
API X70강 배관 모재부의 수소 손상에 관한 연구
2020 The Korean Hydrogen and New Energy Society. All rights reserved.
Abstract
In this study, hydrogen charging was conducted for API X70 steel by the electro-chemical hydrogen charging method. Right after hydrogen was diffused from the specimen surface to the inside of the X70, the small punch tests and hydrogen concentration analysis was conducted within 5 minutes. Hydrogen was analyzed by melting the whole specimen and detect the gas after melting. Mechanical properties were measured by the small punch (SP) testing. Fracture surface and specimen surface were observed using scanning electron microscope. Three tests were repeated for study sensitivity of the SP test results under a same charging condition. It was observed that the variation of the maximum load, SP displacement at failure, hydrogen concentration as the charging period was not much in the case of X70 as the other steel such as Inconel. It can be argued that X70 base metal may have high hydrogen damage resistance and hydrogen diffusion in the base metal would not cause much embrittlement. Limitations of the SP test with 0.5 mm thickness for hydrogen damage test for X70 were discussed.
Keywords:
Electrochemical hydrogen charging, Small punch test, Hydrogen damage, Strength, X70키워드:
전기화학적 수소 장입, 소형 펀치 시험, 수소 손상, 재료강도1. 서 론
수소는 금속재료에 확산 침투되는 경우 재료의 연성 및 인성을 감소1)시키므로, 저장 및 운송 시 설비의 구조건전성을 확보해야 한다. 수소 누출 시는 가연범위가 넓고 폭발력이 커서 에너지 캐리어로 사용하기 위해서는 안전한 사용에 대한 기술적 이해가 필연적이다. 국내 뿐 아니라 미국, 일본, 독일 등에서 금속 재료의 수소 손상 및 수소 취화와 관련하여 활발한 연구가 진행되고 있다. 또한 대규모의 수소를 공급하기 위한 방안으로 기존의 천연가스 배관망을 이용한 수소 및 혼합 수소-천연가스 배송 배관 기술에 관한 연구가 진행되고 있다2). DOE Hydrogen Program에 따르면 천연가스 배관망을 사용하여 수소 및 혼합 수소-천연가스를 공급하고자 할 때 가장 큰 장애물이 수소 누출(hydrogen leakage)과 더불어 재료의 수소 손상(hydrogen damage)이라 여겨지고 있다3).
일반 천연가스 배송 시스템에서 배관의 건전성 및 사용적합성(fitness-for-service, FFS) 평가는 주로 API 579 코드 기준을 따라 수행되지만, 수소가스 배송시스템에서의 배관에 대한 수소 손상 사용 적합성 평가 절차나 기준 코드는 개발되어 있지 않다. 수소 영향에 대한 건전성 평가 연구 결과를 보면 배관 용접부와 불연속점이 수소 손상에 취약한 것으로 보고되었다. 결국 천연가스 배관망을 수소 공급을 위해 사용할 경우, 수소 손상 및 재료의 취화는 필연적으로 발생하게 될 가능성이 있으므로 배관망의 안전을 확보하기 위해서는 어떤 수준까지 수소량을 또는 수소손상을 허용할 수 있는지 판단해야 한다.
본 연구에서는 수소 공급 인프라로 사용을 고려하고 있는 천연가스 배관망의 건전성 평가에 필요한 기초물성 데이터를 얻고자 연구하였다. 이를 위해 전기화학적 습식 장입을 통해 천연가스 배관망으로 쓰이는 X70강 모재부의 표면에서 확산에 의해 금속 내부로 수소를 장입시킨 시험편을 사용하여 소형펀치시험(small punch test, SP test)과 수소 농도 분석을 진행하였다1-8). 재료에 확산된 수소량을 측정하기 위해 시편 용융에 의한 수소 농도 분석기를 이용하여 정량적으로 수소 농도를 분석하였으며, SP 시험을 통해 파단이 일어난 시험편은 주사전자현미경(scanning electron microscope, SEM)으로 관찰하였다.
2. 실 험
2.1 재료 및 시험편
본 연구에 사용된 재료는 배관 재료인 API X70 강의 모재부이며, 재료의 화학적 조성은 Table 1과 같다. 천연가스 배관은 지하에 매설되기 때문에 지반침하 등의 변형에 저항성을 갖도록 설계되어야 하므로 저탄소강을 사용한다. 화학적 조성을 확인한 결과 기계적인 강도에 좋지 못한 영향을 주는 황(S)과 인(P)의 함유량이 적어 양호한 재료임을 알 수 있다9).
본 연구에서 수행하고자 하는 실험 연구는 수소 농도 분석과 소형펀치시험에 의한 재료강도 측정이다. 따라서 시험편은 Fig. 1과 같이 수소 농도 분석과 소형펀치시험 둘 다에 활용 가능한 크기인 10×10×0.5 mm인 사각형 얇은 판형 시편이 사용되었다. 또한, 전기화학적 습식장입법을 통한 수소장입을 용이하기 위해 시험편의 음극에 리드(lead)부를 남겨 가공하였으며, 수소장입 직후 해당 부분을 제거하고 SP시험 또는 농도 측정 실험을 진행하였다. 표면조도에 대한 효과를 최소화하고 시험편 두께에 대한 영향을 줄이고자 시험편의 전면에 걸쳐 600 grit으로 표면 연마하였으며, 0.5±0.005 mm의 균일한 두께를 갖도록 하였다.
2.2 실험 방법
금속재료 내부로 수소를 침투시키기 위해 분극시험법(electrochemical polarization method)을 활용하여 자연전위 이하의 전위를 유지할 수 있도록 구성하였고, 음극반응을 인위적으로 조절하여 재료 표면에 수소를 발생시켰다.
전기분극법10)을 사용하여 금속 시험편에 수소를 발생시키기 위해 0.5 M H2SO4 수용액을 사용하였다. H2SO4 수용액 환경 하에서 음극에 시험편을 장착하여 수소가 발생하게 하였고, 양극에 백금선(Pt wire)을 장착하여 분극 셀을 구성하였다. 상온 환경과 전류밀도 100 mA/cm2의 정전류 조건에서 전기 분극 시험을 실시하였으며, 정전류 조건을 형성하기 위해 Princeton Applied Research 사(Oak Ridge, USA)의 VersaSTAT MC potentiostat 장비를 사용하였다. 기준 전극으로 SCE saturated calomel (saturated KCl, 0.242 V)을 사용하였으며, 이를 통해 실험 중 분극셀 내부의 전압 추이를 관찰하였다. 정상적인 실험의 경우 -900∼-1.1 V의 값을 유지하며, 이를 통하여 반복되는 실험의 신뢰성을 확보하였다. 또한 프로그램 상에서 10초마다 한 번씩 전압값을 기록함으로써 수소장입 시험 중의 수소 발생량을 간접적으로 확인하여 실험 상황을 모니터링 하였다. 전기화학적 습식 장입의 구성을 Fig. 2에 나타냈으며, 실제 수소장입 실험 중 수소가 발생되고 있는 모습을 Fig. 3에 보였다11).
수소 장입 조건에 의한 시편의 수소손상 및 취화 정도에 따른 재료의 기계적 거동을 평균적으로 정확히 평가하기 위해서는 시험편 표면과 시험편 내부의 수소량을 균일하게 할 필요가 있다. 이를 위해 두께가 얇은 평판형태의 시험편으로 실험을 수행할 수 있는 소형펀치시험을 실시하였다.
소형펀치시험편의 제원은 10×10×0.5 mm (가로×세로×두께)이며, 이 시험편의 두께 0.5 mm는 시험편 단면 전체에서 비교적 균일한 수소장입이 가능하다고 가정한 두께이다. 따라서 습식장입에 의한 수소 농도 측정 및 소형펀치시험을 위해 이 두께가 사용되었다. 소형펀치시험은 수소 농도 분석과 동일하게 수소장입시험의 종료시점부터 항상 5분 이내에 수행하였다.
소형펀치시험의 실험장치를 Fig. 4에 보였으며, 지그형상은 Fig. 5에 나타내었다. Fig. 5에 보인 바와 같이 소형펀치시험에 사용되는 지그는 4 mm 직경의 내부 홀을 가진 하부 다이와 2.4+0.01 mm의 내부 홀을 가진 상부 다이, 2.4 mm의 구형 볼 그리고 시험편으로 구성된다. 시험편의 변형은 펀치를 통해 구형 볼에 전달된 하중에 의해 발생한다. 이때, 펀치의 변위와 펀치의 반력이 데이터로 저장된다. 펀치변위와 반력(하중) 사이의 관계선도를 소형펀치곡선(small punch curve)이라 한다.
수소 분석을 위해 독일, Haan, ELTRA 사에서 제작된 OH-900 장비가 사용되었다(Fig. 6). 이 장비는 재료 내의 수소 농도를 ppm 단위로 측정한다. 해당 장비에서는 우선 상하 이동식 다이에 그라파이트로 만들어진 도가니를 장착하고 이를 상부 가열로에 결합하여 전기저항을 이용해 순간적으로 온도를 3,000℃까지 상승시킨다. 이때 결합 당시 가열로 내에 존재하는 불순 가스를 연소시키고, 연소된 가스는 연결된 질소에 의해 모두 배출시켜 가열로 내부를 질소 분위기로 형성시킨다. 이렇게 형성된 질소 분위기에서 시험편을 그라파이트 내로 떨어뜨리고 다시 한 번 온도를 3,000℃까지 상승시켜 해당 재료를 용융시키게 되며, 이를 통해 배출된 금속 내의 가스를 질소 가스와 혼합하여 분석기 내부로 운반시킨 후 최종적으로 수소의 농도를 ppm 단위로 검출하게 된다12).
수소 농도 분석은 시험편의 상태에 따라 그 편차가 상당히 크게 나타날 수 있으므로 모든 시험편은 소형펀치시험에서와 동일하게 장입 종료 후 5분 이내에 실시하였으며, 시험편에 묻어있는 전해질 수용액을 제거하기 위해 분무기를 이용하여 증류수로 30초 동안 동일하게 세척함으로써 분석에서 발생 가능한 오차 변수를 최소화하였다.
3. 결과 및 고찰
3.1 X70강 모재부의 수소 농도 측정 결과
X70 모재부의 수소 농도 분석 결과를 Table 2에 정리하였고, maximum과 minimum 수소 농도값을 제외한 나머지 수소 농도값의 평균과 수소장입시간과의 관계를 Fig. 7에 나타내었다.
농도 분석 결과 20시간 수소 환경에 노출된 시험편의 수소 농도만 원재에서 검출된 수소 농도값보다 높게 나왔으며, 1시간, 5시간, 10시간 수소장입한 시편의 농도값은 원재보다 낮게 나왔다. 원재를 제외한 시험편은 장입시간이 늘어남에 따라 수소 농도값이 증가하는 경향을 확인할 수 있었으나, 그 차이가 크지는 않고 시간별 수소 농도의 편차가 상당히 크기 때문에 장입시간이 늘어나면 수소 농도값이 증가한다는 결론을 도출하기에는 무리가 따른다. 또한 원재의 수소 농도값이 1, 5, 10, 20시간 수소장입한 시편의 수소 농도값보다 높게 나오는 이유를 확인하기 위해서는 금속학적 연구 등의 추가적 실험이 필요한 것으로 판단되지만, 일단 전기분극이 가해지기 전의 단계를 일정한 수소 장입 조건에 놓이기 전의 상황으로 제외한다면 분극에 의한 장입시간에 따른 수소장입량은 증가 곡선으로 표현할 수도 있다.
3.2 X70강 모재부의 수소 손상 강도평가
앞에 설명한 장입조건 0.5 M H2SO4 수용액, 상온 환경, 전류 밀도 100 mA/cm2의 정전류 조건에서 원재와 1, 5, 10, 20시간 수소장입한 시험편에 대해 각각 3번에 걸쳐 소형펀치시험을 실시하였다. SP 시험에 의하여 수소 장입시간에 따른 최대강도값, 파단시점의 변위값인 SP 변위(SP displacement at failure), SP 에너지값을 Table 3에 나타냈으며, 실험 결과 얻은 소형펀치곡선을 Figs. 8-10에 나타내었다.
이들 곡선으로부터 측정된 파단 시의 SP 변위값과 수소 농도 사이의 관계를 Figs. 11, 12에 나타내었으며, 최대 SP 하중의 평균값과 수소 농도 사이의 관계를 Fig. 13에 나타내었다. 또한, SP 에너지와 수소 농도 사이의 관계는 Fig. 14에 나타내었다.
기존 연구 결과에서 공통적으로 관찰되는 것은 고강도 금속의 경우 수소 장입에 의하여 파단 시의 연신율 또는 인성은 저하되지만, 최대 인장강도는 크게 변화하지 않는 것으로 보고되고 있다. 본 연구 결과에서는 Fig. 11과 Fig. 12에 파단 시의 SP 변위를 장입된 수소량에 따라 나타내었다. 수소 장입시간이 일정하여도 수소 장입량이 편차가 크게 나타나므로, Fig. 11에는 수소 장입시간을 X축으로, Fig. 12에는 장입된 수소량을 X축으로 나타내었다. Fig. 11에서와 같이 수소 장입시간이 길어지면 파단 시 SP 변위가 줄어드는 경향을 보이지만, 20시간 장입의 경우는 다시 증가하였다. Fig. 12에서 장입된 수소량의 함수로 나타내 보아도 기존 연구 결과와 같이 수소량에 따라 파단 시 SP 변위가 줄어드는 경향이 보이지는 않는다. 최대 SP 하중 즉, 최대 강도를 나타내는 Fig. 13을 보면 수소 장입량에 따라 강도가 오히려 증가하는 경향을 나타내고 있다. 전체 SP 파단 시까지의 소모에너지인 SP 에너지의 값(Fig. 14)도 특별한 경향을 보이지 않는다. 이는 X70강의 경우 수소의 영향에 그리 민감하지 않다는 것을 나타내는 것이라 할 수 있다. 동일한 조건의 실험에 의한 Inconel의 경우 확연한 수소장입의 차이를 나타내고 있으므로 X70 재료의 수소 저항성이 높다고 볼 수 있다8).
관찰된 SP 시험 결과 10시간 장입한 시편을 제외한 시편의 최대강도 값이 장입시간에 따라 증가하는 경향을 보인 정도의 결과만 나타난 셈이다. 강도값의 미세한 증가와 편차를 고려하였을 때 수소 장입량에 따라 최대강도가 증가한다고 단정하기는 어렵다. 특이점은 20시간 수소장입한 시험편의 강도가 수소 농도가 가장 많이 검출되었음에도 불구하고 가장 높은 소형펀치 강도값을 보인 것이며, 이에 대한 원인은 파단면에 대한 금속학적 분석에서 논의하고자 한다.
3.3 X70강 모재의 수소 취화 손상 관찰
수소장입 시간에 따른 SP 시험 결과 측정값의 변화에 대해 설명하기 위해 X70강의 모재부의 SP시험 후 파단된 시험편의 표면과 파단면을 SEM으로 관찰하여 Figs. 15-19에 나타내었다. 수소 장입되지 않은 시편은 Fig. 15에, 1 h, 5 h, 10 h, 20 h 수소 장입된 시편을 Figs. 16-19에 각각 나타내었다. Inconel의 경우에는 수소장입에 의한 표면층의 균열 발생 차이가 확실히 나타났지만, X70의 경우는 장입시간에 비례하는 표면 취화층이 관찰되지 않는다.
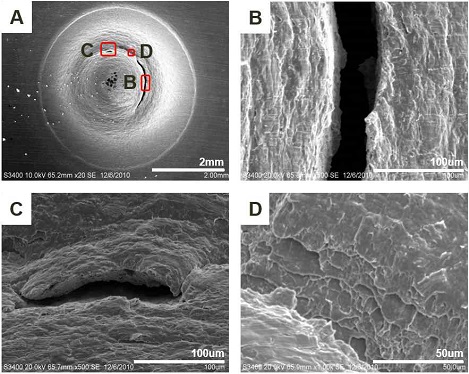
Scanning electron microscope observations of the charged specimen surface (Virgin) under magnification of : (a) ×20, (b) ×500, (c) ×500, (d) ×1,000
10시간 장입된 Fig. 18(d)를 보면, 시편의 표면층에 수소가 확산 침투되어 재질의 취화가 발생하여 얕은 깊이의 균열들이 많이 형성되어 있는 것을 확인할 수 있다. Fig. 16(d)도 이와 유사한 경우이다. 하지만 Fig. 16(c)에 보이는 바와 같이 SP 시편의 내부는 연성 파단이 보이며, 이는 수소 침투가 SP 시편의 내부까지 진행되지 않았음을 보여준다. 가장 긴 20 h 장입시편의 내부(Fig. 19[d])도 연성파면이 관찰된다. 따라서 본 연구에서 사용된 0.5 mm 두께의 시편은 두께 깊이에 따라 재료물성이 균일한 재료의 시험에서는 적절하지만, 습식장입에 의해 X70의 수소침투층의 재료물성을 평가하고자 하는 경우에는 두께가 더 얇은 시편이 유리함을 알 수 있다.
이와 같이 각각 조건의 3개의 시험편의 표면 관찰 결과로부터 시험편 표면의 변형상태가 수소 장입시간이 증가함에 따라 달라지는 현상을 관찰할 수 있다. 수소 장입시간이 길어질수록 시험편의 표면에 생성된 균열의 길이가 길어지고, 숫자가 많아졌다. 균열의 깊이도 장입시간에 따라 깊어지는 것이 육안으로 확인되었으나, 정량적인 측정은 어려웠다.
파단면에서의 SP 시편의 두께를 비교해보면 20시간 장입한 시편의 파단면 부위 두께는 원재의 파단면 주위 두께보다 두꺼웠다. 이는 20시간 장입한 시편의 단면 감소가 적게 발생하였다는 것을 보여준다. 즉, 수소장입시간이 길어지면 재료는 수소취화가 발생하여 연성을 잃고 취화된다는 것을 알 수 있다. 이는 파단면 관찰 결과에서 확인 가능하였다. 수소 장입하지 않은 원재에서 발견되는 연성 파괴 양상은 수소 장입시간이 길어짐에 따라 취성파면 양상을 보이는 경향이 관찰되었으나 표면에 국한된 경우가 많았다.
이와 같이 X70강의 수소장입으로 인한 재료의 표면층에 집중된 취화는 SP 시험 중 하중을 가하는 초기에 표면에 균열이 발생하거나 탄성 굽힘 부분에 영향을 주게 되므로 SP 시험의 파단 시 최종 SP 변위에 영향을 주기보다는 오히려 SP 시험의 초기 단계에서 SP 곡선의 차이를 줄 수 있을 것이다. Fig. 9의 SP 곡선의 초기 부위가 시편마다 서로 다른 이유가 이러한 이유일 수도 있을 것으로 사료된다.
4. 결 론
본 연구에서는 전기화학적 습식 수소장입방법을 이용하여 API X70 강의 모재부 표면에 수소를 발생시켜 확산에 의해 시편 내부로 침투시켰으며, 이후 소형펀치시험에 의한 기계물성 측정값과 정량적 수소 농도 분석값을 비교함으로써 수소 확산이 기계적 물성에 미치는 영향과 실제 장입되는 수소농도량을 분석하였다. 장입시간을 변수로 반복 실험을 진행하였으며, 연구 결과는 다음과 같다.
1) 전기화학적 습식 수소장입법을 이용하여, 0.5M H2SO4 수용액, 상온, 전류 밀도 100 mA/cm2의 정전류 조건에서 API X70 강의 모재부에 수소를 침투시켰으며, 재료의 수소 손상에 대한 민감도를 평가할 수 있었다.
2) 수소 농도 분석 결과 원재를 제외한 시험편은 장입시간이 늘어남에 따라 수소 농도값이 증가하는 경향을 보였다. 하지만 그 차이가 미세하고 시간별 수소 농도의 편차가 크기 때문에 장입시간이 늘어나면 수소 농도값이 증가한다고 표현하기에는 무리가 있다. 이는 X70강의 우수한 수소 저항성을 나타내는 것으로 볼 수 있다.
3) 소형펀치시험 결과 10시간 장입한 시편을 제외한 모든 시편의 최대강도 값이 장입시간에 따라 증가하였다. 하지만 강도의 증가값이 크지 않으며, 강도값 사이의 편차가 존재하여 시간에 따라 최대 강도가 증가한다고 단정하기 어렵다.
4) 소형펀치시험 후 시험편들을 대상으로 SEM 파면분석을 수행한 결과, 시험재들의 표면층에서만 수소취화에 의한 미세 균열이 관찰되었다. 시편 내부에서는 연성파면이 관찰되므로, 수소 확산은 표면에서만 발생하였다.
5) 전체적으로 API X70강의 모재부는 수소장입시간에 따른 수소 농도와 최대강도, SP energy 값의 변화가 거의 없음을 확인하였으며, 이를 통해 장입된 수소가 본 재료에 미치는 영향이 매우 적음을 확인할 수 있었다. 이는 모재부만의 결과이므로 용접부에 대해서는 추가 연구가 필요하다.
Acknowledgments
본 연구는 한국가스공사 가스연구원의 지원을 받아 수행되었습니다.
References
-
S. J. Yoon, H. J. Lee, K. B. Yoon, Y. W. Ma, and U. B. Baek, “Hydrogen damage in 34CrMo4 pressure vessel steel with high tensile strength”, Journal of Mechanical Science and Technology, Vol. 32, No. 2, 2018, pp. 637-646. Retrieved from https://link.springer.com/article/10.1007/s12206-018-0111-7, .
[https://doi.org/10.1007/s12206-018-0111-7]
- H. J. Lee, “Study for hydrogen embrittlement in base metal of API 5L X70 steel pipe”, MS Thesis, Chung-Ang University, 2011.
- T. M. Adams, R. Sindelar, G. Rawls, and P. S. Lam, “Evaluation of natural gas pipeline materials for hydrogen/mixed hydrogen-natural gas service”, DOE Hydrogen Program, 2005. Retrieved from https://www.hydrogen.energy.gov/pdfs/progress05/v_a_4_adams.pdf, .
-
Y. W. Ma and K. B. Yoon, “Assessment of tensile strength using small punch test for transversely isotropic aluminum 2024 alloy produced by equal channel angular pressing”, Materials Science and Engineering: A, Vol. 527, No. 16-17, 2010, pp. 3630-3638.
[https://doi.org/10.1016/j.msea.2010.02.057]
-
I. I. Cuesta and J. M. Alegre, “Hardening evaluation of stamped aluminium alloy components using the small punch test”, Engineering Failure Analysis, Vol. 26, 2012, pp. 240-246.
[https://doi.org/10.1016/j.engfailanal.2012.06.004]
-
S. P. Singh, S. Bhattacharya, and D. K. Sehgal, “Evaluation of high temperature mechanical strength of Cr–Mo grade steel through small punch test technique”, Engineering Failure Analysis, Vol. 39, 2014, pp. 207-220.
[https://doi.org/10.1016/j.engfailanal.2014.01.014]
-
D. H. Lee, “Evaluation of fracture strength and material degradation for weldment of high temperature service steel using advanced small punch test”, KSME International Journal, Vol. 18, No. 9, 2004, pp. 1604-1613. Retrieved from https://link.springer.com/article/10.1007/BF02990375, .
[https://doi.org/10.1007/BF02990375]
- H. U. Seo, Y. H. Ma, and K. B. Yoon, “Evaluation of hydrogen embrittlement behavior in INCONEL alloy 617 by small punch test”, Trans. Korean Hydrogen and New Energy Society, Vol. 21, No. 4, 2010, pp. 340-345. Retrieved from http://www.koreascience.or.kr/article/JAKO201033359738698.page, .
-
A. Torres-Islas, V. M. Salinas-Bravo, J. L. Albarran, and J. G. Gonzalez-Ro driguez, “Effect of hydrogen on the mechanical properties of X-70 pipeline steel in diluted NaHCO3 solutions at different heat treatments”, Int. J. Hydrogen Energy, Vol. 30, No. 12, 2005, pp. 1317-1322.
[https://doi.org/10.1016/j.ijhydene.2005.04.007]
- J. S Oh, H. U. Seo, H. Kim, and K. B. Yoon, “Evaluating hydrogen damage of Inconel 617 using electro-chemical hydrogen charging”, The Korean Institute of Gas, 2008, pp. 227-232. Retrieved from http://www.dbpia.co.kr/Journal/articleDetail?nodeId=NODE02212887, .
- W. D. Jr. Callister, “Materials science and engineering”, 7th ed, Elsevier, Netherlands, 2006.
-
J. Capelle, I. Dmytrakh, and G. Pluvinage, “Comparative assessment of electrochemical hydrogen absorption by pipeline steels with different strength”, Corrosion Science, Vol. 52, No. 5, 2010, pp. 1554-1559.
[https://doi.org/10.1016/j.corsci.2010.02.011]