
수소전기차용 EPDM 고무의 충전재 입자 크기별 고압 수소 환경에서의 거동 연구
1한국가스안전공사 가스안전연구원2평화오일씰공업
2Pyung Hwa Oil Seal Industry Co.,Ltd., 597 Nongong-ro, Nongong-eup, Dalseong-gun, Daegu 42982, Korea
2020 The Korean Hydrogen and New Energy Society. All rights reserved.
Abstract
In this study, ethylene-propylene-diene monomer (EPDM) rubbers reinforced with various particle size of carbon black were prepared and tested. We followed recently published CSA/ANSI CHMC2 standard “the test methods for evaluating material compatibility in compressed hydrogen applications-polyemr”. Measurement of change in hardness, tensile strength and volume were performed after exposure to maximum operating pressure, 87.5 MPa, for 168 hours (1 week). Once EPDM was exposed to high-pressure hydrogen, the samples experience volume increase and degradation of the physical properties. Also, after the dissolved hydrogen was fully eliminated from the specimens, the hardness and the tensile properties were not recovered. The rubber reinforced with smaller sizes of carbon black particles showed less volume expansion and decrease of physical properties. As a result, smaller particle size of carbon black filler led to more resistance to high-pressure hydrogen.
Keywords:
Fuel cell electric vehicle, Sealing material, Rubber, Hydrogen, High pressure키워드:
수소전기차, 씰링소재, 고무, 수소, 고압1. 서 론
화석연료의 고갈 및 환경문제로 인해 친환경 에너지에 대한 관심이 높아지고 있다. 그중 수소 에너지는 수소가스를 연료로 하며 연료전지와 같은 에너지 변환 시스템을 이용하여 발전을 하는 에너지로 유해물질이나 온실가스 등을 배출하지 않아 환경문제를 해결할 수 있는 차세대 에너지원이다. 또한, 수소는 높은 에너지 밀도를 가지고 있으며 운반 시 전기에너지 형태의 운송보다 손실도 적고 보관비용이 전기보다 낮아 수소는 에너지원뿐만 아니라 저장, 수송매체로도 활용이 가능하다1).
자동차 업계에서는 기존 내연기관 자동차를 대체하기 위해 많은 연구를 진행하고 있으며, 수소전기차(fuel cell electric vehicle, FCEV)는 기존 전기차에 비해 긴 주행거리와 짧은 충전 시간 등의 이점이 있어 차세대 자동차로 각광받고 있다. 하지만 에너지 밀도를 높이기 위해 70.0 MPa의 고압 상으로 사용하고 있다. FCEV의 공칭 사용 압력(nominal working pressure)은 70.0 MPa이며 충전 시 온도 상승에 의한 최대 운전 압력(maximum operating pressure, MOP)은 87.5 MPa에 달한다2). 따라서 고압 수소 환경에서 사용되는 재료들에 대한 안전성 및 내구성 확보는 필수적이라 할 수 있다. 하지만 고압 수소 환경에서 고무소재의 경향과 거동에 대한 실증 시험 연구는 안전상의 이유로 그보다 낮은 압력에서 진행하거나 반응성이 낮은 헬륨 또는 질소가스를 이용하고 있어 실증 연구에 많은 한계를 보여주고 있다.
씰링에 사용되는 고무소재는 고압 수소 환경에서 급격한 감압 및 압력반복에 의해 내부 파괴가 발생된다. 이러한 균열은 blister fracture라고 불리며 몇몇 문헌에서 보고된 바 있다3-7). 내부 파괴는 씰링 소재의 영구적인 물성저하를 일으키며 고압 수소 기밀 및 안전성에 중요한 영향을 끼치므로 고무소재의 고압 수소 적합성 향상에 대한 연구가 필요한 실정이다.
본 연구에서는 기존 수소부품에 많이 사용되고 있는 고무 재료인 ethylene-propylene-dien-monomer (EPDM) 고무에 충전된 카본블랙(carbon black, CB) 충전재의 입자 크기별 고압 수소 환경에서의 거동 변화 및 경향을 알아보고자 시험편을 87.5 MPa에서 노출 후 질량 변화, 부피 변화, 경도, 인장강도를 측정하여 분석하였다.
2. 실 험
2.1 시편 제조
CB의 입자 크기별 고압 수소 환경에서 거동변화평가를 위해 EPDM 고무를 사용하였다. EPDM에 입자 크기가 26-30 nm, 40-48 nm, 61-100 nm인 CB 필러 40 wt.%를 각각 혼합하였다. EPDM 고무 배합물은 용량 3 L의 밀폐식 혼합기(kneader)를 사용하였다. 물성을 평가하기 위한 시험편은 점성도계(rheometer)로 175℃에서 최적가교시간을 측정하여 일정 온도로 유지되는 평판식 가류기(80 톤, 평화기공, 2P1U)를 이용하여 제조하였다. 인장 시험편의 경우는 두께 2 mm의 아령형 1A호(ISO 37)의 형태로 압축 성형하여 제조하였고 시험편의 기본 물성을 측정하여 Table 1에 표기하였다.
2.2 수소 노출 및 물성 변화 시험
고압 수소는 폴리머재료에 대한 용해성이 높아 재료의 기계적 성질 및 특성을 변화 시킬 수 있다. 최근 미국 국가 표준 협회(ANSI)와 캐나다 표준 협회(CSA)에서는 고압 수소 환경에서 폴리머 재료의 적합성 평가 시험 방법인 CHMC2를 2019년 8월 개발 및 제정하였다.
준비된 시험편의 고압 수소 노출 시험을 위해 CHMC2의 hydrogen static exposure (S.E.) 시험 방법에 따라 연구를 수행하였다. 시료는 MOP인 87.5 MPa에서 168시간 동안 노출시켰다2,8). 이때 사용된 압력챔버는 설계압력 100 MPa의 SUS316L 재질의 실린더 형태이며, 안전을 위해 야외에 설치된 콘크리트 시설물 내에서 시험을 실시하였다. 노출 시험 완료 후, EPDM 시험편 내에 수소가 용해되어 있는 상태에서 물성 변화를 측정하기 위해 감압 후 30분 이내에 질량 변화, 부피 변화, 경도, 인장강도 측정을 하였고, 48시간 이후 시험편에 용해된 수소가 모두 빠져나간 후 물성 변화를 확인하기 위해 동일한 방법에 의해 재측정 하였다.
수소 노출 후 시편의 질량․부피 변화 및 수소용해도를 확인하였다. 시험에 사용된 시료의 크기는 약 7×7×2 mm의 육면체이며 아르키메데스법을 이용하여 시료의 공기 중 질량, 물속에서의 질량을 측정해 식 (1)로 밀도 및 부피를 계산하였다.
(1) |
식 (1)에서 ρ는 시험편의 밀도, mdry와 mwet은 공기 중 시료의 질량과 물속에서의 시료의 질량이다. ρwater와 ρair는 각각 물과 공기의 밀도이다. 시험은 항온 항습실에서 실행하였으며, 측정 시 물과 공기의 온도를 측정하여 밀도를 계산하였다. 3개의 시편에 대하여 고압 수소 노출 후 15분 이내에 측정하여 평균값을 구하였고, 같은 방법으로 노출 후 24시간, 48시간 이후에도 측정을 진행하였다8).
CHMC2에 명시된 고무 재료의 기계적 물성 평가 항목인 경도(durometer A)와 인장강도를 측정하였다8). 시험은 고압 수소 노출 후 30분 이내 그리고 48시간 이후에 진행하였다.
경도 측정 시험 방법은 ASTM D2240을 따랐다. 경도측정을 위한 고무 시험편은 두께가 6 mm 이상이어야 하나 시트형 시험편의 두께가 2.5 mm 이하인 관계로 36×25 mm의 시험편 4개를 겹쳐서 측정하였다9). 그리고 각 시험편별로 수소 노출 전후로 3초간 5회 측정하여 각각의 시험편에 대한 중간값을 구한 후 평균값을 계산하였다.
인장시험은 ISO 37을 따르며 시험편은 아령형 시험편 1A호형이며, 표점거리(gauge length)는 20 mm 시험 속도는 500 mm/min으로 시험을 진행하였다10). 고압 수소 노출 전, 노출 후 30분 이내 그리고 48시간 이후에 각각 5회씩 측정하여 중간값을 구하여 비교하였다.
3. 결과 및 고찰
Table 2는 EPDM 시험편의 수소 노출 후 질량, 밀도, 부피 변화를 나타낸다. CB의 입자 크기가 작을수록 질량 변화량은 크지만 부피 변화는 크지 않은 것을 알 수 있다. CB는 수소를 흡수하는 것으로 알려져 있으며, 고무시료에 침투한 수소는 Fig. 1과 같이 대부분 CB 입자 주변에 집중된다7,11,12).
충전된 CB의 입자 크기가 작을수록 CB의 표면적이 증가하게 되고 더 많은 수소가 CB 주위에 집중된다. 결과적으로 EPDM 고무에 침투한 수소가 충전된 CB 주변으로 집중되었기 때문에 EPDM 고무에 수소 용해도가 낮아지게 되고 그로 인해 시료가 덜 팽창되었다고 추측할 수 있다. 노출 시험 후 24시간이 경과하면 용해된 수소는 대부분 빠져나가 원래의 부피로 회복되었다. 수소가 빠져나간 이후 무게 및 부피 변화는 실험실 환경에 따른 오차범위로 판단된다.
Table 3은 수소 노출 후 인장강도 변화이다. 수소 노출 직후 인장강도는 80-1, 80-2, 80-3 순으로 각각 11.85%, 16.40%, 18.38%씩 감소하여 80-1 시험편이 가장 적은 변화량을 보였다. 즉, CB 입자 크기가 작을수록 고압 수소의 영향을 덜 받는 것을 확인하였다. 부피 변화 측정 결과와 비교해보면 부피 변화량이 작을수록 인장강도 감소량도 작다. 이는 고압 수소 환경에 노출된 시료 내부에 용해된 수소가 시료의 단면적을 증가시키며 저장 탄성률을 감소시키기 때문에 인장강도 역시 감소한 것으로 판단할 수 있다13).

Change in tensile strength (σ) and standard deviation of CB filled EPDM rubber after static exposure
Table 3과 Table 4에서 노출 시험 48시간 후 용해된 수소가 빠져나가 시료의 부피가 회복된 이후 인장강도와 경도특성을 확인해보면 노출 전보다 감소한 것을 알 수 있다. 이는 고압 수소 환경이 고무 재료에 영구적인 손상을 일으키는 것으로 생각된다.

Change in hardness (durometer A) and standard deviation of CB filled EPDM rubber after static exposure
Fig. 2는 EPDM 시험편의 수소 노출 시험 전, 후의 인장시험 직후 파단면의 scanning electron microscope (SEM) 이미지이다. 수소 노출시험 전후 파단거동의 변화는 나타나지 않았으며, blister 발생에 의한 blister fracture 또한 발생하지 않은 것으로 보아 충분한 양의 CB가 충전되면 blister는 발생하지 않는 것을 알 수 있다. Fig. 2(a)와 (d) 파단면 차이는 (d)에서 균일한 파단면을 확인하였으므로 (a) 시험편의 고무조직의 불균일함으로 인한 부분적 물성차이 때문으로 보인다. 몇몇 연구에서 고압 수소에 노출된 고무 재료는 수소에 의한 화학적인 구조의 변형은 일어나지 않는다고 주장한다12,14). 따라서 고무 재료의 화학적 변화에 의한 물리적 물성의 하락은 아니라고 유추할 수 있다.
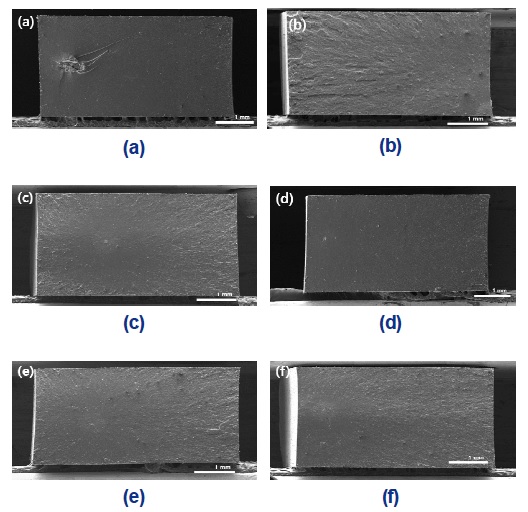
SEM image of tensile fracture plane before static exposure (a) 80-1, (b) 80-2, (c) 80-3, and after static exposure (d) 80-1, (e) 80-2, (f) 80-3.
고무 재료는 고압 수소에 노출 후 감압 과정에서 blister에 의한 마이크로미터 크기의 파괴뿐만 아니라 수십-수백 나노미터 크기의 미세한 조직의 파괴가 일어난다고 알려져 있다. 그리고 고무 재료의 특성상 가교 결합 밀도가 불균등하여 조직 강도가 낮은 부분에서 용해된 수소분자가 빠져나오며 기포를 형성해 조직을 파괴시킨다고 알려져 있다15-17). 그러므로 고압 수소 노출 후 EPDM 시험편은 나노미터 단위의 미세조직 파괴에 의한 영구적인 물성 하락을 겪는다고 추정할 수 있다.
CB 입자 크기가 작을수록 CB의 표면적이 넓어지고 더 많은 수소가 CB 주변으로 집중되어 고무조직 내에 용해된 수소의 양이 적어지기 때문에 가장 작은 입자 크기의 CB가 충전된 80-1 시료가 고압 수소에서 가장 뛰어난 적합성을 보였다.
시험 데이터와 SEM 이미지 분석 결과를 종합해 보면 본 실험에서 사용된 시험편에서는 blister가 발생하지 않아 blister fracture는 발생하지 않았으나 고무 재료의 특성상 나노미터 단위의 미세조직 파괴는 일어나 영구적인 물성하락이 나타난 것으로 보인다. EPDM 고무의 수소 노출 후 물성 하락을 줄여 수소 적합성을 높이기 위해서는 작은 입자 크기를 가진 CB를 충전하여 고무조직에 용해되는 수소의 양을 줄이는 것이 중요하다고 본 연구를 통해 유추할 수 있다.
4. 결 론
CB 충전재의 입자 크기에 따른 고압 수소 환경에서의 거동변화를 확인하고자 3가지 크기의 CB가 각각 충전된 EPDM 시험편을 제조하여 87.5 MPa 고압 수소에 노출 시험 후 물리적 특성을 평가하였다. 본 실험을 통해서 얻은 결과는 다음과 같이 요약할 수 있다.
1) 고무 재료에 충전된 CB는 입자 크기가 감소함에 따라 수소 노출 직후 부피 변화량과 물리적 특성의 변화가 적어진다.
2) 충전된 CB 입자는 수소를 입자 주변으로 집중시켜 고무를 수소로부터 보호하는 효과가 있다. 따라서 충전재의 입자 크기가 작을수록 표면적이 커져 보호효과가 커진다.
3) CB의 입자가 작을수록 고무 재료의 수소용해도를 낮추기 때문에 고압 수소 감압에 의한 영구적인 물성저하가 적게 일어났다.
Acknowledgments
본 연구는 국토교통부 교통물류연구사업(No.19TLRP-C152334-01) 연구비 지원으로 수행되었습니다.
References
-
M. Momirlan and T. Veziroglu, “Current status of hydrogen energy”, Renewable and Sustainable Energy Reviews, Vol. 6, 2002, pp. 141–179.
[https://doi.org/10.1016/S1364-0321(02)00004-7]
- ISO, “ISO 19880-1:2020, gaseous hydrogen — fuelling stations — part 1: general requirements”, ISO, 2020. Retrieved from https://www.iso.org/standard/71940.html, .
-
B. J. Briscoe, T. Savvas, and C. T. Kelly, “Explosive decompression failure of rubbers: a review of the origins of pneumatic stress induced rupture in elastomers”, Rubber Chemistry and Technology, Vol. 67, No. 3, 1994, pp. 384-416.
[https://doi.org/10.5254/1.3538683]
-
A. N. Gent and D. A. Tompkins, “Nucleation and growth of gas bubbles in elastomers”, Journal of Applied Physics, Vol. 40, 1969, pp. 2520-2525.
[https://doi.org/10.1063/1.1658026]
-
A. Stevenson and G. Morgan, “Fracture of elastomers by gas decompression”, Rubber Chemistry and Technology, Vol. 68, No. 2, 1995, pp. 197-211.
[https://doi.org/10.5254/1.3538735]
- S. Zakaria and B. J. Briscoe, “Why rubber explodes”, Chemtech, Vol. 20, No. 8, 1990, pp. 492-495.
-
J. Yamabe and S. Nishimura, “Influence of fillers on hydrogen penetration properties and blister fracture of rubber composites for O-ring exposed to high-pressure hydrogen gas”, Int. J. Hydrogen Energy, Vol. 34, No. 4, 2009, pp. 1977-1989.
[https://doi.org/10.1016/j.ijhydene.2008.11.105]
- ANSI, “CSA/ANSI CHMC2 test methods for evaluating material compatibility in compressed hydrogen applications – polymers”, 2019. Retrieved from https://store.csagroup.org/ccrz__ProductDetails?viewState=DetailView&cartID=&portalUser=&store=&cclcl=en_US&sku=CSA%2FANSI%20CHMC%202%3A19, .
- ASTM International, “ASTM D2240-00, standard test method for rubber property—durometer hardness”, ASTM International, 2002. Retrieved from https://www.astm.org/DATABASE.CART/HISTORICAL/D2240-00.htm, .
- ISO, “ISO 37:2017 rubber, vulcanized or thermoplastic — determination of tensile stress-strain properties”, ISO, 2017. Retrieved form https://www.iso.org/obp/ui/#iso:std:iso:37:ed-6:v1:en, .
-
J. Yamabe and S. Nishimura, “Influence of carbon black on decompression failure and hydrogen permeation properties of filled ethylene‐propylene–diene–methylene rubbers exposed to high‐pressure hydrogen gas”, Journal of Applied Polymer Science, Vol. 122, 2011, pp. 3172-3187.
[https://doi.org/10.1002/app.34344]
-
J. Yamabe and S. Nishimura, “Tensile properties and swelling behavior of sealing rubber materials exposed to high-pressure hydrogen gas”, Journal of Solid Mechanics and Materials Engineering, Vol. 6, No. 6, 2012, pp. 466-477.
[https://doi.org/10.1299/jmmp.6.466]
-
H. Fujiwara, “Analysis of acrylonitrile butadiene rubber (NBR) expanded with penetrated hydrogen due to high pressure hydrogen exposure”, Nippon Gomu Kyokaishi, Vol. 44, No. 3, 2017, pp. 41-48.
[https://doi.org/10.1177/0307174X1704400308]
-
H. Fujiwara, J. Yamabe, and S. Nishimura, “Evaluation of he change in chemical structure of acrylonitrile butadiene rubber after high- pressure hydrogen exposure”, Int. J. Hydrogen Energy, Vol. 37, No. 10, 2012, pp. 8729-8733,
[https://doi.org/10.1016/j.ijhydene.2012.02.084]
-
Y. Yamabe and S. Nishimura, “Nanoscale fracture analysis by atomic force microscopy of EPDM rubber due to high-pressure hydrogen decompression”, J. Mater. Sci., Vol. 46, 2011, pp. 2300-2307.
[https://doi.org/10.1007/s10853-010-5073-4]
-
Y. Ikeda, Y. Yasuda, K. Hijikata, M. Tosaka, and S. Kohjiya, “Comparative study on strain-induced crystallization behavior of peroxide cross-linked and sulfur cross-linked natural rubber”, Macromolecules, Vol. 41, No. 15, 2008, pp. 5876–5884.
[https://doi.org/10.1021/ma800144u]
- H. Dohi, M. Sakai, S. Tai, H. Nakamae, H. Kimura, M. Kotani, H. Kishimoto, and Y. Minagala, “Atomic force microscopy study on mesh structure formed on stretched rubber surface”, KGK Kautschuk Gummi Kunststoffe, Vol. 60, 2007, pp. 52-55.