
Eco-AZ91 MgH2의 반응열 제어에 미치는 촉매 분산 효과
2023 The Korean Hydrogen and New Energy Society. All rights reserved.
Abstract
This study selected Eco-AZ91 MgH2, which shows high enthalpy as a material for this purpose, as the basic material, and analyzed the change in characteristics by synthesizing TiNi as a catalyst to control the thermodynamic behavior of MgH2. In addition, the catalyst dispersion technology using graphene oxide (GO) was studied to improve the high-temperature aggregation phenomenon of Ni catalyst and to secure a source technology that can properly disperse the catalyst. XRD, SEM, and BET analysis were conducted to analyze the metallurgical properties of the material, and TGA and DSC analysis were conducted to analyze the dehydrogenation temperature and calorific value, and the correlation between MgH2, TiNi catalyst, and GO reforming catalyst was analyzed. As a result, the MgH2-5 wt% TiNi at GO composite could lower the dehydrogenation temperature to 478-492 K due to the reduction of the catalyst aggregation phenomenon and the increase in the reaction specific surface area, and an experimental result for the catalyst dispersion technology by GO could be ensured.
Keywords:
Magnesium hydrides, Nitinol, Graphene oxide, Thermal energy, Catalyst dispersion키워드:
마그네슘 수소화물, 니티놀, 산화 그래핀, 열에너지, 촉매 분산1. 서 론
과거에서부터 현재까지 산업화와 기술적 진보 등에 따른 인류의 생활 수준 향상은 소비와 생산을 급격히 증가시키면서 자연에 미치는 압박을 더욱 악화시키고 있다. 이를 경험한 다양한 국가들은 문제를 해결하기 위해 Kyoto Protocols, Paris Agreement, United Nations Framework Convention on Climate Change (UNFCCC) 그리고 COP26 등의 국제 환경 통제 포럼을 개최하여 다양한 환경 문제 해결 방안에 대해 논의해 왔다. 최근 COP26 컨퍼런스에서는 2050년까지 지구온난화 정도를 1.5℃로 낮출 것을 제안하였는데, 이 수치는 Intergovernmental Panel on Climate Change (IPCC) 보고서에 따르면 약 500 GtCO2의 carbon budget에 해당한다. 이를 충족하기 위해 가장 해결해야 하는 문제로 화석연료의 지속적인 사용이 대두되고 있다. 이 때문에 화석연료의 활용을 절감하거나 대체할 수 있는 다양한 물질 탐구에 대한 연구가 필수적으로 요구되며, 여러 연구가 진행되어 왔다1-5).
현재까지는 리튬 이온 배터리나 신재생에너지, 수소 등이 화석연료의 대체제로 고려되고 있다. 그중에서도 수소는 양이 풍부하고 지역에 따른 간헐성 및 불균일성을 보이지 않는 가장 이상적인 물질이다. 또한 독성이 없으며, 다양한 에너지원으로부터 생산되고, 다른 에너지로 변환되기 쉬워 차세대에너지 media로 여겨지고 있다. 수소의 경우 298 K의 조건에서 연소 시 120-141.8 MJ/kg의 에너지를 방출하게 되는데, 이는 44 MJ/kg의 에너지를 제공하는 가솔린의 약 3배에 해당한다. 또한 수소는 연소 시 이산화탄소를 배출하지 않아 지구온난화 개선에 큰 기여를 할 것으로 기대할 수 있다6).
수소는 대기 중에서 기체 상태로 존재하기 때문에 수소를 적절히 활용하기 위해서는 지속적이고 효율이 높은 저장 방법이 요구된다. 현재 많이 주목받고 있는 고압 압축 방식(350 혹은 700 bar)이나 영하 253℃ 이하로 수소를 액화시키는 냉각 방법은 안전성 및 효율성의 문제로 많은 제한 요소가 있다. 이에 비해 물질과의 화학적으로 결합하는 물질 기반 저장 방식은 상온 및 상압 조건에서 수소를 저장할 수 있어 안정성과 에너지 효율의 문제를 해결할 수 있다. 특히 금속을 기반으로 하는 금속수소화물 저장 방식은 체적당 높은 수소 저장량을 지니고 있고, Van der Waals 반경보다 작은 간격으로 형성되어 안정적이다. Fig. 1은 전반적인 물질 기반 저장 방식들을 보여주고 있다7-9).
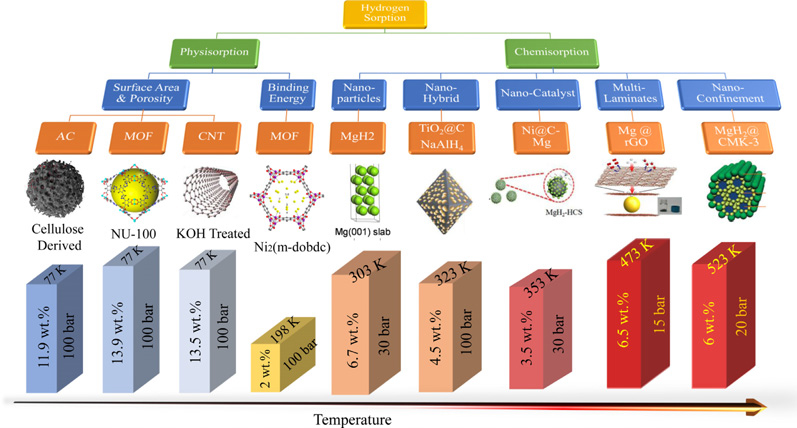
Comparison of hydrogen storage capacity of the various materials with increasing temperature. The materials presented above are (i) AC, (ii) MOF, (iii) CNT, (iv) MOF, (v) MgH2, (vi) TiO2@C, (vii) NaAlH4, (viii) Ni@C-Mg, (ix) Mg@rGO, and (x) MgH2@CMK-3.9
그러나 반응 시 발생하는 반응열로 인해 열안정성 저하 등의 문제가 제기되면서 이를 해소하기 위한 방안들을 탐색하기 시작하였다. 식 (1)은 금속과 수소의 반응에 대한 관계식을 나타내고 있으며, 반응 과정에서 일정량의 열이 발생한다는 것을 보여준다. 형성된 열에너지를 적절히 제어하기 위해 촉매 합성 등의 다양한 연구가 진행되어 왔으며, 일부 연구진들은 열에너지가 폐열로 버려지는 것을 고려해 에너지 하베스팅 관점에서 활용하고자 하는 연구도 진행하였다10).
(1) |
Fig. 2는 태양열 발전을 위한 금속수소화물 기반의 열저장 시스템에 대한 모식도를 나타내고 있다. 발전 시스템은 저장 시간과 발전소의 위치에 따라 달라지는 작업 조건과 전력 수준에 따라 하루 종일 작동된다. 이 thermal energy storage (TES) 시스템은 서로 다른 온도에서 반응하여 다른 엔탈피를 갖는 두 개의 금속수소화물로 구성되어 있다. 충분한 태양열을 공급받는 주간에는 태양열에 의해 직접 구동되고, 잉여 열에너지는 TES 시스템의 high temperature metal hydrides (HTMH)로 들어가면서 저장된다. 이때 HTMH는 반응을 통해 발생한 수소를 low temperature metal hydrides (LTHM)로 공급해 많은 열을 저장하고, LTHM은 수소를 흡수해 저온의 열을 방출한다. 야간에는 LTMH에 저온의 열을 가해 수소를 방출하고, 수소는 HTMH로 이동 후 반응하여 고온의 열을 태양열 시스템에 공급한다. 금속수소화물 기반의 TES 시스템은 별도의 압축기 없이 활용할 수 있어 관리 비용이 적고, 용융염 기반의 TES의 약 15-20배, 상변화 물질 기반 TES의 약 5-10배 수준의 에너지 밀도로 에너지를 저장할 수 있다11).
이러한 관점에서 가장 주목받는 물질 중 하나는 마그네슘 계열이다. 마그네슘의 풍부한 매장량과 저비용으로 높은 가격 경쟁력을 확보할 수 있으며, 합성 시 높은 열에너지를 방출하여 고온 수소화물에 적합한 물질로 고려된다. 예를 들어 MgH2는 약 78 kJ/mol/H2, Mg2Ni 는 65 kJ/mol/H2 정도의 엔탈피를 생성한다. 그러나 산소와의 높은 친화력 때문에 열화 현상 및 초기 활성화를 초래하여 수소 저장량이 감소하는 경향이 있어 장기적인 활용에 다소 한계가 있다. 따라서 이러한 문제점들을 개선하기 위한 연구가 필요한데, 가장 보편적인 방법은 촉매를 활용하는 방법이다12). 현재까지 다양한 전이금속 촉매가 다양하게 연구되어 왔는데, 그중 Ti 기반 촉매는 수소화 반응의 활성화에너지를 낮추고, Ni 계열은 MgH2의 수소화 kinetics를 비롯한 여러 특성을 개선한다는 연구 결과가 여럿 발표되었다. 이러한 관점에서 Ti과 Ni이 화학적으로 결합하고 있는 TiNi 또한 특성 개선에 긍정적인 영향을 줄 수 있다고 판단된다. 실제로 선행 연구에서 rotation-cylinder method (RCM)를 이용해 Mg-TiNi 복합체를 합성 및 분석해 이를 분석했던 연구 결과도 있었다13-18).
단, nickel 기반 촉매를 사용함에 있어서 nickel의 응집 현상을 충분히 고려할 필요가 있다. Nickel을 적용하는 연료전지 연구에서는 nickel이 고온에서 작동 시 응집 현상이 발생한다는 사실이 빈번하게 관찰되고 있다19). 마그네슘 기반 수소 저장 물질의 경우 500℃ 이상에서 수소화/탈수소화 반응이 발생하기 때문에 고온으로 인한 촉매의 응집을 충분히 고려할 필요가 있다. 따라서 촉매의 표면 특성을 적절하게 제어해 응집을 방지할 수 있는 기술도 연구될 필요가 있다.
본 연구에서는 MgH2의 열역학적 에너지를 활용하기 위해 반응 엔탈피를 제어하는 연구를 진행한다. 일정한 열에너지를 확보하기 위해 TiNi 촉매를 특정 비율로 혼합하였으며, 물질의 특성 제어 및 촉매의 응집 현상을 개선하기 위해 촉매를 탄소 나노체인 graphene oxide (GO)의 matrix에 배치시켜 촉매의 응집을 개선하는 방법을 탐색하려고 한다. 결과적으로 해당 연구를 통해 촉매 분산 효과를 유도하고, 반응 비표면적을 증대시켜 촉매 효과를 극대화시킬 수 있는 방법을 찾을 것이다. 궁극적으로 MgH2의 kinetics 및 엔탈피에 대한 TiNi의 특성 제어 여부를 확인하고, 탄소 나노체에 의한 촉매 응집을 제어하는 원천기술을 확보하고자 한다.
2. 실 험
2.1 Eco-AZ91 MgH2 합성
MgH2 합성 과정에서 수분이 포함될 경우 합성 중 수산화물 등의 부산물이 생성될 수 있다. 이를 억제하기 위해 합성 시 수소를 가압한 기계적 합금화 방법(hydrogen-induced mechanical alloying, HIMA)을 활용하였다. 먼저 Eco-AZ91 Mg alloy ingots를 드릴로 가공하여 칩 형태로 채취하였다. Eco-AZ91 Mg alloy를 선정한 이유는 표면의 MgO와 내부에 포함된 CaO의 복합막에 의해 산화를 방지할 수 있어 더 이상적인 저장체 합성이 가능할 것으로 판단하였기 때문이다20). 선행 연구를 고려해 200 mL의 STS 용기에 10 mm balls와 Eco-AZ91 Mg alloy 칩을 넣었으며, balls와 칩의 비율은 66:1의 무게비(ball to chip weight ratio, BCR)로 장입하였다. 합성 중의 마그네슘의 산화 발생 여부를 고려하여 로터리 펌프로 5×10-1 Torr 수준의 진공 상태로 용기 내 분위기를 조성하였다. 이후 수소를 가압해 수소 분위기로 전환시켰으며, 이때의 수소압은 3.0 MPa으로 진행하였다. 합금화 과정은 유성형 ball-mill 장비(planetary ball mill, PULVERISETTE-5; FRITSCH, Idar-Oberstein, Germany)를 96시간 동안 200 rpm의 속도로 회전시켜 진행하였으며, 제조된 Eco-AZ91 MgH2은 X선 회절 분석기(X-ray diffractometer, XRD), 주사전자현미경(scanning electron microscopy, SEM), 비표면적 측정 장치(Brunauer-Emmett-Teller surface analysis, BET) 등을 통해 야금학적 특성을 분석하였다.
2.2 GO 개질형 TiNi 제조
Eco-AZ91 MgH2의 수소화 반응 시의 열역학적 변화를 분석하기 위해 GO 개질형 TiNi 합성을 진행했다. TiNi (granular; Avention, Siheung, Korea)가 GO (powder; Sigma-Aldrich, St. Louis, MO, USA)에 의해 분산되도록 TiNi와 GO를 STS 용기에 장입하였다. TiNi와 GO의 상대적인 비율은 비표면적 크기가 큰 GO의 비율이 필요 이상으로 포함될 경우 열역학적 변화가 GO의 조성에 따른 변화로 나타날 수 있어 TiNi:GO 비를 200:1 (mass ratio)로 진행하였다17). 그리고 10 mL balls를 물질 대비 40:1 (mass ratio)로 넣어 준비하였다. Ball-mill 장비를 200 rpm, 24시간의 조건으로 작동시켜 GO에 의한 TiNi 개질을 진행하였다. 분쇄로 인한 촉매 크기의 미세화에 따라 특성 변화가 나타날 수 있기 때문에 입자 크기에 대한 변수를 최소화할 필요가 있다. 따라서 이를 보정하기 위해 MgH2-TiNi 복합체 합성에 필요한 TiNi에 대해서도 200 rpm의 속도로 24시간 동안 같은 과정을 진행하였다.
2.3 TiNi 및 TiNi@GO 촉매 복합체 제조
TiNi와 GO 개질형 TiNi (TiNi@GO)를 Eco-AZ91 MgH2의 반응 제어를 위한 촉매로 합성시키기 위해 ball-mill을 이용한 기계적 합금화 방식으로 합성을 진행하였다. Eco-AZ91 칩을 넣은 후 질량 기준 5 wt% 또는 10 wt%의 TiNi 혹은 TiNi@GO를 STS 용기에 장입하였다. Balls는 물질의 질량 기준으로 66:1의 비율로 STS 용기에 장입하였다. 이후 로터리 펌프로 5×10-1 Torr의 진공 분위기를 조성하고, 3 MPa의 압력으로 수소를 가압해 수소 분위기를 형성하였다. 마지막으로 24시간 동안 200 rpm의 조건으로 합성을 진행하였다.
2.4 야금학적 특성과 수소화 kinetics 분석
Eco-AZ91 Mg 합금의 열역학적 거동 및 부산물의 형성 등을 분석하기 위해 야금학적 특성과 thermal gravimetric analysis (TGA) 분석을 진행하였다. 합성 결과 분석 및 부산물 형성 여부는 제조된 물질을 XRD (D8 Advance; Bruker, Billerica, MA, USA)로 분석하여 진행하였다. Target은 1.5405 Å의 CuKα로 하였으며, 주사 범위 20-80°, 주사 속도 5 deg/min로 선정하였다. 입자 미세화에 의한 입자 크기 및 군집체 변화 관측은 전계 방사형 SEM (Quanta-400; FEI Company, Hillsboro, OR, USA)을 통해 표면 형상을 관찰하여 진행되었다. 촉매 개질이 원활히 이루어질 경우 표면적의 증가가 나타날 것으로 판단되어 BET (Micromeritics-3-Flex; Micromeritics, Norcross, GA, USA)로 비표면적의 변화를 확인하였고, 최종적으로는 촉매와 촉매 개질에 의한 열역학적 변화를 분석할 수 있도록 TGA와 differential scanning calorimetry (DSC) 분석을 진행하였다. 온도의 증가에 따라 수소가 탈착되면서 질량이 감소하는 것으로 탈수소화 개시온도와 상변화 여부를 분석하기 있어 열역학적 변화를 분석하기에 적합하다고 판단하였다. 합성한 물질을 TGA 분석기(STA490PC, RT-1673K; NETZSCH, Selb, Germany)에 장입한 후, 산소와의 반응을 억제하기 위해 Ar을 50 mL/min씩 일정하게 흘려주며 승온 속도를 분당 1, 5, 10 K 조건으로 다르게 설정하여 진행했다.
3. 결과 및 고찰
3.1 수소 저장 복합체의 야금학적 특성
Eco-AZ91 MgH2와 촉매를 합성한 물질들에 대한 XRD 결과를 Fig. 3과 같이 나타내었다. MgH2의 경우 2θ peaks가 27°, 36° 부근에서 강하게 나타난 것을 알 수 있으며, 이는 이론값과 유사한 수치였다21). 결정 구조를 분석한 결과 정방정 구조(tetragonal)를 갖는 것을 확인하였다. 5 wt% 또는 10 wt% TiNi를 합성한 복합체에서도 MgH2의 peaks의 위치가 유사하였으며, TiNi의 2θ peaks가 45°와 64°에서 검출된 것을 확인할 수 있었다. TiNi의 결정 구조는 입방 구조(cubic)로 확인되었으며, 다른 부산물은 검출되지 않은 것을 보아 HIMA 공정에 의한 합성법이 수소 저장체 합성에 적합하다고 판단할 수 있었다. 다만 TiNi@GO를 합성한 복합체에서 Mg2NiH4와 TiO의 다른 부산물 peaks가 확인되었는데, 이는 합성 중 TiNi가 Ti와 Ni로 분해된 것과 합성된 GO의 산소 작용기 간의 반응이 원인으로 판단된다. 부분적으로 보이는 Zn와 Al의 경우 기본 물질인 AZ91 Mg alloy의 구성 성분으로 보이며, 선행 연구를 고려할 때 Al과 Mg의 합성으로 인해 Mg17Al12이 형성된 것으로 보인다. Mg17Al12의 경우 623℃ 이상의 온도에서 수소화 반응이 일어나는 것을 고려할 때 623℃ 이상의 고온 조건에서 열역학적 반응에 기여할 것으로 판단되며, 부산물로 형성된 Mg2NiH4가 MgH2에 비해 상대적으로 낮은 반응열을 발생시키기 때문에 열역학적 변화를 유도할 수 있을 것으로 생각된다14).
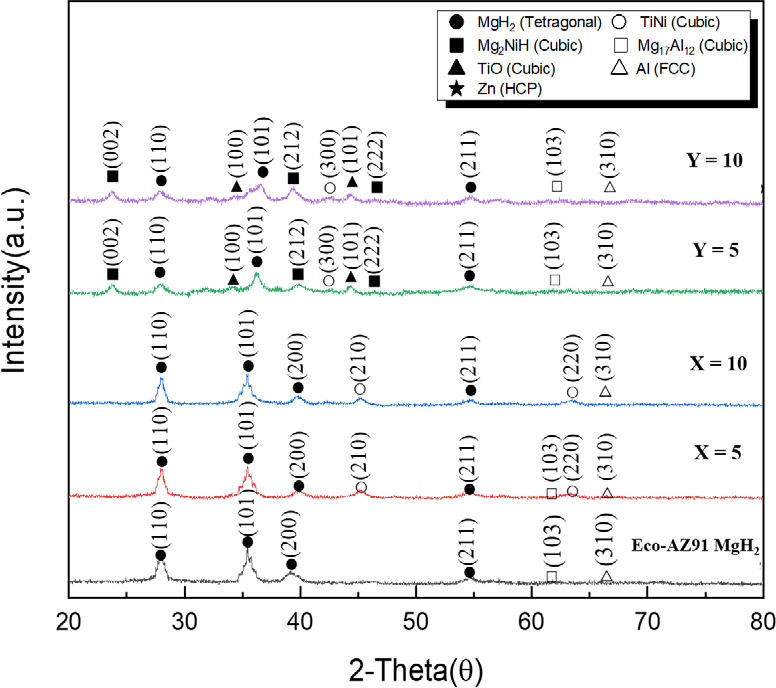
XRD patterns for Eco-AZ91 MgH2, Eco-AZ91 MgH2-X wt% TiNi (X=5, 10) and TiNi@GO (Y=5, 10) composites (●: MgH2, ○: TiNi, ■: Mg2NiH4, □: Mg17Al12, ▲: TiO, △: Al, ★: Zn)
물질들에 대한 SEM 분석의 표면 형상 이미지는 Fig. 4를 통해 알 수 있다. Eco-AZ91 MgH2의 평균 입자 크기는 약 1-2 μm 정도로, 전반적으로 유사한 크기의 입자가 고루 분포하고 있다. 이미지 내에서 부분적으로 입자가 뭉쳐진 군집체가 관측되는데, 이러한 군집체의 형성은 TiNi를 합성한 경우에 더 두드러지게 나타났다. 이에 대해서는 Ni이 고온에서 응집하는 현상과 기계적 합금화에 통해 미세화된 입자 간의 인력의 증가가 주원인으로 보인다. 이와 다르게 TiNi@GO를 합성한 경우에서는 1-4 μm 정도의 입자들이 분포하였으며, 전반적으로 MgH2-TiNi보다 작은 군집체들이 여럿 나타났다. 이러한 결과는 본 연구에서 확인하고자 했던 탄소나노체에 의한 분산 효과로 Ni의 응집 현상을 완화시킨 결과인 것으로 확인되며, 결과적으로 탄소나노체에 의한 촉매 분산 효과를 증명하였다. 입자의 미세화는 입자의 반응 표면적으로 증진시킬 수 있기 때문에 열역학적으로 낮은 열에너지 혹은 빠른 반응 속도를 유도할 수 있을 것으로 보인다.
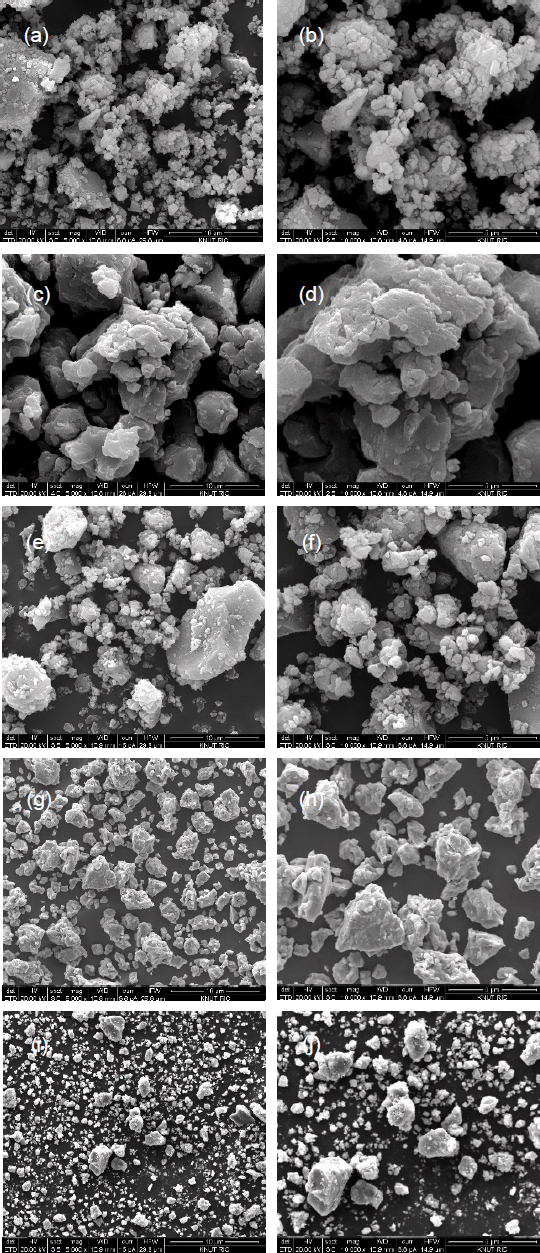
Eco-AZ91 MgH2 SEM morphologies. (a) ×2,500, (b) ×5,000. Eco-AZ91 MgH2-5 wt% TiNi SEM morphologies. (c) ×2,500, (d) ×5,000. Eco-AZ91 MgH2-10 wt% TiNi SEM morphologies. (e) ×2,500, (f) ×5000. Eco-AZ91 MgH2-5 wt% TiNi@GO SEM morphologies. (g) ×2,500, (h) ×5,000. Eco-AZ91 MgH2-10 wt% TiNi@GO SEM morphologies. (i) ×2,500, (j) ×5,000
촉매 분산 효과를 더 상세히 분석하기 위하여 Eco-AZ91 MgH2 기반 물질들에 대해서 비표면적 크기를 비교 분석하였다. 이에 대해서는 Fig. 5와 Table 1에 일괄적으로 나타냈다. 기본 물질인 Eco-AZ91 MgH2의 크기는 약 4.7583 m2/g로 HIMA 공정에 의해 형성된 경우와 유사하였다16). Eco-AZ91 MgH2에 TiNi를 합성한 복합체의 비표면적은 조금 감소한 것을 확인하였다. 이는 SEM 이미지 상에서 확인되는 응집 현상과 군집체 형성이 비표면적 감소의 원인으로 작용하였기 때문인 것으로 보고 있다. 이와 달리 TiNi@GO 촉매를 합성한 복합체의 경우 비표면적이 상당히 증가하는 것을 볼 수 있는데, TiNi@GO 함량이 높아질수록 비례하여 증가하였다.
이러한 결과에 대해서 예상했던 대로 촉매 분산 효과로 입자가 미세화된 것이 주요 원인으로 판단된다. 결과적으로 SEM 분석과 BET 결과값을 상호 고려하였을 때 탄소나노체에 의한 분산 효과를 기계적 합금화로 유도할 수 있으며, 이를 통해 촉매의 효율을 극대화할 수 있다.
3.2 Eco-AZ91 MgH2 기반 수소 저장체의 열역학적 특성 변화
Fig. 6은 탈수소화 반응 개시 온도와 발생하는 열 엔탈피의 변화를 분석하기 위하여 진행한 TGA 및 DSC 분석 결과이다. 자세한 측정값은 세부적인 비교를 위해 Table 2에 따로 정리하였다. 합성된 Eco-AZ91 MgH2의 탈수소화 개시 온도는 승온 속도가 분당 1, 5, 10 K일 때 각각 552, 557, 555 K로 측정되었다. 일반적인 Eco-AZ91 MgH2와 달리 2개의 peaks가 존재하는 것을 확인할 수 있었는데, 이는 ball milling 과정에서 형성된 입자의 크기가 불균일하여 다중의 peaks가 발생한 것으로 보인다. 5 wt%와 10 wt%의 TiNi를 합성한 복합체의 경우 상대적으로 더 낮은 온도에서 수소 탈착 반응이 시작되었으며, GO 개질형 촉매인 TiNi@GO를 합성한 경우 더욱 감소하여 Eco-AZ91 MgH2 대비 50-60 K 정도의 낮은 온도에서 탈수소화 반응이 일어날 수 있도록 조정할 수 있었다. 전반적으로 600 K 이상에서 질량이 급격히 증가하는 것을 확인하였는데, 이는 합성된 물질들이 급격히 산화되면서 중량이 증가하였기 때문으로 판단되며22), 이를 고려하였을 때 Eco-AZ91 MgH2에 대한 추후 실험에서는 50 g/min 보다 높은 속도로 Ar을 주입할 필요가 있다고 본다. Eco-AZ91 MgH2 및 복합 물질들에 대한 DSC 분석은 탈수소화 거동이 흡열 반응임을 알려주고 있다. 전체적인 heat flow 변화를 비교한 결과 TiNi와 TiNi@GO 촉매로 인해 흡열량이 증가한 것을 알 수 있었다. 특히 GO에 의해 특성이 조정된 TiNi@GO를 5 wt%를 합성한 복합체에서 가장 높은 heat flow를 확인할 수 있었다. 따라서 TES 시스템에 활용한다고 할 때 적당한 온도 조건에서 상당량의 열에너지를 공급할 수 있어 가장 이상적인 조건이라고 판단할 수 있다.
4. 결 론
수소 저장 물질을 TES 시스템 등의 분야에서 적용하기 위해 열역학적 특성을 제어하기 위한 연구를 진행하였다. 산화 방지를 위해 Eco-AZ91 Mg alloy를 적용하였고, 열역학적 변화를 주기 위해 TiNi 촉매와 GO에 의한 촉매 분산을 진행하였다. 이후 합성한 물질들에 대해 야금학적 분석과 열역학적 특성을 분석하였으며, 그 결과는 다음과 같다.
1) 합성한 물질들에 대한 XRD를 비교 분석한 결과, Eco-AZ91 Mg alloy와 TiNi를 합성한 복합체에서는 MgH2와 TiNi의 peaks가 이론적 분석 결과와 유사하게 나타났지만, TiNi@GO 촉매를 합성한 경우 Mg2NiH4와 TiO 등 부산물 peaks가 확인되었다. 이는 TiNi가 Ti와 Ni로 분리되고 GO와의 반응 과정에서 발생하였기 때문인 것으로 생각된다. 또한 AZ91의 구성 성분인 Al과 Mg의 화합물인 Mg12Al17가 확인되는데, Mg12Al17의 수소화 거동이 623℃에서 이루어지는 점을 고려할 때 623℃ 이상의 온도에서 열역학적 반응에 변수로 작용할 것으로 판단된다.
2) SEM 표면 형상 이미지를 통해 평균적인 입자 크기를 측정하였으며, 군집체가 형성된 것을 확인하였다. TiNi를 합성한 경우 군집체 수가 더 두드러지게 증가하였으며, 이는 Ni에 의한 촉매 응집 현상과 합금화에 의한 입자 미세화에 의한 것으로 판단된다. TiNi@GO를 합성한 경우 군집체의 크기 및 수가 감소한 것을 확인할 수 있었으며, 이를 통해 GO 개질에 의해 전반적으로 개선된 것을 알 수 있었다. 결과적으로 GO에 의한 촉매 분산 효과가 원활하게 이루어진 것으로 확인된다.
3) SEM 이미지에서의 변화에 맞춰 비표면적 크기에서도 상당한 변화가 확인되었다. Eco-AZ91 MgH2의 비표면적 크기가 4.7583 m2/g으로 측정되었으나, TiNi@GO 합성으로 최대 11.1096 m2/g까지 증가한 것을 알 수 있었다. 이와 같은 결과를 통해 촉매 분산 현상이 확실히 발생했다는 사실을 명확히 확인할 수 있었다.
4) TGA 측정 결과는 TiNi와 TiNi@GO 촉매가 Eco-AZ91 MgH2의 탈수소화 개시 온도를 낮출 수 있었다. DSC 분석 결과를 통해 촉매의 합성으로 발열량을 증대시킬 수 있다는 사실도 확인하였다. 결과적으로 Eco-AZ91 MgH2-5 wt% TiNi@GO 복합체가 상대적으로 낮은 탈수소화 온도를 가지며, 높은 heat flow 값을 갖기 때문에 가장 이상적인 조성으로 결론을 내렸다.
Acknowledgments
본 연구는 교육부에서 지원하는 한국기초과학지원연구원보조금(2019R1A6C1010047)의 연구 지원 및 2023년 한국교통대학교 산학협력단의 지원을 받아 수행하였으며 이에 감사드립니다.
References
-
C. Böhringer, “The Kyoto Protocol: a review and perspectives”, Oxford Review of Economic Policy, Vol. 19, No. 3, 2003, pp. 451-466.
[https://doi.org/10.1093/oxrep/19.3.451]
-
S. N. Seo, “Beyond the Paris Agreement: climate change policy negotiations and future directions”, Regional Science Policy & Practice, Vol. 9, No. 2, 2017, pp. 121-140.
[https://doi.org/10.1111/rsp3.12090]
-
E. L. Tompkins and H. Amundsen, “Perceptions of the effectiveness of the United Nations Framework Convention on Climate Change in advancing national action on climate change”, Environmental Science & Policy, Vol. 11, No. 1, 2008, pp. 1-13.
[https://doi.org/10.1016/j.envsci.2007.06.004]
-
N. K. Arora and I. Mishra, “COP26: more challenges than achievements”, Environmental Sustainability, Vol. 4, 2021, pp. 585-588.
[https://doi.org/10.1007/s42398-021-00212-7]
-
D. B. Müller, G. Liu, A. N. Løvik, R. Modaresi, S. Pauliuk, F. S. Steinhoff, and H. Brattebø, “Carbon emissions of infrastructure development”, Environmental Science & Technology, Vol. 47, No. 20, 2013, pp. 11739-11746.
[https://doi.org/10.1021/es402618m]
-
C. Park, X. Tang, K. J. Kim, J. Gottschlich, and Q. Leland, “Metal hydride heat storage technology for directed energy weapon systems”, In: ASME 2007 International Mechanical Engineering Congress and Exposition; 2007 Nov 11-15; Seattle, WA. Vol. 8, c2007. pp. 961-969.
[https://doi.org/10.1115/IMECE2007-42831]
-
E. Rivard, M. Trudeau, and K. Zaghib, “Hydrogen storage for mobility: a review”, Materials, Vol. 12, No. 12, 2019, pp. 1973.
[https://doi.org/10.3390/ma12121973]
-
R. Janot, A. Rougier, L. Aymard, C. Lenain, R. Herrera-Urbina, G. A. Nazri, and J. M. Tarascon, “Enhancement of hydrogen storage in MgNi by Pd-coating”, Journal of Alloys and Compounds, Vol. 356-357, 2003, pp. 438-441.
[https://doi.org/10.1016/S0925-8388(03)00115-4]
-
A. Gupta, G. V. Baron, P. Perreault, S. Lenaerts, R. G. Ciocarlan, P. Cool, P. G. M. Mileo, S. Rogge, V. Van Speybroeck, G. Watson, P. Van Der Voort, M. Houlleberghs, E. Breynaert, J. Martens, and J. F. M. Denayer, “Hydrogen clathrates: next generation hydrogen storage materials”, Energy Storage Materials, Vol. 41, 2021, pp. 69-107.
[https://doi.org/10.1016/j.ensm.2021.05.044]
-
Q. Luo, J. Li, B. Li, B. Liu, H. Shao, and Q. Li, “Kinetics in Mg-based hydrogen storage materials: enhancement and mechanism”, Journal of Magnesium and Alloys, Vol. 7, No. 1, 2019, pp. 58-71.
[https://doi.org/10.1016/j.jma.2018.12.001]
-
P. A. Ward, C. Corgnale, J. A. Teprovich Jr, T. Motyka, B. Hardy, B. Peters, and R. Zidan, “High performance metal hydride based thermal energy storage systems for concentrating solar power applications”, Journal of Alloys and Compounds, Vol. 645, Suppl. 1, 2015, pp. S374-S378.
[https://doi.org/10.1016/j.jallcom.2014.12.106]
-
J. S. Yu, J. H. Han, H. W. Sin, and T. W. Hong, “Fabrication and evaluation hydrogenation absorbing on Mg2NiHx-10 wt% CaF2 composites”, Journal of Hydrogen and New Energy, Vol. 31, No. 6, 2020, pp. 553-557.
[https://doi.org/10.7316/KHNES.2020.31.6.553]
-
N. A. Elessawy, M. H. Gouda, S. M. Ali, M. Salerno, and M. S. M. Eldin, “Effective elimination of contaminant antibiotics using high-surface-area magnetic-functionalized graphene nanocomposites developed from plastic waste”, Materials, Vol. 13, No. 7, 2020, pp. 1517.
[https://doi.org/10.3390/ma13071517]
-
B. P. Tarasov, S. N. Klyamkin, V. N. Fokin, D. N. Borisov, D. V. Schur, and V. A. Yartys , “Metal hydride accumulators of hydrogen on the basis of alloys of magnesium and rare-earth metals with nickel”, In: T. N. Veziroglu, S. Zaginaichenko, D. V. Schur, B. Baranowski, A. P. Shpak, and V. V. Skorokhod, eds. NATO science series II: mathematics, physics and chemistry. Hydrogen Materials Science and Chemistry of Carbon Nanomaterials; 2003 Sep 14-20; Sudak, Ukraine. Vol. 172. Dordrecht: Springer; 2005. pp. 143-146.
[https://doi.org/10.1007/1-4020-2669-2_13]
-
B. Galey, A. Auroux, S. Sabo-Etienne, S. Dhaher, M. Grellier, and G. Postole, “Improved hydrogen storage properties of Mg/MgH2 thanks to the addition of nickel hydride complex precursors”, International Journal of Hydrogen Energy, Vol. 44, No. 54, 2019, pp. 28848-28862.
[https://doi.org/10.1016/j.ijhydene.2019.09.127]
-
M. Jangir, A. Jain, S. Agarwal, T. Zhang, S. Kumar, S. Selvaraj, T. Ichikawa, and I. P. Jain, “The enhanced de/re-hydrogenation performance of MgH2 with TiH2 additive”, International Journal of Energy Research, Vol. 42, No. 3, 2018, pp. 1139-1147.
[https://doi.org/10.1002/er.3911]
-
G. Liang, J. Huot, S. Boily, A. Van Neste, and R. Schulz, “Catalytic effect of transition metals on hydrogen sorption in nanocrystalline ball milled MgH2–Tm (Tm=Ti, V, Mn, Fe and Ni) systems”, Journal of Alloys and Compounds, Vol. 292, No. 1-2, 1999, pp. 247-252.
[https://doi.org/10.1016/S0925-8388(99)00442-9]
-
T. W. Hong, “Hydrogenation properties of Mg-TiNi hydrogen storage composites materials”, Materials Science Forum, Vol. 486-487, 2005, pp. 586-589.
[https://doi.org/10.4028/www.scientific.net/MSF.486-487.586]
-
J. R. Lee and Y. H. Kim, “Agglomeration of nickel oxide particle during hydrogen reduction at high temperature in a fluidized bed reactor”, Chemical Engineering Research and Design, Vol. 168, 2021, pp. 193-201.
[https://doi.org/10.1016/j.cherd.2021.02.005]
-
S. K. Kim, “Proportional strength-ductility relationship of non-SF6 diecast AZ91D eco-Mg alloys”, Magnesium Technology, 2011, pp. 131-136.
[https://doi.org/10.1007/978-3-319-48223-1_25]
-
K. Chawla, D. K. Yadav, A. Bajpai, S. Kumar, and C. Lal, “Hydrogenation properties and kinetic study of MgH2-x wt% AC nanocomposites prepared by ball milling”, Environmental Science and Pollution Research, Vol. 28, 2021, pp. 3872-3879.
[https://doi.org/10.1007/s11356-020-08964-1]
-
W. Peng, Z. Lan, W. Wei, L. Xu, and J. Guo, “Investigation on preparation and hydrogen storage performance of Mg17Al12 alloy”, International Journal of Hydrogen Energy, Vol. 41, No. 3, 2016, pp. 1759-1765.
[https://doi.org/10.1016/j.ijhydene.2015.11.138]