
수소발생용 Ni-Zn-Fe 합금 전극의 간헐적 작동에 따른 비활성화 특성
2020 The Korean Hydrogen and New Energy Society. All rights reserved.
Abstract
In this study, we investigated the deactivation characteristics of Ni-Zn-Fe electrodes due to intermittent operation in alkaline water electrolysis. To find suitable method to accelerate deactivation of electrode, the accelerated stress-test (AST) which repeated on/off step was performed with constant current/voltage control. The AST under constant voltage control is suitable to deactivate electrode so it were selected to investigate deactivation of electrode. The AST which repeated on/off step in range of –1.3 V and 0 V was performed and the relationship between oxidation current and electrode deactivation in the off step was investigate. As results, it was confirmed that the nickel and zinc on electrode surface were oxidized due to anodic current which occurred at off step.
Keywords:
Alkaline water electrolysis, Accelerated stress-test, Ni-Zn-Fe alloy, Deactivation키워드:
알칼리 수전해, 가속 스트레스 시험, 니켈-아연-철 합금, 비활성화1. 서 론
수소는 에너지원으로 사용하였을 때 공해물질이 거의 배출되지 않는 청정에너지이며 단위 중량당 에너지가 141.9 J/Kg으로, LPG와 LNG 등에 비해 무려 3배나 크다는 이점을 가진다1). 수소는 지구상에 풍부하게 존재하는 물로부터 생산될 수 있으며, 다양한 수소 생산 방법 중에서 물을 전기분해하여 수소를 제조하는 방법을 수전해라 한다. 수전해는 기술의 신뢰도와 성숙도가 가장 높고, 물을 직접 분해하여 수소를 생산하기 때문에 오염물질의 배출이 거의 없어 현재 많은 연구가 이뤄지고 있다2). 알칼리 수전해에 사용되는 전극의 재료로는 알칼리 용액에서 귀금속에 비해 저렴하고 높은 내식성을 가지는 니켈이 주목받고 있다. 이러한 니켈은 귀금속에 비해 활성이 낮기 때문에 다른 물질과의 합금 형태로 제조한다. 그중에서도 철(Fe)은 장기간의 수소발생반응에서 전극의 비활성화를 방지하는 역할을 한다고 알려진 바 있다3). 또한 선택적 침출을 통해 레이니 니켈(Raney Ni)을 제조하여 전극의 활성 표면적을 증가시키는 등의 방법이 있다. 이와 같이 Ni-Zn-Fe 전극을 제조하고 본 논문에서 수소발생반응을 위한 전극으로 사용하였다.
신재생에너지(태양광, 풍력)로부터 간헐적으로 생산되는 에너지를 수전해에 공급하여 수소의 형태로 에너지를 저장할 경우, 신재생에너지의 출력 변동성을 보완할 수 있다4). 그러나 알칼리 수전해는 신재생에너지로부터 불균일하게 전기에너지를 공급받게 되어 간헐적으로 작동하게 된다. 1990년대에 Divisek와 Hu 등은 Ni-Mo와 레이니 니켈(Raney Ni)과 같은 알칼리 수전해용 전극이 간헐적 작동 환경에서 전기화학적 활성을 상실하는 현상을 확인하였다5-8). 또한 Hu, Hall 및 Medway 등은 알칼리 수전해용 전극에 기계적 변형이 발생하였음을 확인하였다9-12). 이와 같이 신재생에너지로 인한 간헐적 작동 환경에서 우려되는 알칼리 수전해 전극의 비활성화에 대해 연구하고 이를 토대로 고내구성의 전극을 개발할 필요가 있다. 그러나 간헐적 작동에서 발생하는 전극의 비활성화에 대한 연구가 이뤄진 바가 적다.
따라서 본 연구에서는 알칼리 수전해를 간헐적 환경에서 작동시켰을 때 Ni-Zn-Fe 전극에 발생하는 비활성화 특성에 대해 알아보기 위해서 작동/정지 단계를 반복하는 가속 스트레스 시험을 실시하였다. 상온에서 전기전도성이 높은 25 wt% KOH 내에서 3-전극 시스템을 구성하고 정전류 및 정전압 제어의 비교를 통해 전극의 비활성화를 가속화하는 가속 스트레스 시험을 채택하였다. 이를 통하여 정전압 제어를 통한 가속 스트레스 시험의 정지 단계에서 발생하는 산화 전류가 아연의 침출 및 니켈의 산화를 발생시키며 비활성화 현상과 관계성을 고찰하였다.
2. 실 험
2.1 전극 제조
표면의 이물질 및 기름을 제거하고 활성화시키는 전처리 과정을 통하여 기판에 도금을 위한 전기도금이 원활히 진행할 수 있도록 한다. 전처리는 ‘탈지(degreasing)-산세척(pickling)-활성화(activation)-스트라이크(strike)’와 같은 4단계로 진행하였다. 먼저 탈지(degreasing)는 90℃, 30 wt%의 NaOH (97.0%, Junsei, Tokyo, Japan) 용액에 60초 동안 담지한 후 증류수로 세척을 하였고 산세척(pickling)은 25℃, HCl (20.0 wt%, Daejung, Siheung, Korea)에서 60초 동안 담근 뒤 증류수로 세척해주며 처리하였다. 활성화(activation)는 작동 전극과 상대 전극을 이용하는 2-전극 시스템으로 구성하여 H2SO4 (70.0 wt% Samchun, Pyeongtaek, Korea) 용액 내에서 108 mA/cm2의 전류밀도를 180초 동안 가하여 실시하였다. 스트라이크(strike) 과정을 통해 전극 표면에 얇은 니켈층을 도금하였다. 스트라이크(strike)는 Wood’s bath인 HCl (35.0 wt%, Samchun)와 NiCl2·6H2O (97.0%, Junsei)로 구성된 용액을 사용하여 –26.8 mA/cm2로 300초 동안 전기도금을 실시해주었다.
전기도금의 작동 전극은 전처리 과정을 거친 폼(foam) 형태의 니켈로 이루어진 기판(substrate)을, 상대 전극으로는 니켈을 사용하여 2-전극 시스템에서 실시되었다. Table 1의 조성으로 도금용액을 제조하여 50℃로 가열한 후에 작동 전극과 상대 전극을 넣고, potentiostat/galvanostat/impedance analyzer (ZIVE SP 2, Wonatech, Seoul, Korea)를 사용하여 80 mA/cm2로 전기도금을 실시하였다.
위에서 제조된 Ni-Zn-Fe 전극 표면의 아연을 알칼리성 용액과 반응시켜 침출시킬 수 있다. 제조된 전극에서 아연을 침출시키는 과정은 전극의 비표면적을 증가시켜 전극의 전기화학적 활성을 높게 한다. 이러한 아연 침출과정은 30 wt% KOH (95.0%, Daejung)와 10 wt%의 KNaC4H4O6·4H2O (potassium sodium tartrate tertrahydrate, 99.0%, Alfa Aesar, lancashire, England)를 혼합하여 80℃로 가열된 용액에 전극을 24시간 동안 담가 실시하였다. 위의 과정을 끝낸 후 제조된 전극의 표면은 니켈 수소화물(NiH2)을 형성하고 있기 때문에 공기 중에 노출 시 급격하게 반응을 하는 자연 발화성이 있다. 그러므로 급격한 반응을 방지하기 위해 여러 차례 전극을 증류수로 세척해준 뒤, 감압 챔버에 넣고 질소(N2) 기반의 혼합가스(1.6 vol% O2)를 주입하여 안정화를 시켜주었다.
2.2 물리화학적 분석
가속 스트레스 시험의 전/후에 따른 전극의 물리화학적 변화를 확인하기 위해 다음과 같은 분석을 실시하였다. 먼저 전극 표면의 형상 변화를 살피기 위해 scanning electron microscope (SEM; S-4800, Hitachi, Tokyo, Japan) 분석을 사용하였고 표면의 성분 변화를 비교하기 위해 energy dispersive spectrometer (EDS; X-MAX 50, Horiba, Tokyo, Japan)를 이용하였다. 또한 가속 스트레스 시험에 사용된 전해질 내 구성성분의 농도를 확인하기 위해 inductivity coupled plasma-optical emission spectrometer (ICP-OES; 5300DV, Perkin Elmer, California, USA) 분석을 실시하였다. 가속 스트레스 시험의 반복횟수에 따른 전극 표면의 결정 구조 변화를 확인하기 위해서 X-ray diffraction (XRD; Dmax-2500pc, Rigaku, Tokyo, Japan) 분석을 사용하였고 표면의 얇은 코팅층을 찍기 위하여 3°의 입사각에서 grazing incidence diffraction 분석을 하였다. XRD의 분석 조건은 CuKa (λ=1.5056 Å) 복사에너지를 사용하였고, 40 kV의 전압과 150 mA의 전류로 실시하였다.
2.3 전기화학적 분석
전기화학적 분석은 3-전극 시스템에서 실시되었으며 이는 작동 전극(working electrode), 상대 전극(counter electrode), 기준 전극(reference electrode)으로 구성되어 있다. 작동 전극은 제조한 Ni-Zn-Fe 전극을 사용하였고, 내경이 1.0 cm인 홀더에 전극을 배치하여 홀더의 면적을 수소발생반응에 노출되는 전극의 면적으로 판단하고 전류밀도를 계산하였다. 상대 전극은 니켈을, 기준 전극은 Hg/HgO (0.115 V vs. RHE)를 사용하였으며, 전해질은 25 wt% KOH를 제조한 뒤 25℃에서 실험을 진행하였다. 직류 전원 장치로는 potentiostat/galvanostat/impedance analyzer (ZIVE SP 2, Wonatech)를 사용하였다.
앞서 제조된 Ni-Zn-Fe 전극과 가속 스트레스 시험 후 전극의 특성을 전기화학 임피던스 분광법(electrochemical impedance spectroscopy, EIS), 선형주사전위법(linear sweep voltammetry, LSV), 순환전압전류법(cyclic voltammetry, CV)과 같은 방법을 통해 비교 분석하였다. 먼저 전기화학 임피던스 분광법을 통해 셀 구조의 용액저항을 계산할 수 있고 이러한 용액 저항의 결과값을 이용하여 선형주사전위법의 IR 보정에 사용하였다. 다음으로 가속 스트레스 시험 후에 전극의 수소발생반응 전기화학적 활성 변화를 비교하기 위해서 선형주사전위법이 –0.9 V에서 –1.5 V의 전압 범위에서 0.2 mV/s의 주사 속도(scan rate)로 실시되었다. 또한 순환전압전류 분석을 하여 매 10 cycle마다 작동 전압 범위 내에서 10 mV/s의 주사 속도(scan rate)로 총 80 cycle 실시하였다. 이를 통하여 수산화니켈(Ni[OH]2)의 형성을 확인하였다.
신재생에너지의 간헐적 작동 환경과 유사한 실험 환경을 조성하기 위하여 전극의 비활성화를 가속화하는 과정을 아래와 같은 작동/정지 단계를 반복하는 가속 스트레스 시험을 정전류/정전압 제어로 각각 실시하였다. 먼저 정전류/정전압 제어의 가속 스트레스 시험은 500 mL의 이중자켓에서 25 wt% KOH의 전해질을 사용하였다. 정전류 또는 정전압 제어의 가속 스트레스 시험의 작동조건이 Fig. 1와 Fig. 2에 각각 나타내었으며 이는 수전해를 5분간 작동시키는 작동 단계(on step)와 5분간 정지하는 정지 단계(off step)로 구성되어 있으며 150 cycle 동안 반복적으로 실시되었다. 정전류 제어의 가속 스트레스 시험의 경우에는 상업적 알칼리 수전해에서 사용하는 전류밀도가 약 200 mA로, 전극 비활성화를 가속화하기 위하여 그보다 2배가량 높은 400 mA를 기준으로 실시하였다. 정전압 제어의 가속 스트레스 시험의 경우에 선형주사전위법을 통해 얻은 –400 mA의 전압값인 약 -1.3 V를 작동 단계의 전압으로 설정하였으며 정지 단계(off step)는 0 V를 가해주었다. 또한 정지 단계에서 각 반복 횟수에서 발생하는 산화 전류량을 적산하였다.
3. 결과 및 고찰
3.1 정전류 제어의 가속 스트레스 시험
정전류 제어를 통해 작동/정지 단계를 반복하는 가속 스트레스 시험을 Fig. 3과 같이 실시하였다. 이를 통해 볼 수 있듯이 작동 단계에서 5분간 -400 mA을 가하면 약 –1.42 V의 환원 전압이 흐른다. 이후에 정지 단계에서 5분간 0 mA을 가하면 초반에는 약 –1.0 V가 흐르다가 점차 감소하여 약 –0.96 V로 유지된다. 이와 같은 작동/정지 단계를 150 cycle 반복한 결과를 Fig. 4에 나타내었다. 작동 단계 동안 동일한 전류가 가해지고 있음에도 작동 전압이 1st cycle에서 약 –1.422 V를 나타내다가 150th cycle에서 약 –1.416 V을 나타내며 최종적으로 작동 전압이 약 -6 mV 감소하였다. 정지 단계의 경우 150 cycle 반복 실시한 후에도 큰 변화 없이 약 –0.96 V를 띠는 것을 볼 수 있었다.

Enlarged graph of accelerated stress-test with constant current control for 150 cycle at 25°C in 25 wt% KOH

Full graph of accelerated stress-test with constant current control for 150 cycle at 25°C in 25 wt% KOH
작동/정지 단계를 150 cycle 반복하는 정전류 제어의 가속 스트레스 시험을 실시한 후에 전극의 전기화학적 활성 변화를 확인하기 위하여 선형주사전위법(Fig. 5)을 실시하였다. 동일한 전류밀도(-400 mA/cm2)에서 가속 스트레스 시험 후 전극의 과전압이 시험 전에 비해 약 -20 mV만큼 상승한 것을 알 수 있었다.
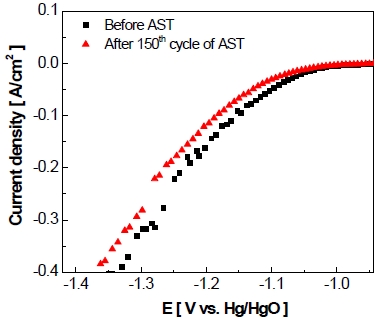
Cathodic potentiodynamic polarization recorded before and after accelerated stress-test with constant current control as scan rate of 0.2 mV/s
또한 가속 스트레스 시험 전과 후에 전극 표면 형상의 변화를 확인하기 위해 가속 스트레스 시험 전 후에 전극의 SEM 분석 결과를 Fig. 6에 나타내었다. 가속 스트레스 시험 전 전극의 표면 형상(Fig. 6[a], [b])의 경우 전극 제조 중 아연 침출 과정으로 인한 균열(crack)을 볼 수 있으며 시험 후에도 전극의 표면 형상에서 이와 큰 차이를 보이지 않았다(Fig. 6[c], [d]). 마찬가지로 가속 스트레스 시험 전과 후에 전극 표면의 조성 변화를 확인하기 위해 실시한 EDS 분석 결과를 Fig. 7에 나타내었다. 시험 전 전극의 경우 초기 조성이 니켈 63.7 at%와 아연 33.1 at%, 철 3.2 at%를 이루고 있었으며 가속 스트레스 시험 후 전극의 조성은 니켈 65.9 at%, 아연 30.5 at%, 철 3.64 at%로, 가속 스트레스 시험 전과 후에 큰 변화를 보이지 않았다.
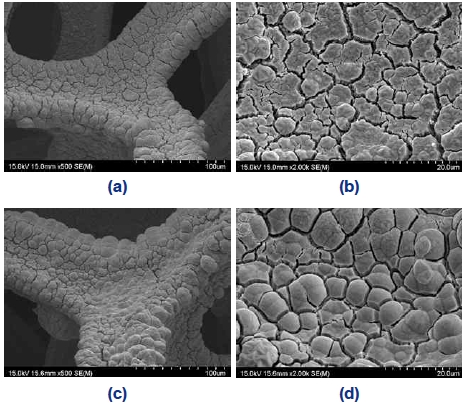
SEM image of the Ni-Zn-Fe electrode (a) before accelerated stress-test (AST) (×500 magnification), (b) before AST (×1,000 magnification), (c) after constant voltage control AST for 150 cycle (×500 magnification), (d) after constant voltage control AST for 150 cycle (×1,000 magnification)
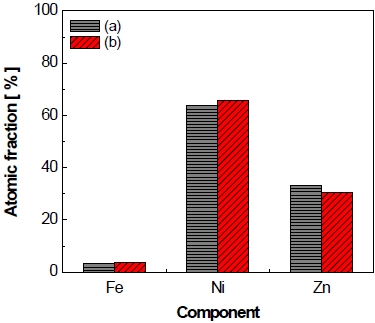
Comparison of the chemical composition quantification on electrode surface by EDS: (a) before accelerated stress-test (AST), (b) after constant current control AST for 150 cycle
정전류 제어를 이용한 가속 스트레스 시험에서 정지 단계의 작동 조건은 0 mA이기 때문에 전압이 두 전극 간의 전기적인 전위차인 개방 회로 전압(open circuit voltage)을 나타낸다. 정전압 제어를 이용한 가속 스트레스 시험에서 정지 단계의 전압을 0 V로 설정할 경우 전극의 비활성화를 더욱 가속화할 것으로 예상되기 때문에 정전압 제어의 가속 스트레스 시험을 실시하여 전극의 비활성화가 진행되는지 확인해보았다.
3.2 정전압 제어의 가속 스트레스 시험
전극의 비활성화를 가속화하기 위하여 정전압 제어로 가속 스트레스 시험을 실시하고 Fig. 8과 같이 나타내었다. Fig. 8을 통하여 볼 수 있듯이 작동 단계에서 5분간 –1.3 V를 가하면 약 6초 동안 비교적 큰 환원 전류가 흘렀다가 이내 곧 –400 mA/cm2를 유지한다. 이후에 정지 단계에서 5분간 0 V를 가하면 약 2분 동안 상당량의 산화 전류가 흐르다가 서서히 0 mA/cm2로 유지되는 것을 볼 수 있다. 이러한 작동/정지 단계를 150 cycle 동안 반복한 결과를 Fig. 9에 나타내었다. 작동 단계 동안 동일한 전압이 가해지고 있음에도 불구하고 1st cycle에서 작동 전류밀도가 약 –400 mA/cm2를 나타내다가 150th cycle에서 약 –200 mA/cm2를 나타내며 최종적으로 작동 전류밀도가 약 -200 mA/cm2만큼 감소하는 것을 알 수 있다. 정지 단계의 경우 반복횟수가 증가할수록 각 정지 단계의 초기에 발생하는 산화 전류의 spark 현상이 1st cycle에서 약 2.8 A까지 발생하였다가 이후에 150th cycle에서는 약 0.5 A까지 감소하였으며 1st cycle에 비해 약 2.3 A가 감소하였다.
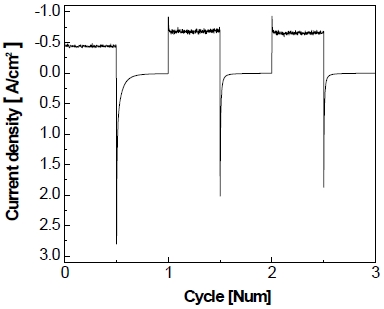
Enlarged graph of accelerated stress-test with constant voltage control for 150 cycle at 25℃ in 25 wt% KOH
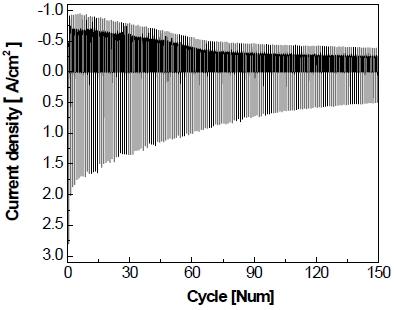
Full graph of accelerated stress-test with constant voltage control for 150 cycle at 25℃ in 25 wt% KOH
마찬가지로 정전압 제어의 가속 스트레스 시험 전과 후의 전극 전기화학적 활성 변화를 확인하기 위하여 선형주사전위법(Fig. 10)을 실시하였다. 동일한 전류밀도(-400 mA/cm2)에서 가속 스트레스 시험 후 전극의 과전압이 약 -183.7 mV만큼 상승한 것을 볼 수 있었다.
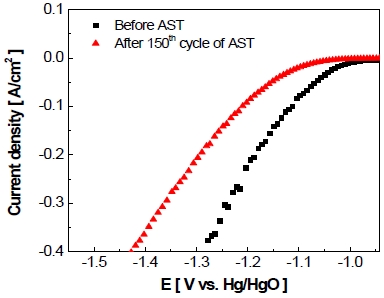
Cathodic potentiodynamic polarization recorded before and after accelerated stress-test with constant voltage control as scan rate of 0.2 mV/s
SEM과 EDS 분석을 통해 가속 스트레스 시험 전과 후에 전극 표면의 형상과 조성 변화를 확인하였으며 각각 Fig. 11과 Table 2에 나타내었다. 정전압 제어의 가속 스트레스 시험 후에 전극 표면은 시험 전 전극의 표면 형상(Fig. 6[a], [b])과 달리 전극 코팅층이 박리된 모습이 관찰되었으며, 가속 스트레스 시험 후 전극 표면 조성은 시험 전 전극에 비해 아연 성분이 약 19.1 at%만큼 상당량 감소한 것을 확인할 수 있었다. 여기서 EDS는 성분의 함량을 퍼센티지(percentage)로 나타내기 때문에 Table 2에 나타나는 니켈과 철 조성의 증가는 아연 성분의 감소로 인하여 발생한 것으로 사료된다.

SEM images of electrode surface after constant voltage control accelerated stress-test: (a) ×500 magnification, (b) ×1,000 magnification

Comparison of the chemical composition quantification on electrode surface of electrode before and after 150th cycle of test by EDS
이러한 결과를 보았을 때 정전압 제어의 가속 스트레스 시험의 경우 이전의 정전류 제어의 가속 스트레스 시험에 비해 전극의 전기화학적 활성이 상당량 감소한 결과를 보았을 때 비활성화가 더욱 가속화된 것으로 확인할 수 있다. 이는 앞서 언급하였던 정전압 제어의 가속 스트레스 시험에서 정지 단계의 작동 전압이 0 V이기 때문에 전극에 산화 전류가 흐르며, 결과적으로 전극의 비활성화가 더욱 가속화된 것을 확인하였다. 그러므로 정전압 제어의 가속 스트레스 시험이 전극을 비활성화 시키기에 적합하다고 판단하였다.
3.3 정전압 제어의 작동/정지 1st cycle 반복 후
앞서 말하였듯이 정전압 제어의 가속 스트레스 시험(Fig. 8)의 1st~2nd cycle 구간에서 특이한 점을 볼 수 있다. 작동/정지 단계 1st cycle에서 작동 전류밀도는 약 –400 mA/cm2를 나타내지만 2nd cycle에서 작동 전류밀도는 이보다 약 –200 mA/cm2만큼 높은 –600 mA/cm2를 나타낸다는 것이다. 그리고 2nd cycle부터 150th cycle까지 전극의 작동 전류밀도는 차츰 감소하는 경향을 보이며 이러한 특이점은 작동 단계에서 뿐만 아니라 정지 단계에서도 나타난다. 각 정지 단계의 초기에 흐르는 산화 전류의 spark 현상이 1st cycle에서 약 2.8 A/cm2까지 발생하였다가 2nd cycle에서는 약 2.0 A/cm2까지 발생하는 것을 볼 수 있다.
작동/정지 단계 1st cycle 후의 전극 전기화학적 활성 변화를 확인하기 위하여 실시한 선형주사전위법의 결과를 Fig. 12에 나타내었다. 동일한 전류밀도(-400 mA/cm2)에서 가속 스트레스 시험 전 전극의 전압은 -1.33 V, 작동/정지 단계 1st cycle 후 전극의 과전압이 약 -42 mV만큼 감소한 것을 보아 전극의 전기화학적 활성이 증가한 것을 볼 수 있었다.
전극의 전기화학적 활성이 상승한 원인을 알아보기 위해 EDS 분석을 실시하여 Table 3에 나타내었다. 그 결과, 작동/정지 단계 1st cycle 후 전극 표면에 존재하는 아연 성분의 조성은 약 23.6 at%로, 시험 전보다 약 9.5 at%만큼 감소한 것을 알 수 있다.

Comparison of the chemical composition quantification on electrode surface of electrode before and after 1st cycle of accelerated stress-test by EDS
가속 스트레스 시험 중 정지 단계에서 발생하는 산화 전류는 전극 표면의 아연을 산화시켜 표면으로부터 침출되도록 하며 침출된 아연 성분은 전해질에 존재하게 된다. Mainar 등13)의 연구에 의하면 pH 11 이상의 환경에서 아연의 산화로 인한 침출 화학반응식은 아래와 같다.
(1) |
(2) |
아연의 pH-전위도를 통해 아연이 산화되어 Zn(OH)3-와 Zn(OH)42-를 형성하는 것을 알 수 있다. 또한 Zn(OH)3-와 Zn(OH)42-는 수용액에서 가수분해되어 HZnO2- 또는 ZnO22-의 형태를 가지게 된다(Fig. 13). 약 pH 13 이상의 범위에서는 –1가 수산화아연(Zn[OH]3-)보다 –2가 수산화아연(Zn[OH]42-)의 형성이 지배적으로 일어난다13-15). 결과적으로 작동/정지 1st cycle 중, 정지 단계에서 발생하는 산화 전류로 인하여 식(2)와 같이 아연이 침출된 것으로 판단된다. 따라서 전극의 활성 표면적이 증가하고 이로 인하여 전극의 전기화학적 활성이 증가한 것으로 사료된다.
3.4 전극의 비활성화 특성
가속 스트레스 시험(Fig. 9)에서 2nd cycle 후 작동 전류밀도는 약 –600 mA/cm2까지 증가하며 이후에 약 50th~70th cycle에서 작동 전류밀도가 비교적 빠르게 감소하는 모습을 보이다가 이내 최종적으로 150 cycle 반복 후에 약 –200 mA/cm2까지 감소하는 것을 볼 수 있다. 작동 전류밀도가 빠르게 감소하는 구간을 찾기 위해 실험을 5 cycle 진행하였으며, 반복횟수 1 cycle당 전류밀도의 평균 변화율을 Fig. 14와 같이 나타내었다. In은 정전압 실험 시 현재의 전극 전류밀도이며, In-1은 정전압 실험 시 바로 이전의 전극 전류밀도를 나타낸다. Fig. 14를 보면 약 1st~2nd cycle 범위(Fig. 14[a])에서 전류밀도의 변화율이 가장 크며, 이는 첫 번째 정지 단계 중 아연 침출로 인한 전극 전기화학적 활성의 증가 때문에 발생한다. 이후에 2nd cycle의 작동 단계에서 최대 전류밀도를 보이지만 이내 바로 3rd cycle에서 급격히 감소하게 되며 이에 대한 변화율은 Fig. 14(b)로 나타난다. 1st~3rd cycle 범위를 제외하고 비교해 보았을 때, 약 50th~70th cycle 부근에서 전류밀도의 변화율이 가장 크게 나타나고 있으며 그중에서도 약 60th cycle에서 변화율이 가장 큰 부근으로 판단하였다. 따라서 Fig. 15와 같이 (a) 가속 스트레스 시험 전~1st cycle 구간과 전류밀도의 감소가 큰 60th cycle를 전/후로, (b) 2nd~60th cycle, (c) 60th~150th cycle 구간으로 나누어 가속 스트레스 시험의 정지 단계에서 발생하는 산화 전류와 전극의 비활성화를 연관지어 설명하였다.
많은 선행연구에 의하면 환원전극(cathode)의 급격한 산화는 전극의 비활성화를 야기하고 성능을 저하시킬 수 있다고 밝혀진 바 있다16-19). 실제로 가속 스트레스 시험 중, 작동 단계에서 환원 반응을 일으키던 전극이 정지 단계로 넘어갈 때 급격히 산화되기 때문에 전극의 비활성화와 직접적인 연관을 가질 것으로 사료된다.
작동 단계에서 정지 단계로 넘어갈 때 급격한 전압 변화(환원→산화)로 인하여 순간 최대의 산화 전류가 흐르고 시간이 지남에 따라 그 크기가 급격히 감소하는 현상을 보인다. 이때 흐르는 산화 전류는 전기 이중층 충전 전류(electric double-layer charging current)와 패러데이 전류(faradaic current)로 이루어져 있다. 전기 이중층 충전 전류는 반응물의 산화/환원을 위해 먼저 전기 이중층을 채우는 데 필요한 전류를 의미하며 충전 전류로 인하여 반응물 내 전자 에너지가 일정 수준을 넘어서게 되면 산화/환원 반응을 일으키게 된다. 이때 소요되는 전류를 패러데이 전류라 하고 즉, 정지 단계의 전압(0 V)이 인가될 때 산화반응을 위하여 전기 이중층 충전 전류가 흐르며 최대의 산화 전류가 흐르게 된다. 이와 같이 충전 전류가 흘러서 전자 에너지가 최고 점유 분자 궤도함수(highest occupied molecular orbital, HOMO)보다 낮아지면 산화 반응이 일어나게 되고 패러데이 전류가 흐르게 된다16). Fig. 8의 정지 단계에서 산화 전류로 인한 spark 현상은 전기화학반응에서 전기 이중층 충전 전류가 먼저 흐르기 때문에 발생하는 것으로 판단할 수 있다17). 전기 이중층은 전극 표면에 축적되는 전자 에너지로, 활성 표면적이 클수록 전기 이중층 충전 전류도 많이 필요하다. Fig. 9에서 볼 수 있듯이 첫 번째 정지 단계에서 spark 현상이 가장 크게 발생하며 이후 150th cycle까지 spark 현상이 점차 감소하는 것을 보아 활성 표면적이 서서히 감소하는 것으로 해석할 수 있다. 또한 전극의 활성 표면적 감소는 전기화학적 활성 감소에 영향을 주었을 것으로 판단된다17).
정지 단계에서 흐르는 산화 전류의 전하량을 수치적으로 비교해보기 위해서 정지 단계에서 0 A/cm2이상의 산화 전류밀도 범위(Fig. 16)를 다음의 식을 이용하여 적분 계산하였으며, 이에 대한 결과 그래프를 Fig. 17에 나타내었다. 이때 계산된 전하량은 전기 이중층 충전 전류(iC)와 패러데이 전류(if) 모두를 적분한 값이다16).
(3) |
가속 스트레스 시험의 첫 번째 정지 단계에서의 전하량이 약 0.059 C/cm2로 가장 크게 발생하며 이후 계속하여 감소하다가 최종적으로 150th cycle에서 약 0.0024 C/cm2만큼 전하량이 흐른 것을 알 수 있으며, 이는 첫 번째 정지 단계의 전하량에 비해 약 96%만큼 감소한 값으로, 150th cycle의 산화 전류는 상당량 감소하는 것으로 판단할 수 있다.
이와 같이 정지 단계에서 발생하는 산화 전류가 전극에 어떤 영향을 주어 비활성화를 발생시키는지 알아보기 위해 다양한 분석을 실시하였다.
반복 횟수에 따른 전극 표면의 조성 변화의 결과를 Fig. 18에 나타내었고 조성을 비교한 결과, 가속 스트레스 시험 전 전극에 비해 작동/정지 단계 1st cycle 후에는 아연 성분이 약 9.5 at%만큼 감소하였으며 2nd cycle부터 약 60th cycle까지 아연 성분이 비교적 점진적으로 감소하는 경향을 나타내는 것을 볼 수 있다.
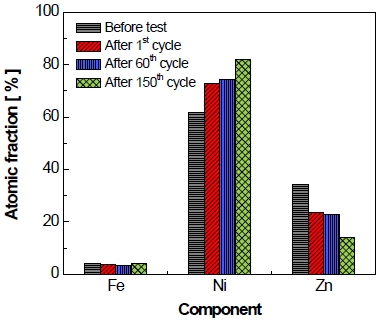
Comparison of the chemical composition quantification on electrode surface of electrode before and after 1st, 60th and 150th cycle of test by EDS
정전압 제어의 가속 스트레스 시험의 작동 범위에서 전극의 산화 과정을 살피기 위해 순환전압전류법을 실시하였다. 순환전압전류법은 작동/정지 단계를 10 cycle 반복할 때마다 가속스트레스의 작동 범위인 –1.3~0 V에서 실시되었고 Fig. 19에 결과를 나타내었으며 전극의 산화 과정에서 니켈이 산화되는 피크가 발견되었다11). 반응식은 다음과 같다.
(4) |
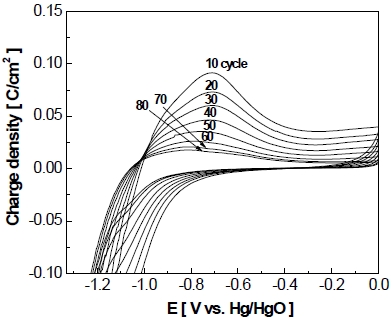
Results of cyclic voltammetry performed every 10 cycle of accelerated stress-test in the operating voltage range (-1.3 V~0 V vs. Hg/HgO)
순환전압전류법의 결과를 보면 알 수 있듯이 작동/정지 단계의 반복횟수가 증가할수록 니켈 산화 피크가 점차 감소하는 경향을 보인다. 이는 작동/정지 단계의 초기에는 전극 표면에 산화될 수 있는 니켈의 양이 많았으나 수산화니켈의 양이 증가하고 기존의 니켈의 양이 감소하였기 때문으로 사료된다.
니켈 Pourbaix diagram (Fig. 20)에 따르면 25 wt% KOH (약 pH 15)의 전해질에서 정지 단계의 전압(0 V)을 가해줄 경우 니켈은 수산화니켈(Ni[OH]2)을 형성한다18). 즉, 정지 단계의 전압에서 니켈은 산화 전류로 인하여 수산화니켈(Ni[OH]2)을 형성할 것으로 예상되며, 수산화니켈(Ni[OH]2)의 경우 전극의 세척 및 건조 과정 중에 쉽게 산화니켈(NiO)의 형태로 변화하기 때문에 결과적으로 전극 표면에 산화니켈(NiO)이 나타날 것으로 사료된다19,20).
산화니켈의 형성을 정확하게 확인하기 위하여 XRD 분석을 통해 반복 횟수에 따른 전극 표면의 결정 구조 변화를 나타내는 XRD 패턴을 Fig. 21에 나타내었다. XRD 분석 결과를 통해 전극 표면의 결정 구조 변화를 확인하였으며 분석에 사용된 피크는 선행연구에서 확인된 결과와, joint committee on powder diffraction standards (JCPDS) 카드(Ni: JCPDS no. 04-085021), NiO: JCPDS no. 75-042922) 등)의 데이터를 통해 해당 결정 구조를 나타내었다. 먼저 45°, 52° 그리고 76°에서 보이는 피크는 전극의 기판(substrate)으로 사용된 니켈의 결정 구조를 나타내는 피크이며, 다음으로 37°, 43° 및 63°에서 보이는 피크는 산화니켈(NiO)의 결정 구조를 나타내는 피크이다.
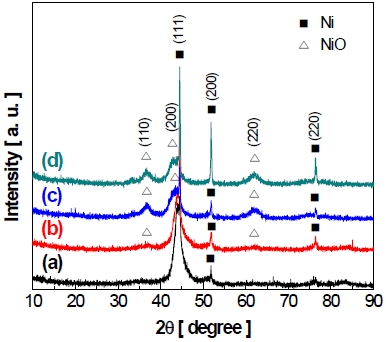
XRD pattern of Ni-Zn-Fe electrode surface: (a) before accelerated stress-test, (b) after 1st cycle, (c) after 60th cycle and (d) after 150th cycle of accelerated stress-test
Fig. 21에서 작동/정지 단계의 반복횟수가 증가할수록 전극 표면의 결정 구조가 변화하는 모습을 보인다. 시험 전 전극의 XRD 피크와 비교하였을 때, 작동/정지 단계의 1st cycle 후에 산화니켈(NiO)의 피크인 37° (111)와 63° (220)이 비교적 낮은 강도로 증가하였다. 이후에도 마찬가지로 약 60th cycle까지 산화니켈(NiO) 피크인 37° (110)와 63° (220)의 강도가 증가하며 타 피크와 겹쳐있던 43° (200)의 피크가 확인되었으며, 결과적으로 전극 표면에서 산화니켈이 형성된 것을 알 수 있었다. 기존의 니켈은 P형 반도체로, 공유 결합하는 전자가 총 7개이며 부족한 하나의 전자를 이웃한 전자들로 메우기 때문에 전도성이 높으나 산화니켈(NiO)은 니켈 격자 내에서 3가 니켈(Ni3+) 대신 산소를 포함하고 있는 분자이기 때문에 기존의 니켈보다 낮은 전도성을 가진다19,23,24). 이러한 산화니켈(NiO)의 형성은 전극의 전기화학적 활성을 감소시키는 원인 중 하나로 판단된다25).
60th~150th cycle 구간(c)에서 Fig. 19와 Fig. 21을 통해 나타나는 변화를 보았을 때, 먼저 Fig. 19에서 볼 수 있듯이 약 60th cycle 이후에 니켈의 산화 피크가 거의 발견되지 않는 것을 알 수 있다. 다음으로 Fig. 21에서 나타난 전극 표면의 결정 구조를 통하여 산화니켈(NiO)의 피크 강도에 큰 변화가 나타나지 않는 것을 보아, 결과적으로 가속 스트레스 시험 중 약 60th cycle까지 산화니켈이 형성되며 이후에는 전극 표면중 대부분의 니켈이 산화된 것으로 해석된다. 또한 가속 스트레스 시험의 150 cycle 후에 니켈(Ni)의 피크인 45° (111), 52° (200) 그리고 76° (220)의 강도(intensity)가 이전의 XRD 패턴들에 비해 증가하는 것을 볼 수 있다. 이는 가속 스트레스 시험 후 전극 표면에서 확인되었던(Fig. 11) 코팅층 박리로 인하여 전극의 기판인 니켈이 표면으로 노출되어 피크 강도가 증가한 것으로 사료된다.
Fig. 18을 보면 알 수 있듯이, 가속 스트레스 시험 전 전극에 비해 작동/정지 단계 1st cycle 후에 아연의 1차적 감소는 앞에서 설명하였으며, 이후에 약 60th cycle까지 아연 성분이 비교적 점진적으로 감소하는 경향을 나타낸다. 그러나 약 60th cycle부터 150th cycle까지 아연이 다시 급격하게 8.7 at%만큼 감소하며 시험 전 전극에 비해 약 19.1 at%만큼 감소한 것을 볼 수 있다.
실제로 아연의 감소가 침출로 인한 것인지 확인하기 위하여 ICP-OES 분석을 통해 전해질에 존재하는 아연의 농도를 확인하였으며 결과를 Table 4에 나타내었다. 검출 한계로 인하여 니켈과 철 성분의 농도는 확인되지 않으며, 아연의 경우 가속 스트레스 시험의 반복 횟수에 따라 농도가 변화하는 것을 확인할 수 있다. EDS와 ICP-OES의 분석 결과를 반복 횟수에 따른 전극 표면의 아연 조성 변화와 전해질 내의 아연 농도 변화로 Fig. 22에 함께 나타내었다. 작동/정지 단계 1st cycle 후에 전해질 내의 아연 농도가 약 10 mg/L만큼 증가하였다. 그리고 2nd cycle부터 약 60th cycle까지 아연의 농도가 서서히 증가하다가 이내 60th cycle 이후에 다시 아연의 농도가 증가하며 최종적으로 25 wt% KOH에 비해 약 15 mg/L만큼 증가하였다. 전해질 내 아연의 농도는 Fig. 18에서 살펴보았던 전극 표면의 조성 변화와 반대로 증가하는 추세를 보이며 이는 전극 표면의 아연 성분이 전해질로 침출되기 때문으로 사료된다. 결과적으로 니켈의 산화 피크 및 전극 표면의 결정구조와 전극 표면에서 니켈이 대부분 산화되어 아연이 60th~150th cycle 구간(c)에서 2차적으로 침출된 것으로 판단된다.
다음의 결과들을 통해 Fig. 15에 나타난 (a), (b), (c)의 구간에 따라 정지 단계에서 발생하는 산화 전류가 전극의 비활성화에 주는 영향을 설명하였다. Fig. 17을 통해 가속 스트레스 시험의 첫 번째 정지 단계에서 산화 전류가 가장 크게 흐르는 것을 확인하였으며 이러한 산화 전류로 인해 시험 전~1st cycle 구간(a)에서 전극 표면으로부터 아연 조성이 1차적으로 감소하였다(Table 3). 이후에 2nd~60th cycle 구간(b)에서 발생하는 산화 전류는 니켈을 산화시켜 전극 표면에 산화니켈(NiO)을 형성하고(Fig. 21), 이러한 현상은 아연 성분의 침출 반응보다 지배적으로 일어난다. 전극 표면에서 대부분의 니켈이 산화된 60th~150th cycle 구간(c)에서는 전극 표면으로부터 아연이 2차적으로 감소하고 이는 전해질로 침출되었음이 확인되었다(Fig. 22). 그러므로 정지 단계에서 발생하는 산화 전류는 전극 표면을 산화시켜 촉매 활성점을 감소시키고 이로 인해 전극의 비활성화가 발생한 것을 알 수 있다.
Fig. 11을 통해 정전압 제어 가속 스트레스 시험 후에 발생하는 전극 코팅층의 박리현상을 보여준 바 있다. 전극 코팅층의 박리는 전극이 가지고 있던 촉매 활성 물질들을 손실시키기 때문에 전극의 전기화학적 활성 감소를 야기하는 현상 중 하나로 사료된다. 전극의 단면을 선주사(line scanning) 분석하여 Fig. 23에 나타내었다. Fig. 23에서 니켈과 철, 아연의 농도에 따라 전극의 기판과 코팅층의 구분이 가능하다. 먼저 ①은 전극의 기판이고, 다음으로 ②는 전기도금을 통해 얻은 코팅층이며, 이를 통해 실제 전극의 코팅층이 어떤 형상으로 비활성화 되었는지 확인이 가능하다. 그 결과 가속 스트레스 시험 전 전극에 비해 코팅층 간 거리가 벌어진 것을 확인할 수 있었다.
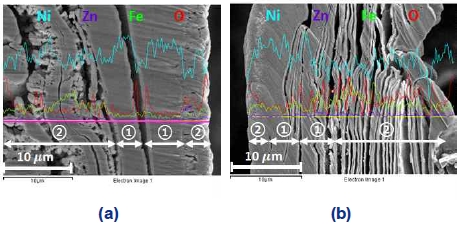
Line scan analysis of cross section of electrode treated with ion milling: (a) before accelerated stress-test (AST), (b) after 150th cycle of AST (① substrate, ② coating layer)
작동/정지 단계를 반복하는 정전압 제어의 가속 스트레스 시험에서 전극 표면의 니켈은 작동 단계(-1.3 V)의 환원 전류에서 니켈 수소화물(NiHx)을 형성하게 된다. 이후에 전극 표면의 니켈 수소화물은 정지 단계의 산화 전류에서 수산화니켈(Ni[OH]2)을 형성한다. 니켈과 수소만을 포함하는 니켈 수소화물(NiHx)과 달리 수산화니켈(Ni[OH]2)는 산소 원자를 포함하고 있기 때문에 비교적 격자(lattice)의 크기가 크다. 작동 단계 중에 형성된 니켈 수소화물(NiHx)이 정지 단계에서 수산화니켈(Ni[OH]2)의 형태로 변화하게 되면서 격자가 팽창하며, 반대로 정지 단계에서 수산화니켈(Ni[OH]2)이 니켈 수소화물(NiHx)의 형태로 변화할 때 격자가 다시 수축하게 된다9). 이와 같은 니켈 화합물에 따른 격자 구조의 팽창 및 수축은 선행연구에서 이미 밝혀진 현상이다. 또한 David 등에 의하면 격자의 팽창 및 수축이 반복적으로 발생할 경우 전극 표면에 기계적 변형이 발생하여 전극 표면을 손상 또는 파괴시킬 수 있다고 연구한 바 있다10-12,26). 즉 작동/정지 단계를 실행하는 과정에서 니켈 수소화물(NiHx)과 수산화니켈(Ni[OH]2) 간의 반복적인 변화는 니켈 격자 구조의 팽창과 수축을 반복적으로 일으키고 그로 인하여 코팅층의 기계적 변형이 발생하며 이와 같은 박리현상이 발생하였을 것으로 판단된다11,12). 뿐만 아니라 제조된 전극의 단면에 비해 가속 스트레스 시험 후 전극의 단면에서 비교적 층간 거리가 넓어진 것을 보아 팽창 및 수축의 반복은 코팅층의 층상구조를 Fig. 23(b)에서 보이는 것처럼 벌어지게 만들었을 것이라 판단된다.
4. 결 론
본 연구에서는 알칼리 수전해 시 작동과 정지를 반복하여 Ni-Zn-Fe 전극의 비활성화를 가속화하는 가속 스트레스 시험을 실시하였다.
1) 정전류와 정전압 제어의 가속 스트레스 시험을 각각 실시한 결과, 정전압 제어의 가속 스트레스 시험이 전극의 비활성화를 가속화하기 위한 방법으로 적합하다고 판단하였다.
2) 정전압 제어의 가속 스트레스 시험 결과에서 작동/정지 단계 1st cycle 후에 전극 표면의 아연이 침출되고 활성 표면적이 증가하여 전극의 전기화학적 활성이 증가한 것으로 판단된다.
3) 2nd~60th cycle 구간에서 니켈의 산화가 지배적으로 발생하며 아연의 침출이 점진적으로 발생하였다.
4) 60th~150th cycle 구간에서 전극 표면 중 대부분의 니켈이 산화되어 아연의 2차적 침출이 지배적으로 진행된 것으로 확인되었다.
5) 작동/정지 단계를 반복하는 과정에서 니켈의 격자가 수축 및 팽창을 반복하고 기계적 변형이 발생하여 전극의 코팅층이 박리된 것으로 판단된다.
Acknowledgments
본 연구는 2019년도 지식경제부 재원으로 한국에너지 기술평가원(KETEP)의 지원을 받아 수행한 연구 과제이다(No. 20173030041350).
References
-
T. N. Veziroglu and S. N. Sahın, “21st century’s energy: hydrogen energy system”, Energy Conv. Manag., Vol. 49, No. 7, 2008, pp. 1820-1831.
[https://doi.org/10.1016/j.enconman.2007.08.015]
- T. H. Lee, “Water electrolyzer technical overview and outlook”, J. of the Electric World, Vol. 459, 2015, pp. 14-17. Retrieved from http://www.kea.kr/elec_journal/2015_3/2.pdf, .
-
A. E. Mauer, D. W. Kirk, and S. J. Thorpe, “The role of iron in the prevention of nickel electrode deactivation in alkaline electrolysis”, Electrochim. Acta, Vol. 52, No. 11, 2007, pp. 3505-3509.
[https://doi.org/10.1016/j.electacta.2006.10.037]
- H. C. Lim, “Use of hydrogen energy for power storage & outlook”, J. of Electrical World, Vol. 465, 2015, pp. 35-41. Retrieved from http://www.kea.kr/elec_journal/2015_9/6.pdf, .
-
J. Divisek, H. Schmitz, and J. Balej, “Ni and Mo coatings as hydrogen cathodes”, J. Appl. Electrochem., Vol. 19, No. 4, 1989, pp. 519-530.
[https://doi.org/10.1007/BF01022108]
-
J. Divisek, J. Mergel, and H. Schmitz, “Advanced water electrolysis and catalyst stability under discontinuous operation”, Int. J. Hydrogen Energy, Vol. 15, No. 2, 1990, pp. 105-114.
[https://doi.org/10.1016/0360-3199(90)90032-T]
-
J. Divisek, H. Schmitz, and B. Steffen, “Electrocatalyst materials for hydrogen evolution”, Electrochem. Acta., Vol. 39, No. 11-12, 1994, pp. 1723-1731.
[https://doi.org/10.1016/0013-4686(94)85157-3]
-
W. Hu, “Electrocatalytic properties of new electrocatalysts for hydrogen evolution in alkaline water electrolysis”, Int. J. Hydrogen Energy, Vol. 25, No. 2, 2000, pp. 111-118.
[https://doi.org/10.1016/S0360-3199(99)00024-5]
-
Y. Hu and D. A. Scherson, “Potential-induced plastic deformations of nickel hydrous electrodes in alkaline electrolytes: an in situ atomic force microscopy study”, J. Phys. Chem., Vol. 101, No. 27, 1997, pp, 5370-5376.
[https://doi.org/10.1021/jp970399m]
-
D. S. Hall, C. Bock and B. R. MacDougall, “Surface layers in alkaline media: nickel hydrides on metallic nickel electrodes”, ECS Transactions, Vol. 50, No. 31, 2013, pp. 165-179.
[https://doi.org/10.1149/05031.0165ecst]
-
D. S. Hall, C. Bock and B. R. MacDougall, “The electrochemistry of metallic nickel: oxides, hydroxides, hydrides and alkaline hydrogen evolution”, J. Electrochem. Soc., Vol. 160, No. 3, 2013, pp. 235-243.
[https://doi.org/10.1149/2.026303jes]
-
S. L. Medway, C. A. Lucas, A. Kowal, R. J. Nichols, and D. Johnson, “In situ studies of the oxidation of nickel electrodes in alkaline solution”, J. Electroanal. Chem., Vol. 587, No. 1, 2006, pp. 172-181.
[https://doi.org/10.1016/j.jelechem.2005.11.013]
-
A. R. Mainar, O. Leonet, M. Bengoechea, I. Boyano, I. de Meatza, A. Kvasha, A. Guerfi, and J. A. Blázquez, “Alkaline aqueous electrolytes for secondary zinc–air batteries: an overview”, Int. J. Energy Res., Vol. 40, 2016, pp. 1032-1049.
[https://doi.org/10.1002/er.3499]
-
A. R. Mainar, L. C. Colmenares, J. A. Blázquez, and I. Urdampilleta, “A brief overview of secondary zinc anode development: the key of improving zinc‐based energy storage systems”, J. Energy Res., Vol. 42, No. 3, 2018, pp. 903-918.
[https://doi.org/10.1002/er.3822]
-
A. Khor, P. Leung, M. R. Mohamed, C. Flox, Q. Xu, L. An, R. G. A. Wills, J. R. Morante, and A. A. Shah, “Review of zinc-based hybrid flow batteries: from fundamentals to applications”, Material Today Energy, Vol. 8, 2018, pp. 80-108.
[https://doi.org/10.1016/j.mtener.2017.12.012]
- S. M. Oh, “Electrochemistry”, 2nd ed. Free Academy, Korea, 2014, pp. 1-26, 145-164.
-
D. Chade, L. Berlouis, D. Infield, P. T. Nielsen, and T. Mathiesen, “Deactivation mechanisms of atmospheric plasma spraying raney nickel electrodes”, J. Electrochem. Soc., Vol. 163, No. 3, 2016, pp. 308-317.
[https://doi.org/10.1149/2.0091605jes]
-
L. F. Huang, M. J. Hutchison, R. J. Santucci, J. R. Scully, and J. M. Rondinelli, “Improved electrochemical phase diagrams from theory and experiment: the Ni−water system and its complex compounds”, J. Phys. Chem., Vol. 121, No. 18, 2017, pp. 9782-9789.
[https://doi.org/10.1021/acs.jpcc.7b02771]
-
C. Li and S. Liu, “Preparation and characterization of Ni(OH)2 and NiO mesoporous nanosheets, J. Nanomaterials”, Vol. 2012, 2012, pp. 1-6.
[https://doi.org/10.1155/2012/648012]
-
M. Cao, X. He, J. Chen, and C. Hu, “Self-assembled nickel hydroxide three-dimensional nanostructures: a nanomaterial for alkaline rechargeable batteries”, Crystal Growth & Design, Vol. 7, No. 1, 2007, pp. 170-174.
[https://doi.org/10.1021/cg060524w]
-
J. Tientong, S. Garcia, C. R. thurber, and T. D. Golden, “Synthesis of nickel and nickel hydroxide nanopowders by simplified chemical reduction”, J. Nano., Vol. 2014, 2014, pp. 1-6.
[https://doi.org/10.1155/2014/193162]
- K. AL-Rashedi, M. Farooqui, and G. Rabbani, “Nickel oxide thin film synthesis by sol-gel method on glass substrates”, Int. J. of Universal Print, Vol. 4, No. 8, 2018, pp. 508-516. Retrieved from http://www.universalprint.org/wp-content/uploads/2018/03/ACTRA-2018-078.pdf, .
-
C. C. Hu and H. Teng, “Structural features of p-type semiconducting NiO as a co-catalyst for photocatalytic water splitting”, J. Catal., Vol. 272, No. 1, 2010, pp. 1-8.
[https://doi.org/10.1016/j.jcat.2010.03.020]
-
D. Jia, Q. Ren, L. Sheng, F. Li, G. Xie, and Y. Miao, “Preparation and characterization of multifunctional polypyrrole–Au coated NiO nanocomposites and study of their electrocatalysis toward several important bio-thiols”, Sens. Actuators B Chem., Vol. 160, No. 1, 2011, pp. 168-173.
[https://doi.org/10.1016/j.snb.2011.07.028]
-
F. Safizadeh, E. Ghali, and G. Houlachi, “Electrocatalysis developments for hydrogen evolution reaction in alkaline solutions – a review”, Int. J. Hydrogen Energy, Vol. 40, No. 1, 2015, pp. 256-274.
[https://doi.org/10.1016/j.ijhydene.2014.10.109]
-
Y. Xiao, Y. Liu, Z. Tang, L. Wu, Y. Zeng, Y. Xu, and Y. He, “Porous Ni–Cr–Fe alloys as cathode materials for the hydrogen evolution reaction”, RSC Advances, Vol. 6, No. 56, 2016, pp. 51096-51105.
[https://doi.org/10.1039/C6RA07316F]