캐소드 측 전극 제조를 위해 Fuel Cells Etc사의 GDL-CT를 기체 확산층(gas diffusion layer, GDL)으로 사용하였고, 애노드 측의 기체 확산 전극(gas diffusion electrode, GDE)도 같은 회사의 2 mg/cm² Platinum Black–Cloth (W1S1009) 제품을 사용하였다. 음이온 전해질 막은 Fumatech BWT GmbH사의 Fumapem FAA-3-PK-75 제품을 사용하였다.
2.2 Pt-Fe 혼합 촉매 제조
비이커에 카본블랙 40 g과 DMF 180 g을 넣고, 초음파 분산기를 사용하여 750 Watts, 20 kHz의 출력으로 3시간 처리하였고, 초음파 출력을 유지하면서 Pt(acac)2와 Fe(acac)2를 다양한 비율로 용해시켰다. Pt(acac)2:Fe(acac)2의 혼합비는 0.5:0, 0.4:0.1, 0.3:0.2, 0.2:0.3, 0.1:0.4 및 0:0.5의 비율로 변화시켰고, 동일한 초음파 조건을 유지하면서 90℃에서 5시간 유지하였다. 이 과정에서 금속 전구체들은 친핵성 DMF 용액 중에서 자발적으로 환원되어 카본블랙 표면에 로딩된다. 반응이 종결된 후, 감압 여과하여 분리하고, 아세톤으로 3회 세척하였다. 이어서 50℃에서 5시간 건조 후, 350℃에서 30분 소성 처리하고, 데시케이터에 보관하였다.
2.3 전극 및 membrane-electrode assembly (MEA) 제작
캐소드 전극 촉매 슬러리의 제조 절차는 다음과 같다. 먼저, iso-propyl alcohol과 증류수를 9:1의 중량비로 혼합한 수용액 25 g에 2.2항에서 제조된 Pt-Fe/카본블랙 촉매 18 g을 넣고 호모 믹서를 사용하여 1시간 동안 혼합하였다. 여기에 음이온 아이노머 용액, Fumion FAA-3-SOLUT-10 1 g과 에틸렌글리콜 6 g을 추가하고, 30분 더 교반하여 촉매 슬러리를 제조하였다. GDL 위에 촉매량이 0.4 mg/cm2이 되도록 스프레이 코팅하고, 실온에서 24시간 건조한 후 130℃ 질소 분위기에서 30분 소결하여 캐소드 전극을 제작하였다. 애노드 전극은 Fuel Cells Etc사 제품을 사용하였다. 전극을 2×2 cm2의 크기로 잘라내어 음이온 전해질 막을 양 쪽에 두고, 130℃, 100기압으로 2분간 가열 압착하여 MEA를 제작하였다. 이렇게 제조된 MEA를 티타늄 메쉬를 포함한 단전지 셀에 장착한 후 테스트하였다.
2.4 수전해 셀 테스트
수전해 셀 테스트를 위하여 증류수 공급부와 전력 공급 장치를 연결하고, 전류를 변화시키면서 전압을 측정하였다. 전압 측정은 전류를 목표값으로 조절하고, 전압이 안정된 상태에서 기록하였다. 테스트는 상온, 상압 조건에서 이루어졌고, 증류수, 산소, 수소는 자체 대류에 의하여 순환되게 하였다.
2.5 기기분석/특성분석
제조된 Pt-Fe/카본블랙 촉매의 모폴로지를 관찰하기 위해 전계 방사형 주사 전자현미경(field emission scanning electron microscopy [FE-SEM], JMS-6701F, JEOL Ltd., Tokyo, Japan)을 사용하였고, 원소 조성을 분석하기 위해 FE-SEM에 장착된 에너지 분산 X-선 분광분석기(energy dispersive x-ray analyzer [EDS], JED-2300, JEOL Ltd.)를 사용하였다. 이 때 가속 전압은 15 kV였다. 또한, Pt-Fe 나노 촉매의 형상 및 크기를 확인하기 위해 고분해 투과 전자현미경(high-resolution transmission electron microscopy [HR-TEM], S-4100, Hitachi Ltd., Tokyo, Japan)을 사용하였고, 이 때 가속 전압은 200 kV에서 관찰하였다. Pt-Fe 나노 촉매가 카본블랙에 로딩된 양을 평가하기 위해 열중량 분석(thermogravimetric analyzer [TGA], TherMax 500, ThermoFischer Scientific Inc., Waltham, MA, USA)을 실시하였다. 10 mg 정도의 Pt-Fe/카본블랙 샘플을 TGA 장치에 넣고, 상온에서 800oC까지 10oC/min의 승온 속도로 열중량 분석하였다. 이 때 공기 유속은 20 mL/min이였다. 그리고 제조된 Pt-Fe/카본블랙 촉매의 비표면적을 측정하기 위해서 비표면적 측정장비(ASAP 2020, Micrometritics Instrument Co., Norcross, GA, USA)를 사용하였다.
3. 결과 및 고찰
친핵성 용매에 의해 금속 전구체들이 자발적으로 환원되어 Pt와 Fe 금속 나노 입자가 생성된 것을 확인하기 위해 Fig. 1에서와 같이 Pt-Fe/카본블랙의 모폴로지를 FE-SEM으로 관찰하였고, 해당 구역에 대한 원소 조성을 확인하기 위해 Fig. 2에서와 같이 EDS 분석을 하였다. 로딩된 촉매의 종류에 관계없이 마이크로 크기의 카본블랙 입자들이 전극 표면에 균일하게 분산된 것을 확인하였고, 카본블랙의 형상에는 변화가 없었다. EDS 분석 결과 Pt 원소와 Fe 원소의 단독 또는 혼합 촉매의 특성 피크가 관찰되었고, 금속 acetylacetonate 분자 구조에 있는 카르복시기에서 기인하는 산소 특성 피크는 전혀 검출되지 않았다. 이 결과는 친핵성 용매로 사용된 DMF 중에서 Pt(acac)2 및 Fe(acac)2 전구체가 Pt와 Fe 금속 원소로 완전히 전환되었기 때문이며, 따라서 미반응 금속 전구체로 인한 산소 특성 피크는 검출되지 않았다. 다시 말해서, DMF의 formamide 그룹이 친핵체로 작용하여 acetylacetonate의 이중결합을 공격함으로써 자발적 환원반응에 의해 금속 원소로 환원되었기 때문이다15-17). EDS 분석을 통해서 금속 전구체로부터 제조된 촉매 중의 Pt와 Fe의 원소 조성비를 Table 1에 나타내었다. 금속 전구체 혼합비에 비례하여 Pt와 Fe의 생성비가 비례함을 확인하였다.
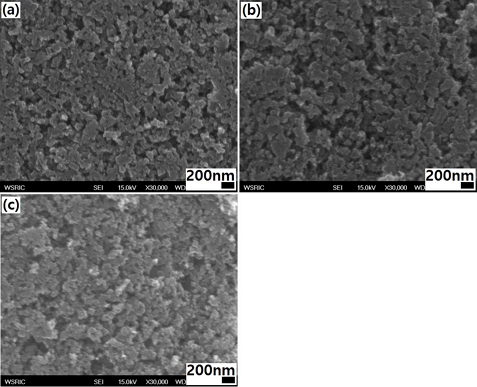
SEM image for Pt-Fe/carbon black catalysts. Mixing ratios of Pt(acac)2 and Fe(acac)2 were (a) 0.5 : 0, (b) 0.3 : 0.2, and (c) 0 : 0.5, respectively
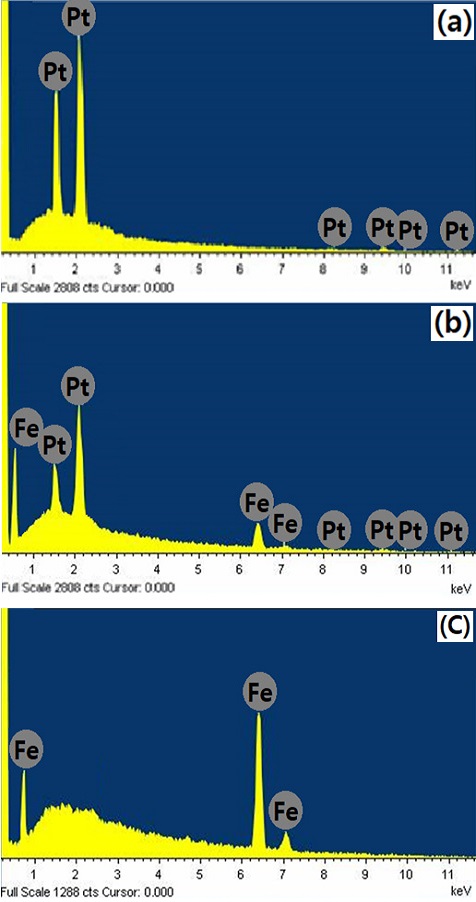
EDS spectra for Pt-Fe/carbon black catalysts. Mixing ratios of Pt(acac)2 and Fe(acac)2 were (a) 0.5 : 0, (b) 0.3 : 0.2, and (c) 0 : 0.5, respectively
Fig. 3은 Pt(acac)2와 Fe(acac)2를 다양한 혼합비로 용해시킨 후 자발적 환원 반응에 의해 Pt와 Fe 금속 촉매를 카본블랙에 로딩시킨 양을 평가하기 위해 TGA 분석한 결과이다. 각각의 열중량 곡선들에서, 카본블랙이 산소와 반응하여 CO2 형태로 모두 제거되면서 중량이 급속히 감소하다가 카본블랙이 모두 없어지면 더 이상의 중량 감소가 일어나지 않는다. 이에 반해 금속이 산화되면 중량이 증가한다. 즉, Fe는 150℃ 정도의 낮은 공기 분위기에서도 산화가 잘 일어나서 중량이 증가하게 된다. 그렇지만 Pt는 화학 반응성이 매우 낮기 때문에 1,000℃ 이상의 공기 분위기에서도 산화되지 않는다. 그렇지만 탄소와 같이 연소시킬 경우 환원 반응이 일어나기 때문에 산화에 의한 중량 증가가 일어나지 않는다18,19). 따라서 금속 촉매 로딩량은 중량 감소가 더 이상 없는 지점에서의 잔류 중량으로 평가하였으며, 그 값들을 Table 2에 나타내었다. 카본블랙 표면에 부착된 촉매 로딩량은 5.95-6.78 wt% 정도였고, Pt 함량이 감소함에 따라 전체 로딩량은 약간씩 증가하였다. 이것은 Pt 나노 입자 생성 속도가 Fe 나노 입자 생성 속도보다 느리기 때문에 Pt 나노 입자 함량이 Fet 나노 입자 함량에 비해 낮게 나타나며, 이것은 EDS 분석 결과와도 일치한다.
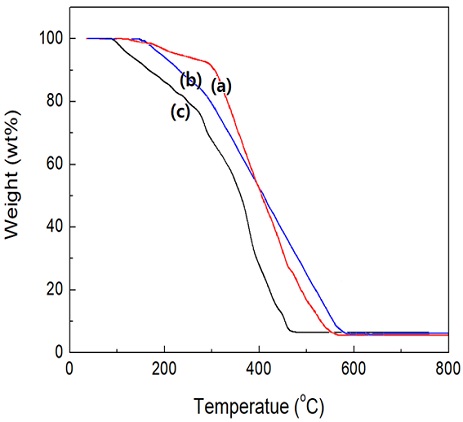
TGA curves for Pt-Fe/carbon black catalysts. Mixing ratios of Pt(acac)2 and Fe(acac)2 were (a) 0.5 : 0, (b) 0.3 : 0.2, and (c) 0 : 0.5, respectively

Loading weights of Pt-Fe catalysts on carbon black synthesized from various mixing ratios of metallic precursors
Fig. 4는 카본블랙 표면에 로딩된 Pt-Fe 나노 촉매를 HR-TEM으로 관찰한 사진이다. 구형에 가까운 나노 입자들이 카본블랙 위에 분산되어 있는 것을 볼 수 있으며, acetylacetonate계 금속 전구체가 Pt 및 Fe 금속 원소들로 환원되어 구형의 나노 촉매 입자를 형성했음을 보여준다. 나노 입자의 크기를 측정하기 위해서 고배율로 관찰하고, image analyzer에 의해 계산된 입자 크기의 평균값은 3.84 nm였다.
Fig. 5는 서포터로 사용된 (a) 카본블랙과 (b)-(d) 다양한 조성비의 Pt-Fe 로딩 카본블랙의 Brunauer, Emmett and Teller (BET) 흡착 등온선을 얻었고, BET 비표면적을 Table 3에 정리하였다. 금속 나노 입자가 로딩되지 않은 카본블랙 자체의 BET 비표면적은 233.9 m2/g이고, Pt-Fe 나노 입자가 도입된 경우에는 비표면적 값이 매우 크게 감소하였다. Pt 나노 입자만 도입된 시료의 BET 비표면적은 100.2 m2/g으로, 카본블랙 자체의 비표면적 대비 57.2% 감소되었고, Fe 나노 입자의 함량이 증가함에 따라 비표면적이 약간씩 감소하였으며, Fe 나노 입자만 도입된 경우의 BET 비표면적은 80.0 m2/g으로 카본블랙 자체의 비표면적 대비 65.8% 감소하였다. 이것은 Pt 나노 입자 및 Fe 나노 입자가 카본블랙의 기공 입구를 막음으로서 비표면적이 크게 감소한 것으로 판단된다. EDS 분석 결과에서 보듯이 Fe 나노 입자 생성 속도가 Pt 나노 입자 생성 속도보다 빠르며, TGA 분석 결과에서 보듯이 Pt 나노 입자 함량이 증가함에 따라 Pt-Fe 혼합 촉매 로딩량은 약간씩 감소하였다. 따라서 Fe 함량이 높을수록 비표면적이 감소하게 되는 것이다.
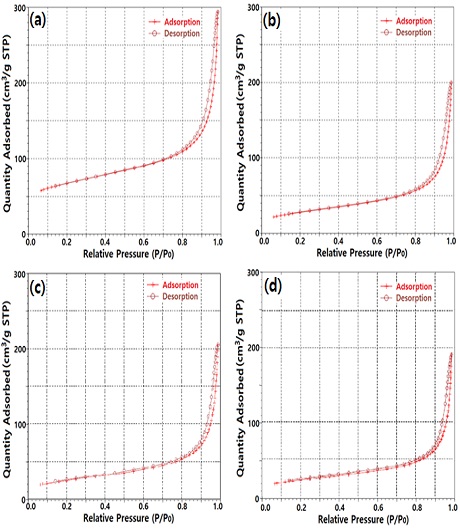
BET hysteresis curves for Pt-Fe/carbon black catalysts. Mixing ratios of Pt(acac)2 and Fe(acac)2 were (a) carbon black, (b) 0.5:0, (c) 0.2:0.3, and (d) 0:0.5, respectively
Pt 및 Fe 금속 나노 입자에 의한 카본블랙의 기공 막힘 현상을 확인하기 위해서 기공 크기별 비표면적의 변화를 비교하여 Fig. 6에 나타내었다. 기공 크기별 비표면적 분포를 분석한 결과 기공 크기가 작아짐에 따라 비표면적 감소 현상이 더 크게 나타났다. 즉, 금속 입자의 평균 입자 사이즈(3.84 nm)보다 작은 미세 기공은 입자 하나에 의해서도 기공이 막힐 수 있으므로 비표면적 감소 효과는 더 크게 나타나게 되는 것이다. 그리고 입구 지름이 큰 기공이라도 나노 입자들이 기공 내부에 생성됨으로서 50 nm 이하의 지름 크기를 갖는 기공들의 비표면적이 크게 감소하였다. 또한, Fe 나노 촉매의 로딩량이 Pt 나노 촉매보다 로딩량보다 더 많기 때문에 기공 막힘 현상이 더 크게 나타났다.
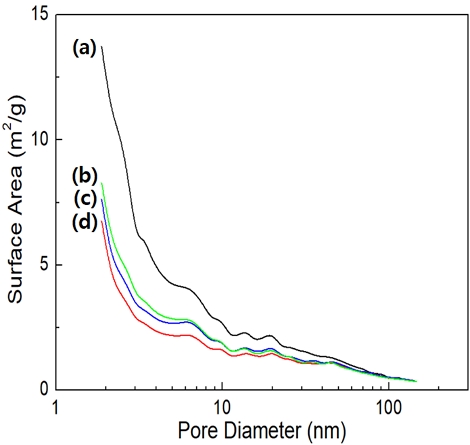
Surface area vs. pore diameter for Pt-Fe/carbon black catalysts. Mixing ratios of Pt(acac)2 and Fe(acac)2 were (a) carbon black, (b) 0.5:0, (c) 0.2:0.3, and (d) 0:0.5, respectively
다양한 조성의 Pt-Fe/카본블랙 촉매를 사용하여 제작한 수전해 셀의 I-V 특성을 Fig. 7에 나타내었다. Pt 촉매만 사용한 경우의 I-V 곡선에서 전류밀도 207.9 mA/cm2는 전압 1.8V에서 얻었고, Fe 촉매만 사용한 경우의 I-V 곡선에서 전류밀도 82.5 mA/cm2는 전압 1.8V에서 얻었으며, 이 값은 Pt 촉매만 사용한 경우에 비해 60.6% 낮은 성능이다. Pt-Fe/카본블랙 시스템에서 Pt 촉매의 함량이 증가함에 따라 전류밀도가 크게 증가하였고, 이것은 Pt의 촉매 특성이 Fe에 비해 훨씬 우수하기 때문이다. 이 값들은 alkaline water electrolysis (AWE)에 비해서는 I-V 특성이 우수하였지만, 다른 AEM에 비해서는 약간 낮은 특성을 나타내었다. 이는 금속 나노 촉매들이 카본블랙의 기공을 막음으로써 내부에 있는 촉매들이 수전해에 기여하지 못하기 때문으로 판단되며, 특히 Fe 함량이 높은 경우에는 BET 비표면적이 더 작아지기 때문에 촉매들의 기여도가 크게 감소하는 것으로 생각된다. 따라서 Pt 및 Fe 나노 촉매 크기를 더 작게 설계할 필요가 있고, 로딩량을 약간 줄여서 카본블랙 미세 기공의 막힘을 방지함으로서 촉매 활성을 개선하는 연구를 수행할 필요가 있다.
4. 결 론
친핵성 DMF 용매 중에서 acetylacetonate계 금속 전구체의 자발적 환원 반응에 의해 Pt-Fe/카본블랙 촉매를 제조할 수 있었으며, AEM 수전해 촉매로 활용 가능성을 확인하였다. Pt-Fe/카본블랙 촉매에서 Pt(acac)2와 Fe(acac)2 혼합비에 따른 Pt-Fe 로딩량은 5.95-6.78 wt% 정도였고, Pt 함량이 감소함에 따라 전체 로딩량은 약간씩 증가하였다. Pt(acac)2와 Fe(acac)2 혼합비에 비례하여 Pt와 Fe의 생성비가 비례함을 확인하였다. 구형의 Pt 및 Fe 금속 나노 입자들이 카본블랙 표면 영역에 분산되어 있으며, 입자 평균 크기는 3.84 nm였다. 이 Pt 및 Fe 금속 나노 입자가 카본블랙의 50 nm 이하의 지름 크기를 갖는 기공들을 막음으로서 카본블랙의 비표면적이 감소하였고, 특히 Fe 나노 입자 로딩량이 증가함에 따라 비표면적은 더 감소하였다. I-V 특성을 개선하기 위해 Pt-Fe 촉매 크기를 더 작게 하여 촉매 표면적을 넓히고, 카본블랙 비표면적을 넓힐 필요가 있으며, Pt 함량이 높을수록 I-V 특성이 더 우수하였다.
Acknowledgments
본 연구는 2021년도 산업통상자원부의 신재생에너지 핵심기술 개발 사업의 연구비 지원을 받아 수행된 연구이다(No. 20213030040520).
References
-
M. K. Cho, A. Lim, S. Y. Lee, H. J. Kim, S. J. Yoo, Y. E. Sung, H. S. Park, and J. H. Jang, “A review on membranes and catalysts for anion exchange membrane water electrolysis single cells”, J. Electrochem. Sci. Technol, Vol. 8, No. 3, 2017, pp. 183-196.
[https://doi.org/10.33961/JECST.2017.8.3.183]
-
D. Gamage, M. Thompson, M. Sutherland, N. Hirotsu, A. Makino, and S. Seneweera, “New insights into the cellular mechanisms of plant growth at elevated atmospheric carbon dioxide concentrations”, Plant Cell Environ., Vol. 41, No. 6, 2018, pp. 1233-1246.
[https://doi.org/10.1111/pce.13206]
-
L. Lu, G. Dai, J. Y. Lee, and H. K. Lee, “Effect of the mixture ratio of Ni-Pt nanocatalysts on water electrolysis characteristics in AEM system”, Trans. of the Korean Hydrogen and New Energy Society, Vol. 32, No. 5, 2021, pp. 285-292.
[https://doi.org/10.7316/KHNES.2021.32.5.285]
-
S. S. Kumar and V. Himabindu, “Hydrogen production by PEM water electrolysis - a review”, Materials Science for Energy Technologies, Vol. 2, No. 3, 2019, pp. 442-454.
[https://doi.org/10.1016/j.mset.2019.03.002]
-
G. Dai, L. Lu, J. Y. Lee, and H. K. Lee, “Preparation and characterization of Fe/Ni nanocatalyst in a nucleophilic solvent for anion exchange membrane in alkaline electrolysis”, Trans. of the Korean Hydrogen and New Energy Society, Vol. 32, No. 5, 2021, pp. 293-298.
[https://doi.org/10.7316/KHNES.2021.32.5.293]
-
B. Lee, H. Lee, J. Heo, C. Moon, S. Moon, and H. Lim, “Stochastic techno-economic analysis of H2 production from power-to-gas using a high-pressure PEM water electrolyzer for a small-scale H2 fueling station”, Sustainable Energy & Fuels, Vol. 3, No. 9, 2019, pp. 2521-2529.
[https://doi.org/10.1039/C9SE00275H]
-
J. Chi and H. Yu, “Water electrolysis based on renewable energy for hydrogen production”, Chinese Journal of Catalysis, Vol. 39, No. 3, 2018, pp. 390-394.
[https://doi.org/10.1016/S1872-2067(17)62949-8]
-
I. Vincent, E. C. Lee, and H. M. Kim, “Highly cost-effective platinum-free anion exchange membrane electrolysis for large scale energy storage and hydrogen production”, RSC Adv., Vol. 10, No. 61, 2020, pp. 37429-37438.
[https://doi.org/10.1039/D0RA07190K]
-
B. H. Oh, A. R. Kim, and D. J. Yoo, “Profile of extended chemical stability and mechanical integrity and high hydroxide ion conductivity of poly(ether imide) based membranes for anion exchange membrane fuel cells”, International Journal of Hydrogen Energy, Vol. 44, No. 8, 2019, pp. 4281-4292.
[https://doi.org/10.1016/j.ijhydene.2018.12.177]
-
J. Y. Chu, K. H. Lee, A. R. Kim, and D. J. Yoo, “Study on the chemical stabilities of poly(arylene ether) random copolymers for alkaline fuel cells: effect of main chain structures with different monomer units”, ACS Sustainable Chem. Eng. Vol. 7, No. 24, 2019, pp. 20077-20087.
[https://doi.org/10.1021/acssuschemeng.9b05934]
-
M. J. Jang, M. S. Won, K. H. Lee, and S. M. Choi, “Optimization of operating parameters and components for water electrolysis using anion exchange membrane”, Journal of the Korean Institute of Surface Engineering, Vol. 49, No. 2, 2016, pp. 159-165.
[https://doi.org/10.5695/JKISE.2016.49.2.159]
-
W. Li, H. Tian, L. Ma, Y. Wang, X. Liu, and X. Gao, “Low-temperature water electrolysis: fundamentals, progress, and new strategies”, Mater. Adv., Vol. 3, No. 14, 2022, pp. 5598-5644.
[https://doi.org/10.1039/D2MA00185C]
-
V. Elayappan, R. Shanmugam, S. Chinnusamy, D. J. Yoo, G. Mayakrishnan, K. Kim, H. S. Noh, M. K. Kim, and H. Lee, “Three-dimensional bimetal TMO supported carbon based electrocatalyst developed via dry synthesis for hydrogen and oxygen evolution”, Applied Surface Science, Vol. 505, 2020, pp. 144642.
[https://doi.org/10.1016/j.apsusc.2019.144642]
-
C. Sathiskumar, S. Ramakrishnan, M. Vinothkannan, A. R. Kim, S. Karthikeyan, and D. J. Yoo, “Nitrogen-doped porous carbon derived from biomass used as trifunctional electrocatalyst toward oxygen reduction, oxygen evolution and hydrogen evolution reactions”, Nanomaterials, Vol. 10, No. 1, 2020, pp. 76.
[https://doi.org/10.3390/nano10010076]
-
F. Qin, Y. Ma, L. Miao, Z. Wang, and L. Gan, “Influence of metal–ligand coordination on the elemental growth and alloying composition of Pt–Ni octahedral nanoparticles for oxygen reduction electrocatalysis”, ACS Omega, Vol. 4, No. 5, 2019, pp. 8305-8311.
[https://doi.org/10.1021/acsomega.8b03366]
-
J. Y. Lee, D. Yin, and S. Horiuchi, “Site and morphology controlled ZnO deposition on Pd catalyst prepared from Pd/PMMA thin film using UV lithography”, Chem. Mater., Vol. 17, No. 22, 2005, pp. 5498–5503.
[https://doi.org/10.1021/cm0506555]
-
J. Y. Lee, Y. Liao, R. Nagahata, and S. Horiuchi, “Effect of metal nanoparticles on thermal stabilization of polymer/metal nanocomposites prepared by a one-step dry process”, Polymer, Vol. 47, No. 23, 2006, pp. 7970-7979.
[https://doi.org/10.1016/j.polymer.2006.09.034]
-
G. Dai, L. Lu, J. Y. Lee, and H. K. Lee, “Preparation and characterization of Fe/Ni nanocatalyst in a nucleophilic solvent for anion exchange membrane in alkaline electrolysis”, Trans. of the Korean Hydrogen and New Energy Society, Vol. 32, No. 5, 2021, pp. 293-298.
[https://doi.org/10.7316/KHNES.2021.32.5.293]
-
P. Zhang, J. Y. Lee, H. K. Lee, “Preparation and characterization of Pt-Ni nanocatalyst for anion exchange membrane in alkaline electrolysis by spontaneous reduction reaction”, Trans. of the Korean Hydrogen and New Energy Society, Vol. 33, No. 3, 2022, pp. 202-208.
[https://doi.org/10.7316/KHNES.2022.33.3.202]