
알칼리 수전해용 코팅 전극에 관한 연구
2023 The Korean Hydrogen and New Energy Society. All rights reserved.
Abstract
An electrode was prepared by dip-coating NiFe2O4 powder on stainless steel (SUS) support for the application in the alkaline water electrolysis. The prepared electrode was analyzed using scanning electron microscopy (SEM) and energy dispersive X-ray spectroscopy (EDXS), and was evaluated for the voltage properties with the change of current density in oxygen evolution reaction (OER) and hydrgen evolution reaction (HER) using 1, 3 and 7 M KOH solution. From the SEM and EDXS analysis, it was confirmed that the prepared electrode had NiFe2O4 on the SUS support. In OER and HER, the voltage in the 7 M KOH solution had a value of 1.35 and -1.90 V at 0.2 and -0.2 A/cm2 of the current density, respectively. It was considered that the prepared electrode could be use as an electrode in the alkaline water electrolysis from the experimental results.
Keywords:
Hydrogen production, Water electrolysis, Alkaline water electrolysis, Electrode, Coating electrode키워드:
수소 제조, 수전해, 알칼리 수전해, 전극, 코팅 전극1. 서 론
최근 2050년 CO2 배출량을 zero로 하는 탄소중립(net-zero)에 대한 제안이 Intergovernmental Panel on Climate Change (IPCC)에 의해 이루어졌으며1), 국제 에너지 기구(International Energy Agency, IEA)는 2050년 탄소중립 달성을 위해 수소 기술에 대한 연구개발 투자 규모의 확대와 함께 2030년 850 GW의 수전해 제조가 필요할 것으로 예측하고 있다2).
알칼리 수전해(alkaline water electrolysis, AWE)는 전해액으로 알칼리 용액을 사용해서 물을 분해하여 수소를 생산하는 방법의 하나로 오래전부터 잘 알려진 수전해 방법이다3,4). AWE는 일반적으로 전해액으로 15-20%의 NaOH 혹은 20-30%의 KOH 용액을 사용하며, 수산화 이온(OH-)만을 선택적으로 통과시키는 분리막과 니켈 기반의 양극과 스테인리스 스틸 또는 니켈 기반의 음극으로 구성된다. 그리고 음극에서 수소를, 양극에서 산소를 생성하고, 40-80℃에서 작동된다5). Fig. 1은 AWE의 개념을 나타낸다.
AWE의 단점은 전극에서의 낮은 효율, 높은 비용, 높은 전력 소비이다5-7). 따라서 AWE에서 전극 재료는 에너지 효율과 수소 생산 비용에 영향을 준다. 이러한 문제는 알칼리 용액에서 높은 촉매 활성, 높은 표면적 및 높은 내식성을 갖는 저렴하고 적절한 전극 재료를 선택함으로써 해결할 수 있다.
기존에 전극 재료로 사용된 니켈(nickel) 또는 레이니 니켈(Raney nickel)은 수소 발생 반응(hydrogen evolution reaction, HER)에서 높은 초기 전기 촉매 활성을 나타내지만, 금속수소화물의 형성으로 인해 AWE 작동 중에 음극으로서 촉매 활성 저하를 보이며7,8) 양극과 음극에서 갈바닉 부식이 일어난다9). Fe가 코팅된 Ni 전극은 코팅된 Fe가 Ni 전극에서의 금속수소화물의 형성을 방지할 수 있기 때문에 AWE에서 비활성화를 나타내지 않는다고 알려져 있다7,10). 또한 NiFe2O4 전극은 HER과 산소 발생 반응(oxygen evolution reaction, OER)에서 알칼리 환경에 대해 높은 화학적 안정성을 보이며, 높은 열전도율과 우수한 전기적 촉매 활성을 보인다고 알려져 있다5,7,11). 전극의 에너지 효율과 성능을 높이기 위해 HER과 OER에서 높은 전기적 촉매 활성을 갖는 전극 개발에 관한 많은 연구가 진행되고 있다12-18).
본 연구에서는 AWE에서의 적용을 위해 stainless steel (SUS) 지지체에 NiFe2O4 분말을 코팅하여 전극을 제작하였다. 또한 제작한 전극은 1, 3, 7 M의 KOH 수용액에서 전류밀도에 따른 OER과 HER의 전압 특성을 측정하여 전극으로의 사용 가능성을 평가하였다.
2. 실 험
2.1 NiFe2O4 분말의 제조
NiFe2O4 분말은 공침법으로 제조하였다5). Ni(NO3)2·6H2O (97%; Junsei Chemical Co., Ltd., Tokyo, Japan)와 Fe(NO3)3·9H2O (99%; Fujifilm Wako Pure Chemical Corporation, Osaka, Japan)는 실온에서 교반하면서 증류수 100 mL에 용해하였다. 질산니켈과 질산철의 몰비는 1:0.2로 하였다. 60℃에서 혼합물을 계속 교반하면서 1 M의 NaOH 용액을 첨가하여 pH가 9를 유지하도록 하였다. 침전이 형성되기 시작하면서 실온에서 5시간 동안 숙성시킴으로써 침전물을 얻었다. 침전물은 진공에서 여과하고, 잔류물과 불순물을 제거하기 위해 증류수로 세척한 후 100℃에서 24시간 동안 건조하였다. 그리고 건조된 침전물은 분쇄하고 체질함으로써 50 μm 이하의 균일한 NiFe2O4 분말을 얻었다. 얻어진 NiFe2O4 분말은 Ar 가스 분위기로 600℃에서 4시간, 800℃에서 8시간 동안 소결하여 질산 등 잔류 불순물을 제거하였다.
2.2 코팅 페이스트의 제조
코팅 전극을 제작하기 위한 코팅 페이스트(paste)는 다음과 같이 제조하였다.
40 wt.%의 NiFe2O4 분말, 바인더인 4 wt.%의 에틸셀룰로스(ethyl cellulose), 4 wt.%의 폴리에틸렌 글리콜(polyethylene glycol)과 디브틸 프탈레이트(dibuthyl phthalate)가 혼합된 가소제, 분산제인 1 wt.%의 피시 오일(fish oil)을 용매인 51 wt.%의 테르피네올(α-terpineol)에 용해하여 페이스트 용액을 제조하였다. 제조한 용액은 볼 밀에 넣고 300 rpm으로 30분 동안 분산시킴으로써 NiFe2O4 페이스트를 제조하였다.
2.3 코팅 전극의 제작
코팅 전극은 지지체 위에 NiFe2O4 페이스트를 딥-코팅(dip-coating)하여 제작하였다.
지지체로는 1 mm 두께의 SUS-316을 사용하였고, 크기는 2×2 cm로 하였다. 또한 지지체는 표면을 연마하여 사용하였다.
딥-코팅은 제조한 NiFe2O4 페이스트에 지지체를 침적시킨 후 3 mm/min의 속도로 상승시킴으로써 진행하였고, 코팅은 3회 반복하여 진행하였으며, 코팅된 전극은 Ar 가스 분위기로 600℃에서 4시간, 800℃에서 8시간 동안 소결하였다.
제작한 코팅 전극은 scanning electron microscopy (SEM) 분석을 통해 표면과 단면을 관찰하였고, energy dispersive X-ray spectroscopy (EDXS) 분석을 통해 원소 분석을 진행하였다.
2.4 제작한 코팅 전극의 current-voltage 측정
제작한 코팅 전극의 OER과 HER에서 전류밀도에 따른 전압 변화를 측정하는 current-voltage (C-V) 측정을 진행하였다. C-V 측정은 제작한 코팅 전극을 작동전극으로, 백금 메시를 상대 전극으로, 포화 칼로멜 전극을 기준 전극으로 하는 3전극법으로 측정하였다. 전해액으로는 1, 3, 7 M의 KOH를 사용하였으며, 측정은 실온에서 진행하였다. Fig. 2는 C-V 측정 장치를 나타낸다.
200 mL의 두 비커에 KOH 전해액을 담고, 기준 전극을 한쪽 비커에 설치하고, 다른 비커에 작동 전극과 상대 전극을 설치하였다. 그리고 두 비커는 용액 전압 차이를 줄이기 위해 포화 염화칼륨 염다리를 연결하였다. OER에서의 전압은 플러스 전류를, HER에서의 전압은 마이너스 전류를 인가하여 측정하였다.
3. 결과 및 고찰
3.1 제작한 코팅 전극의 모폴로지 분석
Fig. 3은 지지체인 SUS-316 표면, 코팅 전극의 표면과 단면을 나타낸다. Fig. 3의 SEM 사진으로부터 지지체인 SUS-316 과 코팅 전극의 표면을 비교해 보면 SUS-316의 표면은 매끄럽지만, 코팅 전극의 표면은 결정들이 있는 것을 확인할 수 있다. 이는 딥-코팅에 의해 지지체인 SUS-316 위에 NiFe2O4 분말이 코팅된 것을 의미한다. 또한 코팅 전극의 단면 사진으로부터 지지체인 SUS-316 위에 NiFe2O4 분말이 100-140 μm의 두께로 코팅되어 있음을 확인할 수 있었다.
지지체인 SUS-316과 코팅 전극의 EDXS 분석 결과를 Table 1에 나타내었다. EDXS의 분석 결과, 지지체인 SUS-316은 SUS의 원소 분포를 그대로 보여주고 있으며, 코팅 전극은 주로 산소, 철, 니켈의 원소 분포를 보여주고 있다.
Table 1을 보면 알 수 있듯이, 코팅 전극에서의 산소와 니켈 함유량의 증가는 코팅된 NiFe2O4에 의한 것으로 보인다. 또한 코팅 전극에서의 Na의 함유량은 NiFe2O4를 제조할 때 pH 조절을 위해 사용하는 NaOH에 의한 영향으로 판단되며, 증류수를 이용한 세척이 약간 미진했던 것으로 생각된다. 그리고 지지체인 SUS-316과 코팅 전극에서의 철 함유량의 차이는 EDXS 분석이 표면을 분석하는 분석법이기 때문으로, SUS-316의 경우는 SUS 자체의 철 함유량을 분석하였고, 코팅 전극의 경우 코팅된 NiFe2O4의 함유량을 분석하였기 때문으로 판단된다.
SEM과 EDXS의 분석 결과, 코팅 전극은 지지체인 SUS-316에 NiFe2O4가 코팅되어 있는 것을 확인할 수 있었다.
3.2 제작한 코팅 전극의 C-V 측정
Fig. 4는 각 KOH 농도에서 제작한 코팅 전극의 OER과 HER에서 전류밀도와 전압 변화와의 관계를 나타낸다. Fig. 4에서 알 수 있듯이, 각 KOH 농도에서 OER과 HER은 전류밀도가 증가함에 따라 전압이 증가하는 경향을 보였다. 또한 KOH의 농도가 높아짐에 따라 전압은 감소하는 경향을 보였다. 이는 KOH 용액 농도가 높아짐에 따라 전기전도도가 높아지는 것에 기인한 것으로 판단된다.
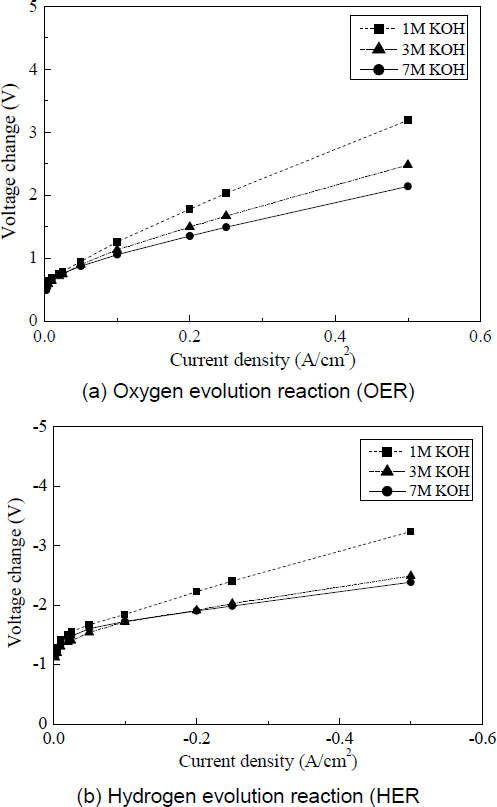
Relationship between current density and voltage change of OER and HER at each KOH concentration in coating electrode
OER의 경우, 1 M의 KOH 용액은 0.1 A/cm2의 전류밀도에서 전압은 1.26 V, 0.2 A/cm2의 전류밀도에서 전압은 1.78 V, 0.5 A/cm2의 전류밀도에서 전압은 3.2 V를 보였다. 3 M의 KOH 용액은 0.1 A/cm2의 전류밀도에서 전압은 1.14 V, 0.2 A/cm2의 전류밀도에서 전압은 1.50 V, 0.5 A/cm2의 전류밀도에서 전압은 2.48 V를 보였다. 7 M의 KOH 용액은 0.1 A/cm2의 전류밀도에서 전압은 1.05 V, 0.2 A/cm2의 전류밀도에서 전압은 1.35 V, 0.5 A/cm2의 전류밀도에서 전압은 2.14 V를 보였다.
HER의 경우, 1 M의 KOH 용액은 -0.1 A/cm2의 전류밀도에서 전압은 -1.85 V, -0.2 A/cm2의 전류밀도에서 전압은 -2.22 V, -0.5 A/cm2의 전류밀도에서 전압은 -3.24 V를 보였다. 3 M의 KOH 용액은 -0.1 A/cm2의 전류밀도에서 전압은 -1.71 V, -0.2 A/cm2의 전류밀도에서 전압은 -1.91 V, -0.5 A/cm2의 전류밀도에서 전압은 -2.49 V를 보였다. 7 M의 KOH 용액은 -0.1 A/cm2의 전류밀도에서 전압은 -1.73 V, -0.2 A/cm2의 전류밀도에서 전압은 -1.90 V, -0.5 A/cm2의 전류밀도에서 전압은 -2.38 V를 보였다.
OER과 HER의 각 KOH 용액에서의 전류밀도에 따른 전압을 비교해 보면, HER이 OER보다 약간 높은 값을 보였다. 이는 전압 측면에서 보면 제작한 코팅 전극은 HER보다 OER에 약간 더 적합하다는 것을 의미한다.
Fig. 4의 결과로부터 제작한 코팅 전극은 알칼리 수전해에 사용하는 7 M KOH 전해액과 0.2 A/cm2의 전류밀도에서 OER의 경우 1.35 V를, HER의 경우 -1.90 V를 보임을 알 수 있다. 따라서 제작한 코팅 전극은 수전해의 이론 전압이 1.23 V임을 고려하면 낮은 전압과 함께 AWE용 전극으로 사용 가능할 것으로 판단된다.
향후 제작한 코팅 전극의 AWE용 전극으로의 적용을 명확하게 파악하기 위해 AWE 셀에 적용한 전압 특성에 관한 연구가 필요할 것으로 사료된다.
4. 결 론
본 연구에서는 AWE용 전극으로의 적용을 위해 SUS 지지체에 NiFe2O4 분말을 딥-코팅하여 전극을 제작하였다. 또한 제작한 전극은 1, 3, 7 M의 KOH 수용액에서 전류밀도에 따른 OER과 HER의 전압 특성을 평가하여 다음과 같은 결론을 얻었다.
1) 코팅 전극은 지지체 위에 NiFe2O4 페이스트를 딥-코팅(dip-coating)하여 제작하였다.
2) SEM과 EDXS의 분석 결과, 코팅 전극은 지지체인 SUS-316에 NiFe2O4가 코팅되어 있는 것을 확인할 수 있었다.
3) 1, 3, 7 M의 KOH 농도에서 OER과 HER은 전류밀도가 증가함에 따라 전압이 증가하는 경향을 보였으며, KOH의 농도가 높아짐에 따라 전압은 감소하는 경향을 보였다.
4) 제작한 코팅 전극은 AWE에 사용하는 7 M KOH 전해액과 0.2 A/cm2의 전류밀도에서 OER의 경우 1.35 V, HER의 경우 -1.90 V를 보였다.
5) 제작한 코팅 전극은 수전해의 이론 전압이 1.23 V임을 고려하면 낮은 전압과 함께 AWE용 전극으로 사용 가능할 것으로 판단되었다.
References
- Intergovernmental Panel on Climate Change (IPCC), “Global warming of 1.5℃: special report”, IPCC, 2020. Retrieved from https://www.ipcc.ch/sr15/, .
- International Energy Agency (IEA), “Net zero by 2050: a roadmap for the global energy sector”, IEA, 2021. Retrieved from https://www.iea.org/reports/net-zero-by-2050, .
- G. J. Hwang, K. S. Kang, H. J. Han, and J. W. Kim, “Technology trend for water electrolysis hydrogen production by the patent analysis”, Journal of Hydrogen and New Energy, Vol. 18, No. 1, 2007, pp. 95-108. Retrieved from https://koreascience.kr/article/JAKO200721036737392.page, .
-
G. J. Hwang and H. S. Choi, “Hydrogen production systems through water electrolysis”, Membrane Journal, Vol. 27, No. 6, 2017, pp. 477-486.
[https://doi.org/10.14579/MEMBRANE_JOURNAL.2017.27.6.477]
-
G. J. Hwang, B. M. Gil, and C. H. Ryu, “Preparation of the electrode using NiFe2O4 powder for the alkaline water electrolysis”, Journal of Industrial and Engineering Chemistry, Vol. 48, 2017, pp. 242-248.
[https://doi.org/10.1016/j.jiec.2017.01.011]
-
R. Solmaz, “Electrochemical preparation and characterization of C/Ni–NiIr composite electrodes as novel cathode materials for alkaline water electrolysis”, International Journal of Hydrogen Energy, Vol. 38, No. 4, 2013, pp. 2251-2256.
[https://doi.org/10.1016/j.ijhydene.2012.11.101]
-
D. Chanda, J. Hnát, M. Paidar, J. Schauer, and K. Bouzek, “Synthesis and characterization of NiFe2O4 electrocatalyst for the hydrogen evolution reaction in alkaline water electrolysis using different polymer binders”, Journal of Power Sources, Vol. 285, 2015, pp. 217-226.
[https://doi.org/10.1016/j.jpowsour.2015.03.067]
-
G. S. Tasic, S. P. Maslovara, D. L. Zugic, A. D. Maksic, and M. P. M. Kaninski, “Characterization of the Ni–Mo catalyst formed in situ during hydrogen generation from alkaline water electrolysis”, International Journal of Hydrogen Energy, Vol. 36, No. 18, 2011, pp. 11588-11595.
[https://doi.org/10.1016/j.ijhydene.2011.06.081]
-
T. Liu, X. Wang, X. Jiang, C. Deng, S. Niu, J. Mao, W. Zeng, M. Liu, and H. Liao, “Mechanism of corrosion and sedimentation of nickel electrodes for alkaline water electrolysis”, Materials Chemistry and Physics, Vol. 303, 2023, pp. 127806.
[https://doi.org/10.1016/j.matchemphys.2023.127806]
-
A. E. Mauer, D. W. Kirk, and S. J. Thorpe, “The role of iron in the prevention of nickel electrode deactivation in alkaline electrolysis”, Electrochimica Acta, Vol. 52, No. 11, 2007, pp. 3505-3509.
[https://doi.org/10.1016/j.electacta.2006.10.037]
-
J. Landon, E. Demeter, N. İnoğlu, C. Keturakis, I. E. Wachs, R. Vasić, A. I. Frenkel, and J. R. Kitchin, “Spectroscopic characterization of mixed Fe-Ni oxide electrocatalysts for the oxygen evolution reaction in alkaline electrolytes”, ACS Catalysis, Vol. 2, No. 8, 2012, pp. 1793-1801.
[https://doi.org/10.1021/cs3002644]
-
X. G. Jiang, Y. P. Zhang, C. Song, Y. C. Xie, T. K. Liu, C. M. Deng, and N. N. Zhang, “Performance of nickel electrode for alkaline water electrolysis prepared by high pressure cold spray”, International Journal of Hydrogen Energy, Vol. 45, No. 58, 2020, pp. 33007-33015.
[https://doi.org/10.1016/j.ijhydene.2020.09.022]
-
M. Koj, J. Qian, and T. Turek, “Novel alkaline water electrolysis with nickel-iron gas diffusion electrode for oxygen evolution”, International Journal of Hydrogen Energy, Vol. 44, No. 57, 2019, pp. 29862-29875.
[https://doi.org/10.1016/j.ijhydene.2019.09.122]
-
A. Delvaux, G. Lumbeeck, H. Idrissi, and J. Proost, “Effect of microstructure and internal stress on hydrogen absorption into Ni thin film electrodes during alkaline water electrolysis”, Electrochimica Acta, Vol. 340, 2020, pp. 135970.
[https://doi.org/10.1016/j.electacta.2020.135970]
-
T. Rauscher, C. I. Bernäcker, S. Loos, M. Vogt, B. Kieback, and L. Röntzsch, “Spark-plasma-sintered porous electrodes for efficient oxygen evolution in alkaline water electrolysis”, Electrochimica Acta, Vol. 317, 2019, pp. 128-138.
[https://doi.org/10.1016/j.electacta.2019.05.102]
-
K. Zhang, W. Xiao, J. Li, J. Liu, and C. Yan, “Two-step preparation of porous nickel-sulfur electrode for hydrogen evolution in alkaline water electrolysis”, Electrochimica Acta, Vol. 228, 2017, pp. 422-427.
[https://doi.org/10.1016/j.electacta.2017.01.105]
-
I. A. Poimenidis, N. Papakosta, A. Klini, M. Farsari, M. Konsolakis, P. A. Loukakos, and S. D. Moustaizis, “Electrodeposited Ni foam electrodes for increased hydrogen production in alkaline electrolysis”, Fuel, Vol. 342, 2023, pp. 127798.
[https://doi.org/10.1016/j.fuel.2023.127798]
-
M. Allam, M. Benaicha, and A. Dakhouche, “Electrodeposition and characterization of NiMoW alloy as electrode material for hydrogen evolution in alkaline water electrolysis”, International Journal of Hydrogen Energy, Vol. 43, No. 6, 2018, pp. 3394-3405.
[https://doi.org/10.1016/j.ijhydene.2017.08.012]