
10 kW 급 암모니아-수소 혼소엔진을 위한 암모니아 개질 촉매 및 반응기 설계에 관한 연구
2020 The Korean Hydrogen and New Energy Society. All rights reserved.
Abstract
Ammonia-hydrogen dual-fuel engine is a way to reduce greenhouse gas emission because ammonia and hydrogen are carbon-free fuels. In ammonia-hydrogen dual-fuel engine, hydrogen is supplied to improve the combustion characteristic of ammonia. In this study, an ammonia reformer was developed to supply hydrogen for 10 kW class ammonia-hydrogen dual-fuel engine. Thermodynamic characteristic and catalyst were investigated for ammonia reforming. Heat transfer was important for high ammonia conversion of ammonia reformer. 99% of ammonia conversion was obtained when 10 LPM of ammonia and 610℃ of hot gas were supplied to the ammonia reformer.
Keywords:
Ammonia, Hydrogen, Dual-fuel engine, Reformer, CO2-free engine키워드:
암모니아, 수소, 혼소엔진, 개질기, 무탄소 엔진1. 서 론
자동차 및 선박을 포함한 다양한 산업분야에서 온실가스 배출 규제가 강화되고 있다. 우리나라 정부는 지난 파리협정에서 2030년까지 전망치 대비 37%의 온실가스를 감축하는 것을 목표로 제시하였다. 자동차 분야에서는 EU가 2020년부터 자동차 1대 당 연평균 이산화탄소 배출량 제한을 130 g/km에서 95 g/km로 강화하였다. 국제해사기구(International Maritime Organization)도 2030년까지 선박 운송 분야의 이산화탄소 배출량을 2008년 대비 40% 감축을 목표로 하고 있으며, 2020년부터 에너지 효율 설계지수(energy efficiency design index) 2단계를 시행하여 신조 선박에 대해 에너지 효율이 20% 향상된 선박의 설계가 요구된다.
암모니아는 강화되는 온실가스 배출 규제에 대응하기 위한 에너지 캐리어로 많은 관심을 받고 있다. 암모니아는 탄소를 포함하지 않아 사용 과정에서 이산화탄소가 발생하지 않는다. 또한, 암모니아는 상온에서 압축하면 10 bar 이하에서 액화되어 저장과 수송이 용이하다1). 현재 암모니아 산업은 비료 생산을 위해 전 세계 수소 생산량의 약 50%를 사용할 정도로 성숙한 산업이다2). 따라서 생산과 공급 측면에서도 기존 암모니아 플랜트와 인프라를 활용할 수 있다는 장점이 있다.
에너지 캐리어로서 암모니아의 장점을 활용하여 재생에너지에서 생산된 수소를 암모니아로 전환하여 수송하고 활용하기 위한 연구가 진행되고 있다. 호주에서는 풍부한 재생에너지를 암모니아로 전환하여 수출하는 전략을 수립하고 있다3). 이의 일환으로 암모니아 생산기업인 Yara는 호주의 필바라(Pilbara)에서 태양에너지를 사용하는 암모니아 생산 플랜트 실증을 진행하고 있다4). 반면, 호주 연방과학원(Commonwealth Scientific and Industrial Research Organization)은 암모니아 기반의 수소 충전소를 개발하여 실증을 진행하였다5). 일본도 전략적 혁신 창조 프로그램(cross-ministerial strategic innovation promotion)의 에너지 캐리어 부분에서 암모니아를 수소 캐리어의 하나로 사용하는 연구 개발을 진행하였다6). 전략적 혁신 창조 프로그램에는 암모니아에서 수소를 추출해 사용하는 연료전지뿐만 아니라 암모니아 가스터빈 및 가열로와 같이 암모니아를 직접 연소해 사용하는 연구도 포함하고 있다. 특히, 연소를 통해 암모니아를 사용하는 방법은 수소 추출 및 순도 향상 공정이 필요 없어 다른 사용 방법보다 높은 가격경쟁력을 확보할 수 있다7).
암모니아 엔진도 연소를 통해 암모니아를 직접 사용하는 방법으로 연구되어 왔다8). 암모니아의 발열량은 18.61 MJ/kg으로 기존 화석연료인 가솔린과 경유보다 낮다9). 반면, 암모니아의 이론 공연비는 6.05로 낮아 공기와 암모니아 혼합기의 발열량은 가솔린 및 디젤과 동등한 수준이다. 하지만, 연소 측면에서 암모니아는 자발화온도가 650℃로 높고 옥탄가가 130 이상으로 자발화가 어렵다. 화염 전파 속도도 다른 탄화수소 연료보다 낮아 높은 엔진 속도에서의 연소에 불리하다10).
암모니아의 연소 특성을 향상시키기 위하여 혼소엔진에 대한 연구가 진행되었다. 한국에너지기술연구원은 가솔린-LPG 이종연료 엔진을 개조하여 가솔린-암모니아 혼소엔진을 개발하였다. 개발된 가솔린-암모니아 혼소엔진은 최대 70%까지 가솔린을 암모니아로 대체하여 연소가 가능하였다11). 아이오와 주립대학에서는 디젤 및 디메틸에테르와 암모니아의 혼소 엔진을 개발하였으며, 최적의 암모니아 혼합비율은 60%였다12,13). 탄화수소 연료와 암모니아의 혼소엔진은 탄화수소 연료를 암모니아로 대체하여 이산화탄소 배출을 일부 줄일 수 있으나, 이종 연료의 저장과 공급이 필요하다는 단점이 있다.
암모니아와 수소의 혼소를 통해서는 이산화탄소 배출이 없는 엔진의 구현이 가능하다. 또한, 수소를 암모니아에서 추출해 공급하면 별도의 수소 저장이 필요 없다. 덴마크 공과대학(Technical University of Denmark)에서는 가스 실린더에 저장된 암모니아와 수소를 612.5 cc 엔진에 공급하였으며, 최적의 암모니아 혼합비 10%에서 약 35%의 도시효율을 보였다14). 덴마크 공과대학은 실험 결과를 바탕으로 Mg(NH3)6Cl를 이용한 암모니아 저장장치와 암모니아 개질기로 구성된 연료시스템을 제안하였다. 도요타도 저온 수소 발생 장치와 고온 암모니아 개질기로 구성된 암모니아-수소 혼소엔진에 대한 개념을 제시하였다15). 암모니아-수소 혼소엔진을 구현하기 위해서는 암모니아에서 수소를 추출하는 개질기가 필요하다. 또한, 효율 향상을 위해서는 배기가스에서 열을 회수하여 개질기에 반응열을 공급해야 한다.
본 연구에서는 10 kW 급 암모니아-수소 혼소엔진에 수소를 공급할 수 있는 암모니아 개질기에 대한 연구를 진행하였다. 이를 위하여 암모니아 개질 반응의 열역학적 특성을 살펴보았으며, 간이반응기 실험을 통해 암모니아 개질에 적합한 촉매를 선정하였다. 최종적으로는 개질기 형상에 따른 개질 성능을 평가하여 10 kW 급 암모니아-수소 혼소엔진에 적용이 가능한 암모니아 개질기를 개발하였다.
2. 실 험
2.1 암모니아 개질 반응의 열역학적 특성
암모니아 개질 반응은 식 1과 같이 수소와 질소로 분해되는 흡열 반응으로 열이 공급되어야 한다. 암모니아 개질반응의 열역학적 평형에서의 조성과 암모니아 공급유량에 따라 반응에 필요한 열량을 계산하였다. 암모니아 개질에 필요한 열량은 가스 승온에 필요한 열량과 반응열을 포함하여 계산하였다.
(1) |
2.2 암모니아 개질 촉매 선정
Fig. 1은 암모니아 개질 촉매 선정에 사용한 간이 반응기의 모식도를 나타낸다. 촉매는 글리신-나이트레이트법(glycine nitrate process)으로 제조한 Ru/CGO (3.0 Ru wt.%) 촉매와 상용 Ru 촉매를 비교하였다16). Ru/CGO 촉매는 파우더와 직경 4.31±0.15 mm 길이 10.57±1.49 mm의 펠렛 형태로 가공하여 사용하였으며, 상용 Ru 촉매는 직경 2.97±0.26 mm의 구형촉매를 구입하였다. 암모니아는 mass flow controller (5850E, Brooks, Hatfield, USA)를 이용하여 유량을 제어하여 반응기에 공급하였다. 반응기는 12.7 mm stainless steel (STS) 관으로 제작하여 전기로 내에 설치하였다. 촉매층의 온도는 상단과 하단에 열전대를 설치하여 proportional-integral-derivative (PID) 제어하였다. 반응을 거치고난 가스의 암모니아 농도는 Fourier-transform infrared spectroscopy (MultiGas 2030-1065 Ready, MKS Co. Ltd., Andover, USA)를 이용하여 측정하였으며, 식 2와 같이 암모니아 전환율을 계산하였다.
(2) |
2.3 암모니아 개질기 성능 평가
암모니아 개질기의 성능을 평가하기 위하여 Fig. 2와 같은 장치를 이용하였다. 엔진의 배기가스를 링 블로워(DHB-700, DHFM Co., Ltd., Incheon, Korea)와 전기히터(LE 10000 HT, Leister Technologies AG, Kaegiswil, Switzerland)를 사용하여 모사하였다. 실험은 65 kg/h의 공기를 560-650℃로 가열하여 개질기에 공급하며 진행하였다. 개질기에 공급되는 암모니아는 mass flow controller (5850E, Brooks, Hatfield, USA)를 이용하여 유량을 제어하였다. 암모니아는 배기가스와 열 교환을 통해 예열하여 암모니아 개질기로 공급되었다. 개질기에서 반응을 거치고난 가스의 암모니아 농도는 Fourier-transform infrared spectroscopy (MultiGas 2030-1065 Ready, MKS Co. Ltd., Andover, USA)를 이용하여 측정하였다. 암모니아 개질기는 Fig. 3과 같이 개질기의 형상에 따라 개질기 A와 개질기 B를 제작하였다. 개질기 A의 촉매층은 50.8×200 mm의 STS 관으로 제작하였으며, 배기가스가 반응기 외부를 통과하면서 반응열을 공급하도록 하였다. 개질기 A에서는 200 mL와 400 mL의 촉매를 장입하고 개질 성능을 평가하였다. 개질기 B는 25.4×400 mm의 반응기 2개를 병열로 설치하여 200 mL의 촉매를 장입하였을 때, 배기가스와 열 교환 면적이 개질기 A와 비교하여 2배가 되도록 제작하였다.
3. 결과 및 고찰
3.1 암모니아 개질 반응의 열역학적 특성
Fig. 4는 암모니아 개질 반응의 열역학적 평형에서의 조성을 나타낸다. 열역학적 평형에서 암모니아는 400℃에서 암모니아 농도가 4,430 ppm으로 약 99.0%의 암모니아 전환율을 보이며, 650℃에서 잔류 암모니아 농도가 340 ppm으로 99.9% 이상의 암모니아 전환율을 보인다. Table 1은 10 kW 암모니아-수소 혼소엔진에서 암모니아 개질기에 공급되는 암모니아 양과 반응에 필요한 열을 계산한 결과이다. 개질기로 공급되는 암모니아 유량은 생성된 수소와 엔진에 공급되는 암모니아의 비율이 1:9가 되도록 설정하였다. 암모니아-수소 혼소엔진에 145 LPM의 암모니아를 공급하면 공급되는 총 열량은 33.60 kW이며, 암모니아-수소 혼소엔진의 효율을 30%로 가정하면 약 10 kW의 엔진 출력을 얻을 수 있다. 생성되는 수소와 암모니아의 비율이 1:9가 되기 위해서는 10 LPM의 암모니아가 개질기에 수소로 전환되어야 한다. 또한, 개질 반응을 위해서는 400℃와 600℃에서 각각 495 W와 583 W의 열이 배기가스에서 회수되어 개질기로 공급되어야 한다. 400-600℃는 일반적인 불꽃점화 엔진에서 얻을 수 있는 배기가스 온도이며, 가스 승온과 개질 반응에 필요한 열을 배기가스에서 회수하여 공급할 수 있는 개질기의 설계가 필요하다.
3.2 암모니아 개질 촉매 선정
Fig. 5는 암모니아 개질 촉매 선정을 위해 간이반응기에서 촉매 평가를 평가한 결과이다. 파우더 형태의 Ru/CGO 촉매는 600℃ 이상의 온도에서 99% 이상의 암모니아 전환율을 보였다. 하지만 펠렛 형태로 가공된 Ru/CGO 촉매의 암모니아 전환율은 크게 감소하였으며, 98% 이상의 암모니아 전환율을 얻기 위해서는 680℃ 이상의 반응 온도가 필요하였다. 반면, 상용 Ru 촉매는 공간 속도 6,000/h에서 파우더 형태의 Ru/CGO와 유사한 암모니아 전환율을 보였으며, 555℃에서도 99%의 암모니아 전환율을 보였다. 또한, 촉매 장입량을 줄여 공간 속도가 12,000/h로 증가한 조건에서도 650℃ 이상에서 99% 이상의 높은 암모니아 전환율을 보였다. 간이반응기의 촉매 평가를 바탕으로 암모니아 전환율이 우수한 상용 Ru 촉매를 암모니아 개질기에 적용하였다.
3.3 암모니아 개질기 성능 평가
Fig. 6은 암모니아 공급유량에 따른 암모니아 개질기의 암모니아 전환율을 나타낸다. 개질기 A에 200 mL의 촉매를 장입하였을 때에는 암모니아 공급유량이 5 LPM 이하인 조건에서 99%의 암모니아 전환율을 보였으나, 암모니아 공급유량이 10 LPM으로 증가함에 따라 암모니아 전환율이 85%로 감소하였다. Fig. 7은 개질기 A에 200 mL의 촉매를 장입하였을 때 촉매층 위치에 따른 온도를 나타낸다. 입구에서 촉매층 20 mm까지는 암모니아 개질 반응에 의해 촉매층의 온도가 감소하고 20 mm 이후에는 열전달에 의해 촉매층의 온도가 증가하였다. 또한, 암모니아의 공급유량이 증가함에 따라 흡열 반응인 암모니아 개질 반응에 의하여 촉매층의 온도가 감소하는 것을 확인하였다. 특히, 암모니아 공급유량이 3 LPM에서 5 LPM으로 증가함에 따라 촉매층 온도가 급격히 감소하였다. 암모니아 공급유량이 10 LPM인 조건에서는 촉매층의 온도가 400℃ 이하로 감소하였다. 암모니아의 공급유량이 증가함에 따라 개질 반응에 의한 흡열량은 증가한다. 반면, 외부 배기가스에서 촉매층으로 열전달이 효과적으로 이루어지지 않아 촉매층의 온도가 낮아지고 암모니아 전환율은 감소하게 된다. 개질기 A에 촉매를 400 mL를 장입하면 촉매를 200 mL 장입한 경우보다 높은 암모니아 전환율을 얻을 수 있었으나, 10 LPM의 암모니아를 공급하는 조건에서 95%의 암모니아 전환율을 얻을 수 있었다. 개질기 B는 촉매층의 직경을 감소시키고 2개 촉매층으로 구성하여 개질기 A와 동일한 촉매 부피에서 열전달 면적이 2배가 되도록 제작하였다. 개질기 B는 촉매량을 증가시키지 않고도 암모니아의 전환율이 증가하였다. 특히, 암모니아를 10 LPM 공급하는 조건에서도 잔류 암모니아 농도가 500 ppm 이하로 암모니아 전환율은 99% 이상이었다. 암모니아 전환율의 향상은 촉매층의 직경을 감소시켜 촉매층으로 열전달량이 증가한 결과이다. Table 2는 개질기로 공급되는 암모니아 유량이 10 LPM인 조건에서 공급되는 암모니아의 압력과 온도를 나타낸다. 촉매층의 직경을 감소시키고 길이를 증가시킨 개질기 B의 개질기 입구압력은 174 mbar로 개질기 A의 입구압력보다 64 mbar 증가하였다. 반면, 예열장치에서의 차압은 개질기 B에서 감소하였다. 이는 암모니아 전환율이 증가와 함께 예열장치로 공급되는 가스의 온도가 낮아져 공급되는 암모니아의 온도도 낮아진 결과이다. 결과적으로 예열장치에서의 개질기 B의 입구압력은 307 mbar로 개질기 A보다 36 mbar가 증가하였다.
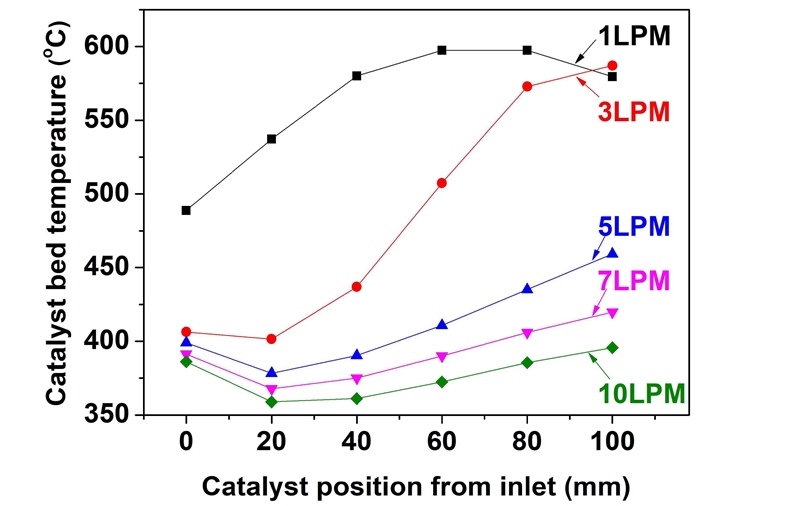
Catalyst bed temperature of ammonia reformer A with 200 mL of catalyst at 65 kg/h and 650℃ of hot gas
Fig. 8은 개질기 B에 공급되는 배기가스의 온도에 따른 암모니아의 전환율을 나타낸다. 엔진의 배기가스 온도는 엔진 운전조건에 영향을 받으며, 높은 배기가스 온도는 낮은 엔진 효율을 나타낸다. 따라서 암모니아 개질기는 낮은 배기온도에서도 높은 암모니아 전환율을 갖도록 설계되어야 한다. 암모니아 개질기 B는 610-650℃ 영역에서 잔류 암모니아 농도가 4,000 ppm 이하로 99% 이상의 암모니아 전환율을 보였다. 해당 개질기는 145 LPM의 암모니아를 공급하는 암모니아-수소 혼소엔진에서 배기온도가 610℃이상으로 제어되면 수소와 암모니아 비율이 1:9로 공급이 가능할 것으로 보이며, 엔진 효율이 약 30%를 만족하면 약 10 kW 암모니아-수소 혼소엔진의 구현이 가능할 것으로 기대된다.
4. 결 론
본 연구에서는 암모니아-수소 혼소엔진에 수소를 공급하기 위한 암모니아 개질기에 대한 연구를 진행하였다.
1) 암모니아 개질반응은 400-600℃의 온도영역에서 열역학적 평형에 도달하면 99.0-99.9%의 암모니아 전환율을 얻을 수 있다. 암모니아-수소 혼소엔진에 수소와 암모니아의 혼합비율을 1:9로 공급하는 조건에서 엔진 효율을 30%로 가정하면 엔진과 암모니아 개질기에 각각 135 LPM과 10 LPM의 암모니아를 공급하면 약 10 kW의 엔진 출력을 얻을 수 있으며, 이때 배기가스에서는 495-583 W의 열을 회수하여 암모니아 개질기에 공급해 주어야 한다.
2) 암모니아 개질 촉매로는 상용 Ru 촉매가 glycine nitrate process로 제조된 Ru/CGO 촉매보다 높은 암모니아 전환율을 보였다. 상용 Ru 촉매는 공간 속도가 6,000/h인 조건에서 555℃ 이상에서 99% 이상의 암모니아 전환율을 얻을 수 있었다.
3) 암모니아 개질기를 촉매 선정 평가 결과를 바탕으로 제작하여 평가하였다. 촉매층이 ∅50.8×200 mm인 개질기는 10 LPM의 암모니아가 공급되는 조건에서 85%의 암모니아 전환율을 보였으며, 열전달이 효과적으로 이루어지지 않는 것을 촉매층 온도로 확인하였다. ∅25.4×400 mm의 촉매층 2개를 병열로 배치한 개질기는 열전달 면적이 2배로 증가하여 10 LPM의 암모니아가 공급되는 조건에도 99%의 암모니아 전환율을 보였다.
4) 본 연구에서 개발된 암모니아 개질기는 약 15 LPM의 수소를 암모니아-수소 혼소엔진에 공급이 가능하다. 하지만, 엔진의 배기온도 및 배기유량은 운전조건에 의해 결정되어 엔진과 연계한 실험이 필요하다. 향후 암모니아 개질기와 엔진을 연계하여 암모니아-수소 혼소엔진을 개발할 계획이다.
Acknowledgments
본 연구는 한국기계연구원의 주요 사업의 개인시드창의형 과제인 “수소 동력시스템을 위한 암모니아 개질기 개발” 과제로 수행되었으며, 이에 감사드립니다.
References
-
H. Lesmana, Z. Zhang, X. Li, M. Zhu, W. Xu, and D. Zhang, “NH3 as a transport fuel in internal combustion engines: a technical review”, J. Energy Resour. Technol., Vol. 141, No. 7, 2019.
[https://doi.org/10.1115/1.4042915]
-
R. Lan, J. T. S. Irvine, and S. Tao, “Ammonia and related chemicals as potential indirect hydrogen storage materials”, Int. J. Hydrogen Energy, Vol. 37, No. 2, 2012, pp. 1482-1494.
[https://doi.org/10.1016/j.ijhydene.2011.10.004]
- C. Ginn, “The National Hydrogen Roadmap provides a blueprint for the development of a hydrogen industry in Australia”, CSIRO, 2018. Retrieved from https://www.csiro.au/en/Do-business/Futures/Reports/Energy-and-Resources/Hydrogen-Roadmap, .
- C. Rijksen, “Green hydrogen in ammonia production”, Western Australia’s Renewable Hydrogen Conference, 2018. Retrieved from http://www.drd.wa.gov.au/Publications/Documents/Hydrogen%20Conference%20Yara%20Chris%20Rijksen.pdf, .
-
K. Y. Koo, H. B. Im, D. Song, and U. Jung, “Status of COx-free hydrogen production technology development using ammonia”, Journal of Energy & Climate Change, Vol. 14, No. 1, 2019, pp. 34-42.
[https://doi.org/10.22728/JECC.2019.14.1.034]
-
S. Iida and K. Sakata, “Hydrogen technologies and developments in Japan”, Clean Energy, Vol. 3, No. 2, 2019, pp. 105-113.
[https://doi.org/10.1093/ce/zkz003]
- S. Muraki, “Development of technologies to utilize green ammonia in energy market”, 2018 NH3 Fuel Conference, 2018. Retrieved from https://nh3fuelassociation.org/wp-content/uploads/2018/11/AEA-Imp-Con-01Nov18-Shigeru-Muraki-Keynote-Address.pdf, .
-
P. Dimitriou and R. Javaid, “A review of ammonia as a compression ignition engine fuel”, Int. J. Hydrogen Energy, Vol. 45, No. 11, 2020, pp. 7098-7118.
[https://doi.org/10.1016/j.ijhydene.2019.12.209]
-
C. Lhuillier, P. Brequigny, N. Lamoureux, F. Contino, and C. Mounaïm-Rousselle, “Experimental investigation on laminar burning velocities of ammonia/hydrogen/air mixtures at elevated temperatures”, Fuel, Vol. 263, 2020, pp. 116653.
[https://doi.org/10.1016/j.fuel.2019.116653]
-
X. Han, Z. Wang, C. Mário, Z. Sun, Y. He, and K. Cen, “Experimental and kinetic modeling study of laminar burning velocities of NH3/air, NH3/H2/air, NH3/CO/air and NH3/CH4/air premixed flames”, Combustion and Flame, Vol. 206, 2019, pp. 214-226.
[https://doi.org/10.1016/j.combustflame.2019.05.003]
-
J. Jang, Y. Woo, H. C. Yoon, J. N. Kim, Y. Lee, and J. Kim, “Combustion characteristics of ammonia-gasoline dual-fuel system in a one liter engine”, Journal of the Korean Institute of Gas, Vol. 19, No. 6, 2015, pp. 1-7.
[https://doi.org/10.7842/kigas.2015.19.6.1]
-
C. W. Gross and S. C. Kong, “Performance characteristics of a compression-ignition engine using direct-injection ammonia–DME mixtures”, Fuel, Vol. 103, 2013, pp. 1069-1079.
[https://doi.org/10.1016/j.fuel.2012.08.026]
-
A. J. Reiter and S. C. Kong, “Combustion and emissions characteristics of compression-ignition engine using dual ammonia-diesel fuel”, Fuel, Vol. 90, No. 1, 2011, pp. 87-97.
[https://doi.org/10.1016/j.fuel.2010.07.055]
-
C. S. Mørch, A. Bjerre, M. P. Gøttrup, S. C. Sorenson, and J. Schramm, “Ammonia/hydrogen mixtures in an SI-engine: engine performance and analysis of a proposed fuel system”, Fuel, Vol. 90, No. 2, 2011, pp. 854-864.
[https://doi.org/10.1016/j.fuel.2010.09.042]
- K. Tange, N. Nakamura, H. Nakanishi, and H. Arikawa, “Hydrogen generator, ammonia-burning internal combustion engine, and fuel cell”, United States Patent, 2016. Retrieved from https://patents.google.com/patent/US9506400B2/en, .
-
S. Lee, M. Bae, J. Bae, and S. P. Katikaneni, “Ni–Me/Ce0.9Gd0.1O2−x (Me: Rh, Pt and Ru) catalysts for diesel pre-reforming”, Int. J. Hydrogen Energy, Vol. 40, No. 8, 2015, pp. 3207-3216.
[https://doi.org/10.1016/j.ijhydene.2014.12.113]