
경질 탄화수소 촉매 열분해를 위한 Ni 기반 구슬 촉매에 대한 연구
2024 The Korean Hydrogen and New Energy Society. All rights reserved
Abstract
In this study, we researched Ni-based bead catalysts for the catalytic thermal decomposition of light hydrocarbons. A Ni-based bead-type catalyst was prepared, and catalytic thermal decomposition performance of light hydrocarbons was evaluated. The 30Ni/Al2O3 catalyst exhibited the most superior performance, with the presence of both fibrous and carbon black forms on the catalyst surface. Catalytic performance was evaluated for particles sized between 150-250 and 500 μm, with excellent catalytic thermal decomposition properties in the 150-250 μm range. After the reaction, carbon removal through collision between catalysts in the fluidized bed was observed. It was confirmed that as the particle size increases, the amount of carbon removed increases.
Keywords:
Catalytic thermal decomposition, Bead catalyst, Light hydrocarbon, Ni-based catalyst, Fluidized bed키워드:
촉매 열분해, 구슬 촉매, 경질 탄화수소, Ni 기반 촉매, 유동층1. 서 론
플라스틱은 생산이 쉽고 경제성, 물성(기계적, 화학적), 가공성의 다양한 장점이 있다. 따라서 이를 기반으로 플라스틱의 수요가 급격하게 증가하였다. 글로벌 플라스틱 생산량은 연간 약 4억 톤에 이르고, 국내 플라스틱 소비량은 약 700만 톤에 이른다. 글로벌 폐플라스틱 발생량은 연간 3.3억 톤이며, 재활용 비율은 약 12%밖에 되지 않는다1). 국내 폐플라스틱 발생량은 연간 796만 톤으로 실질적 재활용 비율은 약 23%밖에 되지 않는다. 재활용 측면에서 철, 유리, 알루미늄, 종이 등은 각각 재활용 비율이 74, 70, 67, 60%로 절반 이상이 다시 사용된다. 그러나 플라스틱의 경우 분류가 어렵고, 재활용 의지가 상대적으로 낮아서 낮은 재활용 비율을 보인다.
최근 코로나19로 인한 비대면 생활 방식으로 포장 및 배달 음식 섭취가 늘고, 감염병 대응을 위해 식당과 같은 식품접객업소에서 일회용품 사용 증가로 인한 재활용 폐기물의 하루 배출량이 증가하였다. 국내 재활용 폐기물 수거 시장의 대부분은 민간업체가 차지하고 있다. 그러나 민간업체는 저유가나 플라스틱의 가격 변동에 따른 폐기물 수거 및 처리가 일정하게 이루어지지 않는다. 지자체에서는 재활용 폐기물 수거를 직접 관리하고, 폐기물 처리 시설을 늘리거나 폐기물의 안정적인 처리 방법을 모색하고 있다.
정부는 국내 폐플라스틱 발생 저감 정책으로 탄소중립 K-순환경제 이행계획을 발표하였다. 이에 따르면 생산, 유통, 소비, 재활용 전 과정 폐기물 감량 및 순환성 강화를 표기하고 있고, 열분해 등 화학적 재활용을 통한 폐플라스틱의 연·원료화를 제시하였고, 폐플라스틱을 통한 열분해 비중을 2020년 0.1%에서 2030년 10%까지 증가시킬 계획을 발표하였다. 정부는 폐플라스틱의 고부가가치화를 위해 연속식 운전 기술, 고부가 제품(합성가스, 고순도 수소)의 생산과 같은 물리적, 화학적 재활용 고도화 기술 획득을 목표로 2022-2025년까지 정부 출연금 총 344억 원의 예산으로 폐플라스틱을 활용한 연·원료화 기술개발 사업을 추진하였다2).
폐플라스틱은 화학적 재활용(chemical recycling), 물질 재활용(material recycling), 에너지 재활용을 통해 재사용할 수 있다3). 물질 재활용은 폐플라스틱을 추가적인 탄소 발생 없이 재활용할 수 있는 장점이 있다. 반면 플라스틱의 순도가 높을 때 재활용하는 방법도 있는데, 재활용 전에 분리 또는 세정, 정제와 같은 사전 처리 비용이 들어간다는 단점이 있다. 에너지 재활용은 소각 기술, 고형 연료와 같이 연소를 통하여 에너지원으로 재활용한다. 화학적 재활용은 폐플라스틱에 화학적 변화를 일으켜 다른 물질로 전환하여 재활용하는 것을 말한다. 즉 고분자 구조를 분해하여 원유에서 추출되는 플라스틱 원료와 동일한 원료를 생산하는 등 새롭고 다양한 chemical을 생산하는 기술이다. 폐플라스틱은 열처리를 통해 화학연료로 전환하고 폐플라스틱 열분해유를 통해 폐플라스틱의 처리뿐 아니라 열분해유 탄화수소 화합물과 촉매의 반응을 통해 4차 산업의 중점 에너지인 수소로의 전환이 가능하다. 열분해유는 탄소 사슬이 길고 성분이 다양하여 수소로의 직접적인 생산에 대해서는 미비한 수준이다. 대부분 단일 성분 가스로부터 수소를 생산하는 공정이 많이 연구되고 있다4,5). 열분해유 자체를 사용한 수소로의 직접적인 생산 공정은 아직 개발되지 않았다. 따라서 열분해유의 수소로의 직접적인 생산 공정 개발이 필요하다.
일반적인 화석 연료의 개질을 통해 수소를 생산하는 공정의 경우 수증기나 산소를 첨가해 촉매상에서 접촉 분해하는 방법을 이용한다. 그러나 이러한 수소를 생산하기 위한 개질 과정에서 대량의 이산화탄소를 발생시킨다는 단점이 있다. 스팀 메탄 개질법(steam methane reforming)은 수소를 효율적으로 생산하는 것으로 알려져 있으나 주로 고가의 귀금속 촉매를 사용하여 높은 수소 제조 단가를 가진다. Ni 촉매를 통한 생산은 가격 경쟁력을 가지나 고온 반응에서의 탄소 침적 및 소결 문제를 가진다6-8). 최근 플라즈마를 이용하여 폐플라스틱 열분해유를 탄소 체인이 낮은 상태(C1-C4의 경질 탄화수소 화합물)로 활성화 후, 탄소계 촉매(activate carbon, 카본블랙 등)나 금속계 촉매(Ni, Fe 등)를 사용하여 활성화된 탄화수소 가스를 직접 탄소(카본블랙, 섬유상 탄소, 흑연 등)와 H2로 전환시키는 공정이 연구되고 있다9,10). 탄소 생산 촉매를 통해 기존의 고온에서의 수소 생산 공정에서 비활성화 문제인 탄소 침적을 카본의 억제가 아닌 고부가가치 물질인 카본블랙이나 섬유상 탄소로의 회수를 통해 경제성 확보가 가능하다.
제시된 공정에서 촉매 표면상에 생성된 탄소의 경우 유동층 반응기에서 기체의 흐름 부분의 촉매 간 충돌을 통해 제거할 수 있으며, 카본의 회수가 가능하다고 제시하였다. 이를 위해 촉매의 내구성 확보를 통해 유동층 적용 가능 촉매 개발이 필요하다. 또한 C1-C4 성분의 열분해에 대해 뛰어난 성능을 가진 성형 촉매 개발이 필요하다. 본 연구에서는 bead 형태의 Ni 기반 촉매를 제조하였고, 경질 탄화수소에 대한 열분해 특성을 평가하였다. 열분해 특성 평가 후 표면에 카본이 형성된 bead 촉매를 유동시켜 촉매 간 충돌을 통해 열분해로 생성된 카본 제거를 확인하였다.
2. 실 험
2.1 경질 탄화수소 열분해 Ni 촉매 선정 및 제조
Ni 기반 pellet 촉매는 Ni nitrate hexa-hydrate (Ni[NO3]2·6H2O) 전구체를 사용하여 γ-Al2O3 bead 지지체에 함침법을 통해 담지하여 제조하였다. 전체 질량에 대해 10, 20, 30 wt.% Ni metal을 기준으로 10Ni/Al2O3, 20Ni/Al2O3, 30Ni/Al2O3 열분해 촉매를 제조하였다. 유동층 운전을 위한 열분해 촉매는 150-250, 500 μm 크기의 beads 형태 r-Al2O3 지지체를 사용하여 30 wt.% Ni을 담지 후 비교하였다.
2.2 실험 장치 구성 및 평가 방법
Fig. 1은 열분해 촉매의 특성을 평가하기 위해 사용된 장치 개략도이다. 반응기의 경우 fixed-bed reactor를 사용하였고, mass flow controller를 통해 반응 가스의 유량을 조절하였다. 분석 장치는 가스 크로마토그래피(gas chromatography)를 통해 분리된 가스를 열전도 검출기(thermistor detector, TCD)와 불꽃 이온화 검출기(flame ionization detector, FID)를 통해 분석하였다. 분리된 가스는 각각 TCD에서 H2, N2, CH4, CO2와 FID에서 C1-C4까지의 경질 탄화수소를 분석하였다. 모든 촉매는 H2 10 vol% (N2 balance), 750℃ 조건에서 2시간 환원 처리 후 평가를 진행하였다. 열분해 평가는 C3H8 10 vol% (N2 balance) 가스와 모사 가스(C2H6, 5 vol%; C2H4, 5 vol%; C3H8, 5 vol%; C3H6, 5 vol%; C4H10, 5 vol%; C4H8, 5 vol%; CH4 balance) 조성에서 진행하였다. 열분해 평가 조건은 반응 온도 750℃, 공간 속도는 6,000/h, 촉매 충진량은 0.1 g, 전체 유량 100 mL/min 조건에서 평가를 진행하였다.
3. 결과 및 고찰
3.1 Ni 기반 pellet 촉매 특성 분석 및 열분해 성능 평가
Fig. 2는 함침법으로 제조된 10Ni/Al2O3, 20Ni/Al2O3, 30Ni/Al2O3 열분해 pellet 촉매의 표면 현미경 사진과 scanning electron microscopy-energy dispersive spectrometer (SEM-EDS) 결과이다. 현미경 사진을 통해 10Ni/Al2O3, 20Ni/Al2O3, 30Ni/Al2O3 열분해 촉매가 잘 제조되었음을 확인하였다. 열분해 촉매는 beads 형태의 γ-Al2O3 pellet 지지체의 표면에 Ni이 담지되어 진한 녹색을 띠고 있다. SEM-EDS 분석을 통해 10Ni/Al2O3, 20Ni/Al2O3, 30Ni/Al2O3 열분해 촉매 표면에서의 Ni 함량을 확인하였다. 넣어준 Ni 함량이 증가함에 따라 표면에서의 Ni 함량도 같이 증가하였고, 대략 9.77, 37.95, 63.75 wt%의 Ni을 포함하고 있다. Fig. 3은 각 제조된 열분해 촉매의 fresh와 reduced 상태에서의 X-ray diffraction (XRD) 분석 결과를 나타내었다. XRD 분석 결과를 통해 제조된 열분해 촉매의 결정 구조를 확인하였다. 세 촉매는 활성 물질인 NiO (JCPDS No. 89-7131)는 환원 처리 후 활성 상태인 Ni0 결정 구조로 모두 전환됨을 확인하였다.
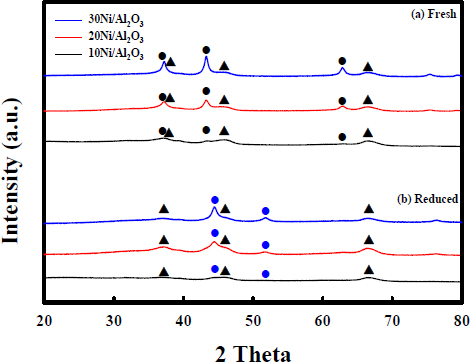
XRD patterns of 10Ni/Al2O3, 20Ni/Al2O3, 30Ni/Al2O3 in the fresh and reduced state (●: NiO, ●: Ni0, ▲: γ-Al2O3).
Fig. 4는 10Ni/Al2O3, 20Ni/Al2O3, 30Ni/Al2O3 열분해 촉매를 고정층 반응기에서 열분해 특성 평가를 진행하였다. 반응 조건은 10 vol.% C3H8 (N2 balance)의 가스를 반응 온도 800℃에서 평가를 진행하였다. Fig. 4(a)는 각 촉매의 평가 결과를 기반으로 시간에 따른 C3H8 전환율을 나타내었는데, 이를 확인해 보면 20Ni/Al2O3, 30Ni/Al2O3 열분해 촉매는 대략 60분까지 99% 이상의 C3H8 전환율을 보였다. 20Ni/Al2O3는 60분부터 미세하게 감소하여 120분에서 대략 96%까지 전환율이 감소하였다. 반면 10Ni/Al2O3의 경우 초기에 대략 90%의 C3H8 전환율을 보였으나 시간이 지남에 따라 급격히 감소 후 60분부터 대략 66%의 C3H8 전환율을 유지하였다. Fig. 4(b)-(d)는 각 열분해 촉매의 반응 후 생성된 가스에 대해 시간에 따른 생산성으로 나타내었다. Fig. 4(b)의 결과를 통해 10Ni/Al2O3 열분해 촉매의 경우, 활성 물질 함량이 적어서 활성사이트가 부족하여 C3H8이 CH4까지의 전환이 덜 되었다. 이로 인해 C2H6, C2H4, C3H6가 일부 검출되었다. H2의 경우 C3H8의 전환율 감소에 따라 H2 생산성도 감소한다. Fig. 4(c)의 결과에서 20Ni/Al2O3는 시간에 따라 H2 생산성이 미세하게 감소하였고, CH4 생산성이 증가한다. 이는 CH4의 전환이 감소하기 때문에 CH4에서 생성되는 H2가 감소하는 것으로 보인다. Fig. 4(d)의 결과에서 30Ni/Al2O3 열분해 촉매도 20Ni/Al2O3와 비슷한 경향을 보이나, 비교적 활성의 감소 폭이 작은 것을 알 수 있다. 이러한 결과를 통해 30Ni/Al2O3에서 대략 120분 동안 경질 탄화수소에 대한 열분해 성능이 우수함을 알 수 있다.
Fig. 5는 경질 탄화수소에 대한 열분해 반응 후 촉매의 표면을 확인하기 위해 SEM 분석을 진행한 것이다. Fig. 5(a), (b)를 통해 10Ni/Al2O3와 20Ni/Al2O3의 경우 경질 탄화수소 열분해 과정에서 생성되는 카본이 섬유형의 형태로 생성되는 것을 알 수 있다. 섬유형 카본의 경우 두께가 대략 100-200 nm까지 형성된다. Fig. 5(c)에서 30Ni/Al2O3는 열분해 반응 후 표면에 카본블랙과 일부 섬유형 탄소가 같이 생성된다.
3.2 유동층 반응기용 촉매 설계 및 모사 가스 평가
유동층 반응기용 촉매를 설계하기 위해 γ-Al2O3 pellet의 입자 크기를 150-250, 500 μm로 선정 후 30 wt%의 Ni을 담지 후 열분해 촉매를 제조하였다. Fig. 6은 150-250, 500 μm 입자 크기를 가진 열분해 촉매를 공정 모사 가스(C1-C4 경질 탄화수소), 750℃의 반응 조건에서 60분 동안 열분해 성능 평가를 진행한 결과이다. Fig. 6(a)에서 150-250 μm 열분해 촉매에서는 C2-C4의 경질 탄화수소가 모두 분해되었고, C1의 전환율이 대략 70%를 보였다. 반면, Fig. 6(b)에서 500 μm 열분해 촉매에서는 150-250 μm 열분해 촉매보다 경질 탄화수소에 대한 열분해 활성이 낮다. C2-C4의 탄화수소가 일부 분해되지 않고 반응이 진행됨에 따라 촉매 활성이 감소하였다. 이는 촉매의 입자가 작아질수록 표면에서의 반응 물질의 흡착, 탈착이 많아져 반응 속도가 증가하게 되고, 촉매 활성에 영향을 주게 된다. Fig. 6(c)는 150-250, 500 μm 열분해 촉매의 활성 평가 결과를 기반으로 H2에 대한 생산성을 나타내었다. 두 촉매는 초기 H2 생산량 6.5 mmol/min을 보였다. 500 μm 열분해 촉매는 시간이 지남에 따라 H2 생산성이 2.63 mmol/min까지 감소함을 확인하였다. 150-250 μm 열분해 촉매의 경우, 대략 6.4 mmol/min의 H2 생산성을 유지하였다.
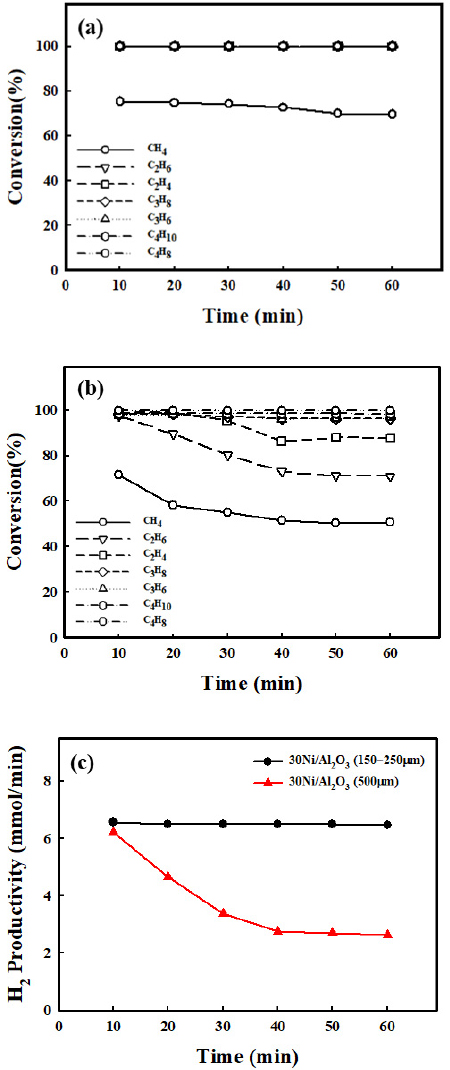
light hydrocarbons (C1-C4) conversion of (a) 10Ni/Al2O3 (150-250 μm) and (b)10Ni/Al2O3 (500 μm), (c) H2 productivity of 30Ni/Al2O3 (150-250 μm) and 30Ni/Al2O3 (500 μm)
Fig. 7은 반응 후 150-250, 500 μm 열분해 촉매를 유동시켜 촉매 간 충돌을 통해 카본을 제거할 수 있는지 확인한 결과를 나타낸 것이다. 1 inch 석영관에서 N2 2,400 mL/min 조건에서 30분간 유동을 진행하였다. 두 촉매 모두 해당 조건에서 유동층이 형성되며, 유동 시 촉매 간 충돌을 확인하였다. 충돌된 유동 입자들에서 카본이 탈착되었고, 촉매량 대비 탈착된 coke는 각각 3.35, 5.75 wt%가 탈착되었다. 500 μm 입자 크기는 촉매 활성 평가에서 급격한 활성 저하를 보였고, 이는 coke의 형성으로 인한 비활성화임을 알 수 있다. 급격한 coke의 형성은 입자의 밀도를 감소시키고, 이는 유동층에서 입자의 유동 속도를 증가시킬 수 있다11). 이로 인해 500 μm 입자에서 충돌 속도의 증가로 인해 탈착된 coke의 양이 증가한다.
4. 결 론
본 연구에서는 유동층 반응기용 경질 탄화수소 촉매 열분해용 Ni nead 촉매에 대하여 분석하였다.
1) 10Ni/Al2O3, 20Ni/Al2O3, 30Ni/Al2O3 열분해 pellet 촉매를 C3H8 경질 탄화수소를 통해 촉매 성능 평가를 진행하였다. 10Ni/Al2O3의 경우 낮은 함량으로 인해 경질 탄화수소의 전환 성능이 부족하다. 20Ni/Al2O3는 초기 성능(>99% 전환율)은 뛰어나나 60분이 지난 시점부터 열분해 성능이 감소한다. 30Ni/Al2O3는 대략 120분 동안 높은 전환율과 H2 생산성(1.6 mmol/min)을 유지한다. 10Ni/Al2O3와 20Ni/Al2O3는 대략 120분의 반응 후 섬유형 탄소가 생성된 것을 알 수 있고, 30Ni/Al2O3의 경우 카본블랙과 일부 섬유형이 같이 생성된다.
2) 유동층 운전을 위한 pellet 촉매의 입자 크기에 따른 경질 탄화수소에 대한 열분해 특성을 비교하였다. 각 150-250, 500 μm 입자 크기를 선정하였고, C1-C4 경질 탄화수소 모사 가스를 통해 열분해 성능을 평가하였다. 150-250 μm 입자 크기에서 뛰어난 열분해 특성을 확인하였다. 이는 촉매의 입자 크기가 작아질수록 표면에서 반응물의 물질 이동이 증가하여 촉매 반응에 영향을 주기 때문이다.
2) 열분해 반응 후 생성된 카본은 유동층을 통해 열분해 촉매 간 충돌로 제거할 수 있는데, 500 μm 입자 크기에서 질량 대비 제거된 카본의 양이 많다. 이는 급격한 coke의 형성으로 입자의 밀도가 감소할 수 있으며, 입자의 밀도 감소로 유동층에서의 유동 속도 증가로 인한 탈착 coke의 양이 증가하였기 때문이다.
Acknowledgments
이 논문은 2021학년도 경북대학교 연구년 교수 연구비에 의하여 연구되었음.
References
-
R. Geyer, J. R. Jambeck, and K. L. Law, “Production, use, and fate of all plastics ever made”, Science Advances, Vol. 3, No. 7, 2017, pp. e1700782.
[https://doi.org/10.1126/sciadv.1700782]
-
T. J. Kang, Y. J. Lee, H. S. Kim, N. K. Park, S. C. Lee, B. C. Choi, D. M. Jeon, and S. H. Kang, “Analysis of domestic and inter-national policies and market trends to promote a circular economy based on waste plastics”, Journal of Energy&Cli-mate Change, Vol. 18, No. 2, 2023, pp. 205-235.
[https://doi.org/10.22728/JECC.2023.18.2.205]
-
J. Huang, A. Veksha, W. P. Chan, A. Giannis, and G. Lisak, “Chemical recycling of plastic waste for sustainable material management: a prospective review on catalysts and proces-ses”, Renewable and Sustainable Energy Reviews, Vol. 154, 2022, pp. 111866.
[https://doi.org/10.1016/j.rser.2021.111866]
-
C. Palmer, E. Bunyan, J. Gelinas, M. J. Gordon, H. Metiu, and E. W. McFarland, “CO2-free hydrogen production by catal-ytic pyrolysis of hydrocarbon feedstocks in molten Ni-Bi”, Energy & Fuels, Vol. 34, No. 12, 2020, pp. 16073-16080.
[https://doi.org/10.1021/acs.energyfuels.0c03080]
-
M. J. Liu, G. Wang, S. N. Xu, T. R. Zheng, Z. D. Zhang, and S. B. He, “Reaction characteristics of maximizing light olef-ins and decreasing methane in C5 hydrocarbons catalytic pyrolysis”, Petroleum Science, Vol. 20, No. 3, 2023, pp. 1909-1921.
[https://doi.org/10.1016/j.petsci.2022.11.026]
-
D. Lee, Y. Kim, and K. Ahn, “Analysis of methane conversion rate and selectivity of methane pyrolysis reaction in ceramic tube according to temperature and reaction time”, Journal of Hydrogen and New Energy, Vol. 33, No. 1, 2022, pp. 1-7.
[https://doi.org/10.7316/KHNES.2022.33.1.1]
-
J. Woo, T. Kim, J. E. Kim, B. Cho, S. Jung, S. Park, S. Lee, and J. Kim “Ni catalyst properties for ammonia reforming: co-mparison of Ni content and space velocity”, Journal of Hy-drogen and New Energy, Vol. 32, No. 6, 2021, pp. 464-469.
[https://doi.org/10.7316/KHNES.2021.32.6.464]
-
S. H. Kim, J. Kim, and H. Y. Shin, “Exploring strategies for implementing hydrogen society based on psychological att-itudes towards hydrogen fuel: focused on risk perception, familiarity and acceptability”, Journal of Hydrogen and New Energy, Vol. 33, No. 4, 2022, pp. 267-283.
[https://doi.org/10.7316/KHNES.2022.33.4.267]
-
I. W. Wang, D. A. Kutteri, B. Gao, H. Tian, and J. Hu, “Meth-ane pyrolysis for carbon nanotubes and COx-free H2 over transition-metal catalysts”, Energy & Fuels, Vol. 33, No. 1, 2019, pp. 197-205.
[https://doi.org/10.1021/acs.energyfuels.8b03502]
-
S. H. Yoon, N. K. Park, T. J. Lee, K. J. Yoon, and G. Y. Han, “Hydrogen production by thermocatalytic decomposition of butane over a carbon black catalyst”, Catalysis Today, Vol. 146, No. 1-2, 2009, pp. 202-208.
[https://doi.org/10.1016/j.cattod.2009.04.006]
-
J. W. Chew, A. Cahyadi, C. M. Hrenya, R. Karri, and R. A. Cocco, “Review of entrainment correlations in gas-solid fl-uidization”, Chemical Engineering Journal, Vol. 260, 2015, pp. 152-171.
[https://doi.org/10.1016/j.cej.2014.08.086]