
발전용 연료전지 형식에 따른 균등화 발전비용 분석
2022 The Korean Hydrogen and New Energy Society. All rights reserved.
Abstract
For the economic analysis of fuel cells, levelized cost of electricity was calculated according to the type, capacity, and annual production of the fuel cells. The cost of every component was calculated through the system component breakdown. The direct cost of the system included stack cost, component cost, assembly, test, and conditioning cost, and profit markup cost were added. The effect of capacity and annual production was analyzed by fuel cell type. Sensitivity analysis was performed according to stack life, capital cost, project period, and fuel cost. As a result, it was derived how much the economic efficiency of the fuel cell improves as the capacity increases and the annual production increases.
Keywords:
Fuel cell system, Economic analysis, Cost, Levelized cost of electricity, Sensitivity analysis키워드:
연료전지 시스템, 경제성 평가, 비용, 균등화발전원가, 민감도 분석1. 서 론
산업혁명 이후 가속화된 이산화탄소의 배출로 지구온난화 및 기후변화는 가속화되고 있으며, 전 세계적으로 이산화탄소 배출을 줄이기 위한 노력이 지속되고 있다. 기술이 발달함에 따라 인간의 편의는 증가하였지만 이에 따른 에너지 사용도 같이 증가하였다. 산업혁명부터 현재에 이르기까지 지구에서 사용되는 에너지원은 대부분 화석연료였으며, 화석연료를 대체하기 위한 기술로 원자력 발전, 태양광 발전, 풍력 발전 등이 개발되었고 현재 사용되고 있다. 이산화탄소 배출을 줄일 수 있는 수소가 대안으로 떠오르고 있으며, 우리나라도 수소 경제를 통하여 무탄소 에너지 공급망을 구축하려는 전략을 가지고 있다.
산업분류별 전력사용량의 통계 자료에 따르면 우리나라의 전력 사용량은 2021년 상반기 기준 약 60%가 제조 산업에 활용되었다. 우리나라 산업 특성상 제조업의 비중이 큰 만큼 제조업에서 가장 많은 에너지를 소비하고 있는 상황이다. 미국, 일본, 독일과 같은 선진국에서 전력 소비량이 감소세를 보이는 반면에 국내 전력 소비량은 증가하고 있는 추세이기 때문에 이산화탄소 배출을 저감할 수 있는 에너지 전환 기술이 더욱 필요하다. 이산화탄소 배출을 저감하기 위해서는 궁극적으로 수소나 암모니아와 같은 무탄소연료를 사용한 에너지원을 사용하거나 carbon capture utilization (CCU) 혹은 carbon capture and storage (CCS)와 같은 이산화탄소 포집·활용 기술을 연계하여야 한다. 그러나 기술의 성숙도를 고려하자면 현재 가장 효과적인 방법은 고효율 에너지 변환 장치를 사용하여 전력 전환 효율을 높이는 것이다.
연료전지는 전기화학 반응을 이용한 에너지 변환 장치로 수소를 연료로 이용하기 때문에 이산화탄소를 배출하지 않고 높은 전력 변환 효율을 가진다는 장점이 있다. 다만, 현재 대부분의 상업용 발전 연료전지는 메탄(CH4)을 주성분으로 하는 도시가스를 이용하고 있어 이산화탄소를 배출한다. 일부 차량용, 지게차용, 비상발전용 연료전지가 순수소를 사용하는 연료전지로 상업화 되었다. 메탄을 연료로 이용하는 발전용 연료전지는 낮은 발전 용량에서도 높은 전력 변환 효율을 가지기 때문에 분산 발전 시 큰 장점을 가진다.
한국전력공사 월별 전력통계속보에서 발표한 2021년 우리나라 발전량은 576,809 GWh로 27.4%가 원자력, 34.3%가 석탄, 29.2%가 가스에서부터 생산되었다. 약 7.5%의 전력만 수소, 태양광, 풍력, 수력 등의 신재생에너지에서 생산되었다. 원자력 발전 40원/kWh, 석탄발전 60원/kWh, 천연가스발전 170원/kWh, 중유발전 220원/kWh의 발전원가를 가지는 것으로 알려져 있으며, 신재생에너지의 경우 이러한 전통적인 발전원보다 더 비싼 발전단가를 가진다. 상대적으로 전력 단가가 비싼 신재생에너지의 보급이 증가하게 된다면 전력 단가 비용의 상승은 불가피하다. 따라서 증가하는 신재생에너지의 전력단가에 대한 분석과 더불어 분산발전의 대안으로 떠오르고 있는 연료전지의 전력단가에 대한 분석도 필수적으로 수행되어야 한다.
연료전지에서 생산된 전력에 대한 정확한 분석 및 예측은 연료전지를 이용하여 분산발전을 하고자 하는 발전 사업자와 연료전지를 국가 전력 믹스에 포함하고자 하는 정책 입안자에 필수적이다. 특히 연료전지 발전의 경우 정책에 따라 RPS REC 판매액이 추가적으로 발생하는 구조이기 때문에 발전사업자의 수익구조에서 상당 부분을 차지한다. 정책 입안자의 적절한 가중치 선정이 연료전지 산업 및 국내 신재생에너지 업계에 대한 지원 정책으로 나타날 것이며, 사업자는 면밀한 경제성 분석을 토대로 사업 전략을 도출하여 수익 창출이 가능하다.
연료전지의 경제성 분석을 수행하기 위해서는 비용과 수익의 구조를 구분하여야 한다. 비용 구조는 연료전지 시스템 비용과 전력설비 등 발전소 설비에 들어가는 투자비용과 천연가스의 연료 사용 시 요구되는 연료비, 그리고 운영을 위해 필요한 유지 및 보수에 관련된 비용이다. 수익구조의 경우 3가지 수익 구조가 있다. 생산된 전력을 전력 도매시장에 판매하여 계통한계가격(system marginal price, SMP)의 수익을 얻을 수 있으며, 신재생에너지 의무발전 공급 인증서(renewable energy certificate, REC)를 판매하여 얻을 수 있는 수익이 있다. 연료전지는 전기만 생산하는 게 아니라 열도 생산하기 때문에 열 수요처에 열을 판매하여 수익을 창출할 수도 있다.
연료전지 경제성 평가 시 고려하여야 하는 부분은 실제 설비를 구축하는 데 들어가는 설비비 비용을 타당하게 추정하는 것이며, 발전소 운영에 필요한 운영비용을 합리적으로 예측하는 것이다. 이러한 부분은 공학적 접근에 바탕하여 혹은 기존의 공개된 자료를 통하여 도출이 가능하다. 그러나 유가 변동에 의한 연료비 예측은 매우 어렵다. 이러한 예측 불가능한 부분은 여러 시나리오에 기반하여 분석을 수행하여야 한다. 예측 불가능한 변수를 배제하면 경제성 분석에서 가능한 가장 합리적이고 타당한 접근은 연료전지의 장치 비용을 가장 정확하게 예측하여 여러 변수에서의 영향을 분석하는 것이다.
연료전지 기술은 이미 상용화 되어 여러 국내외 업체에서 제품을 판매하고 있지만, 연료전지 시장은 초기 단계이기 때문에 연료전지가 대량 생산되지는 않고 있다. 현재 연료전지의 장치 비용은 대량 생산되지 않기 때문에 비싼 편이다. 현재 높은 가격의 장치 비용을 적용한 경제성 평가는 낮은 경제성을 보이기 때문에 정확한 평가 방법이 아니다. 대량 생산됨에 따라 연료전지의 장치 비용이 얼마나 낮아지고, 가까운 미래에 대량 생산함으로써 낮은 장치 비용을 가지는 연료전지를 통하여 전력을 생산하였을 때 가지는 경제성 분석이 더 의미 있는 경제성 분석이라고 할 수 있다.
Erdmann1)은 독일 시장에서 가정용 고체산화물 연료전지(solid oxide fuel cell, SOFC)가 경제성을 확보하기 위한 분석을 수행하였으며, 용량이 증가함에 따라 SOFC 연료전지 시스템의 비용이 감소하는 자료를 활용하여 용량이 경제성에 주는 영향을 반영한 결과를 도출하였다.
Staffell과 Green2)은 일본의 대규모 연료전지 실증 프로그램인 ENE·FARM의 회계 자료 및 실증 결과를 활용하여 보급 확대에 따른 가정용 연료전지의 가격 저감 정도를 분석하였다. 또한 이를 활용하여 경험의 가격 추정 곡선을 도출하였으며, 미래 연료전지의 단가를 전망하였다.
Naeini 등3)은 SOFC에서 발생하는 열화에 따른 내구성 저하를 경제성 분석에 반영하여 균등화전력비용(levelized cost of electricity, LCOE)을 도출하였으며, 여러 변수를 토대로 민감도 분석을 수행하였다.
발전용 연료전지의 경제성에 대한 연구는 많이 수행되었다4-6). 형식에 따른 연료전지의 발전단가 분석은 수행되지 않았으며, 특히, 대량 생산 및 기술 개발에 따라 시스템 비용이 낮아지는 영향을 고려한 연구는 수행되지 않았다.
본 연구에서는 다양한 연료전지 형식에 따라 그리고 용량 증가 및 규모화에 따른 장치 비용을 추정하였으며, 이를 토대로 전력단가를 분석하고 주요 변수에 대하여 민감성 분석을 수행하였다.
2. 연료전지 형식별 장치 비용
2.1 형식에 따른 연료전지 분류
연료전지는 전해질막의 종류, 전달 이온의 종류, 작동 온도에 따라 다양하게 분류되며, 연료전지가 가지는 특성에 따라 활용처가 상이하다. Table 1에 연료전지의 종류에 따른 특성을 나타내었다. SOFC는 높은 전력 변환효율을 갖고 있어 발전용 연료전지로 사용되고 있으며, 고분자 전해질막 연료전지(polymer electrolyte membrane fuel cell, PEMFC)는 낮은 작동온도 및 높은 동적 특성으로 인하여 가정용 연료전지 및 차량용으로 사용되고 있다. 용융탄산염 연료전지(molten carbonate fuel cell, MCFC)와 인산염 연료전지(phosphoric acid fuel cell, PAFC)도 대용량 발전에 유용하기 때문에 발전용 연료전지로 사용되고 있다.
연료전지는 스택 자체만 가지고 운전이 불가능하며, balance of plant (BOP)와 같은 보조 장치와 유기적으로 결합되어 작동한다. 형식에 따라 다르지만, 일반적으로 개질기, 블로워, 열교환기, 히터, 가습기 등으로 구성된다. 시스템을 어떻게 구성하느냐에 따라 전력 변환 효율, 구성품 종류 및 사양, 시스템 비용이 결정되게 된다.
2.2 발전용 연료전지 시스템의 구성
본 연구에서는 발전용 연료전지로 사용되는 PEMFC, SOFC, MCFC, PAFC를 대상으로 선정하였으며, 각 연료전지의 시스템 구성은 문헌4-13)에 기반하여 선정하였다.
PEMFC와 SOFC는 용량에 따라 25 kW 급 이하의 적은 용량에서는 가정용으로 사용되며, 100 kW급 이상의 큰 용량에서는 상업용으로 사용되기 때문에 가정용과 상업용을 구분하였으며, MCFC와 PAFC의 경우 특성상 큰 용량에 적합하기 때문에 상업용만 고려하였다.
Fig. 1은 가정용과 상업용 PEMFC 시스템의 대표적인 구성도를 나타낸다. 스택에 공급되는 수소는 개질기를 통해서 메탄을 개질하여 생산되는데, 이때 일부의 일산화탄소가 발생한다. PEMFC의 스택은 Pt를 촉매로 사용하고, Pt 촉매의 내구성 확보를 위해서는 고순도 수소가 스택에 공급되어야 한다. Pt 촉매의 내구성 확보를 위하여 개질기와 더불어 일산화탄소 선택적 산화반응(preferential oxidation, PrOx) 장치가 시스템의 연료극측 구성품으로 있다. 공기측의 경우 공기 필터, 블로워, 가습공기 공급을 위한 가습장치로 구성된다. 연료전지에서 발생하는 열을 회수 및 제거하고 연료전지의 작동온도를 맞춰주기 위한 냉각 시스템이 있다. 냉각 시스템은 냉각수 펌프, 열교환기, 냉매 등으로 구성된다.
연료전지 스택에서 발생되는 전기는 직류이기 때문에 계통연결의 위한 electrical balance of plant (EBOP)도 연료전지 시스템의 중요한 구성품이다. 전력 제어 장치, DC-DC converter, DC-AC converter 등으로 구성된다.
Fig. 1(b)는 상업용 PEMFC 시스템이 구성도를 나타낸다. 가정용과 유사하게 구성되어 있으나, BOP를 공유하고 여러 개의 스택이 병열형으로 구성된다는 특징이 있다.
Fig. 2는 가정용과 상업용 SOFC 시스템의 대표적인 구성도를 나타낸다. PEMFC와 유사하게 개질기가 연료극측에 있지만, SOFC는 일산화탄소도 연료로 사용하기 때문에 일산화탄소 처리를 위한 PrOx 반응기는 사용하지 않는다. 또한, 가습공기 장치와 냉각장치도 사용되지 않는다. 높은 온도에서 작동하지만 상대적으로 적은 BOP로 구성된다.
가정용과 상업용에서는 발전 용량의 차이를 가지며, 상업용 시스템에서는 하나의 BOP 시스템이 여러 개의 병렬형 스택과 연결된 구조를 가진다.
MCFC와 PAFC의 경우 문헌상 발표된 자료가 제한적이며, 상용화된 모델이 각 연료전지 형식의 대표성을 띄고 있어 Fuel Cell Energy 사(Fairfield, CT, USA)의 DFC 1500과 Doosan Fuel Cell (Iksan, Korea)의 PureCell 400을 대표적인 모델로 선정하였다.
2.3 형식에 따른 시스템 장치 비용 추산
경제성 평가를 위하여 시스템 구축에 요구되는 비용을 추정하는 방법은 시스템 업체로부터 전달받은 전체 비용을 사용하는 방법과 시스템 구성에 들어가는 각 구성품의 비용을 종합하여 전체 시스템의 비용을 추정하는 방법이 있다. 전자의 경우 실질적인 값이기 때문에 신뢰도가 높고, 빠른 경제성 분석이 가능하다. 후자의 경우는 실제 업체에서 요구하는 비용과 검증이 필요하나 구체적으로 각 구성품에서 요구되는 비용을 산출할 수 있기 때문에 장기적으로 시스템 대량 생산에 따른 비용 추정, 각 구성품이 전체 비용에서 차지하는 비율 등 다양한 분석이 가능하다.
본 연구에서는 PEMFC와 SOFC에 대하여 시스템의 하위 구성품 비용을 구체화하여 전체 비용을 계산하였다. MCFC와 PAFC의 경우 실증 사례 및 문헌에서 나타난 전체 비용을 값을 활용하여 시스템 비용 추정하였다.
PEMFC 및 SOFC 시스템에 대한 비용 데이터는 여러 용량 및 생산량에 대하여 나타낼 수 있다. 이러한 세부 정보에는 스택 제조에 대한 비용 데이터, BOP 비용, 조립, 컨디셔닝 및 테스트 비용이 포함되며, 총 시스템 비용(CSYS)은 시스템 직접 비용(CTDC)과 회사 수익 마크 업(markup) 비용(mkp)에 따라 다음과 같이 계산할 수 있다. 마크 업 비용이란 부수적인 비용과 이익을 포함하여 판매 가격에 도달하기 위해 판매자가 시스템 직접 비용 가격에 추가 한 값을 말하며 본 연구에서는 50%로 가정하였다.
(1) |
시스템 직접 비용은 스택 비용(CSTK), BOP 비용(CBOP) 그리고 조립·시험·컨디셔닝 비용(CATC)으로 구성된다.
(2) |
문헌에서 조사된 PEMFC 및 SOFC 시스템에 대한 가정용 및 상업용 시스템의 총 시스템 비용을 구성하는 각 요소의 자료들은 문헌에서 찾은 자료의 평균값을 사용하여 계산하였다. 또한, 문헌에 제시된 구성품의 비용을 사용함에 있어서 바로 사용하지 않고, Chemical Engineering Plant Cost Index (CEPCI)값을 이용하여 2019년의 값으로 모두 통일하여 비용을 추산하였다.
MCFC와 PAFC의 경우 시스템 전체 비용을 추산함에 있어서 앞선 PEMFC와 SOFC처럼 하위 구성품의 모든 비용을 기반으로 전체 시스템 비용을 추정할 수 있는 자료가 제한적이었기 때문에 시스템 전체 비용에 대한 자료만 확보할 수 있었다.
2.4 연료전지 시스템 비용 분석
PEMFC의 스택은 촉매, membrane electrode assembly (MEA), gas diffusion layer (GDL), 가스켓, 분리판, 체결판 등으로 구성되며, 스택 비용에는 위의 구성품 뿐만 아니라 조립 설비, 인건비, 시험·검사비용이 추가적으로 들어간다.
BOP에는 연료 공급 및 처리장치, 물 공급 장치, 공기 공급 장치, 열교환기, AC 및 DC 전력 변환기 등으로 구성되며, 여기에도 시스템 조립을 위한 조립비용이 추가적으로 고려되어야 한다.
Fig. 3은 연간 생산량 및 발전 용량에 따른 가정용 PEMFC 스택 및 BOP의 비용을 나타낸다. 연간 생산량이 증가함에 따라 그리고 발전 용량이 증가함에 따라 비용이 감소하는 것을 볼 수 있다. 생산의 규모화를 통하여 비용이 저감되기 때문이며, 이러한 효과는 스택에서 두드러진다. BOP의 경우 기상용화된 구성품들이 다수이기 때문에 대량생산을 하여도 비용 저감의 영향이 크지 않다.
연간 생산량이 적은 경우에서 스택의 비용은 kW 당 7,390 $에 달하는 반면 5, 10, 25 kW 용량의 비용은 kW당 각각 2,106, 1,267 및 755 $로 감소한다.
Table 2는 Fig. 3의 스택과 BOP 비용에서 가장 낮은 비용을 가지는 경우와 가장 높은 비용을 가지는 경우 각 구성품들이 차지하는 비율을 나타낸다. 1 kW 시스템이 연간 100대 생산될 경우 대부분의 비용은 MEA로부터 발생하며 그 다음으로 발생하는 비용은 시험 및 테스트 비용이 차지한다. 그러나 연간 생산량이 증가하고 용량이 증가하는 경우 시험 및 테스트 비용이 차지하는 비율이 급격히 줄어든다. 1 kW 시스템의 BOP 비용은 kW 당 16,000-9,500 $이다. 그러나 연간 생산량이 증가하는 경우 이러한 비용은 kW 당 3,200-2,100 $ 범위로 감소하며, 연간 50,000대가 생산되는 250 kW 시스템의 경우 kW 당 800 $까지 감소하게 된다.

Proportion of the components the total cost of the 1kW residential PEMFC system at low production volumes and 25kW system at high production volumes
Fig. 4은 연간 생산량 및 발전 용량에 따른 상업용 PEMFC 스택 및 BOP의 비용을 나타낸다. 가정용과 동일하게 연간 생산량이 증가함에 따라 그리고 발전 용량이 증가함에 따라 비용이 감소하는 것을 볼 수 있다. 그러나 비용이 감소되는 정도는 가정용에 비하여 상대적으로 적은 것을 알 수 있다. 생산의 규모화를 통하여 비용이 저감되지만, 최소 용량이 50 kW정도이기 때문에 최소 용량에서도 어느 정도 생산이 규모화를 가지고 있기 때문이다. BOP의 경우 이미 기상용화된 구성품들이 다수이기 때문에 상업용에서도 대량생산을 하여도 비용 저감의 영향이 크지 않다.
상업용 50 kW 급 PEMFC시스템은 연간 생산량이 적은 경우에서 스택의 비용은 kW당 563 $에 달하는 반면 100, 250 kW 용량의 비용은 kW당 각각 436, 352 $로 감소한다.
Table 3는 Fig. 4의 스택과 BOP 비용에서 가장 낮은 비용을 가지는 경우와 가장 높은 비용을 가지는 경우 각 구성품들이 차지하는 비율을 나타낸다. 가장 높은 비용을 가지는 경우에서 가장 낮은 비용을 가지게 되는 경우와 비교하면, 각 구성품이 차지하는 비율은 거의 유사하다. 상업용 시스템의 경우 가장 작은 용량이 50 kW이기 때문에 이 경우에도 이미 대량생산에 가깝기 때문에 용량과 연간 생산량이 증가하여도 비율이 크게 변화하지 않음을 확인 할 수 있다.

Proportion of the components the total cost of the 100 kW commercial PEMFC system at low production volumes and 250 kW system at high production volumes
SOFC의 스택은 셀, 분리판, 연료극 프레임 및 메쉬, 공기극 프렘 및 메쉬, 체결판, 유리 실링제 등으로 구성되며, PEMFC 비용과 동일하게 위의 구성품뿐만 아니라 조립 설비, 인건비, 시험·검사비용이 추가적으로 들어간다. 또한, SOFC의 경우 고온에서 스택의 전처리가 필요하기 때문에 이러한 금액도 필수적으로 반영되어야 한다.
BOP도 PEMFC와 유사하게 연료 공급 및 처리장치, 공기 공급 장치, 열교환기, AC 및 DC 전력 변환기 등으로 구성되나, 일산화탄소를 연료로 사용하기 때문에 일산화탄소 선택적 산화반응기가 제외된다. SOFC의 BOP도 시스템 조립을 위한 조립비용이 추가적으로 고려되어야 한다.
Fig. 5는 연간 생산량 및 발전 용량에 따른 가정용 SOFC 스택 및 BOP의 비용을 나타낸다. 생산의 규모화를 통하여 비용이 저감되기 때문에 연간 생산량과 발전 용량이 증가함에 따라 비용이 감소한다. SOFC 기술은 PEMFC에 비하여 기술 초기 단계로 생산량 증가와 용량 증가에 대하여 매우 급격하게 변동되는 것을 알 수 있다. 그러나 BOP의 경우 PEMFC와 마찬가지로 기상용화된 구성품들이 다수이기 때문에 대량생산을 하여도 비용 저감의 영향이 크지 않다.
연간 생산량이 적은 경우에서 스택의 비용은 kW당 7,880 $에 달하는 반면 5, 10, 25 kW 용량의 비용은 kW 당 각각 2,231, 1,243 및 799 $로 감소한다.
Table 4는 Fig. 5의 스택과 BOP 비용에서 가장 낮은 비용을 가지는 경우와 가장 높은 비용을 가지는 경우 각 구성품들이 차지하는 비율을 나타낸다. 1 kW 시스템이 연간 100대 생산될 경우 대부분의 비용은 유리 밀봉제로부터 발생한다. 그러나 연간 생산량이 증가하고 용량이 증가하는 경우 셀이 차지하는 비용이 급격히 상승함을 알 수 있다.

Proportion of the components the total cost of the 1 kW residential SOFC system at low production volumes and 25 kW system at high production volumes
BOP의 경우 1 kW 시스템이 연간 100대 생산될 경우 많은 비용이 연료공급 및 처리 시스템에서 발생하나 규모화가 되는 경우 EBOP가 차지하는 비율이 증가함을 알 수 있다.
Fig. 6은 연간 생산량 및 발전 용량에 따른 상업용 SOFC 스택 및 BOP의 비용을 나타낸다. 가정용과 동일하게 연간 생산량과 발전 용량이 증가함에 따라 비용이 감소하는 것을 볼 수 있다. 그러나 생산의 규모화를 통하여 비용이 저감되지만, 최소 용량이 50 kW이기 때문에 최소 용량에서도 어느 정도 규모화를 가지고 있어 비용이 감소되는 정도는 가정용에 비하여 상대적으로 적다. BOP의 경우도 가정용과 상업용에서 초기 시동의 방식이 다르기 때문에 초기 시동 히터의 유무와 일체화된 전력변환기의 차이 외에 이미 기상용화된 구성품들이 다수이기 때문에 상업용에서도 대량생산을 하여도 비용 저감의 영향이 크지 않다.
상업용 50 kW 급 SOFC 시스템은 연간 생산량이 적은 경우에서 스택의 비용은 kW 당 732 $에 달하는 반면 100, 250 kW 용량의 비용은 kW 당 각각 438, 323 $로 감소한다.
Table 5는 Fig. 6의 스택과 BOP 비용에서 가장 낮은 비용을 가지는 경우와 가장 높은 비용을 가지는 경우 각 구성품들이 차지하는 비율을 나타낸다. 가장 높은 비용을 가지는 경우에서 가장 낮은 비용을 가지게 되는 경우와 비교하면, 각 구성품이 차지하는 비율은 거의 유사하다.

Proportion of the components the total cost of the 100 kW commercial SOFC system at low production volumes and 250 kW system at high production volumes
Fig. 7은 연료전지의 용량과 연간 생산량에 따른 전체 장치 비용을 추산한 그래프이다. 스택 비용, BOP 비용, 조립 및 컨디셔닝 비용과 더불어서 마크 업 비용까지 더해진 실제 구매 비용이라고 볼 수 있다. PEMFC와 SOFC 두 경우에서 연간 생산량이 증가함에 따라 비용이 저감되는 정도보다 용량이 증가함에 따라 비용이 저감되는 정도가 더 큰 것을 알 수 있다. 앞서 분석한 스택과 BOP의 비용뿐만 아니라 조립 및 컨디셔닝 비용에 의한 영향으로 볼 수 있으며, 작은 시스템의 경우 조립과 컨디셔닝을 여러 차례 수행하여야 하는 반면에 큰 용량의 경우 이러한 비용을 줄일 수가 있게 되기 때문이다.
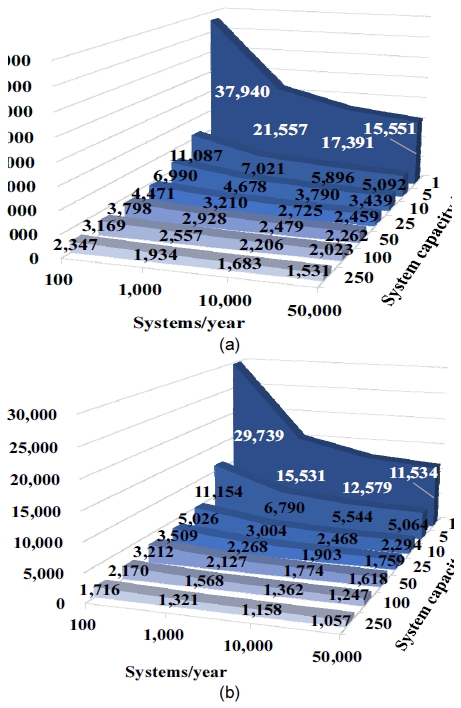
Cost of the total systems cost with markup of 50% for the stationary (a) PEMFC and (b) SOFC systems with the average data
연료전지 기술이 성숙되고, 보급이 증가함에 따라 연간 생산량이 증가할 경우 PEMFC의 시스템 가격은 1 kW 당 1,531 $까지 낮출 수 있을 것으로 예상되며, SOFC의 경우는 1,057 $까지 낮아질 것으로 전망된다.
Fig. 8은 MCFC와 PAFC 시스템에 대한 비용을 나타내며 이는 앞선 결과처럼 구성품의 비용을 산정하여 도출한 비용이 아닌 실증 및 설치 사례시 보고된 비용을 나타낸다. 또한, 장치 비용과 더불어서 설치비까지 포함된 비용을 나타낸다. 신뢰성 있는 데이터의 확보가 제한적이었으며, NREL의 자료를 참고하였다13-16).
3. 균등화 발전비용 계산 과정
3.1 균등화 발전 비용 계산을 위한 가정
앞서 추정된 총 비용은 연료전지 장치만을 구입한 장비 비용(purchased equipment cost, PEC)을 나타낸다. 이러한 장비 비용은 배관, 계기 및 제어, 전기 장비 및 재료, 토지, 토목, 구조 및 건축 작업, 서비스 시설과 같은 직접 비용의 일부이며, 실제 사업 및 설비 구축을 위해서는 엔지니어링 및 감독, 건설, 사고, 창업 비용, 운영 자본, 라이센스, 연구 개발 등의 간접 비용이 추가되어야 한다.
대부분의 발전 사업의 장치 비용을 제외한 직접비용와 간접비용은 구체화된 경우에 상황에 맞게 계산될 수 도 있으나, 경제성 평가에서는 일반적인 경험칙이 적용된다. 본 연구에서는 Bejan 등17)의 연구에 기초한 값을 사용하였으며, Table 6에 각 요소별 값을 나타내었다.
3.2 투자비용 및 운영비용 분석
장치 비용의 백분율에 기반한 값은 용량이 큰 경우 대략적인 추정 시 유용하지만 적은 용량의 시스템에서는 부적절할 수 있다. 토지, 토목, 구조 및 건축 작업 등의 부지 비용의 경우 PEC의 약 100%로 추정하는데17), 적은 용량의 시스템의 경우 이러한 방식의 비용이 실제보다 과하게 계산되어 타당하지 않다. 앞선 결과에서 보았듯이, PEMFC과 SOFC 시스템의 연간 생산량과 용량에 따른 비용 감소 정도는 꽤 가파르다. 따라서 PEC의 백분율로 추정되는 모든 비용은 이러한 시스템의 용량에 영향을 받는다. 예를 들어, 토지, 토목, 구조 및 건축 작업은 실제로 PEC의 생산 용량에 관계없이 발전용 시스템에서 일정한 비용을 가질 수 있다. 소규모 발전 시스템의 경우 토지 비용은 PEC 비용보다는 설치 용량에 비례하는 게 타당하다. MCFC 설비의 경우 180-215 m2/MW 사이의 설치 공간을 가정하며, SOFC는 32 m2/MW만 사용한다고 알려져 있다. 이렇게 보듯이 토지 비용은 PEC의 백분율이 아니라 시스템 설치 공간의 함수로 추정해야 타당하다.
가정용 연료전지 시스템은 토지 비용 측면에서 상업용과 차이를 가진다. 상황에 따라 다르지만, 일반적으로 가정에 설치하는 경우 연료전지 설치와 관련된 개별적인 토지를 구입하지 않는다. 가정용 경우 비용이 운영비용으로 할당할 수 있다.
일반적으로 직접 비용에서 고려되는 항목들의 대부분이 PEC에 포함되어 있다. 포함되어 있지 않은 토지, 토목, 구조 및 건축 작업은 1.4 MW 미만의 시스템에 대해 앞서 표에 제시된 비율에 따라 추정하였다. 또한, 대부분의 연료전지 시스템은 모듈식이어서 건설에 필요한 시간이 짧다(2.4 MW 시스템의 경우 3개월18), Bloom Energy의 경우 1.35 MW 시스템의 경우 3개월 반19)). 본 연구에서 다루는 용량 범위에서는 서비스 시설이 무시될 수 있다. 간접비 중에 설계 및 감독(E&S), 건설 비용(CC) 및 비상 시스템에 대한 비용이 일반적으로 33%를 산정하나, 가정용 규모 시스템의 경우 대부분 설치비로 직접 비용에 포함되기 때문에 무시될 수 있다. 시동 비용과 같은 다른 비용은 대부분 건설 완료 후에 수행해야 하는 설계 변경과 관련이 있기 때문에 무시될 수 있다17). 250 kW 미만의 경우 운전 자본이 무시될 수 있는데, 이는 전기와 열 발전에서 이익을 얻기 위해 설치되는 것이 아니라 주택이나 건물에서 그리드의 대안으로 사용되기 때문이다.
운영비는 고정비와 변동비로 나뉜다. 고정비용은 기업의 소득율, 보험료율 및 기타 세금, 인건비, 경영, 마케팅, 유통 등과 같은 일반 및 행정 비용(G&A)을 포함한다. 소득율과 세금은 지역 규정에 따라 달라지며 시간에 따라 크게 달라질 수 있지만 평균 연간 가치는 비용 추정에 충분하다. 인건비는 연봉과 인원수에 따라 달라진다. 소규모 연료전지 시스템에서는 운영 및 유지보수 인력이 필요하지 않는다. 이러한 시스템의 대부분은 사용자가 원격으로 제어할 수 있는 모니터링 시스템을 포함하며, 특히 가정용 시스템에서는 인력을 두어야 할 만큼의 운영 사항 및 고려해야 할 시스템의 부품이 없다. 대부분의 상업용 시스템은 일반적으로 연료전지 시스템 제작자가 할당한 인력에 의해 원격으로 운영된다.
그러나 최근의 원격 제어 시스템은 시스템의 모든 측면을 24시간 모니터링 하는 자동화된 알고리즘에 의해 제어가 수행되기 때문에 직원의 필요성도 감소하는 추세이다. 이런 상황에서 인건비로 인한 고정 운영비 배정은 쉽지 않다. 연료전지 시스템의 인건비 산정에서 인력의 시간과 비용은 여러 설비로 나눌 수 있다. 일반적인 발전소의 경우 O&M 인력은 MW 당 0.18 작업자20)로 가정한다. 연간 작업 시간이 2,080시간임을 고려하면 직원은 250 kW 시스템에 연간 93시간을 할애할 수 있으며, 해당 인력을 사용함을 가정하였다. Table 7에 본 연구에서 사용한 시스템의 운영비용 가정을 나타내었다.
4. 균등화 발전비용 계산 결과
4.1 연료전지 형식에 따른 균등화 발전비용
앞의 결과를 이용하여 PEMFC, SOFC, MCFC, PAFC의 균등화 발전비용을 계산하였다. 특히, 연료전지의 용량에 따라 설비 가격 저감의 영향 및 연간 생산량 증가에 따른 설비 가격 저감의 효과를 분석하도록 다양한 조건에서 결과 값을 도출하였다. 각 조건에서의 균등화 발전비용에서 CAPEX, carrying charge, O&M 그리고 fuel이 차지하는 비율을 구분하여 나타내었다.
Fig. 9는 가정용과 상업용 PEMFC 시스템의 균등화 발전비용을 나타낸다. PEMFC 시스템에서 1 kW 급 시스템을 연간 100대 생산하는 경우 2.7 $/kWh의 균등화 발전비용을 가지며, 균등화 발전비용은 용량이 증가함에 따라 그리고 연간 생산량이 증가함에 따라 크게 감소하는 것을 알 수 있다. 모든 시스템의 효율은 동일하기 때문에 연료가 차지하는 비용은 모두 동일하다. 25 kW 급의 시스템을 연간 50,000대 생산하는 경우 0.43 $/kWh의 균등화 발전비용을 가짐을 확인할 수 있다.
발전용 시스템 또한 가정용 시스템과 동일하게, 용량이 증가함에 따라 그리고 연간 생산량이 증가함에 따라 균등화 발전비용은 감소하나 상업용 시스템의 경우 감소폭이 가정용에 비하여 적다. 가장 작은 용량이 50 kW임을 고려하면 연간 100대를 생산하는 경우라도 스택의 구성품은 상용화에 가깝기 때문에 용량 증가 및 연간 생산량 증가하더라도 설비 비용이 크게 감소하지 않아 균등화 발전비용도 감소폭이 적다. 250 kW 시스템을 연간 50,000대 생산하는 경우 0.36 $/kWh의 균등화 발전비용에 도달할 수 있음을 알 수 있다.
Fig. 10은 가정용 및 상업용 SOFC 시스템의 균등화 발전비용을 나타낸다. PEMFC 시스템과 동일하게 용량이 증가함에 따라 그리고 연간 생산량이 증가함에 따라 균등화 발전비용이 감소한다. SOFC 시스템에서 1 kW 급 시스템을 연간 100대 생산하는 경우 2.43 $/kWh의 균등화 발전비용을 가지며, 25 kW 시스템을 연간 50,000대 생산하는 대량생산 체제에서는 0.33 $/kWh의 균등화 발전비용을 가진다. PEMFC에 비하여 상대적으로 높은 효율을 가지기 때문에 균등화 발전비용이 더 낮다.
상업용 시스템의 경우 큰 용량으로 인하여 균등화 발전비용이 더 낮다. 250 kW 시스템을 연간 50,000대 생산하는 경우 0.28 $/kWh의 균등화 발전비용에 도달하게 된다.
Fig. 11은 MCFC와 PAFC의 균등화 발전비용을 나타낸다. MCFC의 경우 가정용 시스템에 해당하는 작은 용량의 시스템은 없고, 가장 작은 시스템이 200 kW이다. 따라서 매우 큰 용량을 가지기 때문에 PEMFC나 SOFC에 비하여 대량생산이 가지는 효과를 가지는 특성이 있다.
본 연구에서는 MCFC와 PAFC의 장치 비용을 계산함에 있어서, 앞선 PEMFC와 SOFC와 동일하게 모든 하위 구성품에 대하여 비용을 산정하고 규모화의 영향을 고려한 방식을 사용하지 않았기 때문에, 연간 생산량이 증가함에 따른 균등화 발전비용의 저감 영향을 분석하지 않았다.
MCFC 시스템은 200 kW 용량에서 발전 시 0.68 $/kWh의 균등화 발전 비용을 가지며, 250 kW로 증가하면 0.66 $/kWh의 균등화 발전 비용을 가진다. 1,400 kW의 용량으로 증가하면 균등화 발전비용은 더 감소하게 되며, 0.42 $/kWh까지 감소함을 확인할 수 있다.
PAFC 시스템은 200 kW 용량에서 발전 시 0.5 $/kWh의 균등화 발전 비용을 가지며, 400 kW로 증가하면 0.46 $/kWh의 균등화 발전 비용을 가진다.
4.2 주요 인자 민감도 분석
스택 수명, 투자 비용, 운영 기간 그리고 연료비에 대한 항목을 가지고 민감도 분석을 수행하였다. Fig. 12는 각 형식에 따른 연료전지 균등화 발전비용의 민감도 분석을 나타낸다. 스택의 내구의 경우 기본 가정을 5년으로 하였으며, 2.5년과 10년의 두 경우를 추가하였다. 투자 비용의 경우 연료전지 발전 용량과 연간 생산량이 가지는 투자비용에서 ±20%의 경우를 고려하였다. 운영 기간의 경우 기본 가정을 20년으로 하였으며, 15년과 30년의 두 경우를 추가하였다. 연료 비용의 경우 국내 천연가스 가격인 14 $/GJLHV에서 ±20%의 경우를 고려하였다.
PEMFC에서는 1 kW의 시스템이 연간 100대 생산되는 경우, 25 kW의 시스템이 연간 50,000대 생산되는 경우, 그리고 50 kW의 시스템이 연간 50,000대 생산되는 경우를 계산하였다. 작은 용량, 적은 연간 생산량에서는 높은 장치 비용을 가지기 때문에 스택의 수명이 향상됨으로써 균등화 발전비용이 가장 크게 감소하였다. 스택의 수명이 감소하는 경우 높은 비용의 스택의 비용이 추가적으로 들어가기 때문에 가장 높은 균등화 발전비용을 나타내었다. 그 다음으로 영향을 받은 인자는 투자 비용으로 역시 높은 장치 비용으로부터 기인한다. 이 경우 연료비용에 대한 민감도가 낮았으며, 이는 장치 비용이 미치는 영향이 지배적이기 때문이다. 용량이 커지고, 연간 생산량이 증가함에 따라 장치 비용은 감소하게 되며, 이러한 영향을 결과에서도 볼 수 있다. 25 kW의 시스템이 연간 50,000대 생산되는 경우에도 스택의 수명이 가장 큰 민감도를 보이지만, 영향성은 앞선 조건에 비하여 많이 감소하였다. 연료비 및 운영 기간이 균등화 발전비용에 주는 영향이 커지면서 민감도가 증가하였다. 스택의 발전 용량이 250 kW로 더 증가하게 되면, 스택의 수명 다음으로 민감도를 주는 인자는 연료비가 된다. 결국 대량 생산으로 넘어가고 장치 비용이 감소하게 되면 대량 생산의 영향을 받지 않고 항상 같은 값을 가지는 연료비의 영향이 커지게 된다.
SOFC가 각 인자에서 보이는 경향도 매우 유사하다. 작은 용량 및 적은 연간 생산량에서는 스택의 수명이 가장 높은 민감도를 보이며, 스택의 수명이 2.5년이 될 경우 균등화 발전비용은 4.07 $/kWh까지 높아진다. SOFC에서도 용량이 증가함에 따라, 그리고 연간 생산량이 증가함에 따라 장치 비용이 감소하고 스택의 민감도 및 투자 비용의 민감도는 낮아지고, 연료비의 민감도는 증가하게 된다.
MCFC와 PAFC도 스택의 수명이 가장 민감한 인자로 도출되었으며, 또한, 높은 장치 비용으로 인하여 투자 비용이 스택 수명에 이은 민감한 인자로 도출되었다.
Table 8은 기본 조건에서의 균등화 발전비용과 가장 이상적인 조건을 가진 경우의 균등화 발전비용을 나타낸다. 1 kW 시스템이 연간 100대 생산되는 경우 2.64 $/kWh의 균등화 발전비용을 보이나, 스택 수명이 10년으로 증가, 투자 비용이 20% 감소, 운영 기간이 30년으로 증가, 연료 비용이 20% 감소하는 경우 1.47 $/kWh까지 감소할 수 있음을 나타낸다. 250 kW의 대용량 PEMFC가 연간 50,000대 생산되는 대량생산 상황에서는 0.19 $/kWh까지 균등화 발전비용을 낮출 수 있으며, SOFC의 경우 동일한 조건에서 0.18 $/kWh까지 낮출 수 있다.
5. 결 론
본 연구에서는 발전용 연료전지의 형식에 따른 균등화 발전비용을 분석하였다. PEMFC, SOFC, MCFC, PAFC에 대하여 균등화 발전비용을 계산하였다. PEMFC와 SOFC의 경우 각 세부 구성품들의 비용을 나눠 용량 및 연간 생산량 증가 시 구성품의 가격 저감의 영향을 반영하였으며 이를 통하여 용량과 연간 생산량에 따른 시스템 비용을 추산하였다. MCFC와 PAFC의 경우 제한적인 문헌 결과로 인하여 실증 기반의 전체 비용을 추산하였다.
각 용량과 연간 생산량에서의 균등화 발전비용을 계산하였으며, 스택 수명, 투자비, 프로젝트 기간 그리고 천연가스 비용에 대하여 민감도 분석을 수행하였다.
가정용 PEMFC의 경우 1 kW 용량의 시스템이 연간 100대 생산될 경우 kW 당 37,940 $의 비용이 예상되지만, 상업용으로 대형화되는 250 kW 용량이 연간 50,000대 생산될 경우 kW 당 1,531 $까지 줄일 수 있을 것으로 예측되며, 이 경우 균등화 발전 비용은 2.64 $/kWh에서 0.31 $/kWh로 줄어들게 된다.
가정용 SOFC의 경우 1 kW 용량의 시스템이 연간 100대 생산될 경우 kW 당 29,739 $의 비용이 예상되지만, 상업용으로 대형화되는 250 kW 용량이 연간 50,000대 생산될 경우 kW 당 1,057 $까지 줄일 수 있을 것으로 예측되며, 이 경우 균등화 발전비용은 2.43 $/kWh에서 0.28 $/kWh로 줄어든다.
연료전지의 경제성 확보를 위해서는 연료전지의 수명을 늘려 스택 교체 시 소요되는 비용을 감소시키는 것이 효율적일 것으로 판단된다.
Acknowledgments
본 연구는 산업통상자원부(MOTIE)와 한국에너지기술평가원(KETEP)의 지원을 받아 수행되었으며(No. 20203020040010), 한국기계연구원 기관 기본사업(Project ID: NK237G)의 지원을 받아 수행된 결과입니다.
References
-
G. Erdmann, “Future economics of the fuel cell housing market”, Int. J. Hydrogen Energy, Vol. 28, No. 7, 2003, pp. 685-694.
[https://doi.org/10.1016/S0360-3199(02)00281-1]
-
I. Staffell and R. J. Green. “Estimating future prices for stationary fuel cells with empirically derived experience curves”, Int. J. Hydrogen Energy, Vol. 34, No. 14, 2009, pp. 5617-5628.
[https://doi.org/10.1016/j.ijhydene.2009.05.075]
-
M. Naeini, J. S. Cotton, and T. A. Adams, “Economically optimal sizing and operation strategy for solid oxide fuel cells to effectively manage long-term degradation”, Ind. Eng. Chem. Res., Vol. 60, No. 47, 2021, pp. 17128-17142.
[https://doi.org/10.1021/acs.iecr.1c03146]
-
V. T. Giap, Y. D. Lee, Y. S. Kim, and K. Y. Ahn, “Techno-economic analysis of reversible solid oxide fuel cell system couple with waste steam”, Trans Korean Hydrogen New Energy Soc, Vol. 30, No. 1, 2019, pp. 21-28.
[https://doi.org/10.7316/KHNES.2019.30.1.21]
- S. Y. Hwang, M. J. Kim, J. H. Lee, and W. Y. Lee, “A simulation based study on the economical operating strategies for a residential fuel cell system”, Trans Korean Hydrogen New Energy Soc, Vol. 20, No. 2, 2009, pp. 104-115. Retrieved from https://koreascience.kr/article/JAKO200918133144995.pdf, .
-
B. Gim, “An economic analysis of domestic fuel cell vehicles considering subsidy and hydrogen price”, Trans Korean Hydrogen New Energy Soc, Vol. 26, No. 1, 2015, pp. 35-44.
[https://doi.org/10.7316/KHNES.2015.26.1.035]
- Battelle Memorial Institute, “Manufacturing cost analysis of PEM fuel cell systems for 5- and 10-kW backup power applications”, Energy.gov, 2016. Retrieved from https://www.energy.gov/sites/default/files/2016/12/f34/fcto_cost_analysis_pem_fc_5-10kw_backup_power_0.pdf, .
- Battelle Memorial Institute, “Manufacturing cost analysis of 100 and 250 kW fuel cell systems for primary power and combined heat and power applications”, Energy.gov, 2016. Retrieved from https://www.energy.gov/sites/default/files/2016/07/f33/fcto_battelle_mfg_cost_analysis_pp_chp_fc_systems.pdf, .
- Battelle Memorial Institute, “Manufacturing cost analysis of 1, 5, 10 and 25 kW polymer electrolyte membrane (PEM) fuel cell systems for material handling applications”, Energy.gov, 2017. Retrieved from https://www.energy.gov/eere/fuelcells/downloads/manufacturing-cost-analysis-1-5-10-and-25-kw-polymer-electrolyte-membrane, .
- Battelle Memorial Institute, “Manufacturing cost analysis of 1, 5, 10 and 25 kW fuel cell systems for primary power and combined heat and power applications”, Energy.gov, 2017. Retrieved from https://www.energy.gov/sites/default/files/2018/02/f49/fcto_battelle_mfg_cost_analysis_1%20_to_25kw_pp_chp_fc_systems_jan2017_0.pdf, .
- B. D. James, J. M. Huya-Kouadio, C. Houchins, and D. A. DeSantis, “Mass production cost estimation of direct H2 PEM fuel cell systems for transportation applications: 2018 update”, Energy.gov, 2018. Retrieved from https://www.energy.gov/sites/default/files/2020/02/f71/fcto-sa-2018-transportation-fuel-cell-cost-analysis-2.pdf, .
-
B. D. James, J. M. Huya-Kouadio, C. Houchins, and D. A. DeSantis, “Final report: mass production cost estimation of direct H2 PEM fuel cell systems for transportation applications (2012-2016)”, Energy.gov, 2016.
[https://doi.org/10.2172/1346414]
-
D. W. Hengeveld and S. T. Revankar, “Economic analysis of a combined heat and power molten carbonate fuel cell system”, Journal of Power Sources, Vol. 165, No. 1, 2007, pp. 300-306.
[https://doi.org/10.1016/j.jpowsour.2006.12.053]
-
R. Remick and D. Wheeler, “Molten carbonate and phosphoric acid stationary fuel cells: overview and gap analysis”, National Renewable Energy Laboratory, 2010.
[https://doi.org/10.2172/990108]
-
D. Steward, M. Penev, G. Saur, W. Becker, and J. Zuboy, “Fuel cell power model version 2: startup guide, system designs, and case studies. Modeling electricity, heat, and hydrogen generation from fuel cell-based distributed energy systems”, Office of Scientific and Technical Information, 2013.
[https://doi.org/10.2172/1087789]
- M. Lauterwasser, “Case studies in real estate development”, Becker + Becker, 2011. Retrieved from https://www.hydrogen.energy.gov/pdfs/htac_june2011_becker.pdf, .
- A. Bejan, G. Tsatsaronis, and M. J. Moran, “Thermal design and optimization”, John Wiley & Sons, USA, 1996.
- Lazard, “Lazard’s levelized cost of energy analysis—version 12.0”, Lazard, 2018. Retrieved from https://www.lazard.com/media/450773/lazards-levelized-cost-of-energy-version-120-vfinal.pdf, .
- Bloom Energy, “Petition of bloom energy corporation for a declaratory ruling for the location and construction of a 1350-kilowatt fuel cell customer side distributed resource at Southern Connecticut State University”, Vol. 21, No. 2, 2020. Retrieved from https://portal.ct.gov/-/media/CSC/3_Petitions-medialibrary/Petitions_MediaLibrary/MediaPetitionNos1401-1410/PE1407/PE1407-20200814-DCLTR.pdf, .
- V. Singh and J. Fehrs, “The work that goes into renewable energy”, Renew. Energy Policy Proj., 2001. Retrieved from https://globalurban.org/The_Work_that_Goes_into_Renewable_Energy.pdf, .