
촉매 지지용 다층 컵 구조를 이용한 메탄올 수증기 개질 반응 연구
2020 The Korean Hydrogen and New Energy Society. All rights reserved.
Abstract
In methanol steam reforming, commercial catalysts in the form of pellets are mainly used, but there are limitations to directly apply them to underwater weapon systems that require shock resistance and heat transfer characteristics. In this study, to overcome this problem, a multi-layer cup structure (MLCS) was applied to support a pellet type catalyst. The characteristics of pellet catalyst supported by MLCS and the pellet catalyst supported by conventional structure (CS) were compared by the reforming experiment. In the case of MLCS, a high methanol conversion rate was shown in the temperature range 200 to 300℃ relative to the CS manufactured with the same catalyst weight as MLCS. CS shown similar characteristics to MLCS when it manufactured in the same volume as MLCS by adding an additional 67% of the catalyst. In conclusions, MLCS can not only reduce catalyst usage by improving heat transfer characteristics, but also support pellet catalyst in multiple layers, thus improving shock resistance characteristics.
Keywords:
Methanol, Steam reforming, Multilayer, Catalyst, Pellet키워드:
메탄올, 수증기 개질, 다층, 촉매, 펠렛1. 서 론
최근 개발되는 수중무기체계는 수중 운용 시간을 증가시키기 위하여 연료개질 플랜트와 연료전지 플랜트가 탑재된 공기불요추진체계를 적용하기 위해 노력하고 있다1-3). 특히 메탄올은 다른 액체연료 대비 개질 온도가 200-300℃로 낮고, 탄소 대비 수소 함량이 높기 때문에 수중무기체계에 적합한 연료로 고려되고 있다. 메탄올은 자열개질(autothermal reforming), 부분산화 개질(partial oxidation), 수증기 개질(steam reforming) 반응으로 수소를 생산할 수 있다. 이 중 수증기 개질방식은 생산되는 수소의 분율이 상대적으로 높고, 흡열반응이기 때문에 반응기로 열을 지속적으로 공급해줘야 하는 특징이 있다. 촉매에 의한 메탄올 수증기 개질 반응은 3가지 반응 기구에 의해 설명된다4).
· 메탄올 수증기 개질 반응
(1) |
· 메탄올 분해 반응
(2) |
· 수성가스 전환 반응
(3) |
이러한 메탄올 수증기 개질 반응은 산업계에서도 많이 활용하고 있다. 수중무기체계와는 달리 산업계에서 사용하는 개질기는 지상 공간에 고정 설치된 상태로 운전되므로, 부피 및 기계적 특성에 대해 완화된 제한 조건을 가진다. 이러한 이유로 산업용 개질기는 제작단가가 낮고 유지·보수가 유리한 펠렛 형태의 촉매 사용을 선호하고, 촉매 제조업체 역시 펠렛 형태의 촉매를 주로 공급한다. 하지만 펠렛 촉매는 모노리스(monolith) 촉매와 대비하여 열전달 특성이 낮고 기계적 충격 및 진동에 취약하다는 단점이 있다5). 따라서 수중무기체계용 메탄올 개질기의 가격 경쟁력을 확보하고 유지·보수 능력을 향상시키기 위해서는 펠렛 형태의 상용 촉매를 수중무기체계에 적용하기 위한 연구가 필요하다.
메탄올 개질기와 관련된 대부분의 연구에서는 펠렛 형태로 제작된 촉매를 필요한 양만큼 튜브 반응기 안에 패킹(packing)하여 실험하였다6). Krummrich와 Llabrés7)는 잠수함용 메탄올 개질기에 대한 연구개발 진행 과정 및 일부 설계 결과를 발표하였으나, 촉매 종류 및 형태에 대해서는 언급하지 않았다. Ji 등8)은 잠수함 및 잠수정 탑재를 목표로 간접가열방식을 적용한 메탄올 개질기 연구결과를 발표하였으나, 펠렛 촉매를 종래의 구조로 튜브에 패킹하였다. Han 등9)은 수중무기체계 활용을 위하여 디젤용 자열개질 촉매 및 과산화수소 분해 촉매를 펠렛 형태로 제조한 후 종래의 구조로 개질기 및 반응기에 패킹하여 연구하였다.
본 연구에서는 펠렛 형태의 촉매를 수중무기체계에 적용하기 위하여 컵 형태로 제작된 다공성 매질 지지체에 촉매를 담아 모듈화 시키고, 다층 컵 구조(MLCS)를 필요한 양만큼 다층으로 적층하는 방법을 제시하였다. MLCS로 패킹된 개질기에 대한 개질 성능의 변화를 분석하기 위하여 종래의 구조(CS)로 패킹된 2가지 종류의 개질기와 비교하였다. 개질 실험은 전기로의 온도를 200, 225, 250, 275, 300℃로 설정한 후, 반응물 유량을 증가하며 메탄올 전환율, 기체별 생성량, 개질기 후단 온도, 압력차를 분석하였다.
2. 실험장치의 구성
Fig. 1은 메탄올 수증기 개질 실험장치 구성도이다. 메탄올(>99.9%, Sigma-Aldrich Co., St. Louis, US) 및 탈이온수는 고정밀 메탄올 펌프(Primeline, ASI Co., Richmond, US)를 통해 공급되고, 고순도 N2는 질량 유량 제어기(F-211AV, Bronkhorst Co., Ruurlo, Netherlands)를 통해 공급된다. 전기오븐(electric oven) 내에는 증발기, 가열기, 전기로 등을 설치하였으며, 전기오븐 내부는 180℃로 유지시켰다. 반응물 및 N2는 증발기 및 가열기를 통해 기화 및 가열되었다. 개질기 입구에서의 반응물 및 N2 온도를 전기로 설정 온도와 최대한 유사하게 제어하기 위하여 반응물 및 N2는 전기로에 의해 추가로 가열된 뒤 전기로 내부에 위치한 개질기로 공급하였다. 개질기의 밑면에는 K-타입 열전대를 장착하여 개질기 후단 온도를 측정하였다. 또한 개질기 전단 및 후단에는 압력계(PHP-E-0100-BCTG, Sensys Co., Ansan, Korea)를 설치하여 촉매 패킹 방법에 따른 압력차를 측정하였다.
개질기는 MLCS 및 CS 방식으로 패킹하였다. MLCS의 경우 Fig. 2와 같이 Ni foam (>99.5%, 350 g/cm3, Invisible Co., Suwon, Korea)을 컵 형태로 제작한 뒤, Cu/Zn 촉매(RP-60, BASF Co., Ludwigshafen, Germany)를 담아 모듈화시켰다. 컵 모듈은 STS 316L 재질의 1/2 inch 튜브(SS-T8-S-065-20, Swagelok Co., Solon, US) 내부에 삽입한 후, 수직방향으로 압력을 가해 컵 모듈 벽이 1/2 inch 튜브 내벽에 밀착시켰으며, 컵 모듈 밑면 역시 펠렛 촉매 형태에 따라 변형되도록 하였다. 이때 Ni foam은 압력에 의해 소성변형이 되므로 압력 제거 후에도 벽면에 고정될 수 있다. 즉, MLCS은 기설치된 컵 모듈 위에 추가의 컵 모듈을 적층하는 방식으로 총 10개의 컵모듈을 적층하여 제작하였다(Fig. 3[a]).
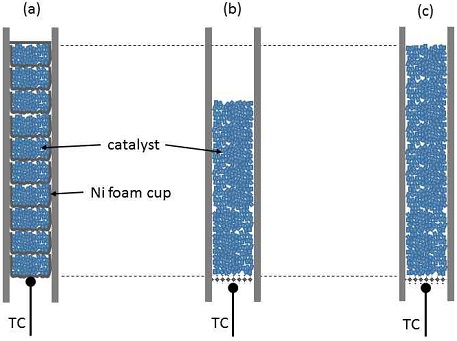
Catalyst loading structure (a) multilayer cup structure (MLCS), (b) conventional structure loaded to equal weight to MLCS (CS-W), (c) conventional structure loaded to equal volume to MLCS (CS-G)
CS 방식의 경우, STS 316L 재질의 다공성 디스크 지지체를 1/2 inch 튜브 안에 삽입 및 고정한 후, 그 위로 펠렛 형태의 Cu/Zn 촉매를 삽입하였다. 이때 개질기는 촉매 사용량을 2가지로 구분하여 제작하였다. CS-W는 MLCS에서 사용한 촉매와 유사한 무게로 삽입하여 MLCS와 weight hourly space velocity (WHSV)가 유사하도록 제작하였고(Fig. 3[b]), CS-G는 MLCS와 유사한 부피로 촉매를 삽입하여 GHSV가 유사하도록 제작하였다(Fig. 3[c]).
실험에 앞서 개질기 촉매는 300℃ 조건에서 H2 = 50 sccm, N2 = 50 sccm의 유량으로 4시간 이상 환원하였다. 개질 실험을 위하여 전기로의 온도는 200, 225, 250, 275, 300℃로 설정하였다. 반응물인 메탄올과 H2O 공급량은 촉매의 공간속도가 F1, F2, F3가 되도록 공급하였으며, SCR은 공간속도에 관계없이 1.5를 유지하였다. 구체적인 촉매 사용량 및 공간속도는 Table 1과 같다.
개질 후 생성 기체의 조성 및 분율은 가스 크로마토그래피(Micro-GC 490, Agilent, Santa Clara, US)를 통해 확인하였다. 가스 크로마토그래피는 2채널(molecular sieve 5Å & PLOT U)으로 구성하여 thermal conductivity detection (TCD)로 분석하였으며, 캐리어 가스(carrier gas)는 고순도 Ar (>99.999%)을 사용하였다. 가스 크로마토그래피에 의해 정성적으로 분석된 기체별 분율은 N2 공급량을 기준으로 정량적인 생산량으로 변환하였다. 메탄올 전환율은 Eq. 4에 의해서 계산하였다.
(4) |
3. 결과 및 고찰
3.1 메탄올 전환율
Fig. 4는 전기로의 셋팅 온도를 200℃에서 25℃ 간격으로 300℃까지 증가하였을 때, 패킹 방법 및 반응물 유량(공간속도)에 따른 메탄올 전환율의 변화를 보여주고 있다. 전반적으로 전기로의 온도가 증가할수록 메탄올 전환율은 증가하고 공간속도가 증가할수록 메탄올 전환율이 감소하는 것을 볼 수 있다.
공간속도 F2를 보면 메탄올 전환율은 S자형 곡선을 보여주었으며, 공간속도가 F1, F2, F3으로 증가함에 따라 S자형 곡선이 그래프의 우측(높은 온도 영역)으로 이동하는 것을 볼 수 있다. 즉, 공간속도 F1에서는 S자형 곡선의 포화단계가 두드러지게 나타났으며, 공간속도 F3에서는 S자형 곡선의 초기단계가 주로 나타났다. 공간속도가 가장 낮은 F1의 경우, MLCS와 CS-G의 개질 특성은 거의 유사하게 거동하였으며, 250℃ 이후부터는 메탄올 전환율이 100% 가까이 도달한 것을 볼 수 있다. 다만 CS-W는 MLCS 및 CS-G와 대비하여 전체 온도 범위에서 메탄올 전환율이 상대적으로 낮았으며, 250℃ 이후부터 약 95%로 포화되었다. 공간속도를 2배 증가시킨 F2의 경우, MLCS와 CS-G는 메탄올 전환율이 275℃부터 100% 가까이에 도달하였다. 이것은 F1 경우와 대비하여 포화점이 25℃ 상향 이동한 것이다. 이에 반해 CS-W은 포화점이 생성되지 않았다. 반응물 공급 유량을 3배 증가시킨 F3의 경우에는 MLCS와 CS-G가 300℃에서 메탄올 전환율이 100%에 도달하였지만, 전체 온도범위 내에서 포화점은 존재하지 않았다. 결론적으로 MLCS는 CS-W와 동일한 촉매량을 사용하였음에도 불구하고 촉매를 67% (무게 기준) 더 사용한 CS-G와 유사한 성능을 보여주었다.
3.2 기체별 생성량
Fig. 5는 전기로의 셋팅 온도를 200℃에서 25℃ 간격으로 300℃까지 증가하였을 때, 패킹 방법 및 반응물 유량(공간속도)에 따라 메탄올 공급 몰수에 따른 기체별 생성 몰수를 계산한 결과를 보여주고 있다. 전반적으로 기체별 생성 몰수는 메탄올 전환율 결과와 유사한 경향성을 보여주었다.
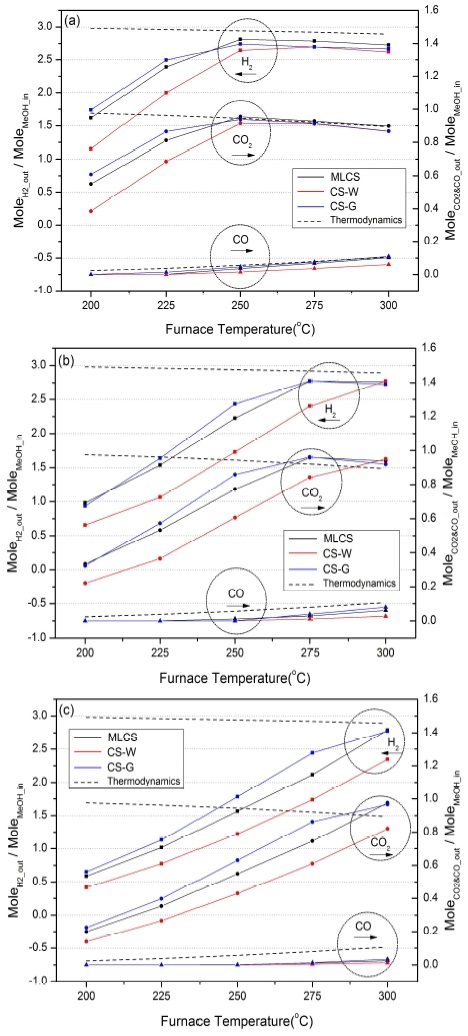
Yield mole (H2, CO2 and CO mole per mole of MeOHin) of MeOH steam reformer outlet as function of furnace temperature (a) F1, (b) F2, (c) F3
공간속도가 F1일 경우, 패킹 방법에 관계없이 H2와 CO의 몰수는 200-250℃에서 지속적으로 증가하였으나, 250℃ 이후부터는 열역학적 데이터의 경향과 동일하게 온도 증가에 따라 생성 몰수가 감소하였다. CO2와 CO는 250℃ 이상부터 열역학적 데이터와 거의 유사한 값을 보여 주었다. 이러한 결과의 원인은 Fig. 6의 개질기 후단에서 측정한 온도 데이터를 통해서 유추할 수 있었다. 공간속도 F1의 경우, 200-250℃ 구간에서 전반적으로 개질기 후단 온도는 전기로 세팅 온도보다 낮았으나, 250℃에서 두 온도가 유사해졌고 275℃ 이상부터는 개질기 후단온도가 전기로 세팅 온도보다 더 높아진 것을 볼 수 있다. 수성가스 전환 반응(Eq. 3)의 반응속도는 메탄올 수증기 개질 반응(Eq. 1)과 메탄올 분해 반응(Eq. 2)보다 느리다10). 즉, 흡열반응인 메탄올 수증기 개질 반응(Eq. 1)과 메탄올 분해 반응(Eq. 2)은 수성가스 전환 반응 대비 반응속도가 빠르므로 개질기의 전단부에서 주로 일어나게 되고, 이로 인하여 개질기 전단부 온도가 낮아진다. 전기로의 온도가 낮을 경우, 개질기의 반응속도가 느려지기 때문에 메탄올 수증기 개질 반응과 메탄올 분해 반응은 개질기 후단부까지 확장하게 된다11). 또한 개질기와 전기로 사이의 △T가 낮기 때문에 열전달 양이 충분하지 않아 흡열반응으로 낮아진 개질기 내부온도를 충분히 상승시키지 못한다. 이에 반해 전기로 온도가 증가할 경우, 촉매로 전달되는 열량도 증가하여 흡열반응으로 낮아진 개질기 내부 온도를 빠르게 회복시킬 수 있게 되고, 발열반응인 수성가스 전환반응(Eq. 3)까지 일어날 수 있었던 것으로 판단할 수 있었다.
공간속도가 F1에서 F2로 증가할 경우, MLCS와 CS-G에 한해 H2 및 CO2 생성 몰수 증가의 종료 시점이 275℃로 지연된 것을 볼 수 있다. MLCS와 CS-G는 F1일 때와 마찬가지로 275℃ 이후부터는 열역학적 데이터의 경향과 동일하게 온도 증가에 따라 생성 몰수가 감소하였다. 하지만 CO2의 생성 몰수는 열역학적 데이터보다 크고, CO의 생성 몰수는 적은 것을 볼 수 있다. 개질기 내부온도는 개질 반응에 의한 흡열량/발열량 및 전기로에 의해 공급되는 열량에 의해 결정되는데, 공간속도가 증가함에 따라 개질기 내부온도가 전기로 세팅온도보다 낮은 영역에서 포화되었기 때문이라 판단되었다. 공간속도 F2에서는 메탄올 전환율이 100% 수준이고(Fig. 4[b]), 생성 기체가 열역학적 데이터의 경향성을 추종하고 있음에도 불구하고(Fig. 5[b]), 개질기 내부온도가 전기로 세팅 온도보다 낮을 것을 확인할 수 있다(Fig. 6). 또한 공간속도 F2일 때 측정한 MLCS와 CS-G의 내부온도를 기준으로 CO2 및 CO의 열역학적 데이터를 확인해 보면 생성 몰수가 열역학적 데이터와 거의 유사한 것을 볼 때, 개질기 내부 온도는 개질기 후단에서 측정한 온도 근처에서 포화되었다고 판단할 수 있었다.
공간속도가 F3으로 증가할 경우, 200-300℃ 구간에서는 패킹 방법에 관계없이 더 이상 열역학적 데이터의 경향성을 추종하지 않았다. MLCS와 CS-G는 전기로 세팅 온도 300℃에서 메탄올 전환율이 100% 수준까지 도달하였지만(Fig. 4[c]), CO2 및 CO의 생성 몰수는 열역학적 데이터보다 크게 나타났다(Fig. 5[c]). 이러한 현상은 F2의 경우와 동일한 이유 때문이라 생각할 수 있다. 하지만 공간속도 F3에서 MLCS와 CS-G는 공간속도 F2일 때와 비교하여 개질기 내부온도가 더 낮아지므로 생성 몰수가 열역학적 데이터보다 더 크게 벗어난 것을 볼 수 있다.
개질기 후단 온도만 고려한다면, 200-300℃ 구간에서 공간속도에 관계없이 MLCS와 CS-G가 CS-W보다 더 높은 값을 보여주었다. 특히 MLCS의 후단온도는 공간속도 F1에서 CS-G와 거의 유사하게 나타났지만, 공간속도가 F2, F3로 증가할 경우 CS-G보다 더 높아지는 것을 볼 수 있다(Fig. 6). 이러한 결과들로 유추해 볼 때, MLCS가 CS-G보다 열전달 측면에서 더 유리한 구조라고 말할 수 있다. 특히 F1에서의 MLCS는 CS-G 및 CS-W에 비하여 기체별 생성량이 열역학적 데이터와 더 유사한 값을 보여주었다. 이것은 MLCS의 경우, 후단 온도뿐만 아니라 내부 온도 역시 전기로의 세팅온도와 유사하여 열역학적 데이터에 근접할 수 있었다고 판단되었다.
CS-G의 경우, 개질기 외벽을 통해 공급되는 열이 펠렛 촉매 간의 점 혹은 면 접촉을 통해 내부로 전달되지만, MLCS는 높은 열전달 계수를 가지는 Ni foam을 통해 촉매 내부로 빠르게 공급될 수 있다. 특히 Ni foam은 개질기 외벽 및 촉매에 밀착되어 있으므로 개질기 내부로 유입되는 열저항을 감소시킬 수 있으며, 촉매와 접촉하고 있는 Ni foam은 압력에 의해서 촉매 적층 형상에 따라 소성변형되어 있으므로 열전달 면적도 증가한다. 또한 Ni foam이 다단으로 적층되어 있으므로 촉매 전체 영역에 최대한 균질하게 열을 공급할 수 있다.
MLCS의 열전달 효과는 Fig. 7에서와 같이 공간 속도 F1에서의 후단온도(TF1)와 공간속도 F3에서의 후단온도(TF3) 차이(△TF = TF1 - TF1)를 통해서도 확인할 수 있다. 전기로의 세팅 온도가 증가함에 따라 패킹 방법에 관계없이 △TF가 증가하였지만, MLCS는 다른 패킹 방법에 비해 상승 기울기 및 △TF의 값이 상대적으로 낮았다. 오히려 CS-G의 경우 가장 높은 △TF의 값을 보여주었다.
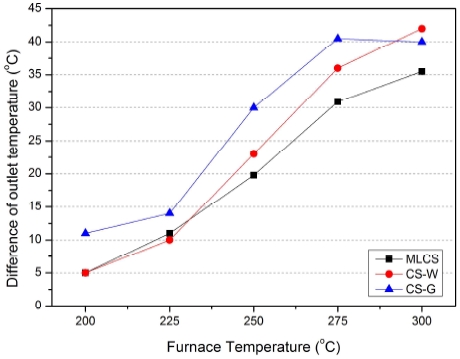
Difference of outlet temperature between F1 and F3 as function of furnace temperature (△TF = outlet temperature when F1[TF1] - outlet temperature when F3[TF3])
MLCS는 높은 열전달 특성을 통해 동일한 촉매 무게를 사용한 CS-W와 비교하여 향상된 개질 성능을 보여주었으나, 동일한 촉매 부피로 패킹된 CS-G의 개질 성능까지는 미치지 못하였다. 이것은 패킹 구조 개선을 통해 열공급 능력이 향상되었다 하더라도 해당 운전온도에서의 반응속도로 인하여 촉매당 개질할 수 있는 반응물의 한계가 존재하기 때문이라 판단되었다. 결국 열역학에 가까운 메탄올 수증기 개질 반응을 기대하기 위해서는 촉매로의 열전달을 향상시키는 것과 동시에 공간속도 및 포화온도를 고려하여 최소한의 촉매 양을 패킹할 필요가 있다고 판단하였다.
촉매 패킹 방법은 개질기 입구와 출구에서의 압력차에도 영향을 미친다. Fig. 8과 같이 개질기의 압력차는 패킹 방법과는 관계없이 전기로의 세팅 온도가 상승함에 따라 기체 부피 팽창에 의해 증가하는 것을 볼 수 있다. 또한 공간속도가 증가할수록 온도에 따른 압력차의 기울기가 증가하였다. 압력차는 상대적으로 적은 양의 촉매를 넓은 공간에 배치한 MLCS가 가장 낮았으며, 많은 양의 촉매를 넓은 공간에 배치한 CS-G가 가장 높은 값을 가졌다. 상식적으로 이러한 MLCS의 촉매 배치는 기계적 충격에 의한 펠렛 촉매의 재배열 및 파손을 감소시킬 수 있다. 결론적으로 MLCS는 기존 촉매 패킹 방법과 비교하여 개질 특성 및 내충격 특성을 향상시켜주고, 개질기 차압 및 그에 따른 펌프 소비전력을 감소시킬 수 있으므로 수중무기체계에 적용할 수 있는 촉매 패킹구조라고 판단되었다.
4. 결 론
본 연구에서는 펠렛 촉매가 삽입된 Ni foam 컵을 다층으로 적층시킨 개질기(MLCS)와 일반적인 방법으로 촉매를 패킹한 개질기 2종(CS-W, CS-G)과 비교·분석하였다. 메탄올 전환율 및 기체별 생성량을 분석한 결과, MLCS는 MLCS와 동일한 촉매 무게를 삽입하여 패킹한 CS-W 대비 향상된 개질 성능을 보여주었다. 또한 촉매를 추가 삽입하여(MLCS 대비 촉매 무게 67% 증가) MLCS와 동일한 부피로 패킹한 CS-G와는 거의 유사한 개질 특성을 보여주었다. 이것은 열전달 특성이 우수한 Ni foam이 개질기 벽면 및 펠렛 촉매에 밀착하여 열저항을 감소시켜 주고, 다층으로 구성된 Ni foam이 펠렛 촉매 내부를 균질하게 분배하고 있으므로, 개질기 외벽에서 공급되는 열을 펠렛 촉매 내부까지 빠르게 전달할 수 있기 때문이었다. 이러한 이유로 MLCS의 후단온도는 CS-W 및 CS-G보다 높게 나타났다.
MLCS는 전기로 세팅 온도에 따른 메탄올 전환율 및 기체별 생성량의 경향성은 CS-G와 유사하였으나, 개질 성능 측면에서 CS-G를 능가하지는 못하였다. 비록 MLCS가 패킹 구조 개선을 통해 열전달 특성이 향상되었다 하더라도 해당 운전온도에서의 반응속도로 인하여 촉매 당 개질할 수 있는 반응물 유량의 한계가 존재하였다. 따라서 개질기에 MLCS 구조를 적용하더라도 공간속도 및 포화온도를 고려하여 최소한의 촉매 양을 패킹할 필요가 있었다. 결론적으로 MLCS는 기존 촉매 패킹 방법과 비교하여 개질 특성 및 내충격 특성을 향상시켜주고 개질기 차압을 감소시켜줄 수 있지만, 충분한 개질 성능 확보를 위해서는 적정량의 촉매량을 투입해야 한다는 것을 알 수 있었다.
Acknowledgments
본 연구는 극환경 전원 고기능화 특화연구실 예산으로 수행되었다.
References
-
A. Psoma and G. Sattler, “Fuel cell systems for submarines: from the first idea to serial production”, J. Power Sources, Vol. 106, No. 1-2, 2002, pp. 381-383.
[https://doi.org/10.1016/S0378-7753(01)01044-8]
-
“HDW, SENER develop methanol reformer for fuel cell submarines”, Fuel Cells Bulletin, Vol. 2012, No. 12, 2012.
[https://doi.org/10.1016/S1464-2859(12)70342-5]
-
“UTC power to develop fuel cell for Spanish sub”, Fuel Cells Bulletin, Vol. 2008, No. 1, 2008.
[https://doi.org/10.1016/S1464-2859(08)70009-9]
-
K. I. Cho, J. W. Yun, S. S. Yu, “Experimental study on catalytic characteristics of 1-kW methanol Reformer”, Trans. Korean Soc. Mech. Eng. B, Vol. 43, No. 12, 2019, pp. 817-823. Retrieved from http://www.dbpia.co.kr/Journal/articleDetail?nodeId=NODE09273564, .
[https://doi.org/10.3795/KSME-B.2019.43.12.817]
- E. Y. Choi, “Characteristics of ZrO2 felt supported Cu/Zn catalyst for methanol steam reforming”, Trans. of Korean Hydrogen and New Energy Society, Vol. 28, No. 2, 2017, pp. 129-136.
- J. H. Lee, “A study on the characteristics of Ni/Ce0.9Gd0.1O2-x and Cu/Ce0.9Gd0.1O2-x catalysts for methanol steam reforming synthesized by solution combustion process”, Trans. of Korean Hydrogen and New Energy Society, Vol. 30, No. 3, 2019, pp. 209-219.
-
S. Krummrich and J. Llabrés, “Methanol reformer – the next milestone for fuel cell powered submarines”, Int. J. Hydrogen Energy, Vol. 40, No. 15, 2015, pp. 5482-5486.
[https://doi.org/10.1016/j.ijhydene.2015.01.179]
-
H. J. Ji, J. H. Lee, E. Y. Choi, and I. S. Seo, “Hydrogen production from steam reforming using an indirect heating method”, Int. J. Hydrogen Energy, Vol. 43, No. 7, 2018, pp. 3655-3663.
[https://doi.org/10.1016/j.ijhydene.2017.12.137]
-
G. W. Han, S. H. Lee, and J. M. Bae, “Diesel autothermal reforming with hydrogen peroxide for low-oxygen environments”, Applied Energy, Vol. 156, 2015, pp. 99-106.
[https://doi.org/10.1016/j.apenergy.2015.06.036]
-
Y. T. Choi and H. G. Stenger, “Kinetics, simulation and optimization of methanol steam reformer for fuel cell applications”, J. Power Sources, Vol. 142, No. 1-2, 2005, pp. 81-91.
[https://doi.org/10.1016/j.jpowsour.2004.08.058]
- K. M. Kim, Y. S. Choe and H. K. Song, “A simulation of steady and dynamic states of methanol reforming reaction”, Institute of Control Robotics and Systems, Vol. 1, No. 1, 1989, pp. 395-395. Retrieved from http://www.dbpia.co.kr/Journal/articleDetail?nodeId=NODE06316937, .