
0.5 TPD 급 수소액화 파일럿 플랜트의 콜드박스 열해석
2020 The Korean Hydrogen and New Energy Society. All rights reserved.
Abstract
Thermal analysis was performed for a cold box of a hydrogen liquefaction pilot plant with 0.5 ton/day capacity. The pilot plant has adopted a hydrogen liquefaction process using two-stage helium Brayton cycle with precooling of liquid nitrogen. The cold box for hydrogen liquefaction has generally vacuum insulation but inevitable heat invasion by conduction and radiation exists. The heat loads were calculated for cold box internals according to multilayer insulation emissivity. Total heat load of 181.7 W is estimated for emissivity of 0.03 considered in field condition.
Keywords:
Hydrogen liquefaction, Cold box, Thermal analysis, Vacuum insulation, Multilayer insulation키워드:
수소액화, 콜드박스, 열해석, 진공단열, 다층박막단열재1. 서 론
화석연료의 사용으로 인한 환경오염 및 지구 온난화를 막기 위해 2016년 11월 파리협정이 공식 발효되었다. 이에 따라 2020년부터 전 세계 195개 협정 당사국은 각국이 스스로 정한 기여 의지(intended nationally determined contributions)에 따라서 온실가스 감축을 위해 노력해야 한다1). 수소는 이러한 온실가스 저감을 위해서 또한 지속가능한 저탄소 에너지원으로 많은 관심을 받고 있다2). 수소는 현재 천연가스 개질, 석유화학산업의 부생가스, 석탄, 수전해 등 다양한 방법으로 생산되고 있다. 그중에서 가장 생산 비중이 크고 경제성이 있는 것은 천연가스 개질을 통한 방식이다. 생산된 수소는 고압 기체수소, 액체수소, 메탈 하이드라이드(metal hydrides), 액상 암모니아 등과 같은 방식으로 저장 및 이송이 가능하다. 그러나 고압 기체수소와 액체수소 방식을 제외하고는 상용화까지 추가적인 기술개발이 더 필요한 실정이다. 액체수소는 고압 기체수소 대비 대용량 저장 및 운송이 용이하여 수소의 사용이 늘어날수록 경제성이 높아진다3). 따라서 현재의 고압 기체수소 위주의 저장 및 운송방식은 차츰 액체수소 기반으로 옮겨갈 것으로 전망된다.
액체수소 기반의 저장 및 운송을 위해서는 액화공정을 통해서 기체상태의 수소를 액체로 변환하는 것이 필요하다. 액화공정에는 많은 에너지가 필요하기 때문에 액화공정의 효율성을 높이기 위한 많은 연구들이 수행되어 왔다4-6). 그리고 최근 국내에서 0.5 ton/day (TPD) 규모의 수소액화 파일럿 플랜트를 구축하기 위한 연구로 LNG와 액체질소의 냉열을 활용하는 2단 브레이튼(Brayton) 사이클 기반 수소액화 공정이 제안되었다7).
본 연구에서는 액체질소의 냉열을 활용하고 2단 헬륨 브레이튼 사이클을 적용한 0.5 TPD 급 수소액화 파일럿 플랜트의 콜드박스 열해석을 수행하였다. 콜드박스는 액화의 주요 공정을 구성하는 열교환기, 팽창기, 흡착기 등의 기자재들이 공정에 따라서 내부에 연결/배치되어 있는 커다란 단열 용기이다. 수소액화용 콜드박스는 수소 액화가 20 K의 극저온에서 이루어지기 때문에 외부로부터의 열유입을 최소화하기 위하여 일반적으로 진공단열 구조를 채택하고 있다8,9). 그럼에도 상온으로부터 전도 및 복사에 의한 콜드박스 내부 기자재로의 열유입은 피할 수 없으며 이는 액화공정의 손실로 작용하기 때문에 콜드박스의 열유입량 산정은 매우 중요하다. 본 연구에서는 0.5 TPD 급 수소액화 파일럿 플랜트의 콜드박스에서 주요 기자재를 감싸는 다층박막단열재(multilayer insulation, MLI)의 방사율(emissivity)에 따른 복사 열유입량의 변화를 살펴보았다. 또한 전도 열유입량 산정을 통하여 콜드박스 내 주요기자재로의 열유입량을 예측하였다.
2. 콜드박스 구성 및 열해석 조건
2.1 콜드박스 구성
Fig. 1은 액체질소의 냉열을 활용하는 2단 헬륨 브레이튼 사이클을 적용한 0.5 TPD 급 수소액화 파일럿 플랜트의 공정을 간략하게 나타낸다. 수소는 액체질소에 의해서 예냉된 뒤 헬륨을 작동유체로 사용하고 2대의 팽창기를 적용한 브레이튼 냉각 사이클을 통해서 순차적으로 냉각되고 액화된다. 이때 열교환기 내에 설치된 촉매를 통해서 수소의 Ortho-Para 변환이 이루어지고 변환열이 열교환기를 통해서 흡수된다. Fig. 1의 점선은 콜드박스 경계를 나타낸다. 콜드박스 내의 주요 기자재는 4개의 열교환기(HX-100~HX-103), 2개의 헬륨 팽창기(T-201, T-202), 헬륨 흡착기(helium adsorber)로 구성된다. Fig. 2는 이러한 콜드박스의 3차원 도면을 나타낸다. 콜드박스는 수직형 구조(vertical type)를 가지며 크기는 지름 2,700 mm, 높이 2,700 mm이다.
2.2 열해석 조건
콜드박스는 진공단열이 되기 때문에 전도 및 복사에 의한 열유입만이 존재한다고 볼 수 있다. 전도 및 복사에 의한 열유입 계산에서 온도 경계조건으로 Fig. 1의 주요 기자재 입/출구 온도를 사용하였다. Table 1은 열해석에 사용된 경계조건을 나타낸다. 콜드박스에서 전도를 통한 열유입 통로는 크게 주요 기자재의 지지부와 콜드박스 상판에 설치되어 배관까지 연결되는 극저온 밸브를 들 수 있다. 콜드박스 내의 주요 기자재는 Fig. 2에서와 같이 콜드박스 상판에 지지되는데, 이를 지지하는 지지부는 열전도도가 매우 낮은 glass fiber reinforced plastic 재질로 만들어졌기 때문에 상대적인 열유입량은 무시할 만하다. 따라서 본 연구에서 콜드박스에서 전도를 통한 열유입은 극저온 밸브만을 고려하였다. 복사를 통한 열유입의 경우 표면 방사율(emissivity)이 중요한 변수이다. 콜드박스 내부는 복사에 의한 열유입을 줄여주기 위해서 방사율이 낮은 MLI로 감싸게 된다. MLI의 방사율은 깨끗한 실험실 환경에서는 0.001의 낮은 값(22 layer package, polyimide foil/polyester net)을 나타내지만 오염 가능성이 있는 실제 설치 환경에서는 0.03의 높은 값을 나타내는 것으로 알려져 있다10,11). 본 연구에서는 이러한 측면을 고려하여 MLI가 설치되지 않았을 때와 MLI의 방사율이 각각 0.001, 0.03인 경우에 대해서 해석을 수행하였고 그 결과를 비교하였다. 복사 열전달 해석에는 콜드박스 내부가 매질이 없는 고진공이기 때문에 surface-to-surface radiation12)만을 고려하였고 배관들은 열교환기나 흡착기에 비해서 표면적이 상대적으로 매우 작아서 열전달에 미치는 영향이 작기 때문에서 해석에서 제외하였다. 상용 소프트웨어인 COMSOL MultiphysicsTM (COMSOL Inc., Stockholm, Sweden)13)를 복사 열전달 해석에 사용하였다. Table 2는 MLI 외에 해석에 사용된 주요 재질의 방사율14)을 나타낸다.
3. 결과 및 고찰
3.1 전도에 의한 열유입량
콜드박스에 설치되는 극저온 밸브는 밸브 상부가 상온에 노출되고 하부는 극저온 배관과 연결되기 때문에 전도 열유입의 주요한 통로가 된다. 주요 극저온 밸브 제조사들은 밸브의 길이, 크기, 적용 온도에 따라서 밸브를 통해 유입되는 열유입량 데이터를 제공하고 있다15). 따라서 콜드박스에 설치되는 극저온 밸브의 사양과 작동 온도로부터 밸브를 통한 전도 열유입량을 산정할 수 있다. 밸브 제조사의 데이터의 경우 상온(300 K)과 특정 온도(4.2 K, 20 K, 77 K) 사이에 대해서만 열유입량이 주어지기 때문에 현재의 작동 온도에 대해서 보간법을 사용하여 극저온 밸브를 통한 열유입량을 산정하였다. Table 3은 현재의 콜드박스에 설치되는 밸브의 사양과 이로부터 예상되는 열유입량을 나타낸다. 다만 산정 결과를 살펴보면 HX100의 밸브가 온도가 높은데도 불구하고 같은 크기의 다른 밸브들에 비해서 열유입량이 크게 나타내는데 이것은 HX100의 밸브의 스템 길이가 다른 밸브들에 비해서 짧기 때문이다.
3.2 복사에 의한 열유입량
콜드박스의 제작 및 설치 환경을 고려할 때 MLI로 감싼 콜드박스와 내부 기자재들의 표면 방사율은 보수적인 값인 0.03으로 보는 것이 설계 기준점이 될 수 있다. 이런 관점에서 표면 방사율 0.03에 대해서 복사 열유입 해석을 수행하였다. Figs. 3, 4는 콜드박스 내부 주요 기자재들의 온도분포와 복사열유속에 대한 해석 결과를 나타낸다. 해석 결과에서 복사 열유속이 음의 값을 나타내는 것은 열을 방출하는 것을 의미하고 양의 값은 그 반대를 나타낸다. 복사 열유속 분포를 보면 복사 열유입의 근원인 상온의 콜드박스 내벽을 직접 바라보는 쪽에 위치한 기자재 표면에서 높은 복사 열유속 값을 나타내는 것을 알 수 있다. 반면에 직접 바라보지 않는 위치에 있는 표면은 상대적으로 낮은 열유속 값을 나타낸다. 그래서 온도가 상대적으로 높더라도 표면이 바라보는 방향에 따라서 더 높은 열유속 값을 나타낼 수 있다. 또한 상온의 헬륨과 수소가 처음 유입되는 열교환기 HX100 상부에서는 오히려 열유속이 음수를 나타내어 차가운 다른 내부 기자재들에게 열을 빼앗기고 있음을 알 수 있다. 전체적으로 MLI의 방사율이 0.03일 경우 기자재 표면이 받는 복사 열유속은 수 W/m2 정도의 크기를 나타내었다. Fig 5는 콜드박스 내부 각 기자재가 받는 전도와 복사를 포함한 전체 열유입을 나타낸다. 전도와 복사를 합하여 181.7 W가 내부 기자재로 유입되었다. 이러한 열부하는 수소액화 공정 설계 시에 손실로 고려되어야 한다. 다만 계산된 열유입량이 열교환기 전열량의 1% 미만이어서 현재 공정에의 영향은 미미할 것으로 판단된다.
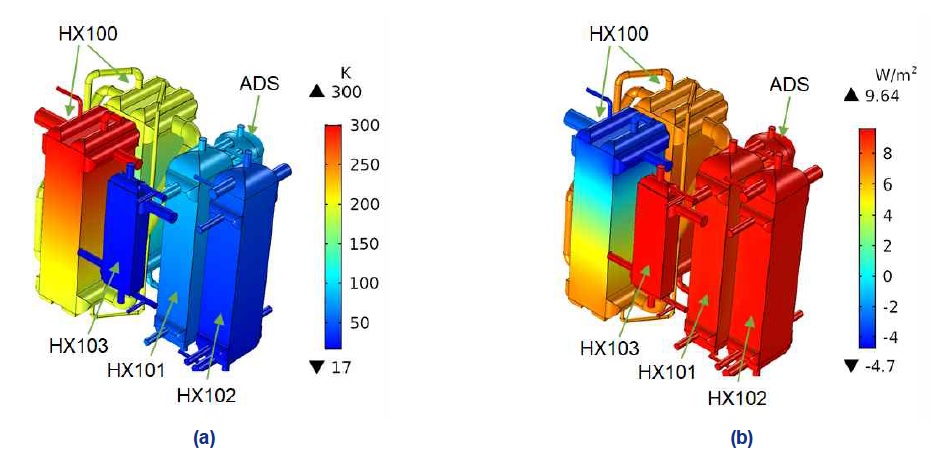
Temperature distribution and radiation heat load in internals of cold box (a) temperature distribution, (b) radiative heat flux
콜드박스 내벽과 내부 기자재에 설치되는 MLI의 방사율에 따른 복사 열유입량의 변화를 살펴보았다. 앞 장에서 언급한 바와 같이 MLI는 설치환경에 따라서 0.001에서 0.03까지 크게 변화할 수 있다. 실제 콜드박스에 설치되는 MLI의 방사율은 이 둘 사이의 값을 나타낼 것으로 예상된다. MLI의 방사율이 각각 0.001, 0.03인 경우와 MLI가 설치되지 않은 경우에 대해서 복사 열유입량을 계산하였다. Fig. 6은 계산 결과를 나타낸다. 방사율이 0.001에서 0.03으로 커질 경우 4.8 W에서 141.9 W로 약 30배가량 복사 열유입량이 커졌다. 반면 MLI가 설치되지 않은 경우는 545.6 W로 방사율이 0.03인 경우보다 약 4배 정도 복사 열유입이 커진다. MLI를 콜드박스에 적용하더라도 설치환경 관리가 매우 중요함을 알 수 있다
4. 결 론
액체질소의 냉열을 활용하고 2단 헬륨 브레이튼 사이클을 적용한 0.5 TPD 급 수소액화 파일럿 플랜트의 콜드박스 열해석을 수행하였다. 수소액화 공정설계 있어서 콜드박스를 통한 추가적인 열유입량을 산정하고 반영하는 것은 매우 중요하다. 본 연구에서는 콜드박스 상판에 설치되는 극저온 밸브를 통한 전도 열유입과 콜드박스 내벽으로부터 내부 기자재로의 복사 열유입을 고려하였다.
1) 콜드박스 설치환경을 고려하여 MLI의 방사율을 0.03으로 보수적으로 잡았을 경우 전도 및 복사에 의해서 콜드박스 내부 기자재로 유입되는 열량은 총 181.7 W로 계산되었고 내부 기자재에 따라서 각각의 열유입량이 산정되었다.
2) 전도 및 복사에 의한 열유입량은 열교환기 전열량의 1% 미만으로 현재 공정에의 영향은 미미할 것으로 판단된다.
3) MLI의 방사율에 따른 콜드박스로의 복사 열유입량 변화를 비교하였고 MLI의 설치환경에 따른 방사율의 변화가 복사 열유입량에 큰 영향을 줌을 알 수 있었다.
Acknowledgments
본 연구는 국토교통부와 국토교통과학기술진흥원의 2020년 상용급 액체수소 플랜트 핵심기술 연구개발사업의 연구비 지원에 의해 수행되었습니다(과제번호: 20IHTP-B151601-02).
References
- S. Kang and W. Jaegal, “US declaration of withdrawal from Paris Agreement and prospect and response to new climate regime”, KEI Focus, Vol. 5, No. 5, 2017. Retrieved from https://www.kei.re.kr/board.es?mid=a10102020000&bid=0028&act=view&list_no=22711, .
- S. K. Huh, “Activating Korea’s hydrogen energy industry”, KIET Industrial Economic Review, No. 3, 2019, pp. 24-36. Retrieved from https://www.kiet.re.kr/kiet_web/?sub_num=14&state=view&idx=55479, .
- B. Choi, K. H. Do, S. In, and T. Kim, “Hydrogen liquefaction plant for realization of a hydrogen society”, Journal of the KSME, Vol. 59, No. 4, 2019, pp. 50-55.
-
M. S. Sadaghiani and M. Mehrpooya, “Introducing and energy analysis of a novel cryogenic hydrogen liquefaction process configuration”, Int. J. Hydrogen Energy, Vol. 42, No. 9, 2017, pp. 6033-6050.
[https://doi.org/10.1016/j.ijhydene.2017.01.136]
-
Y. E. Yukel, M. Ozturk, and I. Dincer, “Analysis and assessment of a novel hydrogen liquefaction process”, Int. J. Hydrogen Energy, Vol. 42, No. 16, 2017, pp. 11429-11438.
[https://doi.org/10.1016/j.ijhydene.2017.03.064]
-
U. Cardella, L. Decker, J. Sundberg, and H. Klein, “Process optimization for large-scale hydrogen liquefaction”, Int. J. Hydrogen Energy, Vol. 42, No. 17, 2017, pp. 12339-12354.
[https://doi.org/10.1016/j.ijhydene.2017.03.167]
-
T. Kim, B. Choi, Y. Han, and K. H. Do, “Thermodynamic analysis of a hydrogen liquefaction process for a hydrogen liquefaction pilot plant with a small capacity”, Trans Korean Hydrogen New Energy Soc, Vol. 31, No. 1, 2020, pp. 41-48.
[https://doi.org/10.7316/KHNES.2020.31.1.41]
- Linde Kryotechnik, “Liquefaction for highest density hydrogen solutions”, 2016, p. 4. Retrieved from https://www.linde-kryotechnik.ch.
- P. Barjhoux, “H2 production and liquefaction overview“, EASISchool2 on Cryogenics, Grenoble, France, Sep. 2019.
- RUAG International Holding AG, “Thermal insulation products”. Retrieved from https://www.ruag.com/en/products-services/space/spacecraft/multi-layer-insulation, .
- T. Miyakita, R. Hatakenaka, and H. Sugita, “Evaluation of thermal insulation performance of a new multi-layer insulation with non-interlayer-contact Spacer”, 45th International Conference on Environmental Systems, Washington, United States, Jul. 2015.
- COMSOL Inc., “COMSOL 5.4 Heat transfer module user’s guide”, 2018, pp. 201-219. Retrieved from https://www.comsol.com, .
- COMSOL Inc., “COMSOL Multiphysics”. Retrieved from https://www.comsol.com, .
- W. Obert, J. R. Copland, D. P. Hammond, T. Cook, and K. Harwood, “Emissivity measurements of metallic surfaces used in cryogenic applications”, Adv. in Cryogenic Engineering, Vol. 27, 1982, pp. 293-300.
- Weka AG, “Weka specification no. 19930219”, Switzerland, private communication.